Les matériaux réfractaires sont des substances spécialisées, résistantes à la chaleur, utilisées dans des applications à haute température telles que les fours et les réacteurs. Ils sont composés de matériaux naturels et synthétiques, principalement non métalliques, et comprennent souvent des combinaisons de composés et de minéraux tels que l'alumine, les argiles réfractaires, la bauxite, la chromite, la dolomie, la magnésite, le carbure de silicium et la zircone. Ces matériaux sont choisis pour leur capacité à résister aux températures extrêmes, aux chocs thermiques et à la corrosion chimique. Les revêtements réfractaires des équipements tels que les fours utilisent souvent des conceptions d'isolation multicouches, incorporant des fibres céramiques d'alumine légères et des panneaux d'isolation de haute qualité, qui garantissent une faible perte de chaleur et une bonne efficacité énergétique. Des matériaux réfractaires avancés, tels que l'alumine ou le carbure de silicium à haute résistance, sont également utilisés pour assurer des conditions de traitement précises et uniformes dans les environnements industriels.
Explication des points clés :
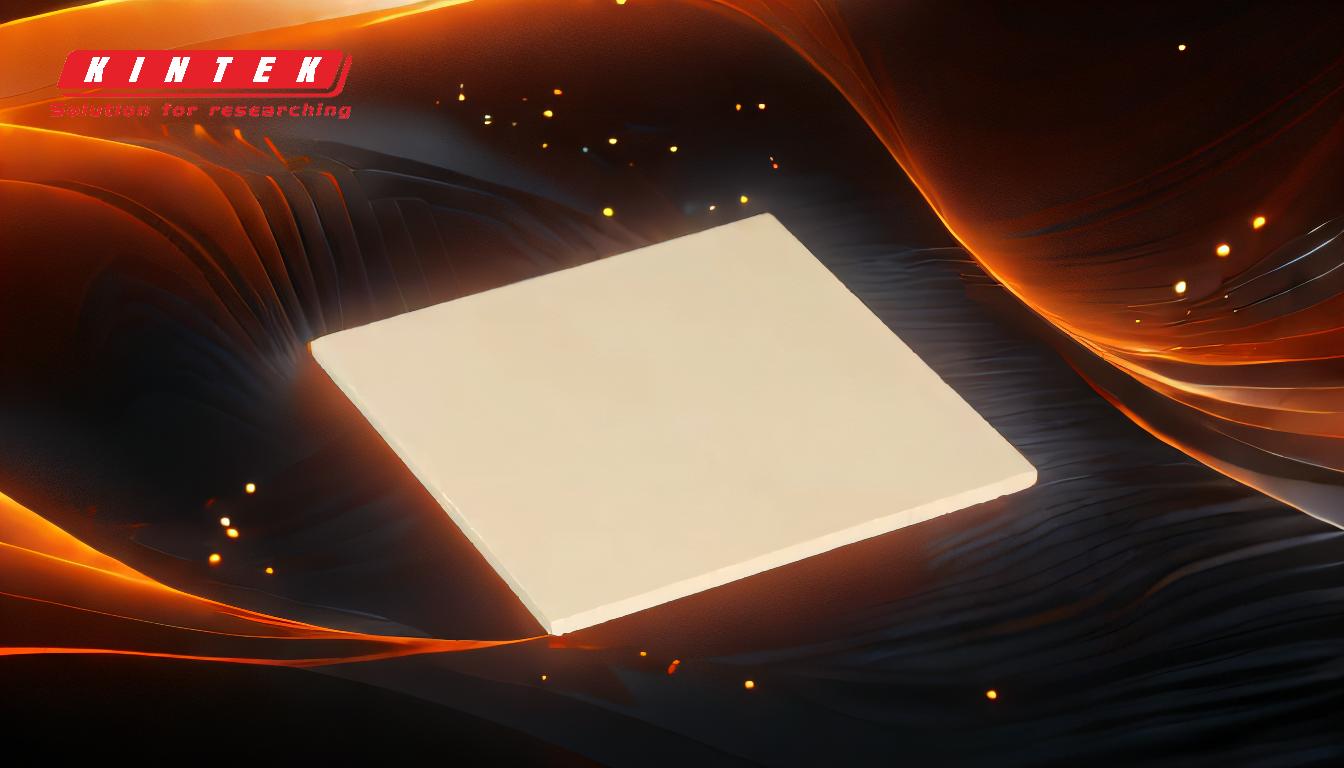
-
Composition des matériaux réfractaires:
- Les matériaux réfractaires sont constitués d'une combinaison de composés non métalliques et de minéraux naturels et synthétiques.
-
Les matériaux les plus courants sont les suivants
- l'alumine (Al₂O₃): Elle offre une résistance élevée et une grande stabilité thermique.
- Argiles réfractaires: Offrent une bonne isolation thermique et une bonne résistance aux chocs thermiques.
- Bauxite: Source d'alumine, utilisée pour son point de fusion élevé.
- Chromite (FeCr₂O₄): Ajoute une résistance à la corrosion et une stabilité à haute température.
- Dolomite (CaMg(CO₃)₂): Utilisée pour ses propriétés réfractaires dans les environnements basiques.
- Magnésite (MgCO₃): Offre une résistance aux scories basiques et aux températures élevées.
- Carbure de silicium (SiC): Connu pour sa conductivité thermique exceptionnelle et sa résistance à l'usure.
- Zircone (ZrO₂): Offre une résistance thermique élevée et une faible conductivité thermique.
-
Types de matériaux réfractaires:
- Réfractaires acides: Fabriqués à partir de matériaux tels que la silice (SiO₂) et la zircone, ils conviennent aux environnements acides.
- Réfractaires basiques: Composés de magnésite, de dolomie et de chromite, idéaux pour les conditions basiques ou alcalines.
- Réfractaires neutres: Comprennent l'alumine et la chromite, qui résistent aux scories acides et basiques.
-
Applications dans les revêtements de four:
- Les matériaux réfractaires sont utilisés dans des conceptions d'isolation multicouche pour les revêtements de fours.
-
Les conceptions les plus courantes sont les suivantes
- Fibre céramique d'alumine légère: Fournit une excellente isolation thermique et réduit les pertes de chaleur.
- Panneaux isolants de haute qualité: Matériaux de support qui améliorent l'efficacité énergétique et l'intégrité structurelle.
- Ces modèles sont exempts d'amiante, ce qui garantit la sécurité et la conformité aux normes environnementales modernes.
-
Matériaux réfractaires avancés:
- Alumine à haute résistance (Al₂O₃): Utilisée dans les fours à moufle pour sa durabilité et sa capacité à maintenir des conditions de traitement uniformes.
- Carbure de silicium (SiC): Utilisé dans les revêtements de fours avancés pour sa conductivité thermique et sa résistance aux chocs thermiques.
- Ces matériaux assurent un contrôle précis de la température et la longévité des processus industriels à haute température.
-
Principales propriétés des matériaux réfractaires:
- Point de fusion élevé: Essentiel pour résister aux températures extrêmes.
- Résistance aux chocs thermiques: Capacité à supporter des changements de température rapides sans se fissurer.
- Stabilité chimique: Résistance à la corrosion par les scories, les gaz et les métaux en fusion.
- Faible conductivité thermique: Minimise les pertes de chaleur et améliore l'efficacité énergétique.
- Résistance mécanique: Assure l'intégrité structurelle dans des conditions de contraintes et de charges élevées.
-
Critères de sélection des matériaux réfractaires:
- Température de fonctionnement: Les matériaux doivent résister à la température maximale de l'application.
- Environnement chimique: Compatibilité avec la composition chimique du processus (acide, basique ou neutre).
- Conductivité thermique: Une faible conductivité est préférable pour l'isolation, tandis qu'une conductivité élevée est nécessaire pour les applications de transfert de chaleur.
- Charge mécanique: Les matériaux doivent supporter le poids de la structure et toute charge supplémentaire.
- Coût et disponibilité: Équilibre entre les performances et la faisabilité économique.
En comprenant la composition, les types, les applications et les propriétés des matériaux réfractaires, les acheteurs d'équipements et de consommables peuvent prendre des décisions éclairées afin d'optimiser les performances, l'efficacité et la sécurité des procédés industriels à haute température.
Tableau récapitulatif :
Aspect | Détails |
---|---|
Composition | Alumine, argiles réfractaires, bauxite, chromite, dolomie, magnésite, SiC, zircone |
Types de réfractaires | Réfractaires acides, basiques, neutres |
Applications | Revêtements de fours, isolation multicouche, procédés industriels à haute température |
Propriétés principales | Point de fusion élevé, résistance aux chocs thermiques, stabilité chimique, faible conductivité thermique, résistance mécanique |
Critères de sélection | Température de fonctionnement, environnement chimique, conductivité thermique, charge mécanique, coût |
Optimisez vos procédés à haute température avec les bons matériaux réfractaires. contactez nos experts dès aujourd'hui !