L'histoire du four à vide est un voyage fascinant qui reflète les progrès de la science des matériaux, de l'ingénierie et des processus industriels.Les fours à vide, qui sont conçus pour fonctionner dans un environnement contrôlé à basse pression, ont considérablement évolué depuis leur création.Initialement développés pour répondre aux exigences des applications à haute température dans la métallurgie et le traitement des matériaux, ces fours sont devenus indispensables dans les industries exigeant des traitements thermiques précis, telles que l'aérospatiale, l'automobile et l'électronique.Leur capacité à fonctionner sans oxydation ni contamination a fait des fours à vide une pierre angulaire de la fabrication et de la recherche modernes.
Explication des points clés :
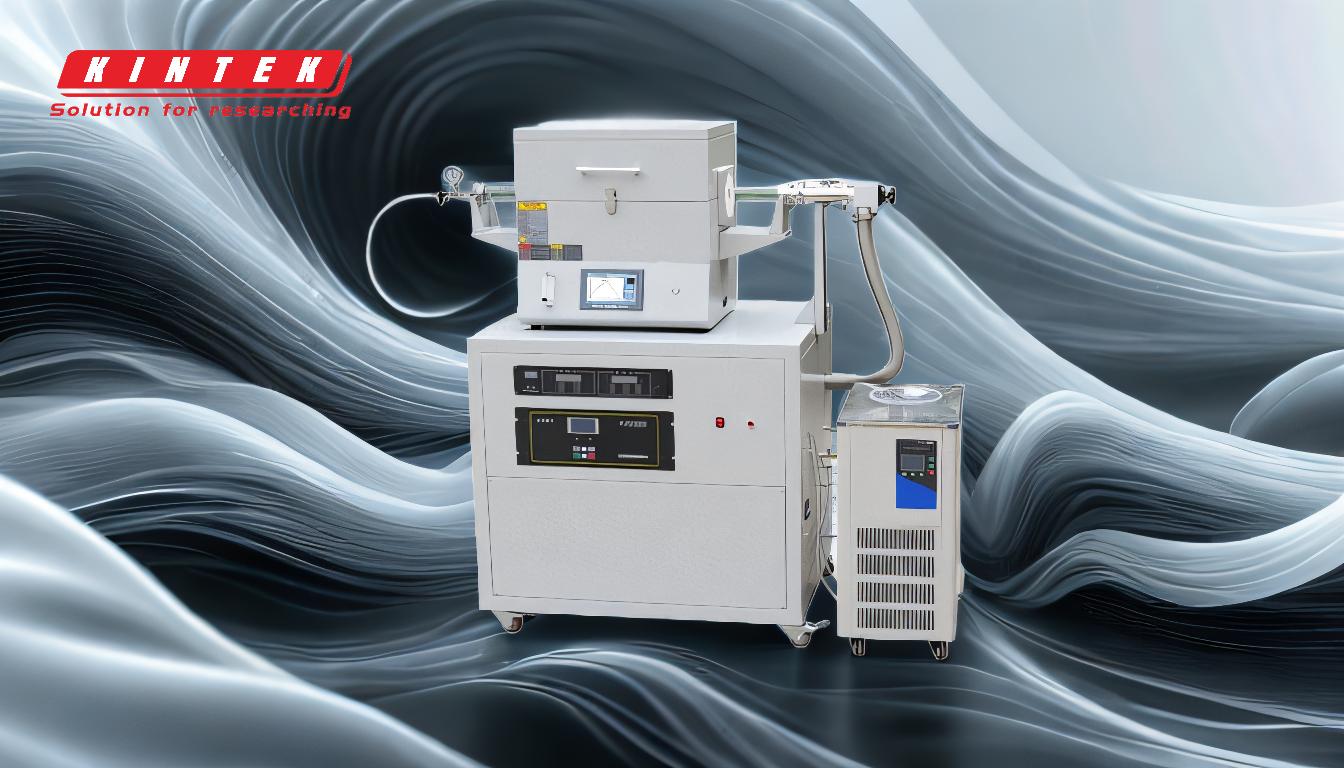
-
Origines et premiers développements:
- Le concept de chauffage sous vide remonte au début du XXe siècle, lorsque des scientifiques et des ingénieurs ont commencé à explorer les moyens de traiter les matériaux sans les exposer aux gaz atmosphériques.
- Les premiers fours à vide étaient rudimentaires et principalement utilisés en laboratoire pour des expériences impliquant des matériaux à haute température.
- Le développement de la technologie du vide pendant la Seconde Guerre mondiale, en particulier dans les secteurs de l'aérospatiale et de la défense, a accéléré l'adoption des fours à vide pour les applications industrielles.
-
Progrès dans la conception et les matériaux:
- Les fours à vide modernes intègrent des matériaux avancés, tels que des fibres d'isolation sous forme rigide, pour résister aux vitesses élevées du ventilateur de convection et assurer des taux de chauffage et de refroidissement rapides.
- L'utilisation de ces matériaux permet d'ouvrir et de décharger le four à n'importe quelle température, ce qui améliore la flexibilité opérationnelle.
- Les innovations en matière d'éléments chauffants, tels que le graphite ou le molybdène, ont permis d'améliorer l'efficacité thermique et la durabilité.
-
Types de fours à vide:
- Les fours à vide peuvent être classés en fonction de leurs méthodes de chauffage, comme les systèmes à gaz ou les systèmes électriques.
- Les fours à vide à chauffage électrique sont plus courants en raison de leur contrôle précis de la température et de leur capacité à maintenir un environnement sous vide constant.
- Des conceptions spécialisées, telles que des configurations horizontales ou verticales, répondent à des besoins industriels spécifiques.
-
Applications et impact sur l'industrie:
- Les fours à vide sont largement utilisés dans les processus de traitement thermique, notamment le recuit, le brasage, le frittage et la trempe, où l'absence de contamination est essentielle.
- Les industries telles que l'aérospatiale, l'automobile et l'électronique font appel aux fours à vide pour produire des composants de haute performance dotés de propriétés mécaniques supérieures.
- La possibilité de traiter des matériaux tels que le titane, les superalliages et les céramiques avancées a élargi le champ d'application des fours à vide.
-
Tendances et innovations futures:
- Les recherches en cours se concentrent sur l'amélioration de l'efficacité énergétique, la réduction des temps de cycle et l'intégration de technologies intelligentes pour la surveillance et le contrôle en temps réel.
- Le développement de fours à vide hybrides, combinant plusieurs méthodes de chauffage, devrait encore améliorer les performances et la polyvalence.
- Les initiatives en matière de développement durable favorisent l'adoption de matériaux et de procédés écologiques dans la fabrication des fours à vide.
Pour plus d'informations sur les fours à vide, vous pouvez consulter cette ressource : four sous vide .
L'histoire des fours à vide témoigne de l'ingéniosité humaine et de la poursuite incessante du progrès technologique.Après des débuts modestes, les fours sous vide sont devenus un outil essentiel de l'industrie moderne et continuent de repousser les limites de ce qui est possible en matière de traitement des matériaux et de traitement thermique.
Tableau récapitulatif :
Principales étapes | Détails |
---|---|
Origines et premiers développements | - Début du 20e siècle :Concept de chauffage sous vide. |
- SECONDE GUERRE MONDIALE :Adoption accélérée dans les industries de l'aérospatiale et de la défense. | |
Progrès dans la conception | - Les matériaux modernes tels que les fibres isolantes améliorent les vitesses d'échauffement et de refroidissement. |
- Les innovations en matière d'éléments chauffants (graphite, molybdène) améliorent l'efficacité. | |
Types de fours à vide | - Les systèmes à chauffage électrique dominent en raison de la précision du contrôle de la température. |
- Des conceptions spécialisées (horizontales/verticales) répondent aux besoins de l'industrie. | |
Applications | - Utilisé dans les processus de recuit, de brasage, de frittage et de durcissement. |
- Essentiel dans les industries aérospatiale, automobile et électronique. | |
Tendances futures | - L'accent est mis sur l'efficacité énergétique, les technologies intelligentes et les conceptions hybrides. |
Découvrez comment les fours à vide peuvent révolutionner vos processus. contactez nos experts dès aujourd'hui !