La température la plus appropriée pour brûler le ciment dans un four rotatif se situe généralement entre 1400°C à 1500°C .Cette plage de température garantit la formation correcte du clinker, qui est le produit intermédiaire de la fabrication du ciment.En dessous de cette plage, les réactions chimiques nécessaires à la formation du clinker peuvent être incomplètes, tandis que des températures supérieures à cette plage peuvent entraîner une consommation d'énergie excessive et une détérioration potentielle du revêtement du four.Le processus consiste à chauffer les matières premières (calcaire, argile et autres additifs) à cette température pour faciliter les réactions chimiques qui produisent le clinker.
Explication des points clés :
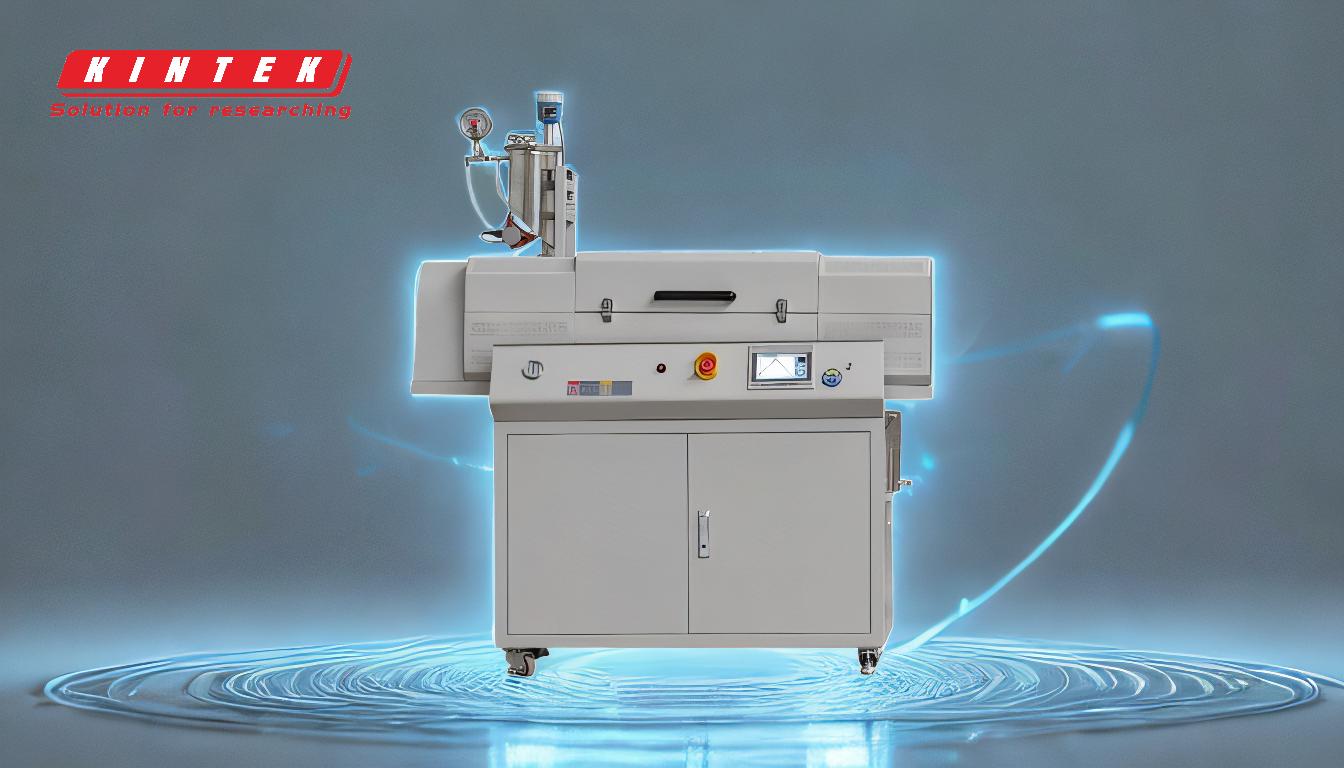
-
Plage de température optimale pour le ciment:
- La plage de température idéale pour la cuisson du ciment dans un four rotatif est la suivante 1400°C à 1500°C .Cette plage est critique pour la formation du clinker, qui est le composant principal du ciment.
- À cette température, les matières premières subissent une série de réactions chimiques, notamment la calcination (décomposition du calcaire en chaux) et le frittage (formation de composés du clinker tels que l'alite et la bélite).
-
Pourquoi les températures de 1400°C à 1500°C conviennent-elles ?:
- Réactions chimiques:À des températures inférieures à 1400°C, les réactions chimiques nécessaires à la formation du clinker peuvent ne pas être menées à terme, ce qui conduit à un clinker de mauvaise qualité.Au-dessus de 1500°C, les réactions peuvent devenir trop intenses, entraînant une surcombustion et un manque d'efficacité énergétique.
- Efficacité énergétique:Le maintien de la température dans cette plage garantit une utilisation efficace de l'énergie.Des températures excessives entraînent une augmentation de la consommation de combustible et des coûts d'exploitation.
- Protection du revêtement du four:Une exposition prolongée à des températures supérieures à 1500°C peut endommager le revêtement réfractaire du four, ce qui réduit sa durée de vie et augmente les coûts de maintenance.
-
Comparaison avec d'autres types de fours:
- Fours rotatifs indirects:Ces fours fonctionnent généralement à des températures plus basses (1200-1300°C pour le tube du four et moins de 1150°C pour le matériau).Ils ne conviennent pas à la production de ciment car ils ne peuvent pas atteindre les températures nécessaires à la formation du clinker.
- Fours rotatifs électriques:Avec une température maximale de 1100°C, les fours rotatifs électriques ne conviennent pas non plus à la production de ciment en raison de leur incapacité à atteindre les températures nécessaires à la formation du clinker.
-
Facteurs influençant le choix de la température:
- Composition des matières premières:La composition chimique des matières premières peut influencer la température de combustion requise.Par exemple, les matières premières à forte teneur en silice peuvent nécessiter des températures légèrement plus élevées.
- Conception du four:La conception du four rotatif, y compris sa longueur, son diamètre et son revêtement réfractaire, peut affecter la distribution de la température et l'efficacité du transfert de chaleur.
- Type de combustible:Le type de combustible utilisé (charbon, gaz naturel ou combustibles alternatifs) peut influencer la température de combustion et, par conséquent, la température globale du four.
-
Considérations pratiques:
- Contrôle de la température:Un contrôle précis de la température est essentiel pour maintenir des conditions de combustion optimales.Ce contrôle est généralement assuré par des systèmes de contrôle avancés qui surveillent et ajustent l'alimentation en combustible et en air.
- Processus de refroidissement:Une fois le clinker formé, il doit être rapidement refroidi pour préserver sa qualité.Cette opération s'effectue généralement dans un refroidisseur rattaché au four, où le clinker est refroidi d'environ 1400°C à moins de 200°C.
-
Impact de la température sur la qualité du ciment:
- Qualité du clinker:La température affecte directement la qualité du clinker, qui à son tour influence la résistance et la durabilité du produit cimentier final.
- Consommation d'énergie:Le fait de travailler dans la plage de température optimale minimise la consommation d'énergie, ce qui rend le processus plus rentable et plus respectueux de l'environnement.
- Considérations environnementales:Le maintien d'une température correcte permet de réduire les émissions de polluants tels que les oxydes d'azote (NOx) et le dioxyde de soufre (SO2), qui sont des sous-produits de la combustion à haute température.
En résumé, la température la plus appropriée pour brûler le ciment dans un four rotatif se situe entre 1400°C et 1500°C.Cette plage garantit une formation efficace du clinker, une efficacité énergétique et la protection du revêtement du four, tout en contribuant à la production d'un ciment de haute qualité.
Tableau récapitulatif :
Aspect | Détails |
---|---|
Température optimale | 1400°C à 1500°C |
Objectif | Assure la formation correcte du clinker et l'efficacité énergétique. |
Réactions chimiques | La calcination et le frittage se produisent à cette distance |
Efficacité énergétique | Réduit la consommation de combustible et les coûts d'exploitation |
Protection du revêtement du four | Prévient les dommages au revêtement réfractaire |
Qualité du ciment | Un clinker de haute qualité permet d'obtenir un ciment durable et résistant |
Impact sur l'environnement | Réduction des émissions de NOx et de SO2 |
Vous avez besoin de conseils d'experts sur l'optimisation de votre four rotatif pour la production de ciment ? Contactez nous dès aujourd'hui pour en savoir plus !