Le procédé de dépôt physique en phase vapeur (PVD) est une méthode sophistiquée utilisée pour déposer des couches minces de matériaux sur un substrat.Il implique la transformation d'un matériau solide en une phase vapeur, qui est ensuite déposée sur un substrat pour former un revêtement mince et uniforme.Le processus est généralement réalisé dans un environnement sous vide afin de garantir la pureté et le contrôle du dépôt.Le dépôt en phase vapeur est largement utilisé dans diverses industries pour des applications telles que l'amélioration de la résistance à l'usure, l'amélioration de la résistance à la corrosion et la réalisation de finitions décoratives.Le processus comprend plusieurs étapes clés, notamment la vaporisation du matériau de revêtement, la migration des particules vaporisées et le dépôt sur le substrat.
Explication des points clés :
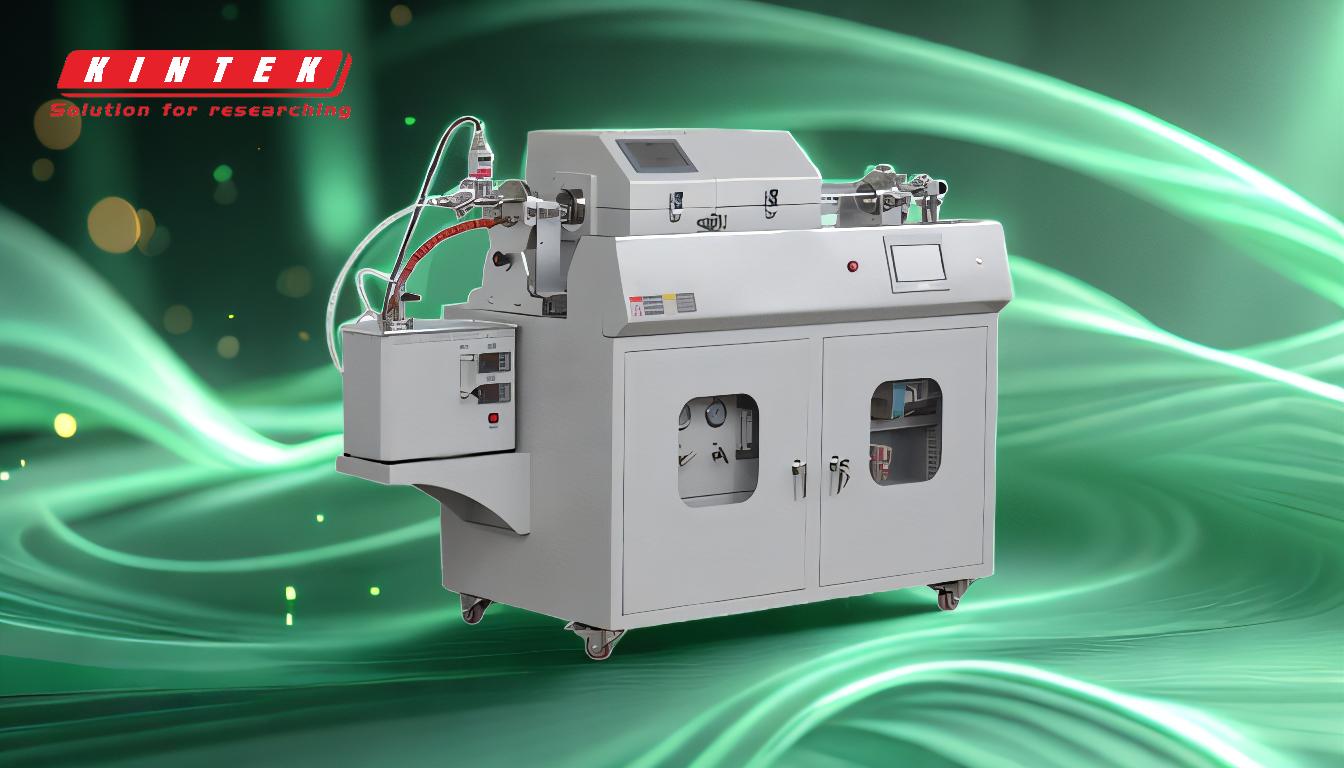
-
Vaporisation du matériau d'enrobage:
- La première étape du processus PVD est la vaporisation du matériau de revêtement.Cette vaporisation peut être réalisée par plusieurs méthodes, notamment l'évaporation, la pulvérisation cathodique ou l'ablation laser.
- L'évaporation:Le matériau est chauffé à haute température jusqu'à ce qu'il se vaporise.Cette opération est souvent réalisée à l'aide d'un faisceau d'électrons ou d'un chauffage résistif.
- Pulvérisation:Des ions à haute énergie sont utilisés pour bombarder le matériau cible, provoquant l'éjection des atomes de la surface et leur entrée dans la phase vapeur.
- Ablation par laser:Un laser à haute puissance est utilisé pour vaporiser directement le matériau.
-
Migration des particules vaporisées:
- Une fois que le matériau est en phase vapeur, les particules (atomes, molécules ou ions) migrent à travers la chambre à vide.Cette migration est influencée par l'environnement sous vide, qui minimise les collisions avec d'autres particules et garantit un dépôt propre.
- Au cours de cette phase, les particules vaporisées peuvent subir des réactions, surtout si des gaz réactifs (tels que l'azote ou l'oxygène) sont introduits dans la chambre.Ces réactions peuvent former des composés qui se déposent ensuite sur le substrat.
-
Dépôt sur le substrat:
- L'étape finale est le dépôt du matériau vaporisé sur le substrat.Cela se produit lorsque les particules vaporisées se condensent sur la surface plus froide du substrat, formant un film mince et uniforme.
- Le substrat est généralement maintenu à une température inférieure à celle du matériau vaporisé, ce qui favorise la condensation et l'adhésion du revêtement.
- L'épaisseur du film déposé peut être contrôlée avec précision à l'aide de techniques telles que la surveillance du taux de cristal de quartz, qui mesure le taux de dépôt et l'ajuste en fonction des besoins.
-
Utilisation du plasma et des gaz réactifs:
- Dans de nombreux procédés PVD, le plasma est utilisé pour améliorer le processus de vaporisation et de dépôt.Le plasma est créé par l'ionisation d'un gaz, souvent à l'aide d'une source de plasma à couplage inductif (ICP).
- Le plasma à haute énergie peut aider à dissocier les molécules de gaz en espèces réactives, qui peuvent ensuite réagir avec le matériau vaporisé pour former des composés.Ce procédé est particulièrement utile pour créer des revêtements durs et résistants à l'usure, tels que le nitrure de titane (TiN) ou le nitrure de chrome (CrN).
- L'introduction de gaz réactifs (azote, oxygène, etc.) permet la formation de revêtements composés, qui peuvent avoir des propriétés supérieures à celles des revêtements métalliques purs.
-
Environnement sous vide:
-
L'ensemble du processus de dépôt en phase vapeur (PVD) est réalisé dans un environnement sous vide poussé.Ce point est crucial pour plusieurs raisons :
- La pureté:Le vide minimise la présence de contaminants, ce qui garantit un dépôt propre.
- Contrôle:La faible pression permet un contrôle précis du processus de dépôt, y compris la vitesse et l'uniformité du revêtement.
- Contrôle de la réaction:L'environnement sous vide permet de contrôler les réactions entre le matériau vaporisé et les gaz réactifs, ce qui garantit des propriétés de revêtement constantes.
-
L'ensemble du processus de dépôt en phase vapeur (PVD) est réalisé dans un environnement sous vide poussé.Ce point est crucial pour plusieurs raisons :
-
Applications des revêtements PVD:
-
Les revêtements PVD sont utilisés dans une large gamme d'applications, notamment :
- Résistance à l'usure:Les revêtements tels que TiN et CrN sont utilisés pour améliorer la résistance à l'usure des outils de coupe, des moules et d'autres composants.
- Résistance à la corrosion:Les revêtements PVD peuvent constituer une barrière contre la corrosion, prolongeant ainsi la durée de vie des composants exposés à des environnements difficiles.
- Finitions décoratives:Le dépôt en phase vapeur (PVD) est utilisé pour créer des revêtements décoratifs avec une large gamme de couleurs et de finitions, que l'on retrouve souvent dans l'électronique grand public et la bijouterie.
- Revêtements optiques:Le dépôt en phase vapeur (PVD) est utilisé pour déposer des couches minces ayant des propriétés optiques spécifiques, telles que les revêtements antireflets sur les lentilles.
-
Les revêtements PVD sont utilisés dans une large gamme d'applications, notamment :
En résumé, le procédé PVD est une méthode très contrôlée et polyvalente de dépôt de films minces sur un substrat.Il implique la vaporisation du matériau de revêtement, la migration des particules vaporisées et le dépôt sur le substrat, le tout dans un environnement sous vide.L'utilisation de plasma et de gaz réactifs permet de créer des revêtements composés aux propriétés améliorées, ce qui fait du dépôt en phase vapeur une technique précieuse dans diverses applications industrielles.
Tableau récapitulatif :
Étapes clés | Description de l'opération |
---|---|
Vaporisation | Le matériau de revêtement est vaporisé par évaporation, pulvérisation ou ablation laser. |
Migration | Les particules vaporisées se déplacent dans le vide, ce qui minimise les collisions. |
Dépôt | Les particules se condensent sur le substrat, formant un film mince et uniforme. |
Plasma et gaz réactifs | Améliore les propriétés du revêtement, par exemple en formant du TiN ou du CrN pour la résistance à l'usure. |
Environnement sous vide | Assure la pureté, le contrôle et la cohérence des réactions pendant le dépôt. |
Applications | Résistance à l'usure, protection contre la corrosion, finitions décoratives et revêtements optiques. |
Découvrez comment les revêtements PVD peuvent améliorer vos produits. contactez nos experts dès aujourd'hui !