Le dépôt physique en phase vapeur (PVD) est un processus essentiel dans la fabrication moderne, en particulier pour créer des couches minces et des revêtements sur des substrats. Le dépôt physique en phase vapeur dans un environnement sous vide est essentiel pour plusieurs raisons, notamment la réduction de la contamination, l'augmentation du libre parcours moyen des particules et le contrôle précis du processus de dépôt. Le vide minimise la présence d'atomes et de molécules indésirables, garantissant ainsi un environnement propre et contrôlé nécessaire à la réalisation de revêtements de haute qualité. En outre, il permet un transfert et une adhésion efficaces des matériaux, qui sont essentiels pour les applications en microélectronique, en optique et dans d'autres technologies de pointe.
Explication des points clés :
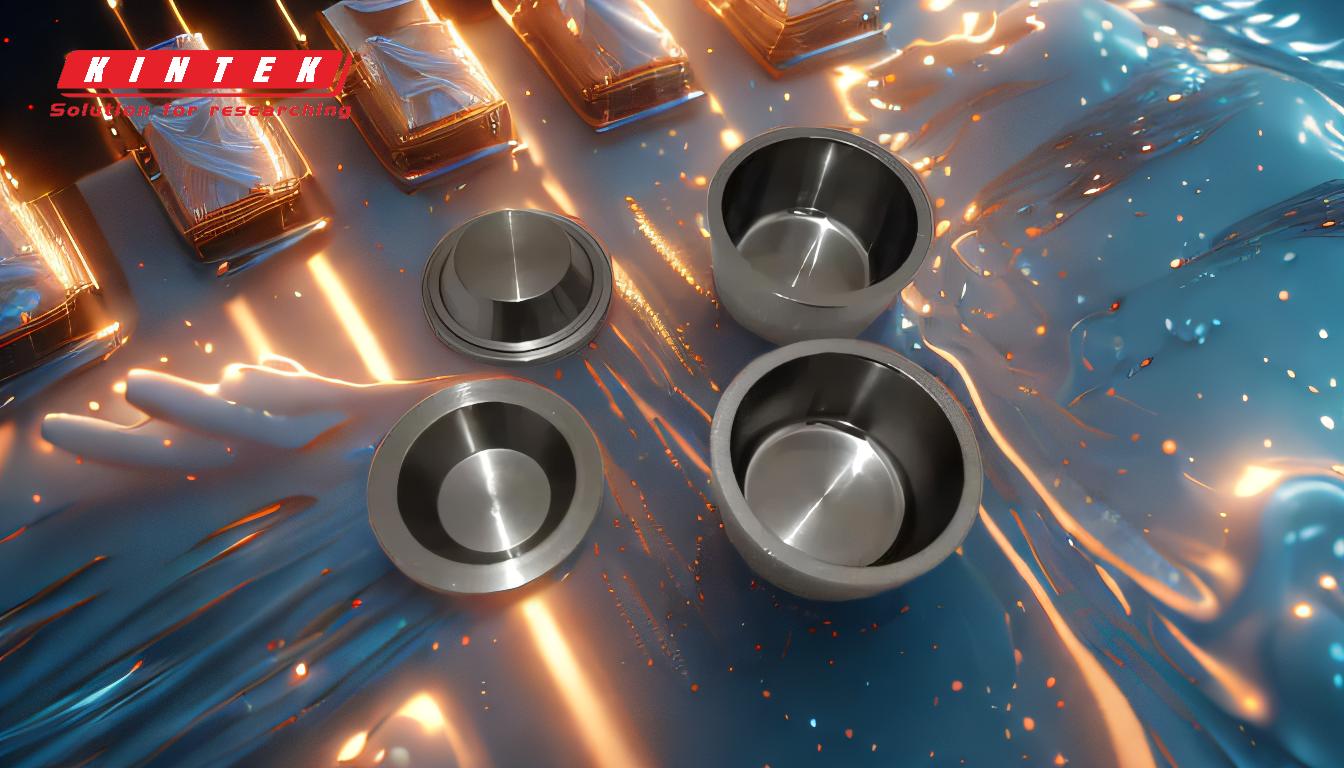
-
Réduction de la densité des particules et augmentation du trajet libre moyen:
- Dans un environnement sous vide, la densité des molécules de gaz est considérablement réduite. Cette réduction augmente le libre parcours moyen des particules, c'est-à-dire la distance moyenne parcourue par une particule avant d'entrer en collision avec une autre particule. Un trajet libre moyen plus long permet au matériau vaporisé d'atteindre directement le substrat sans être dispersé ou ralenti par les collisions avec les molécules de gaz. Cette trajectoire directe est cruciale pour obtenir des revêtements uniformes et de haute qualité.
-
Minimisation de la contamination:
- Un environnement sous vide réduit la présence d'atomes et de molécules indésirables, tels que l'oxygène, l'azote et la vapeur d'eau, qui peuvent contaminer le film déposé. Les contaminants peuvent dégrader la qualité du revêtement, entraînant des défauts, une adhérence réduite et des performances compromises. En maintenant un vide poussé, le procédé garantit un environnement plus propre et mieux contrôlé, ce qui est particulièrement important pour des applications telles que la fabrication de puces électroniques, où même d'infimes contaminants peuvent causer des problèmes importants.
-
Composition contrôlée des gaz et des vapeurs:
- Le vide permet de contrôler avec précision la composition des gaz et des vapeurs dans la chambre de traitement. Ce contrôle est essentiel pour adapter les propriétés du film déposé, telles que son épaisseur, son uniformité et sa composition chimique. En ajustant la pression et la composition des gaz, les fabricants peuvent obtenir les propriétés spécifiques requises pour différentes applications, telles que les revêtements optiques, les couches résistantes à l'usure ou les films conducteurs.
-
Taux d'évaporation thermique élevé:
- Dans le vide, le taux d'évaporation thermique des matériaux est nettement plus élevé que dans les conditions atmosphériques. En effet, la pression réduite abaisse le point d'ébullition des matériaux, ce qui leur permet de se vaporiser à des températures plus basses. Un taux d'évaporation élevé garantit un transfert et un dépôt efficaces des matériaux, ce qui est essentiel pour obtenir l'épaisseur et la qualité de film souhaitées dans un délai raisonnable.
-
Amélioration de l'adhérence des matériaux:
- L'absence d'air ou d'autres fluides dans un environnement sous vide permet au matériau vaporisé d'atteindre le substrat avec plus d'énergie. Cette énergie accrue améliore l'adhérence du matériau au substrat, ce qui permet d'obtenir un revêtement plus solide et plus durable. L'amélioration de l'adhérence est particulièrement importante pour les applications où le revêtement est soumis à des contraintes mécaniques, à des cycles thermiques ou à des environnements corrosifs.
-
Processus de dépôt répétable et contrôlé:
- Un environnement sous vide offre un processus stable et reproductible, ce qui est essentiel pour les applications industrielles. En maintenant des conditions de pression et de température constantes, les fabricants peuvent obtenir des revêtements uniformes aux propriétés prévisibles. Cette répétabilité est cruciale pour la production de masse, où la cohérence et le contrôle de la qualité sont primordiaux.
-
Environnement plasma basse pression:
- Le vide facilite la création d'un environnement plasma à basse pression, souvent utilisé dans les procédés PVD tels que la pulvérisation. Le plasma renforce l'ionisation du matériau vaporisé, améliorant ainsi l'énergie et la direction des particules qui se déposent sur le substrat. Il en résulte une meilleure densité, une meilleure adhérence et une meilleure qualité générale du film.
-
Exigences spécifiques à l'application:
- Certaines applications, telles que la production de micropuces, de CD et de DVD, nécessitent des environnements extrêmement propres et contrôlés. Un vide poussé permet d'éliminer les plus petites particules, évitant ainsi les défauts qui pourraient compromettre la fonctionnalité du produit final. Ce niveau de propreté est impossible à atteindre dans des conditions atmosphériques.
En résumé, il est essentiel d'effectuer le dépôt en phase vapeur dans un environnement sous vide pour obtenir des revêtements de haute qualité, uniformes et exempts de contamination. Le vide fournit les conditions nécessaires à un transfert efficace des matériaux, à un dépôt contrôlé et à une meilleure adhérence, ce qui le rend indispensable pour une large gamme d'applications industrielles et technologiques.
Tableau récapitulatif :
Principaux avantages | Description |
---|---|
Réduction de la contamination | Minimise les atomes/molécules indésirables, garantissant des revêtements plus propres et de meilleure qualité. |
Augmentation du trajet libre moyen | Améliore la distance de déplacement des particules pour un dépôt uniforme et précis. |
Gaz contrôlé Composition | Permet de personnaliser les propriétés du film telles que l'épaisseur, l'uniformité et la composition chimique. |
Taux d'évaporation thermique élevé | Permet un transfert efficace des matériaux et une déposition plus rapide. |
Adhésion renforcée | Améliore la résistance et la durabilité du revêtement pour les applications exigeantes. |
Processus répétable | Garantit des résultats cohérents et prévisibles pour la production de masse. |
Environnement plasma basse pression | Améliore la densité et la qualité des films grâce à une meilleure ionisation. |
Propreté spécifique à l'application | Répond aux exigences strictes des industries telles que la microélectronique et l'optique. |
Vous avez besoin d'une solution PVD sous vide pour vos besoins de fabrication ? Contactez-nous dès aujourd'hui pour en savoir plus !