L'augmentation de la température pendant le forgeage est un aspect critique du processus de transformation des métaux, car elle a une incidence directe sur les propriétés du matériau et la facilité de mise en forme.Le forgeage consiste à déformer le métal pour lui donner la forme souhaitée à l'aide de forces de compression, et la température joue un rôle essentiel dans la réussite de ce processus.Chauffer le métal à haute température le rend plus malléable, réduit la force nécessaire à la déformation et minimise le risque de fissure ou de rupture.En outre, les températures élevées permettent d'affiner la structure du grain, ce qui améliore les propriétés mécaniques du produit final.Comprendre les raisons de l'augmentation de la température pendant le forgeage permet d'optimiser le processus en termes d'efficacité et de qualité.
Explication des points clés :
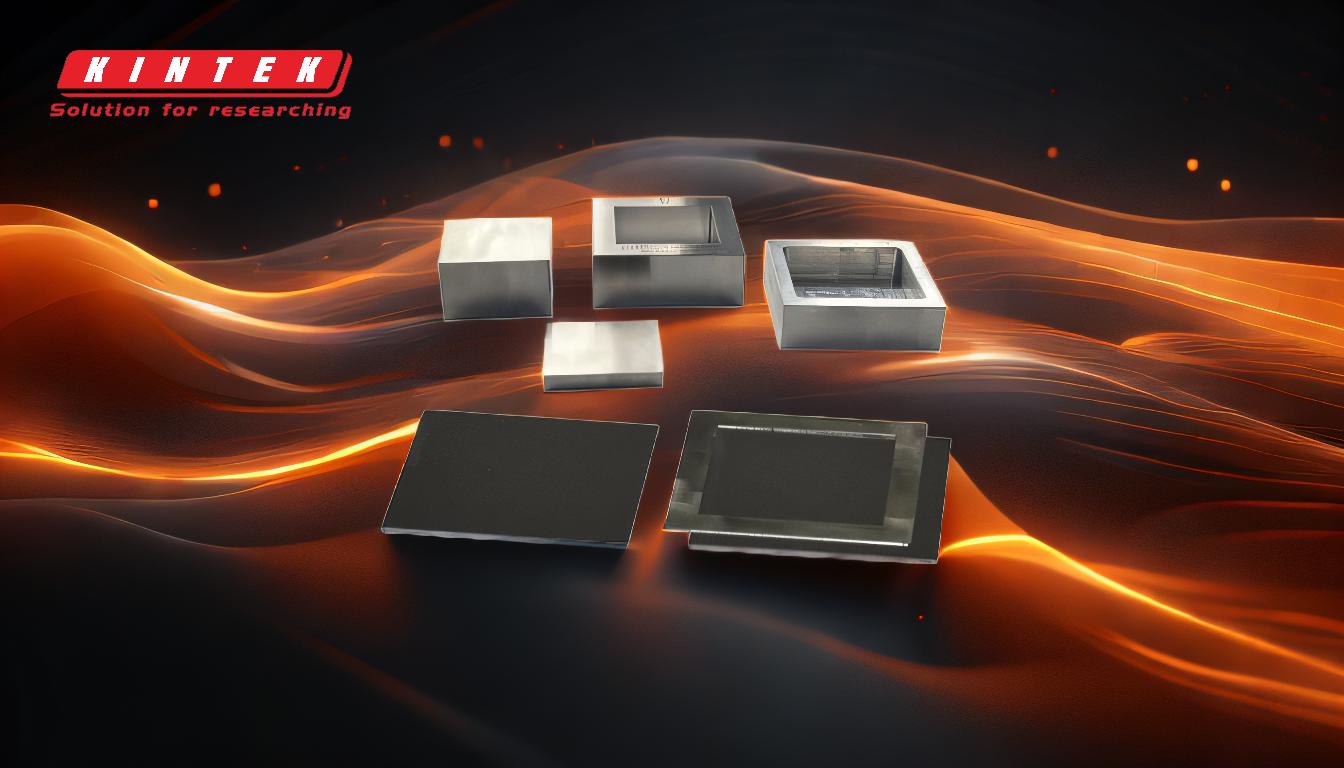
-
Amélioration de la malléabilité et réduction des exigences en matière de force:
- Les métaux deviennent plus ductiles et plus faciles à façonner lorsqu'ils sont chauffés.En effet, l'énergie thermique rompt les liaisons atomiques, ce qui permet au métal de se déformer plus facilement sous la pression.
- À des températures plus élevées, la limite d'élasticité du métal diminue, ce qui signifie qu'il faut moins de force pour obtenir la déformation souhaitée.Cela réduit l'usure des équipements de forgeage et la consommation d'énergie.
-
Prévention des fissures et des défaillances:
- Le forgeage à froid (forgeage à température ambiante ou proche de celle-ci) peut entraîner une fragilité et des fissures, en particulier dans les métaux durs.Le chauffage du métal réduit les contraintes internes et prévient les fractures pendant la déformation.
- Les températures élevées garantissent une répartition plus uniforme des contraintes dans l'ensemble du matériau, ce qui minimise le risque de défaillances localisées.
-
Affinement de la structure du grain:
- Le chauffage du métal à sa température de recristallisation permet aux grains du matériau de se reformer en une structure plus fine et plus uniforme.Cela améliore les propriétés mécaniques de la pièce forgée, telles que la solidité, la ténacité et la résistance à la fatigue.
- Un contrôle adéquat de la température pendant le forgeage garantit que le flux de grain suit les contours de la forme finale, ce qui améliore la durabilité de la pièce.
-
Amélioration de la maniabilité des formes complexes:
- Des températures plus élevées permettent au métal de s'écouler plus facilement dans des moules ou des matrices complexes, ce qui permet de forger des géométries complexes avec précision.
- Ceci est particulièrement important pour les industries telles que l'aérospatiale et l'automobile, où les composants nécessitent souvent des conceptions complexes et des tolérances serrées.
-
Efficacité énergétique et optimisation des processus:
- Bien que le chauffage nécessite de l'énergie, le processus global devient plus efficace car moins de force mécanique est nécessaire pour façonner le métal.Cela permet d'équilibrer l'apport et la production d'énergie, ce qui rend le processus plus durable.
- Une bonne gestion de la température réduit également le nombre d'étapes de forgeage nécessaires, ce qui permet d'économiser du temps et des ressources.
-
Considérations spécifiques aux matériaux:
- Les températures de forgeage varient d'un métal à l'autre.Par exemple, l'acier est généralement forgé à des températures comprises entre 950°C et 1250°C, tandis que les alliages d'aluminium sont forgés à des températures plus basses (environ 350°C à 500°C).
- Comprendre les exigences de température spécifiques à chaque matériau permet d'obtenir des résultats optimaux et d'éviter la surchauffe, qui peut dégrader les propriétés du métal.
-
Impact sur la qualité du produit final:
- La température pendant le forgeage affecte directement la microstructure et les propriétés mécaniques du produit final.Un chauffage adéquat garantit une finition de haute qualité avec un minimum de défauts.
- Un contrôle constant de la température tout au long du processus est essentiel pour obtenir une uniformité des propriétés de la pièce forgée.
En résumé, l'augmentation de la température pendant le forgeage est essentielle pour améliorer la maniabilité du métal, prévenir les défauts et améliorer les propriétés mécaniques du produit final.En contrôlant soigneusement la température, les fabricants peuvent obtenir des processus de forgeage efficaces et de haute qualité, adaptés aux exigences spécifiques du matériau et au résultat souhaité.
Tableau récapitulatif :
Bénéfice principal | Explication |
---|---|
Amélioration de la malléabilité | Le chauffage des métaux les rend plus ductiles, réduisant ainsi la force nécessaire à leur déformation. |
Prévient les fissures et les défaillances | Les températures élevées réduisent les contraintes internes et préviennent les fractures. |
Affinement de la structure du grain | Améliore la solidité, la ténacité et la résistance à la fatigue. |
Amélioration de l'usinabilité des formes complexes | Permet de forger avec précision des modèles complexes. |
Efficacité énergétique | Réduit les besoins en force mécanique, en équilibrant l'apport et la production d'énergie. |
Considérations spécifiques aux matériaux | Différents métaux ont des plages de températures de forgeage optimales pour obtenir les meilleurs résultats. |
Impact sur la qualité du produit final | Garantit une finition de haute qualité avec un minimum de défauts et des propriétés uniformes. |
Prêt à optimiser votre processus de forgeage ? Contactez nos experts dès aujourd'hui pour des solutions sur mesure !