L'ammoniac est utilisé dans le processus de recuit principalement parce qu'il peut être dissocié en un mélange gazeux composé de 75 % d'hydrogène et de 25 % d'azote, ce qui présente plusieurs avantages.L'hydrogène, un composant clé de ce mélange, a un coefficient de transfert de chaleur élevé, ce qui rend le processus de recuit plus efficace.En outre, l'hydrogène contenu dans l'ammoniac dissocié empêche l'oxydation, ce qui garantit l'intégrité des matériaux traités.L'utilisation de l'ammoniac dissocié est également rentable par rapport à l'hydrogène pur, ce qui en fait un choix pratique pour les applications industrielles.Cette combinaison d'efficacité, de protection et de rentabilité fait de l'ammoniac une ressource précieuse dans les processus de recuit.
Explication des points clés :
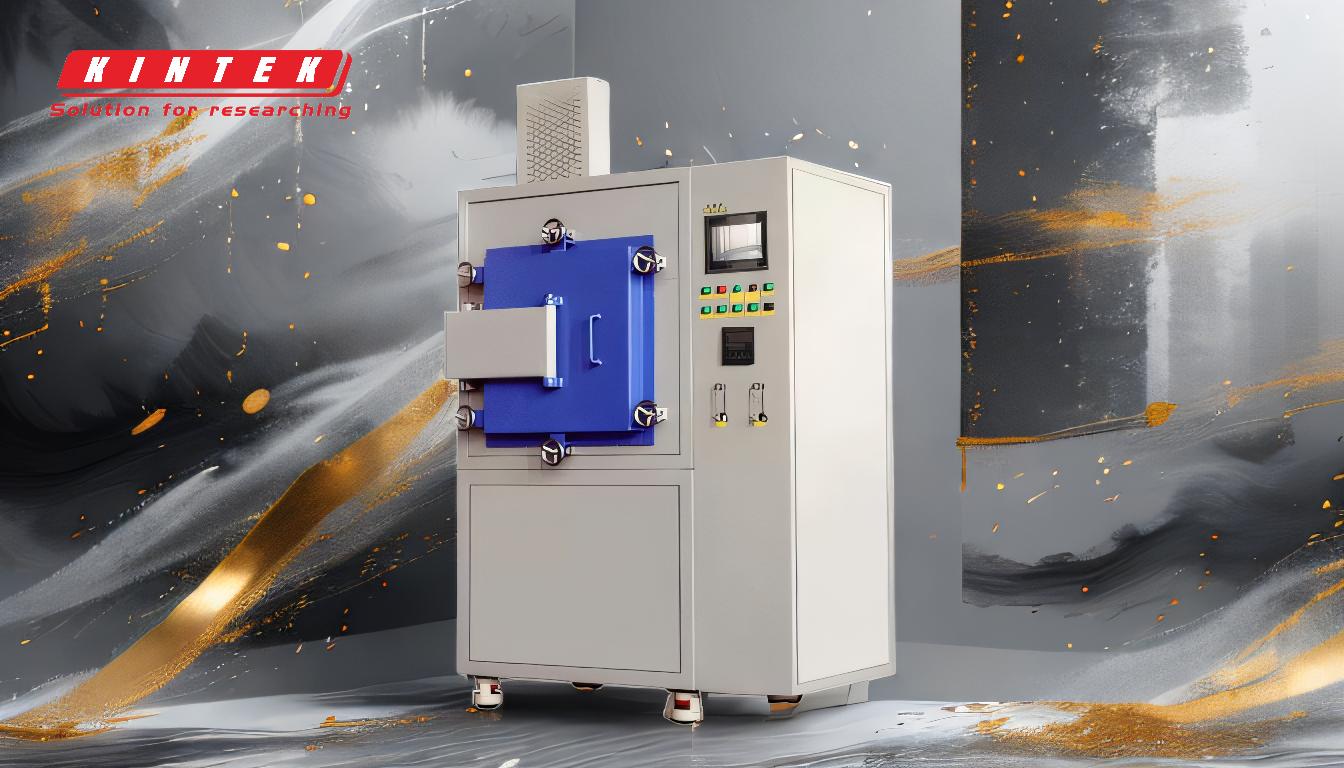
-
Dissociation de l'ammoniac:
- L'ammoniac peut être dissocié (craqué) en un mélange gazeux contenant 75 % d'hydrogène et 25 % d'azote.
- Ce processus de dissociation fait de l'ammoniac une source polyvalente d'hydrogène et d'azote, qui sont essentiels dans divers processus de traitement thermique, y compris le recuit.
-
Rôle de l'hydrogène dans le recuit:
- L'hydrogène, un composant majeur de l'ammoniac dissocié, a un coefficient de transfert de chaleur élevé, ce qui améliore l'efficacité du processus de recuit.
- Un transfert de chaleur efficace garantit un chauffage et un refroidissement uniformes des matériaux, ce qui est essentiel pour obtenir les propriétés mécaniques souhaitées et réduire les contraintes internes.
-
Prévention de l'oxydation:
- L'hydrogène contenu dans l'ammoniac dissocié agit comme un agent réducteur, empêchant l'oxydation des matériaux pendant le processus de recuit.
- L'oxydation peut entraîner des défauts de surface et une dégradation des propriétés des matériaux. L'atmosphère protectrice fournie par l'hydrogène est donc essentielle au maintien de l'intégrité des matériaux.
-
Rapport coût-efficacité:
- L'ammoniac dissocié offre de nombreux avantages par rapport à l'hydrogène pur, mais à un coût moindre.
- Cet avantage financier en fait une option intéressante pour les applications industrielles nécessitant de grands volumes de gaz.
-
Polyvalence et praticité:
- L'ammoniac peut être produit et stocké sous différentes formes (gaz généré, gaz en bouteille ou gaz stocké en vrac), ce qui en fait un choix flexible et pratique pour différentes installations industrielles.
- Sa capacité à servir deux objectifs (comme source d'azote pour la nitruration et d'hydrogène pour la réduction) ajoute à sa polyvalence dans les processus de traitement thermique.
-
Application au traitement thermique des pièces moulées et soudées:
- L'utilisation de l'ammoniac dissocié est particulièrement bénéfique pour le traitement thermique des composants moulés et soudés, où un transfert de chaleur efficace et la prévention de l'oxydation sont cruciaux.
- Ces composants nécessitent souvent un traitement thermique précis pour obtenir les propriétés mécaniques et l'intégrité structurelle souhaitées.
En tirant parti des propriétés de l'ammoniac dissocié, les industries peuvent mettre en place des processus de recuit efficaces et rentables, garantissant des résultats de haute qualité pour les matériaux traités.
Tableau récapitulatif :
Bénéfice principal | Explication |
---|---|
Dissociation de l'ammoniac | L'ammoniac se dissocie en 75 % d'hydrogène et 25 % d'azote, ce qui est idéal pour le traitement thermique. |
Transfert de chaleur efficace | Le coefficient élevé de transfert de chaleur de l'hydrogène assure un chauffage et un refroidissement uniformes. |
Prévention de l'oxydation | L'hydrogène agit comme un agent réducteur, protégeant les matériaux de l'oxydation. |
Rapport coût-efficacité | L'ammoniac dissocié est plus économique que l'hydrogène pur pour une utilisation industrielle. |
Polyvalence | L'ammoniac sert deux objectifs : l'hydrogène pour la réduction et l'azote pour la nitruration. |
Applications industrielles | Idéal pour le traitement thermique des pièces moulées et soudées, garantissant l'intégrité des matériaux. |
Optimisez votre processus de recuit avec l'ammoniac dissocié. contactez-nous dès aujourd'hui pour en savoir plus !