Comprendre le pressage à chaud
Table des matières
- Comprendre le pressage à chaud
- Définition et procédé du pressage à chaud
- Utilisation et application principales
- Densification par réarrangement des particules et écoulement plastique
- Utilisation des moules en graphite et températures de chauffage
- Pressions impliquées dans le processus
- Pressage à chaud dans l'industrie des polymères
- Types de chauffage en pressage à chaud
- Introduction à trois types de chauffage : chauffage par induction, chauffage par résistance indirecte et technique de frittage assisté sur site (FAST) / pressage direct à chaud
- Chauffage inductif
- Chauffage par résistance indirecte
- Technique de frittage assisté sur site (FAST) / Pressage à chaud direct
- Chauffage inductif
- Chauffage par résistance indirecte
- Technique de frittage assisté sur site (FAST) / Pressage à chaud direct
- Applications du pressage à chaud
- Fabrication d'articles critiques tels que des cibles de pulvérisation et des composants céramiques hautes performances
- Avantages de l'utilisation de poudre métallique
- Adéquation du procédé à des vitesses de chauffe élevées
- Rôle du pressage direct à chaud dans l'industrie des matériaux de friction
- Applications des plaquettes de frein frittées et des disques d'embrayage
Définition et procédé du pressage à chaud
Le pressage à chaud est un procédé de métallurgie des poudres à haute pression et à faible taux de déformation utilisé pour former de la poudre ou un compact de poudre à haute température afin d'induire des processus de frittage et de fluage. Cela implique l’application simultanée de chaleur et de pression pour fabriquer des matériaux durs et cassants.
Utilisation et application principales
Le pressage à chaud est principalement utilisé dans la consolidation d’outils de coupe composites diamant-métal, de céramiques techniques et d’autres matériaux durs et cassants. Cela fonctionne par réarrangement des particules et écoulement plastique au niveau des contacts des particules. La poudre libre ou la partie pré-compactée est versée dans un moule en graphite, permettant un chauffage par induction ou par résistance jusqu'à des températures typiquement de 2 400 °C (4 350 °F). Des pressions allant jusqu'à 50 MPa (7 300 psi) peuvent être appliquées. Le pressage à chaud est également utilisé dans le pressage de différents types de polymères.
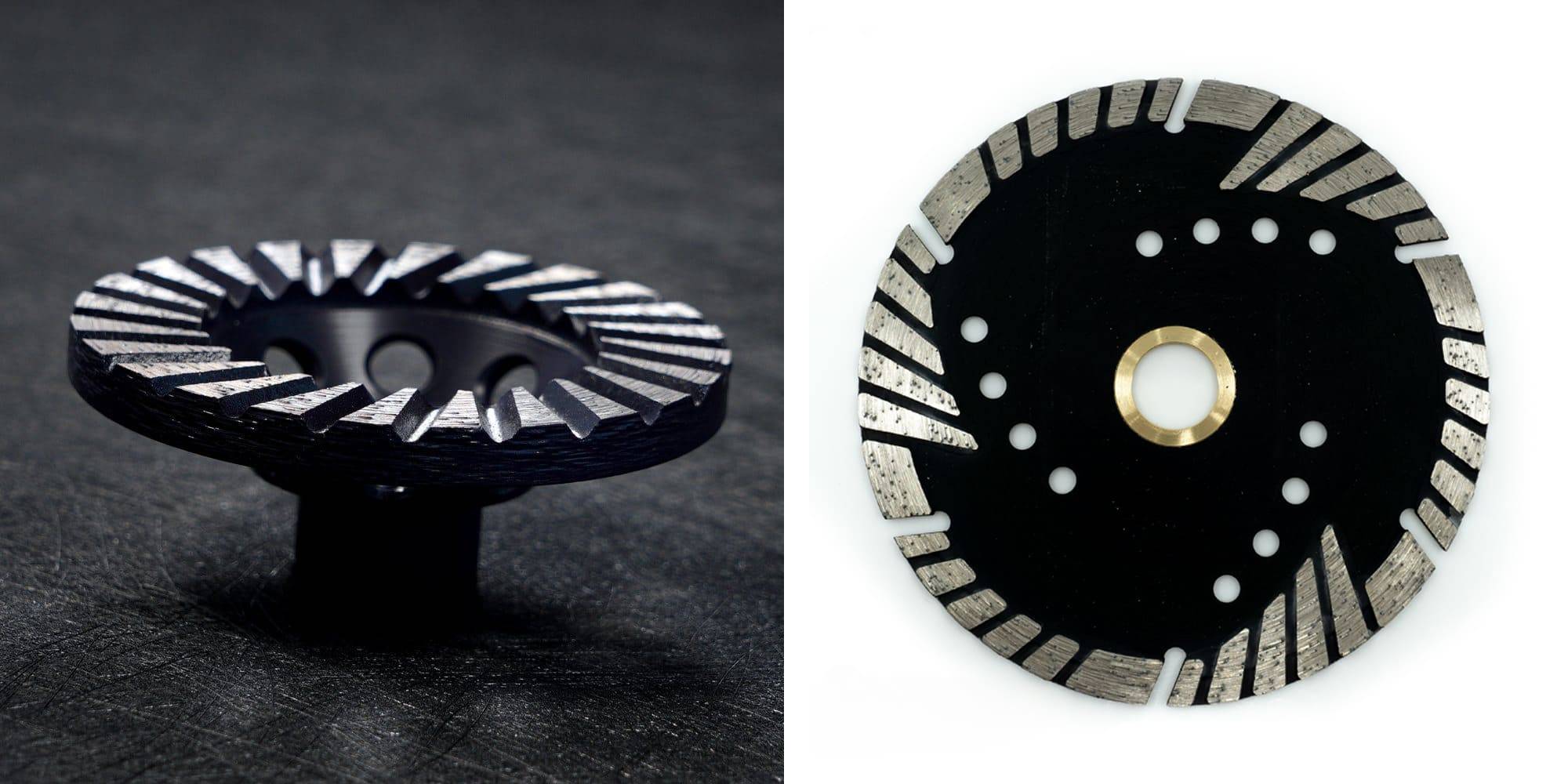
Diamants pressés à chaud
Densification par réarrangement des particules et écoulement plastique
Le processus de densification lors du pressage à chaud se produit par réarrangement des particules et écoulement de plastique au niveau des contacts des particules. La pression externe appliquée lors du pressage à chaud provoque la destruction des défauts internes et des pores, entraînant le contact des surfaces internes les unes avec les autres. Le matériau subit ensuite un fluage à haute température, permettant une pénétration mutuelle et une liaison par diffusion, éliminant complètement les défauts et la porosité.
Utilisation des moules en graphite et températures de chauffage
En pressage à chaud, un moule en graphite est couramment utilisé pour contenir la poudre libre ou la pièce précompactée. Le moule en graphite permet un chauffage efficace par induction ou par résistance. Les températures utilisées en pressage à chaud peuvent atteindre jusqu'à 2 400 °C (4 350 °F), assurant les processus de frittage et de fluage nécessaires à la densification.
Pressions impliquées dans le processus
Le pressage à chaud implique l’application de hautes pressions pour obtenir une densification. Des pressions allant jusqu'à 50 MPa (7 300 psi) peuvent être appliquées pendant le processus de pressage à chaud. La haute pression facilite le réarrangement des particules et l'écoulement du plastique, ce qui donne un produit final compact et dense.
Pressage à chaud dans l'industrie des polymères
Le pressage à chaud est également largement utilisé dans l’industrie des polymères. En utilisant la technique de pressage à chaud, les fabricants peuvent éliminer le besoin de liants dans leur processus de fabrication et utiliser à la place la combinaison de force et de température pour lier complètement leurs pièces. Cela permet la production de produits polymères de haute qualité avec des propriétés mécaniques et une précision dimensionnelle améliorées.
En résumé, le pressage à chaud est un procédé de métallurgie des poudres utilisé pour fabriquer des matériaux durs et cassants. Cela implique l’application de chaleur et de pression pour induire des processus de frittage et de fluage, entraînant une densification. Le pressage à chaud est largement utilisé dans diverses industries, notamment l’aérospatiale, la céramique et la fabrication de polymères. Le processus utilise un moule en graphite et peut atteindre des températures et des pressions élevées pour obtenir les résultats souhaités.
Types de chauffage en pressage à chaud
Introduction à trois types de chauffage : chauffage par induction, chauffage par résistance indirecte et technique de frittage assisté sur site (FAST) / pressage direct à chaud
Le pressage à chaud est une technique largement utilisée dans l’industrie manufacturière pour créer des liens durables et serrés entre les matériaux. Il s'agit de la combinaison d'une force ajoutée lors du frittage de matériaux à haute température, soit sous vide, soit sous une pression positive de gaz inerte. Cette pression contribue à la densification accrue du matériau, ce qui donne lieu à une billette de matériau dont les densités sont proches de la théorie.
Il existe deux principaux types de fours de pressage à chaud : ceux qui utilisent des tiges chaudes et froides pour appliquer la pression et ceux qui utilisent des poinçons et des matrices en graphite ou des plateaux de pressage pour exercer la force lors du collage par diffusion. Ces fours éliminent le besoin de liants dans le processus de fabrication, ce qui les rend très efficaces.
Dans la technologie de pressage à chaud, trois types distincts de méthodes de chauffage sont utilisés : le chauffage par induction, le chauffage par résistance indirecte et la technique de frittage assisté sur site (FAST)/pressage à chaud direct.
Chauffage inductif
Le chauffage par induction est une méthode couramment utilisée pour le frittage du métal, de la céramique et de certaines poudres de composés intermétalliques de métaux réfractaires. Cela implique l’utilisation de l’induction électromagnétique pour générer de la chaleur au sein du matériau.
Dans ce processus, un courant alternatif traverse une bobine, créant un champ magnétique. Ce champ magnétique induit des courants de Foucault au sein du matériau, qui génèrent à leur tour de la chaleur. La chaleur est ensuite utilisée pour fritter le matériau et créer la liaison souhaitée.
Le chauffage inductif est connu pour son efficacité et sa précision. Il permet des vitesses de chauffage rapides et un contrôle précis de la répartition de la température, ce qui donne lieu à des liaisons de haute qualité. Il est particulièrement adapté aux matériaux à haute conductivité électrique.
Chauffage par résistance indirecte
Le chauffage par résistance indirecte est une autre méthode couramment utilisée dans le pressage à chaud. Cela implique l’utilisation d’une résistance électrique pour générer de la chaleur à l’intérieur du matériau.
Dans ce processus, un courant électrique traverse le matériau, provoquant une résistance et générant de la chaleur. La chaleur est ensuite utilisée pour fritter le matériau et créer la liaison souhaitée.
Le chauffage par résistance indirecte est connu pour sa simplicité et sa polyvalence. Il peut être utilisé avec une large gamme de matériaux et convient particulièrement aux matériaux à faible conductivité électrique. Il permet un contrôle précis de la température et peut atteindre des vitesses de chauffage élevées.
Technique de frittage assisté sur site (FAST) / Pressage à chaud direct
La technique de frittage assisté sur site (FAST), également connue sous le nom de pressage direct à chaud, est une méthode relativement nouvelle utilisée dans le pressage à chaud. Cela implique l’utilisation d’un champ électrique pour faciliter le processus de frittage.
Dans ce processus, un courant électrique traverse le matériau, créant ainsi un champ électrique. Ce champ électrique améliore la mobilité des atomes au sein du matériau, permettant un frittage et une densification accélérés.
Le pressage à chaud RAPIDE/direct est connu pour sa capacité à produire des matériaux très denses et uniformes. Il permet des vitesses de frittage rapides et peut atteindre des densités élevées proches de la théorie. Il est particulièrement adapté aux matériaux à faible diffusivité et à haute conductivité électrique.
En conclusion, le pressage à chaud est une technique précieuse dans l’industrie manufacturière pour créer des liens durables et serrés entre les matériaux. Dans la technologie de pressage à chaud, trois types de méthodes de chauffage sont couramment utilisés : le chauffage par induction, le chauffage par résistance indirecte et la technique de frittage assisté sur site (FAST)/pressage à chaud direct. Chaque méthode présente ses propres avantages et convient à différents matériaux et applications.
Chauffage inductif
Processus et fonctionnement du chauffage inductif
Le chauffage inductif est le processus de chauffage de matériaux électriquement conducteurs, tels que des métaux ou des semi-conducteurs, par induction électromagnétique. Ceci est réalisé en faisant passer un courant alternatif haute fréquence à travers un électro-aimant, créant un champ magnétique alternatif rapide. Ce champ magnétique induit des courants de Foucault au sein du matériau, qui traversent sa résistance et génèrent de la chaleur par chauffage Joule. Dans les matériaux ferromagnétiques et ferrimagnétiques, la chaleur est également générée par les pertes par hystérésis magnétique. La fréquence du courant électrique utilisé dépend de facteurs tels que la taille et le matériau de l'objet, le couplage entre la bobine de travail et l'objet et la profondeur de pénétration.
Cette méthode de chauffage est couramment utilisée pour faire fondre des métaux et fabriquer des alliages. La fusion par induction sous vide, qui combine atmosphère contrôlée et contrôle précis du processus de fusion, est une application populaire du chauffage par induction. Les fours à induction peuvent atteindre des températures de 1 800 ºC ou plus et se composent généralement d'un refroidisseur, d'une unité de puissance et d'une unité de vide.
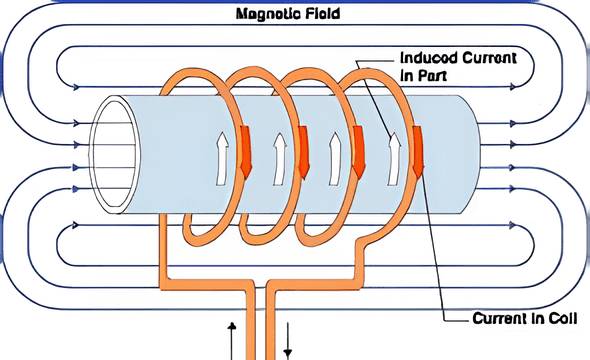
Avantages et inconvénients du chauffage inductif
Le chauffage inductif offre plusieurs avantages par rapport aux autres méthodes de chauffage. C'est un processus plus rapide que le chauffage électrique ou au gaz, grâce à son principe d'induction. Les fours à induction ont également un temps de démarrage rapide, car ils ne nécessitent pas de cycle de préchauffage ou de refroidissement. L'alimentation par induction crée une forte action d'agitation, résultant en des mélanges homogènes de métal liquide. De plus, les fours à induction nécessitent moins de matériaux réfractaires que les appareils alimentés au combustible. Ils sont plus économes en énergie et capables de réduire la consommation d’énergie nécessaire à la fusion des métaux. Les fours à induction sont également de taille compacte, ce qui permet une installation plus facile et permet des taux de production plus élevés grâce à des temps de fusion plus courts.
Cependant, il existe également certains inconvénients à prendre en compte. La puissance nominale des fours à induction ne reflète pas toujours leur puissance de fonctionnement réelle, ce qui entraîne une efficacité de fusion réduite. Il est important de s'assurer que le fournisseur dispose d'une technologie de carte de puissance à induction auto-développée et qu'il peut fournir des solutions personnalisées flexibles. De plus, le chauffage par induction peut poser des problèmes de distribution de chaleur et de vitesse de chauffage, nécessitant un examen attentif de l'application spécifique et du matériau à chauffer.
Problèmes de distribution de chaleur et de vitesse de chauffage
Le chauffage par induction peut produire des densités de puissance élevées, permettant des temps d’interaction courts pour atteindre la température requise. Il en résulte un contrôle strict du modèle de chauffage, suivant de près le champ magnétique appliqué. Ce contrôle précis permet de réduire la distorsion thermique et les dommages causés au matériau chauffé.
Cependant, la distribution de la chaleur et la vitesse de chauffage peuvent constituer des problèmes potentiels dans le chauffage par induction. Une distribution inégale de la chaleur peut se produire si la bobine d'induction n'est pas en contact approprié avec le matériau ou si le matériau a une forme ou une composition irrégulière. Il est important d'assurer un bon couplage entre la bobine de travail et l'objet à chauffer pour obtenir un chauffage uniforme.
La vitesse de chauffage peut également être influencée par des facteurs tels que la taille et le matériau de l'objet, ainsi que la profondeur de pénétration du champ électromagnétique. Comprendre ces facteurs et leur impact sur le processus de chauffage est crucial pour obtenir les résultats souhaités dans les applications de chauffage par induction.
Dans l’ensemble, le chauffage par induction est une méthode polyvalente et efficace pour chauffer des matériaux électriquement conducteurs. Ses avantages en termes de vitesse, d’efficacité énergétique et de contrôlabilité en font un choix populaire dans diverses industries, notamment la métallurgie, la fabrication de semi-conducteurs et la fonderie d’or. En tenant compte des exigences et des défis spécifiques de chaque application, les entreprises peuvent prendre des décisions éclairées lorsqu'elles utilisent la technologie de chauffage par induction.
Chauffage par résistance indirecte
Le chauffage par résistance indirecte est une technologie utilisée dans les fours électriques qui consiste à chauffer un moule ou une charge à l'aide d'éléments chauffants en graphite. La chaleur est générée en faisant passer un courant électrique à travers ces éléments, qui la transfèrent ensuite au moule par convection. Ce processus est connu sous le nom de chauffage par résistance indirecte.
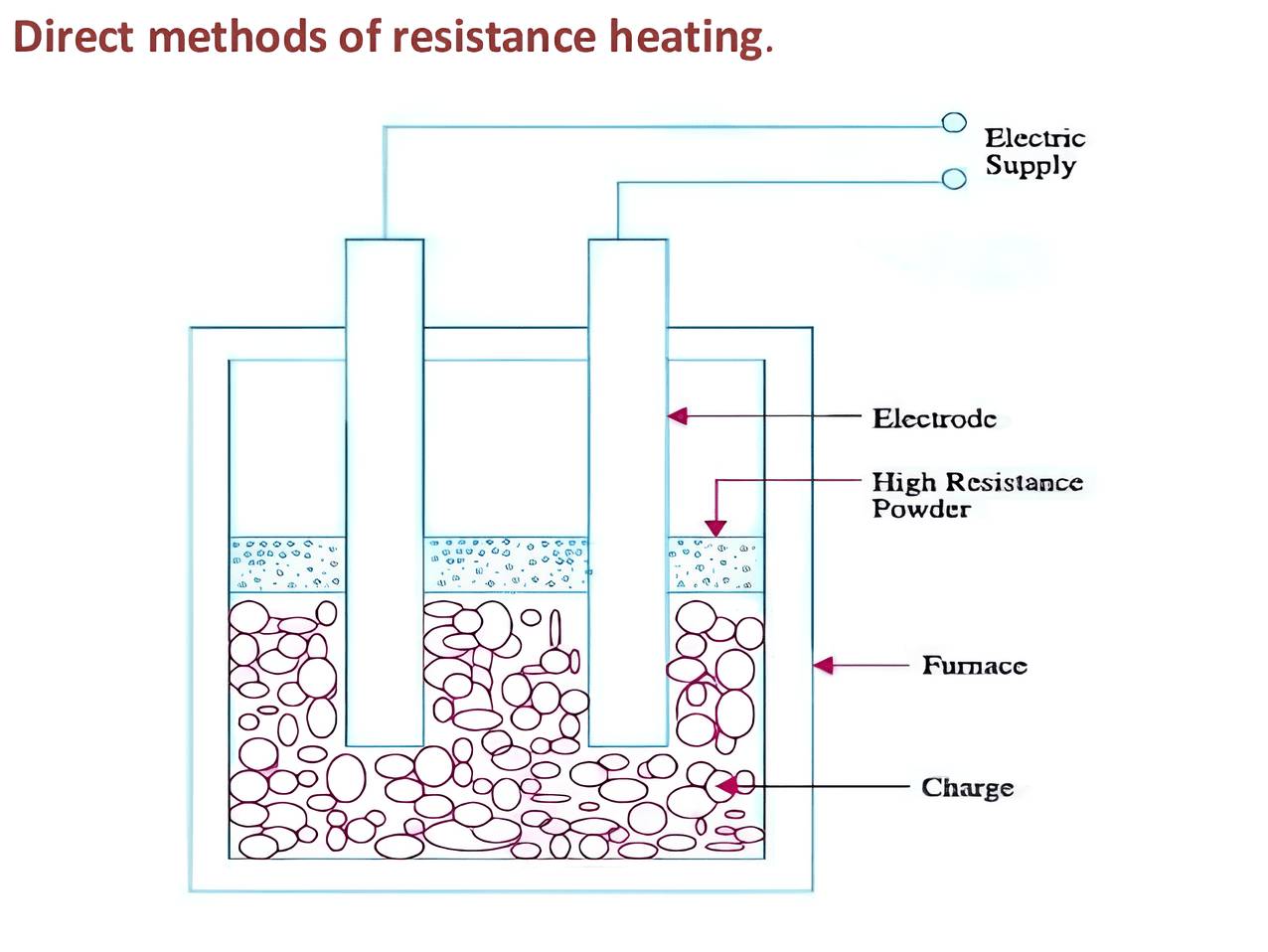
Processus et fonctionnement du chauffage par résistance indirecte
Lors du chauffage par résistance indirecte, le moule est placé dans une chambre de chauffage où se trouvent des éléments chauffants en graphite. Ces éléments sont chauffés par le courant électrique qui les traverse. La chaleur générée par les éléments chauffants est ensuite transférée au moule par convection, entraînant le chauffage du moule.
Avantages et inconvénients du chauffage par résistance indirecte
L’un des avantages du chauffage par résistance indirecte est la possibilité d’atteindre des températures élevées. La température atteinte est indépendante de la conductivité du moule et n'est pas affectée par la chaleur et la pression. Cependant, l’un des principaux inconvénients du chauffage par résistance indirecte est le temps nécessaire pour chauffer le moule. Le transfert de chaleur de l’atmosphère du four à la surface du moule et dans toute la section transversale du moule est relativement lent.
Histoire et intérêt actuel pour le chauffage par résistance
Le chauffage par résistance est utilisé depuis de nombreuses années dans diverses applications. Il est couramment utilisé dans les appareils électroménagers tels que les cuisinières électriques et les grille-pain. Ces dernières années, le chauffage par résistance a suscité un intérêt croissant pour les applications industrielles, telles que la technologie de pressage à chaud. Le chauffage par induction et la technique de frittage assisté sur site (FAST)/pressage à chaud direct sont d'autres méthodes de chauffage utilisées conjointement avec le chauffage par résistance.
Les éléments chauffants à résistance, tels que les fils ou rubans de résistance, sont couramment utilisés dans divers appareils de chauffage et fours industriels. Ces éléments convertissent l’énergie électrique en chaleur grâce au chauffage Joule. La résistance rencontrée par le courant électrique traversant l’élément entraîne l’échauffement de l’élément.
En conclusion, le chauffage par résistance indirecte est une technologie qui utilise des éléments chauffants en graphite pour chauffer un moule ou une charge par convection. Il offre des avantages tels que des températures élevées pouvant être atteintes, indépendamment de la conductivité du moule et de la chaleur/pression. Cependant, il présente l’inconvénient d’un transfert de chaleur relativement lent. Les éléments chauffants à résistance, tels que les fils à résistance, sont couramment utilisés dans divers appareils de chauffage et fours industriels.
Technique de frittage assisté sur site (FAST) / Pressage à chaud direct
Concept et réalisation de FAST
La technologie de frittage assisté sur site/frittage plasma par étincelle (FAST/SPS) utilise un courant électrique continu pour chauffer directement le moule et/ou l'échantillon par chauffage Joule. Ce chauffage direct permet d'obtenir des vitesses de chauffage élevées et des temps de cycle de traitement réduits. Il permet également la consolidation d'une large gamme de matériaux métalliques, céramiques et fonctionnels. FAST/SPS offre de nouvelles possibilités pour fabriquer des matériaux aux caractéristiques potentiellement extraordinaires. Il peut également traiter des composites multi-matériaux, des matériaux de qualité fonctionnelle et des matériaux à liaison par diffusion.
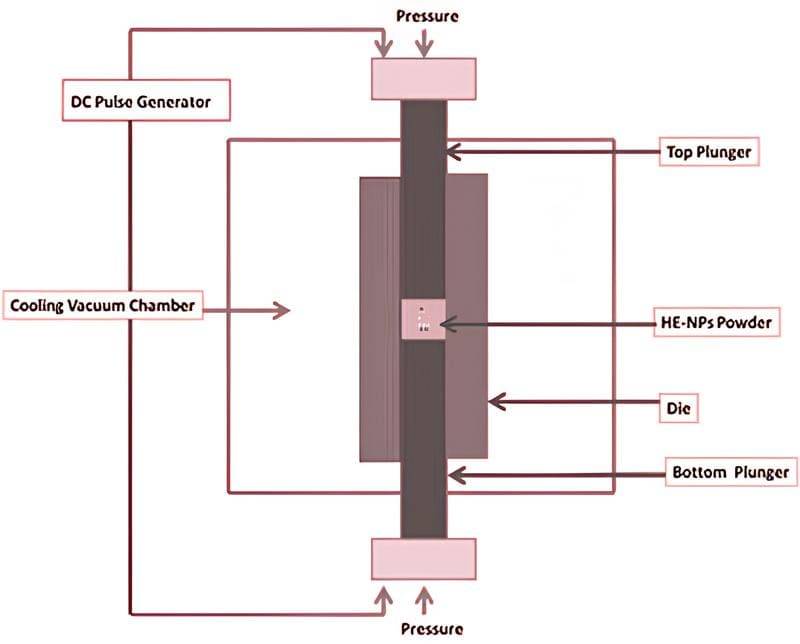
Raisons du raccourcissement du temps de cycle
La raison impérieuse de raccourcir la durée du cycle dans le pressage direct à chaud est d’éviter la croissance des grains et d’économiser de l’énergie. Lors du pressage direct à chaud, le moule est directement connecté à l'alimentation électrique, générant de la chaleur dans le moule grâce à la résistivité du moule et de la partie poudre. Cela entraîne des vitesses de chauffage très élevées et augmente considérablement l'activité de frittage des agrégats de poudres métalliques fines. Des temps de cycle courts de quelques minutes deviennent possibles et le processus abaisse la température et la pression seuil de frittage par rapport aux techniques de frittage conventionnelles. Le chauffage par résistance directe garantit que la chaleur est générée là où elle est nécessaire.
Avantages du pressage direct à chaud
Le pressage direct à chaud offre plusieurs avantages par rapport aux techniques conventionnelles de frittage de la métallurgie des poudres. Il permet la production de propriétés uniques en utilisant des températures de traitement plus basses et/ou des temps de traitement plus courts. Il permet le frittage par pressage à chaud de poudres métalliques et céramiques, la préparation de composites céramique/métal et de composés intermétalliques, ainsi que la recherche et le développement de procédés de soudage par diffusion. Il facilite également la densification par frittage à chaud des composés oxygène/azote/bore/carbone et de leurs mélanges.
Différences entre le frittage avec courant pulsé ou non pulsé
Les dernières recherches suggèrent qu'il n'y a pas de différence fondamentale entre le frittage avec un courant pulsé ou non (SPS ou FAST). En principe, toutes les techniques de pressage à chaud direct peuvent permettre d'obtenir des résultats de frittage améliorés par rapport au pressage à chaud conventionnel si l'amélioration est uniquement due au chauffage in situ de la poudre. Cependant, si des effets physiques supplémentaires associés à la densité de courant électrique elle-même sont présents, un courant pulsé a souvent des effets bénéfiques supplémentaires. En effet, lors de chaque impulsion, la densité du courant électrique atteint une valeur nettement supérieure à celle d'un courant continu avec une puissance de chauffage comparable.
En résumé, la technique de frittage assisté par champ (FAST) ou pressage direct à chaud utilisant un courant électrique continu offre de nombreux avantages en termes de temps de cycle de traitement plus courts, de températures et de pressions plus basses et de capacité à produire des propriétés uniques dans une large gamme de matériaux. Qu'elle utilise un courant pulsé ou non, la technique de pressage direct à chaud permet d'obtenir des résultats de frittage améliorés par rapport aux méthodes conventionnelles.
Applications du pressage à chaud
Fabrication d'articles critiques tels que des cibles de pulvérisation et des composants céramiques hautes performances
La technologie de pressage à chaud a été utilisée avec succès dans la fabrication d'articles critiques tels que des cibles de pulvérisation cathodique et des composants en céramique haute performance. Des matériaux comme le carbure de bore, le diborure de titane et le sialon ont été obtenus grâce à ce procédé. En utilisant de la poudre métallique, la conductivité du moule permet un chauffage rapide de la pièce. Cette méthode est particulièrement adaptée aux applications nécessitant des vitesses de chauffage élevées, ce qui la rend idéale pour les matériaux qui ne peuvent être maintenus à haute température que brièvement ou pour les processus nécessitant des vitesses de chauffage rapides pour une productivité élevée.
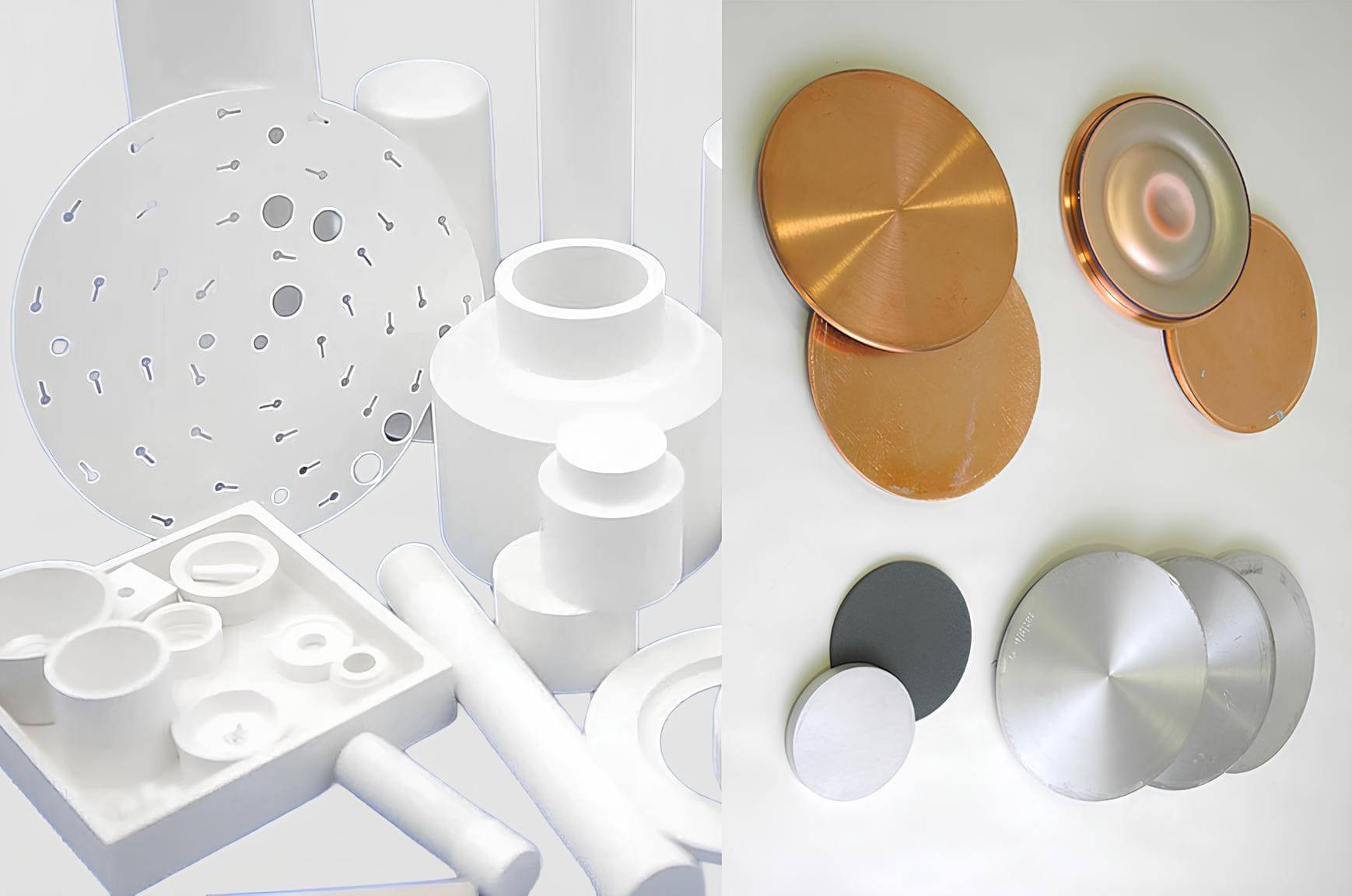
Avantages de l'utilisation de poudre métallique
L’un des avantages de l’utilisation de poudre métallique dans le processus de pressage à chaud est qu’elle permet un chauffage rapide de la pièce. Les moules de grand diamètre et de hauteur relativement faible peuvent être chauffés rapidement, ce qui entraîne une efficacité et une productivité accrues. De plus, l’utilisation de poudre métallique élimine le besoin de liants dans le processus de fabrication, permettant une liaison complète des pièces en utilisant une combinaison de force et de température.
Adéquation du procédé à des vitesses de chauffe élevées
Le procédé de pressage à chaud est particulièrement adapté aux applications nécessitant des vitesses de chauffage élevées. Ceci est avantageux pour les matériaux qui ne peuvent être maintenus à des températures élevées que brièvement ou pour les processus qui nécessitent des vitesses de chauffage rapides pour atteindre une productivité élevée. La combinaison de la force et de la température lors du pressage à chaud permet un collage rapide et efficace des pièces.
Rôle du pressage direct à chaud dans l'industrie des matériaux de friction
La technologie de pressage direct à chaud joue un rôle important dans l’industrie des matériaux de friction. Il permet aux matériaux d'être frittés jusqu'à leur densité finale, atteignant ainsi un haut niveau de précision de forme proche de la valeur nette. Cette précision élimine souvent le besoin de retravailler mécaniquement des matériaux difficiles à traiter. Le pressage direct à chaud est particulièrement utile pour les matériaux qui nécessitent un haut niveau de densité et de précision dans leur forme finale.
Applications des plaquettes de frein frittées et des disques d'embrayage
Le pressage à chaud est couramment utilisé dans la production de plaquettes de frein et de disques d'embrayage frittés. Le processus permet la création de matériaux denses et performants qui offrent des capacités supérieures de freinage et d’engagement d’embrayage. Les plaquettes de frein et disques d'embrayage frittés sont connus pour leur durabilité, leur résistance à la chaleur et leurs performances constantes, ce qui les rend très appréciés dans l'industrie automobile.
En conclusion, le pressage à chaud est un procédé polyvalent et précieux qui trouve des applications dans diverses industries. Il est particulièrement utile dans la fabrication d’articles critiques tels que des cibles de pulvérisation et des composants céramiques hautes performances. L'utilisation de poudre métallique dans le pressage à chaud offre des avantages tels qu'un chauffage rapide et l'élimination des liants. Le procédé convient aux vitesses de chauffage élevées et joue un rôle important dans l'industrie des matériaux de friction. De plus, le pressage à chaud est largement utilisé dans la production de plaquettes de frein et de disques d'embrayage frittés, offrant des performances et une durabilité supérieures dans les applications automobiles.
CONTACTEZ-NOUS POUR UNE CONSULTATION GRATUITE
Les produits et services de KINTEK LAB SOLUTION ont été reconnus par des clients du monde entier. Notre personnel se fera un plaisir de répondre à toute demande que vous pourriez avoir. Contactez-nous pour une consultation gratuite et parlez à un spécialiste produit pour trouver la solution la plus adaptée aux besoins de votre application !