Principes de base du procédé de revêtement PVD
Évaporation
Dans un environnement sous vide, le matériau solide, appelé cible, subit une transformation à l'état gazeux par le biais de diverses méthodes, principalement par chauffage. Ce processus, connu sous le nom d'évaporation, est fondamental pour le processus de revêtement par dépôt physique en phase vapeur (PVD). Plusieurs techniques sont utilisées pour réaliser cette transformation :
-
Évaporation thermique: Cette méthode consiste à chauffer le matériau cible jusqu'à sa température d'évaporation à l'aide d'une résistance électrique ou d'autres éléments chauffants. Lorsque le matériau atteint son point de vaporisation, il se transforme en gaz, qui se diffuse et se condense sur le substrat pour former un film mince.
-
Évaporation par faisceau d'électrons: Un faisceau d'électrons à haute énergie est dirigé vers le matériau cible, ce qui provoque son évaporation. Cette technique est particulièrement utile pour les matériaux ayant un point de fusion élevé, car l'effet de chauffage localisé permet un contrôle précis du processus d'évaporation.
-
Évaporation par laser: Cette méthode utilise des impulsions laser à haute énergie pour vaporiser le matériau cible. L'évaporation laser est avantageuse pour la préparation de matériaux complexes en couches minces, car elle offre une grande précision et peut être utilisée pour évaporer des matériaux difficiles à manipuler avec les méthodes traditionnelles.
Chacune de ces méthodes présente des avantages uniques et est choisie en fonction des exigences spécifiques du processus de revêtement, telles que le type de matériau utilisé et les propriétés souhaitées du film obtenu.
Le transport
Le matériau gazeux, une fois transformé à l'état de vapeur, subit une diffusion à l'intérieur de la chambre à vide. Cette diffusion est une phase critique du processus PVD, car elle influence directement l'uniformité et la qualité du dépôt ultérieur du film. Plusieurs facteurs clés ont un impact significatif sur cette phase de transport :
-
Pression du gaz: La pression dans la chambre à vide joue un rôle essentiel. Des pressions plus faibles améliorent généralement l'efficacité de la diffusion, garantissant que le matériau gazeux se propage plus uniformément sur le substrat. À l'inverse, des pressions plus élevées peuvent entraîner des collisions entre les molécules de gaz, ce qui risque de réduire le taux de diffusion global et d'affecter l'uniformité du film.
-
La température: La température de l'environnement sous vide est une autre variable cruciale. Des températures plus élevées peuvent accélérer le processus de diffusion, mais elles doivent être soigneusement contrôlées pour éviter tout dommage thermique au substrat ou la formation de dépôts non uniformes. Il est essentiel d'équilibrer la température avec les autres paramètres du processus pour obtenir une diffusion optimale.
-
Position du substrat: La disposition spatiale du substrat par rapport à la source de la matière gazeuse est également importante. Un alignement correct garantit que la matière gazeuse atteint toutes les zones du substrat de manière uniforme, évitant ainsi un surdépôt ou un sous-dépôt localisé. Des techniques telles que la rotation ou l'inclinaison du substrat peuvent aider à obtenir une couverture plus uniforme.
En résumé, le transport de matières gazeuses dans le vide est un processus nuancé qui nécessite un contrôle méticuleux de la pression du gaz, de la température et du positionnement du substrat pour garantir le dépôt réussi d'un film de haute qualité.
Dépôt
Pendant la phase de dépôt, le matériau gazeux, qui a été transporté jusqu'au substrat, commence à refroidir et à se condenser. Ce processus de refroidissement est crucial car il transforme le gaz en un film mince solide qui adhère à la surface du substrat. Le processus de dépôt n'est pas seulement un changement physique, mais aussi une transformation, qui modifie considérablement les propriétés du substrat en fonction de l'application spécifique.
Le type de gaz utilisé pendant le dépôt joue un rôle essentiel dans la détermination de la structure et des caractéristiques finales du film. Par exemple, les gaz inertes comme l'argon et l'hélium sont souvent utilisés pour maintenir la pureté du film, en veillant à ce qu'aucune réaction chimique indésirable ne se produise. D'autre part, des gaz réactifs tels que l'oxygène, l'azote et le fluor sont introduits pour créer des composés spécifiques tels que des oxydes, des nitrures et des fluorures, améliorant ainsi la fonctionnalité du film pour des applications particulières.
En outre, la pression du gaz dans la chambre de dépôt est un paramètre critique qui influence à la fois la vitesse de dépôt et la qualité du film. Des pressions de gaz plus faibles donnent généralement des films plus denses et plus homogènes, ce qui est souhaitable pour de nombreuses applications. Inversement, des pressions de gaz plus élevées peuvent conduire à des films plus rugueux, ce qui peut être bénéfique dans certains contextes, par exemple lorsqu'une surface accrue est nécessaire pour améliorer l'adhérence ou la réactivité.
En résumé, le processus de dépôt est une interaction sophistiquée entre le refroidissement, le type de gaz et la pression, chaque facteur étant méticuleusement contrôlé pour obtenir les propriétés de film souhaitées. Cette orchestration minutieuse garantit que le film mince obtenu répond aux normes rigoureuses exigées par diverses industries, de l'électronique à l'optique et au-delà.
Principaux types de procédés PVD
Dépôt par évaporation
Le dépôt par évaporation est une technique sophistiquée utilisée pour produire des couches minces en chauffant les matériaux cibles jusqu'à leur point de vaporisation. Ce procédé est particulièrement efficace pour les métaux et certains alliages, les faisant passer de l'état solide à l'état gazeux grâce à l'énergie thermique. Les atomes vaporisés se condensent ensuite sur le substrat, formant un film mince uniforme et conforme. Cette méthode est généralement utilisée dans un environnement sous vide poussé afin de minimiser les collisions et la contamination, garantissant ainsi la pureté et l'intégrité du film déposé.
L'un des principaux avantages du dépôt par évaporation est sa capacité à créer des films de haute qualité présentant une uniformité et une conformité excellentes. Cette technique est polyvalente et permet de déposer un large éventail de matériaux, notamment des métaux, des céramiques et des semi-conducteurs. Toutefois, le processus exige un vide poussé et est très sensible aux facteurs environnementaux, ce qui peut limiter son applicabilité dans certains scénarios.
Dépôt par pulvérisation cathodique
Le dépôt par pulvérisation est une technique sophistiquée de dépôt physique en phase vapeur (PVD) qui consiste à bombarder un matériau cible avec des particules à haute énergie, généralement des ions provenant d'un plasma. Ce bombardement provoque l'éjection d'atomes ou de molécules du matériau cible, qui se déplacent ensuite dans le vide et se condensent sur un substrat, formant un film mince. Ce procédé est polyvalent et s'applique à un large éventail de matériaux, notamment les métaux, les oxydes et les nitrures.
Lors du dépôt par pulvérisation cathodique, le matériau cible est exposé à un plasma, souvent composé d'ions argon et d'électrons. Ces particules énergétiques "arrachent" des atomes de la cible, créant ainsi un nuage d'atomes sources. Ce nuage se condense ensuite sur le substrat, où il forme un film mince. Le choix du matériau cible et les conditions du plasma influencent considérablement les caractéristiques du film déposé.
Un aspect notable du dépôt par pulvérisation cathodique est le phénomène de resputation, où le matériau déjà déposé peut être réémis par un bombardement ionique ou atomique ultérieur. Ce phénomène peut affecter l'uniformité et l'épaisseur du film, ce qui nécessite un contrôle minutieux des paramètres de dépôt pour obtenir les résultats souhaités.
Le dépôt par pulvérisation cathodique est largement utilisé dans diverses industries en raison de sa capacité à produire des films denses et de haute qualité avec une excellente adhérence au substrat. Elle est particulièrement appréciée pour son applicabilité à une large gamme de matériaux, ce qui en fait un outil polyvalent dans la fabrication de films minces avancés pour l'électronique, l'optique et les composants mécaniques.
Dépôt par laser pulsé (PLD)
Le dépôt par laser pulsé (PLD) est un processus d'évaporation sophistiqué qui utilise des impulsions laser à haute énergie pour vaporiser un matériau cible dans une chambre à vide. Cette méthode est particulièrement adaptée à la préparation de matériaux complexes en couches minces, ce qui en fait un choix privilégié pour diverses applications scientifiques et industrielles.
Le processus PLD commence par un faisceau laser ciblant le matériau, provoquant sa vaporisation et la formation d'un panache de plasma. Ce plasma se dépose ensuite sur un substrat, où il se condense pour former un film mince. La complexité de ce processus, qui comprend l'évaporation, l'ablation, la formation de plasma et l'exfoliation, nécessite une optimisation minutieuse. Malgré l'augmentation du temps et des efforts nécessaires pour gérer les nombreuses variables impliquées, le dépôt par laser pulsé offre plusieurs avantages.
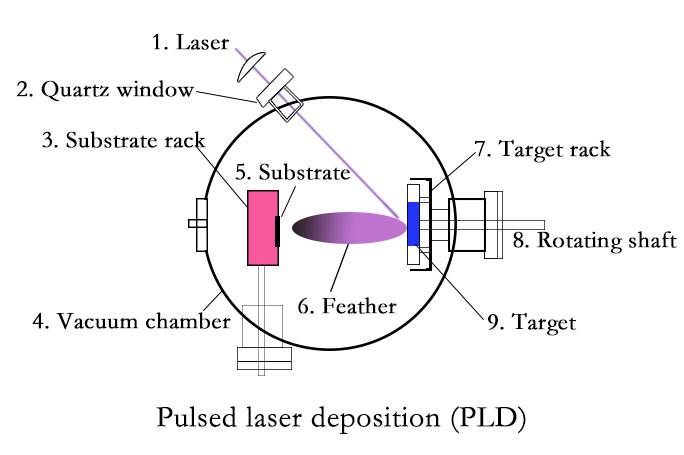
L'un des principaux avantages de la PLD réside dans ses taux de dépôt élevés, qui rationalisent considérablement le processus par rapport à d'autres méthodes. En outre, la PLD élimine le besoin de filaments, ce qui simplifie la maintenance et réduit les sources potentielles de contamination. La technologie PLD est donc particulièrement adaptée aux applications exigeant une grande précision et une grande pureté, notamment dans les secteurs de l'électronique et de l'optique.
En résumé, si la complexité du PLD exige un contrôle méticuleux, sa capacité à produire des couches minces complexes de haute qualité de manière efficace et avec un minimum d'entretien en fait un outil précieux dans le domaine des procédés de revêtement par PVD.
Dépôt chimique en phase vapeur (CVD)
Bien que le dépôt chimique en phase vapeur (CVD) diffère fondamentalement du dépôt physique en phase vapeur (PVD), il arrive que ces deux techniques soient combinées pour obtenir des propriétés de film supérieures. Le dépôt chimique en phase vapeur, une méthode de dépôt sous vide, est réputé pour produire des matériaux solides de haute qualité et de haute performance, en particulier des films minces utilisés dans l'industrie des semi-conducteurs. Le procédé consiste à exposer une plaquette (substrat) à un ou plusieurs précurseurs volatils, qui réagissent et/ou se décomposent à la surface du substrat pour former le dépôt souhaité. Cette méthode est polyvalente et permet de déposer des matériaux sous diverses formes, notamment des structures monocristallines, polycristallines, amorphes et épitaxiales.
Contrairement au dépôt en phase vapeur (PVD), qui repose sur des processus physiques tels que l'évaporation ou la pulvérisation, le dépôt en phase vapeur (CVD) s'appuie sur des réactions chimiques pour déposer des matériaux. Cette approche chimique permet de mieux contrôler la composition et les propriétés du film déposé. Toutefois, dans certaines applications, l'utilisation complémentaire de la CVD et de la PVD peut permettre d'obtenir des films aux caractéristiques améliorées, telles qu'une meilleure adhérence, de meilleures propriétés mécaniques ou des revêtements plus uniformes. Par exemple, les couches PVD préliminaires peuvent être utilisées pour créer une surface plus réceptive pour les couches CVD suivantes, optimisant ainsi la qualité globale du film.
L'intégration de la CVD et de la PVD est particulièrement bénéfique dans les processus complexes de microfabrication, où la combinaison des techniques de dépôt chimique et physique permet de relever des défis spécifiques qu'aucune des deux méthodes ne pourrait traiter seule. Cette approche hybride permet non seulement d'élargir la gamme des matériaux pouvant être déposés, mais aussi d'améliorer la fonctionnalité et les performances du produit final.
Application des gaz dans le processus de dépôt en phase vapeur (PVD)
Gaz inertes
Les gaz inertes, tels que l'argon (Ar) et l'hélium (He), jouent un rôle crucial dans les processus de dépôt par pulvérisation cathodique en agissant comme des gaz porteurs. Ces gaz sont privilégiés pour leur capacité à améliorer l'efficacité de la pulvérisation du matériau cible sans provoquer de réactions chimiques. Cette nature non réactive garantit le maintien de la pureté du film déposé, ce qui est essentiel pour obtenir des revêtements de haute qualité.
L'utilisation de gaz inertes ne se limite pas au dépôt par pulvérisation cathodique ; ils sont également employés pour prévenir les réactions chimiques indésirables susceptibles de dégrader un échantillon. Ces réactions indésirables comprennent généralement l'oxydation et l'hydrolyse, qui sont généralement déclenchées par la présence d'oxygène et d'humidité dans l'air. En remplaçant ces éléments réactifs par des gaz inertes, l'intégrité de l'échantillon est préservée.
L'argon, en particulier, est le gaz inerte le plus couramment utilisé dans diverses applications en raison de sa grande abondance naturelle et de son coût relativement faible. Il représente environ 1 % de l'atmosphère terrestre, ce qui le rend facilement disponible pour une utilisation industrielle. Si l'argon est le plus répandu, d'autres gaz nobles comme l'hélium et le néon peuvent également être utilisés en fonction des exigences spécifiques du processus.
Il convient de noter que le terme "gaz inerte" dépend du contexte. Bien que les gaz rares soient souvent considérés comme inertes, ils peuvent réagir dans certaines conditions, bien qu'avec une faible probabilité. Cette caractéristique est largement due aux enveloppes de valence complètes de ces gaz, qui les rendent généralement non réactifs. Il ne s'agit toutefois pas d'une règle absolue, car même les gaz nobles peuvent former des composés dans des conditions spécifiques.
Lorsque l'on spécifie la pureté des gaz inertes, il est courant d'indiquer le niveau de contamination en parties par million (ppm). Par exemple, un niveau de contamination de 100 ppm signifie que sur un million de molécules du gaz inerte, 100 sont des molécules étrangères. Cette mesure est cruciale pour garantir l'efficacité du gaz inerte dans le maintien de la pureté du film déposé.
En résumé, les gaz inertes tels que l'argon et l'hélium sont indispensables pour le dépôt par pulvérisation cathodique et d'autres procédés où le maintien de la pureté et de l'intégrité des matériaux est primordial. Leur nature non réactive et leur disponibilité les rendent idéaux pour une large gamme d'applications industrielles.
Gaz réactifs
Les gaz réactifs jouent un rôle crucial dans la préparation de diverses couches minces dans les procédés de dépôt en phase vapeur (PVD). Ces gaz, qui comprennent l'oxygène (O₂), l'azote (N₂) et le fluor (F₂), sont essentiels pour créer des films d'oxyde, de nitrure et de fluorure, respectivement. L'introduction de ces gaz réactifs est souvent nécessaire pour obtenir la composition chimique et les propriétés souhaitées dans les films déposés.
Par exemple, lors de la préparation de films minces d'oxyde d'aluminium (Al₂O₃), l'oxygène est généralement introduit comme gaz de réaction. Cela garantit que les atomes d'aluminium en phase vapeur réagissent avec l'oxygène pour former un film d'Al₂O₃ stable et uniforme. L'utilisation de gaz réactifs ne se limite pas à l'oxyde d'aluminium ; elle s'étend également à d'autres matériaux, tels que le nitrure de silicium (Si₃N₄) et le dioxyde de titane (TiO₂), où l'azote et l'oxygène sont respectivement utilisés.
Le choix du gaz réactif et sa concentration peuvent influencer de manière significative les propriétés du film, notamment sa densité, sa dureté et sa stabilité chimique. Par exemple, des concentrations d'oxygène plus élevées peuvent conduire à des films plus poreux et moins denses, tandis que des concentrations plus faibles peuvent entraîner une oxydation incomplète, affectant la qualité globale du film.
En résumé, l'utilisation judicieuse des gaz réactifs est un aspect essentiel des procédés de dépôt en phase vapeur (PVD), qui permet de créer des films minces de haute performance avec des propriétés adaptées à diverses applications.
Gaz organiques
Dans certaines applications spécialisées, les gaz organiques tels que l'éthylène et le propylène jouent un rôle crucial dans la préparation des films polymères et des composites. Ces gaz sont souvent introduits dans le procédé PVD pour faciliter la formation de structures de films spécifiques qui ne sont pas réalisables avec des gaz inertes ou réactifs seuls.
L'utilisation de gaz organiques dans les procédés PVD est particulièrement avantageuse pour créer des films polymères qui nécessitent des fonctionnalités chimiques spécifiques. Par exemple, l'éthylène peut être utilisé pour former des films de polyéthylène, connus pour leurs excellentes propriétés mécaniques et leur résistance chimique. De même, le propylène peut être utilisé pour créer des films de polypropylène, qui sont très résistants à la chaleur et aux produits chimiques.
En outre, les gaz organiques peuvent être combinés à d'autres gaz pour créer des films composites qui présentent un mélange de propriétés provenant à la fois de composants organiques et inorganiques. Cette approche hybride permet de personnaliser les propriétés des films, ce qui permet d'adapter les films à des applications spécifiques dans des secteurs tels que l'électronique, l'optique et l'ingénierie mécanique.
En résumé, l'incorporation de gaz organiques dans les procédés PVD ouvre de nouvelles possibilités pour la création de films polymères et de composites avancés, permettant le développement de matériaux aux propriétés uniques et améliorées.
Réglage de la pression du gaz
La pression du gaz dans le procédé PVD joue un rôle essentiel dans la détermination de la vitesse de dépôt et de la qualité du film. Ce paramètre influence directement le comportement du matériau gazeux lorsqu'il se déplace de la cible au substrat.
À des pressions de gaz plus faibles, la matière gazeuse a tendance à se diffuser plus uniformément, ce qui améliore la densification et l'homogénéité du film. En effet, la pression réduite minimise les collisions entre les molécules de gaz, ce qui permet un processus de dépôt plus ordonné. Par conséquent, le film obtenu présente moins de défauts et une structure plus cohérente.
Inversement, des pressions de gaz plus élevées peuvent entraîner une augmentation de la rugosité du film. Dans ces conditions, le matériau gazeux subit des collisions plus fréquentes, ce qui peut perturber le processus de dépôt ordonné. Il en résulte un film moins uniforme avec une rugosité de surface potentiellement plus élevée. Toutefois, il convient de noter que des pressions plus élevées peuvent également améliorer la vitesse de dépôt, mais au détriment de la qualité du film.
Pression du gaz | Qualité du film | Vitesse de dépôt |
---|---|---|
Plus faible | Amélioration de la densification et de l'homogénéité | Plus lente |
Plus élevée | Augmentation de la rugosité | Plus rapide |
La pression de gaz optimale est souvent déterminée par les exigences spécifiques de l'application, en équilibrant le besoin de films de haute qualité et le désir de vitesses de dépôt efficaces. Cet équilibre délicat est crucial pour obtenir les propriétés souhaitées dans le produit final.
Domaines d'application du procédé de revêtement PVD
Industrie électronique
Dans le domaine des semi-conducteurs, des circuits intégrés et des écrans, le procédé de dépôt physique en phase vapeur (PVD) joue un rôle essentiel dans la fabrication de divers films. Plus précisément, le dépôt en phase vapeur est utilisé pour préparer trois principaux types de films : les films conducteurs, les films isolants et les films optiques.
Films conducteurs
Les films conducteurs sont essentiels pour assurer la circulation du courant électrique dans les appareils électroniques. Ces films sont généralement fabriqués à partir de métaux tels que l'aluminium, le cuivre et l'or, qui sont déposés à l'aide de techniques telles que l'évaporation thermique ou la pulvérisation cathodique. Le choix du métal et de la méthode de dépôt peut avoir un impact significatif sur la conductivité, l'adhérence et les performances globales du film.
Films isolants
Les films isolants, quant à eux, sont essentiels pour éviter les courts-circuits électriques et protéger les composants sensibles. Des matériaux tels que le dioxyde de silicium (SiO₂) et le nitrure de silicium (Si₃N₄) sont couramment utilisés pour créer ces films. Le procédé PVD permet un contrôle précis de l'épaisseur et de l'uniformité du film, ce qui est essentiel pour maintenir l'intégrité et la fiabilité de l'appareil.
Films optiques
Les films optiques sont conçus pour gérer l'interaction de la lumière avec la surface de l'appareil, afin d'améliorer la clarté de l'affichage et de réduire les reflets. Ces films comprennent souvent des revêtements antireflets et des couches d'amélioration de la transmission. Le procédé PVD permet de créer ces films avec des propriétés optiques spécifiques, telles que l'indice de réfraction et la transmittance, adaptées aux exigences de l'appareil.
En résumé, le procédé PVD est indispensable à l'industrie électronique, car il offre une méthode polyvalente et précise pour produire les films conducteurs, isolants et optiques qui sont essentiels aux appareils électroniques modernes.
Appareils optiques
Le procédé PVD (Physical Vapor Deposition) joue un rôle crucial dans la fabrication de revêtements optiques, qui sont essentiels pour améliorer les performances de divers appareils optiques. Ces revêtements comprennent des revêtements antireflets, des films d'amélioration de la transmission et des couches de protection, tous conçus pour optimiser l'interaction de la lumière avec la surface de l'appareil.
Types de revêtements optiques
-
Revêtements antireflets: Ces revêtements sont conçus pour minimiser la réflexion de la lumière, augmentant ainsi la quantité de lumière qui passe à travers la surface optique. Ceci est particulièrement important dans des applications telles que les lentilles d'appareil photo, les lunettes et les panneaux solaires.
-
Films d'amélioration de la transmission: Ces films sont conçus pour augmenter la transmission de longueurs d'onde spécifiques de la lumière, ce qui est crucial dans des dispositifs tels que les filtres optiques et les capteurs.
-
Couches protectrices: Ces revêtements protègent le matériau sous-jacent des facteurs environnementaux tels que l'humidité, la poussière et les dommages mécaniques, garantissant ainsi la longévité et les performances du dispositif optique.
Avantages du dépôt en phase vapeur dans les revêtements optiques
- Précision: Le procédé PVD permet un contrôle précis de l'épaisseur du film, ce qui est essentiel pour obtenir les propriétés optiques souhaitées.
- Durabilité: Les dispositifs optiques revêtus par PVD présentent une durabilité supérieure à celle des dispositifs revêtus par d'autres méthodes, ce qui les rend idéaux pour une utilisation à long terme dans divers environnements.
- Polyvalence: Le procédé PVD peut être adapté pour créer une large gamme de revêtements, répondant aux besoins spécifiques des différentes applications optiques.
Applications dans les appareils optiques
Type d'appareil | Objectif du revêtement |
---|---|
Lentilles d'appareil photo | Revêtements antireflets pour une meilleure imagerie |
Lunettes | Couches antireflets et résistantes aux rayures |
Panneaux solaires | Revêtements antireflets pour maximiser la capture de l'énergie |
Filtres optiques | Amélioration de la transmittance pour des longueurs d'onde spécifiques |
Capteurs | Couches protectrices pour garantir des performances constantes |
Le procédé PVD permet non seulement d'améliorer la fonctionnalité de ces dispositifs, mais aussi de prolonger leur durée de vie, ce qui en fait une technologie indispensable dans l'industrie optique.
Composants mécaniques
Dans le domaine du traitement de surface des composants mécaniques, les procédés de dépôt physique en phase vapeur (PVD) jouent un rôle essentiel dans l'amélioration de leur longévité et de leurs performances. Les techniques PVD sont employées méticuleusement pour augmenter la résistance à l'usure, à la corrosion et à l'oxydation de ces composants. Il en résulte une prolongation significative de leur durée de vie, ce qui les rend plus fiables et plus durables dans les environnements industriels exigeants.
L'application du dépôt en phase vapeur dans les composants mécaniques ne consiste pas simplement à ajouter une couche protectrice ; il s'agit d'intégrer la science des matériaux avancés pour créer des surfaces capables de résister à des conditions extrêmes. Par exemple, les composants des moteurs automobiles, des turbines aérospatiales et des machines industrielles sont souvent soumis à des conditions rigoureuses qui peuvent entraîner une dégradation rapide. En appliquant des revêtements PVD, ces composants sont renforcés contre l'usure causée par la friction, les réactions chimiques et l'exposition à des températures élevées.
En outre, les revêtements PVD peuvent être adaptés pour répondre aux exigences spécifiques des différents composants mécaniques. Qu'il s'agisse d'un outil de haute précision dans le secteur manufacturier ou d'une pièce critique dans un appareil médical, la possibilité de personnaliser le revêtement garantit que chaque composant fonctionne de manière optimale dans ses propres conditions. Ce niveau de personnalisation est obtenu en faisant varier les paramètres de dépôt, tels que le type de matériau cible, la pression du gaz et la température, afin d'affiner les propriétés du film obtenu.
En résumé, l'utilisation des procédés PVD pour le traitement de surface des composants mécaniques est un investissement stratégique qui permet d'améliorer leur durabilité et leurs performances, contribuant ainsi à l'efficacité et à la fiabilité de diverses applications industrielles.
Revêtements décoratifs
Le procédé PVD permet de créer des films décoratifs qui rehaussent l'attrait esthétique de divers produits. Ces films, caractérisés par leur éclat métallique et leurs couleurs vives, sont largement utilisés dans des secteurs tels que la bijouterie, l'horlogerie et les articles ménagers. Le procédé permet un contrôle précis de l'épaisseur et de l'uniformité du film, ce qui garantit que le produit final répond aux normes élevées d'attrait visuel et de durabilité exigées dans ces secteurs.
Dans le domaine de la bijouterie, les revêtements PVD offrent une finition sophistiquée qui peut imiter l'aspect des métaux précieux pour une fraction du coût. C'est particulièrement avantageux pour la production en grande série où le maintien d'un aspect luxueux est crucial. Les montres, quant à elles, bénéficient de revêtements PVD qui non seulement améliorent leur attrait visuel, mais offrent également une résistance aux rayures et à la corrosion, prolongeant ainsi la durée de vie de ces garde-temps.
Les produits ménagers, tels que les ustensiles de cuisine et les objets de décoration, tirent également parti des revêtements PVD pour obtenir une apparence moderne et élégante. La possibilité d'incorporer diverses couleurs et motifs dans les revêtements ouvre un large éventail de possibilités de conception, ce qui fait du PVD un outil polyvalent dans la fabrication des biens de consommation.
En outre, le procédé PVD est respectueux de l'environnement, car il fonctionne sous vide, ce qui minimise les déchets et réduit l'impact sur l'environnement associé aux méthodes de revêtement traditionnelles. Cet aspect de durabilité renforce son attrait dans les industries où l'esthétique et la responsabilité environnementale sont primordiales.
Avantages et défis du procédé PVD
Avantages du procédé PVD
Les procédés de revêtement PVD offrent plusieurs avantages indéniables qui en font un choix privilégié dans diverses industries. L'un des avantages les plus significatifs est la production defilms de haute qualité. Ces films présentent uneadhérence,uniformitéetintégrité structurelleCes caractéristiques sont cruciales pour améliorer les performances des matériaux revêtus. Par exemple, dans l'industrie électronique, les films conducteurs revêtus par PVD garantissent une conductivité électrique supérieure et une perte de signal minimale, tandis que dans les appareils optiques, les revêtements fournissent des propriétés optiques précises qui améliorent les performances de l'appareil.
Un autre avantage notable est lerespect de l'environnement des procédés PVD. Contrairement à d'autres méthodes de revêtement, le procédé PVD fonctionne sous vide, ce qui minimise le rejet de substances nocives dans l'environnement. Cela fait du dépôt en phase vapeur une option durable, en particulier dans les industries où les réglementations environnementales sont strictes. En outre, l'utilisation de gaz inertes tels que l'argon et l'hélium garantit la pureté des films sans introduire de sous-produits réactifs susceptibles de nuire à l'environnement.
Lapolyvalence des procédés PVD est également un atout majeur. Le dépôt en phase vapeur peut être appliqué à une large gamme de matériaux, y compris les métaux, les céramiques et les polymères, ce qui le rend adapté à diverses applications. Qu'il s'agisse de préparer des couches minces pour les semi-conducteurs, d'améliorer la durabilité des composants mécaniques ou de créer des revêtements décoratifs pour les produits de consommation, le dépôt en phase vapeur offre une solution flexible qui peut être adaptée pour répondre à des besoins spécifiques. Par exemple, l'utilisation de gaz réactifs comme l'oxygène et l'azote permet de créer des films complexes d'oxyde et de nitrure, ce qui élargit encore la gamme des applications possibles.
En résumé, la combinaison d'une production de films de haute qualité, d'une durabilité environnementale et d'une large applicabilité fait des procédés de revêtement PVD une technologie très avantageuse dans de nombreux secteurs.
Défis
L'un des principaux défis associés aux procédés de dépôt physique en phase vapeur (PVD) est l'importantcoût de l'équipement. Les systèmes PVD avancés, tels que ceux qui utilisent l'évaporation par faisceau d'électrons ou le dépôt par laser pulsé, nécessitent des machines sophistiquées et des systèmes de contrôle précis, dont le coût peut être prohibitif pour les petites entreprises. En outre, la maintenance et l'étalonnage de ces systèmes requièrent une expertise spécialisée, ce qui contribue encore à augmenter le coût global.
Un autre défi important est celui desles taux de dépôt. Il est essentiel d'atteindre des taux de dépôt optimaux pour une production efficace, mais ils peuvent être influencés par une myriade de facteurs, notamment la pression du gaz, la température du substrat et le type de matériau cible utilisé. Des vitesses de dépôt plus lentes peuvent entraîner des temps de traitement plus longs, ce qui augmente les coûts d'exploitation et risque d'affecter la qualité du film déposé. Inversement, des vitesses de dépôt plus élevées peuvent donner lieu à des films présentant des propriétés sous-optimales, telles qu'une densité réduite ou une rugosité accrue.
Le contrôle de l'épaisseur du film est également un obstacle important dans les procédés PVD. Garantir une épaisseur de film uniforme sur le substrat est essentiel pour la performance et la fiabilité du produit final. Cependant, le maintien d'un contrôle précis de l'épaisseur du film peut s'avérer difficile, en particulier lorsqu'il s'agit de géométries complexes ou de substrats de grande surface. Les variations d'épaisseur peuvent entraîner des incohérences dans les propriétés du film, telles que ses caractéristiques optiques, mécaniques ou électriques, ce qui peut être préjudiciable à l'application prévue.
Pour relever ces défis, les recherches en cours et les avancées technologiques se concentrent sur le développement d'équipements plus rentables, l'optimisation des paramètres de dépôt et l'amélioration des mécanismes de contrôle de l'épaisseur des films. Ces efforts visent à améliorer l'efficacité et la fiabilité des procédés PVD, les rendant plus accessibles et plus efficaces dans diverses industries.
CONTACTEZ-NOUS POUR UNE CONSULTATION GRATUITE
Les produits et services de KINTEK LAB SOLUTION ont été reconnus par des clients du monde entier. Notre personnel se fera un plaisir de répondre à toute demande que vous pourriez avoir. Contactez-nous pour une consultation gratuite et parlez à un spécialiste produit pour trouver la solution la plus adaptée aux besoins de votre application !