Pour accroître l'efficacité de votre four à induction, vous pouvez vous concentrer sur l'optimisation de l'utilisation de l'énergie, l'amélioration de la vitesse de fusion et la réduction des pertes d'énergie.Les principales stratégies consistent à passer à la technologie d'induction IGBT, à augmenter la capacité d'alimentation électrique, à optimiser la taille de la charge et les méthodes d'alimentation, à maintenir des températures de sortie du fer fondu adéquates et à minimiser les pertes d'énergie thermique.En outre, l'utilisation de bobines primaires à haute tension, la vidange complète du four après la fusion et l'intégration de systèmes de récupération de la chaleur résiduelle permettent d'améliorer encore l'efficacité.L'ensemble de ces mesures permet d'accélérer le chauffage, de réduire la consommation d'énergie et d'augmenter la production.
Explication des principaux points :
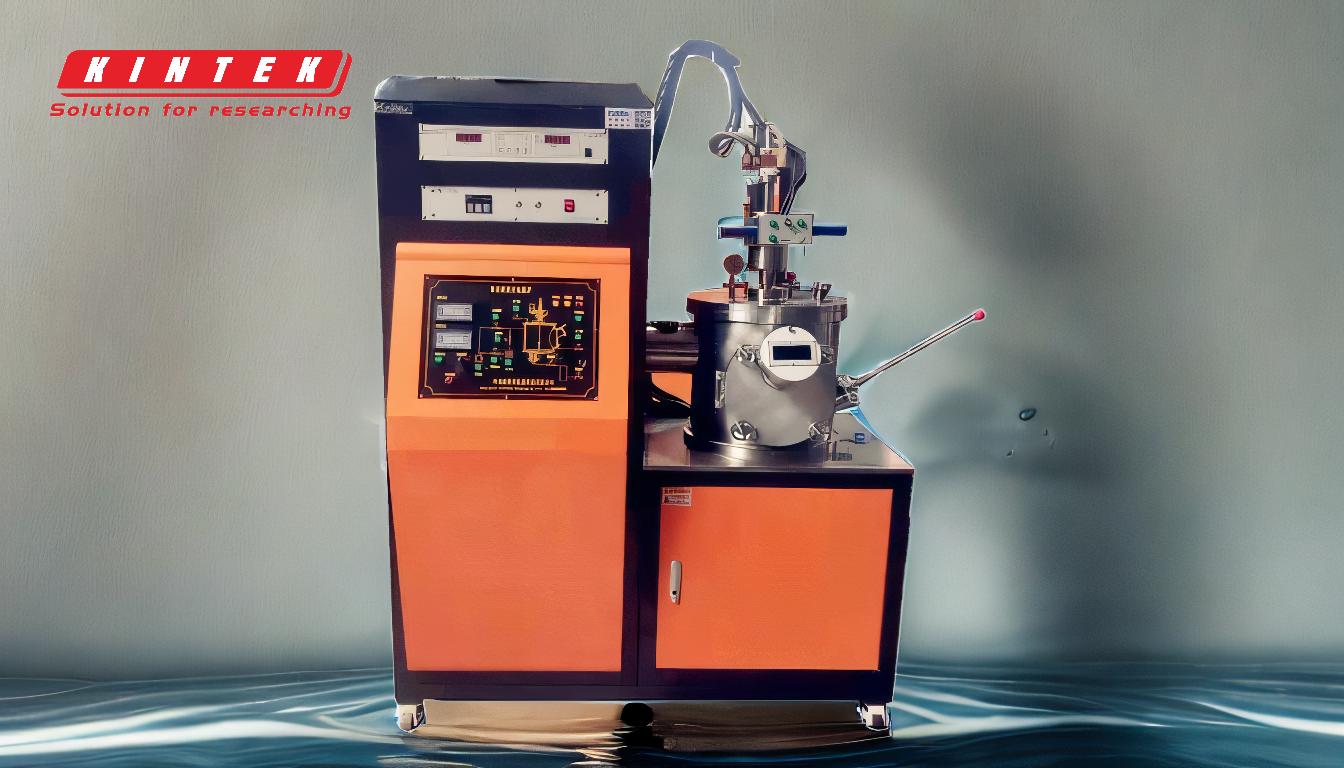
-
Passer à la technologie d'induction IGBT:
- La technologie d'induction IGBT (Insulated Gate Bipolar Transistor) est une avancée moderne qui réduit considérablement la consommation d'énergie de 15 à 30 %.Cette technologie améliore l'efficacité globale du four en optimisant l'utilisation de l'énergie et en minimisant les pertes de chaleur.
-
Augmentation de la capacité d'alimentation électrique:
- L'un des moyens les plus directs d'augmenter la vitesse de fusion consiste à augmenter la puissance de l'alimentation électrique du four à induction.Une alimentation électrique plus élevée permet de chauffer et de fondre plus rapidement, ce qui accroît l'efficacité de la production.
-
Optimiser la taille des charges et les méthodes d'alimentation:
- Le choix de la bonne taille de charge et de la bonne méthode d'alimentation est crucial pour une fusion efficace.Une charge bien dimensionnée garantit un chauffage uniforme, tandis qu'une méthode d'alimentation correcte minimise les retards et le gaspillage d'énergie.Une bonne gestion de ces facteurs peut conduire à des temps de fusion plus rapides et à une réduction de la consommation d'énergie.
-
Maintenir une température de sortie du fer fondu appropriée:
- Maintenir la température de sortie du fer fondu à un niveau optimal est essentiel pour un fonctionnement efficace.Une température trop élevée peut entraîner une consommation excessive d'énergie, tandis qu'une température trop basse peut ralentir le processus de fusion.Le maintien d'un bon équilibre garantit une utilisation efficace de l'énergie et un traitement plus rapide.
-
Utiliser des bobines primaires à haute tension:
- Les fours à induction dotés de bobines primaires à haute tension peuvent produire des fréquences allant de 50 Hz à 10 000 Hz.Ce fonctionnement à haute fréquence permet un chauffage rapide et un rendement thermique plus élevé, ce qui accélère la fusion et réduit les pertes d'énergie.
-
Vider complètement le four après la fusion:
- Le fait de s'assurer que le four est complètement vidé à la fin du processus de fusion permet de séparer correctement le métal fondu des impuretés.Cela permet non seulement d'améliorer la qualité de la production, mais aussi de préparer plus rapidement le four pour le lot suivant, ce qui permet d'économiser du temps et de l'énergie.
-
Minimiser les pertes de puissance thermique:
- La réduction des pertes de puissance thermique peut être obtenue en optimisant l'agencement de l'espace du four et en utilisant des matériaux qui garantissent un flux de courant régulier.La réduction de ces pertes permet une utilisation plus efficace de l'énergie et une diminution des coûts d'exploitation.
-
Intégrer des systèmes de récupération de la chaleur perdue:
- L'ajout d'un récupérateur à matrice céramique au système d'échappement permet de récupérer la chaleur perdue et de l'utiliser pour préchauffer l'air de combustion.Cette méthode peut améliorer l'efficacité énergétique jusqu'à 50 %, ce qui rend le four plus respectueux de l'environnement et plus rentable.
-
Alimentation continue en acier d'agitation auxiliaire:
- L'alimentation continue du four en acier d'agitation auxiliaire permet d'augmenter la vitesse de fusion et de réduire la consommation d'énergie.Cette méthode garantit que le métal en fusion est chauffé uniformément, ce qui permet d'obtenir une fusion plus efficace et de réduire le gaspillage d'énergie.
En mettant en œuvre ces stratégies, vous pouvez améliorer considérablement l'efficacité de votre four à induction, ce qui se traduira par des temps de production plus courts, une consommation d'énergie réduite et un rendement global plus élevé.
Tableau récapitulatif :
Stratégie | Principaux avantages |
---|---|
Passage à la technologie d'induction IGBT | Réduit la consommation d'énergie de 15 à 30 %, en optimisant l'utilisation de l'énergie et en minimisant les pertes de chaleur. |
Augmentation de la capacité d'alimentation | Augmente la vitesse de fusion et l'efficacité de la production. |
Optimiser la taille de la charge et les méthodes d'alimentation | Assure un chauffage uniforme, une fusion plus rapide et une réduction du gaspillage d'énergie. |
Maintien de la température de sortie de la fonte | Équilibre la consommation d'énergie et la vitesse de traitement pour un fonctionnement efficace. |
Utiliser des bobines primaires à haute tension | Permet un chauffage rapide et une meilleure efficacité thermique. |
Vider complètement le four après la fusion | Améliore la qualité de la production et réduit les temps d'arrêt. |
Minimiser les pertes de puissance thermique | Améliore l'efficacité énergétique et réduit les coûts d'exploitation. |
Intégrer des systèmes de récupération de la chaleur perdue | Récupère la chaleur perdue, améliorant ainsi l'efficacité énergétique jusqu'à 50 %. |
Alimentation continue de l'acier d'agitation | Augmente la vitesse de fusion et réduit la consommation d'énergie. |
Prêt à optimiser votre four à induction ? Contactez nos experts dès aujourd'hui pour des solutions sur mesure !