Le revêtement par dépôt physique en phase vapeur (PVD) est un procédé sophistiqué utilisé pour appliquer des revêtements minces, durables et très adhérents sur divers substrats.Le procédé consiste à créer un environnement sous vide poussé, à vaporiser un matériau cible et à le déposer sur un substrat pour former une couche protectrice ou fonctionnelle.Les revêtements PVD sont largement utilisés dans des industries telles que l'aérospatiale, l'automobile et l'électronique en raison de leur dureté exceptionnelle, de leur résistance à l'usure et de leur protection contre la corrosion.Le processus comprend généralement des étapes telles que la vaporisation, le transport, la réaction et le dépôt, avec des techniques telles que la pulvérisation cathodique et l'évaporation thermique qui sont couramment utilisées.
Explication des points clés :
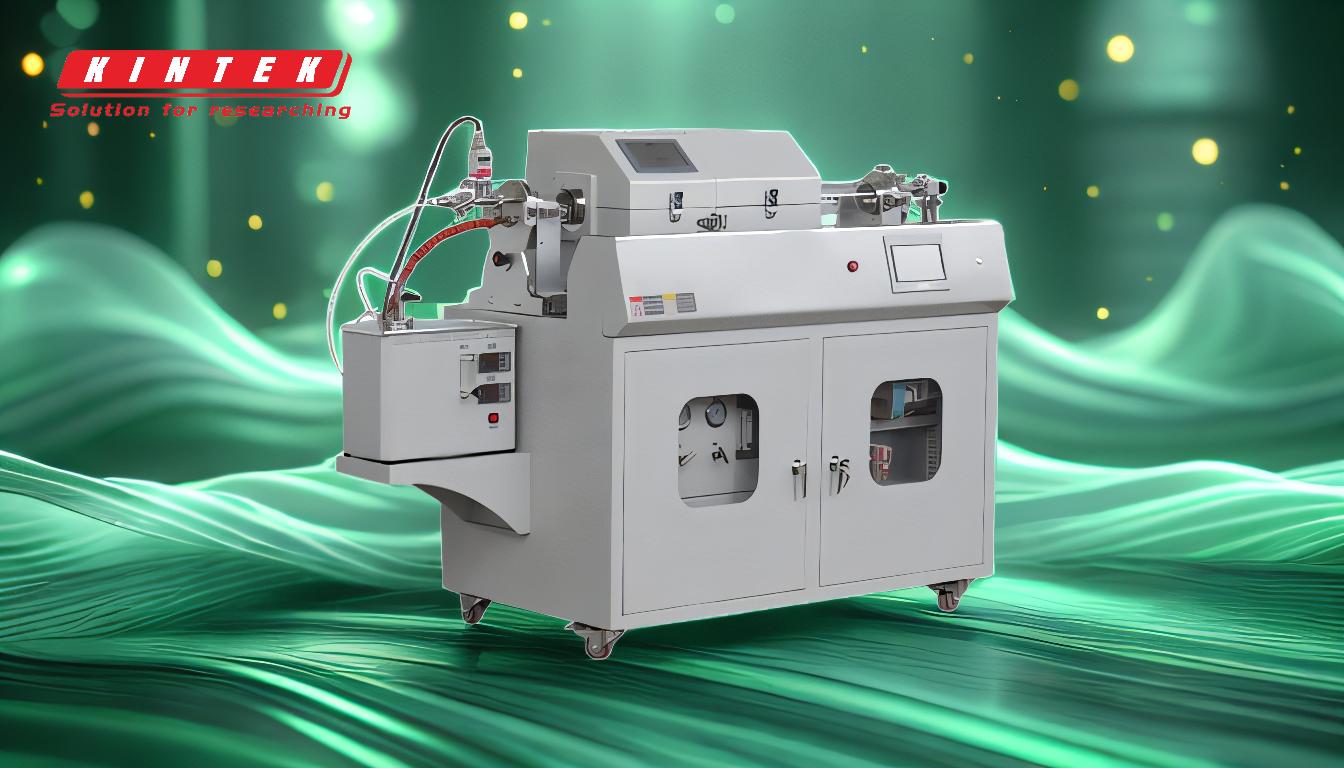
-
Préparation de la chambre à vide:
- Le processus PVD commence par placer le matériau cible (le matériau à revêtir) et le substrat (le matériau sur lequel il doit être revêtu) dans une chambre à vide.
- La chambre est ensuite mise sous vide pour créer un environnement à vide poussé, généralement à des pressions allant de 10^-2 à 10^-6 Torr, ce qui se rapproche des conditions de l'espace extra-atmosphérique.
- Cet environnement sous vide est essentiel pour éviter toute contamination et garantir la pureté du revêtement.
-
Vaporisation du matériau cible:
- Le matériau cible est vaporisé à l'aide de sources à haute énergie telles que des faisceaux d'électrons, des ions ou des photons.Cette étape est connue sous le nom d'évaporation.
- Dans les techniques telles que la pulvérisation, le matériau cible est bombardé avec des ions à haute énergie (souvent des ions Argon) pour déloger les atomes de la surface de la cible, créant ainsi un plasma d'atomes ou de molécules.
- Dans le cas de l'évaporation thermique, le matériau cible est chauffé à haute température jusqu'à ce qu'il se vaporise.
-
Transport de la matière vaporisée:
- Les atomes ou molécules vaporisés sont ensuite transportés à travers la chambre à vide vers le substrat.
- Ce transport s'effectue dans une atmosphère chimiquement inerte, souvent créée à l'aide de gaz inertes tels que l'argon, afin d'éviter toute réaction chimique indésirable au cours du processus.
-
Réaction (facultatif):
- En fonction des propriétés souhaitées du revêtement, le matériau vaporisé peut réagir avec des gaz sélectionnés (tels que l'azote, l'oxygène ou le méthane) pour former des composés tels que des oxydes métalliques, des nitrures ou des carbures.
- Cette étape de réaction détermine les principales propriétés du revêtement, telles que la dureté, la couleur et la résistance chimique.
-
Dépôt sur le substrat:
- Le matériau vaporisé se condense sur le substrat, formant un film mince et uniforme qui adhère fortement à la surface.
- Le processus de dépôt est soigneusement contrôlé pour garantir l'épaisseur et l'uniformité souhaitées du revêtement, généralement de l'ordre de quelques microns.
- Le résultat est un revêtement très adhérent qui s'interpénètre avec le matériau sous-jacent, évitant ainsi les problèmes d'écaillage.
-
Purge et refroidissement:
- Une fois le dépôt terminé, la chambre est purgée avec du gaz inerte pour éliminer toute vapeur résiduelle.
- Le substrat revêtu est ensuite laissé à refroidir avant d'être retiré de la chambre.
-
Techniques utilisées pour le revêtement par PVD:
- Pulvérisation:Technique de dépôt en phase vapeur (PVD) largement utilisée, dans laquelle des ions à haute énergie bombardent le matériau cible, provoquant l'éjection d'atomes qui se déposent sur le substrat.
- Evaporation thermique:Il s'agit de chauffer le matériau cible jusqu'à ce qu'il se vaporise, la vapeur se condensant ensuite sur le substrat.
- Dépôt de vapeur par arc:Utilise un arc électrique pour vaporiser le matériau cible, souvent utilisé pour les revêtements durs comme le nitrure de titane.
-
Applications et avantages des revêtements PVD:
- Les revêtements PVD sont utilisés dans une variété d'applications, y compris les outils de coupe, les appareils médicaux et les finitions décoratives.
- Ces revêtements offrent une excellente résistance à l'usure, une protection contre la corrosion et un attrait esthétique.
- Le procédé est respectueux de l'environnement, car il ne fait pas appel à des produits chimiques nocifs et ne produit pas de déchets importants.
En suivant ces étapes, le revêtement PVD crée une couche durable et performante qui améliore les propriétés du substrat, ce qui le rend adapté à des applications exigeantes dans de nombreux secteurs.
Tableau récapitulatif :
Étape | Description de l'étape |
---|---|
1.La préparation | Le matériau cible et le substrat sont placés dans une chambre à vide poussé. |
2.Vaporisation | Le matériau cible est vaporisé à l'aide de sources à haute énergie telles que des faisceaux d'électrons. |
3.Transport | Les atomes vaporisés sont transportés dans une atmosphère de gaz inerte. |
4.Réaction (facultatif) | La matière vaporisée réagit avec les gaz pour former des composés tels que des nitrures ou des oxydes. |
5.Dépôt | La vapeur se condense sur le substrat, formant une couche mince et uniforme. |
6.Purge et refroidissement | La chambre est purgée et le substrat revêtu est refroidi. |
7.Techniques | La pulvérisation cathodique, l'évaporation thermique et le dépôt en phase vapeur par arc sont couramment utilisés. |
8.Applications | Utilisé dans les outils de coupe, les appareils médicaux et les finitions décoratives. |
Vous souhaitez améliorer vos matériaux avec des revêtements PVD ? Contactez nos experts dès aujourd'hui pour en savoir plus !