Une machine à revêtir sous vide est une machine spécialisée utilisée pour appliquer des revêtements fins et protecteurs sur des substrats, généralement des métaux ou des céramiques, par un processus connu sous le nom de dépôt physique en phase vapeur (PVD).Le processus se déroule dans une chambre à vide où le matériau de revêtement est vaporisé ou ionisé à l'aide d'une énergie thermique ou d'un plasma, puis déposé sur le substrat dans un environnement contrôlé.Cela crée des couches nanométriques qui améliorent les propriétés telles que la dureté, la résistance à l'usure et la résistance à la corrosion.La machine à revêtir sous vide se compose de plusieurs éléments essentiels, notamment la chambre à vide, le système de vide, l'alimentation électrique, le système d'alimentation en gaz et le système de refroidissement, qui fonctionnent tous ensemble pour garantir un dépôt de revêtement précis et efficace.
Explication des points clés :
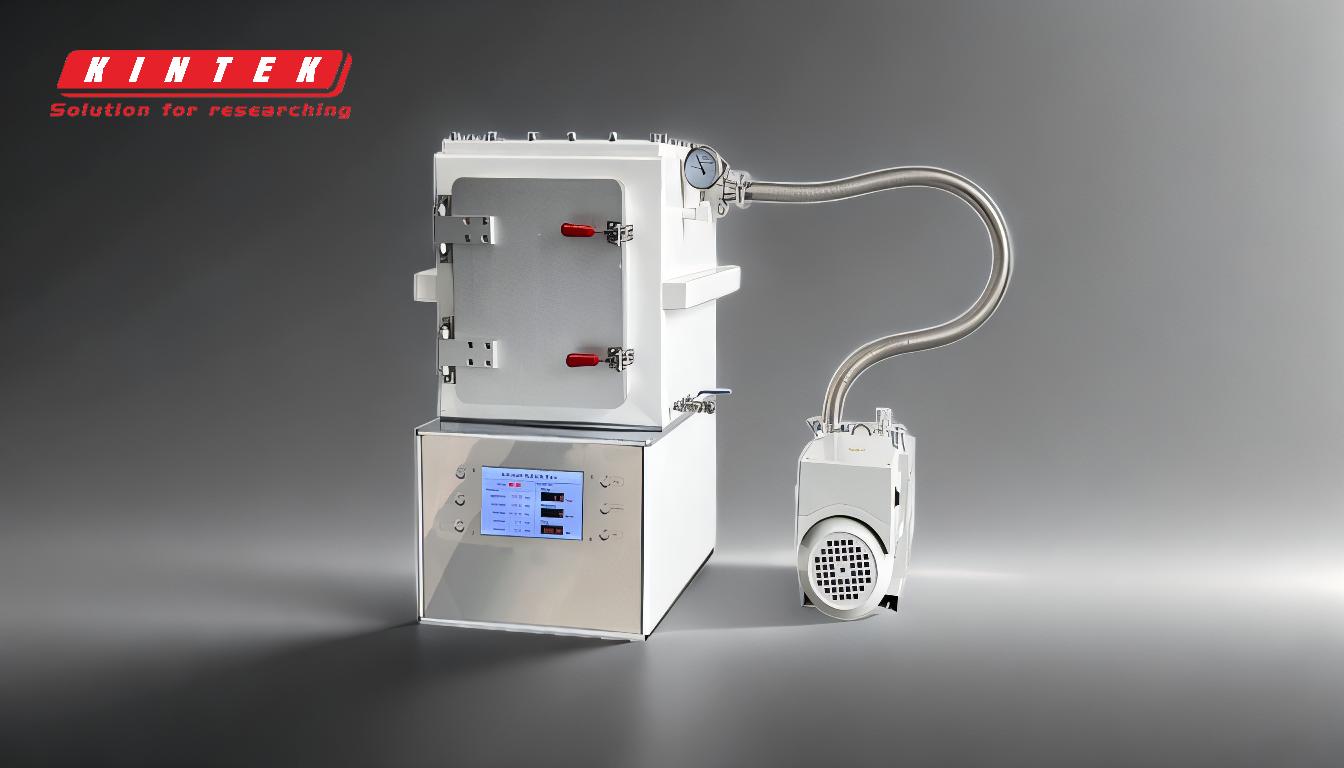
-
Chambre à vide et environnement de revêtement
- La chambre à vide est le cœur de la machine à revêtir sous vide. Elle fournit un environnement contrôlé et sub-atmosphérique pour le processus de revêtement.
- Le vide est essentiel pour éliminer les contaminants et garantir la pureté du revêtement.Il permet également un contrôle précis des particules vaporisées, qui sont déposées sur le substrat.
- La chambre est conçue pour supporter des températures et des pressions élevées, ce qui garantit la stabilité du processus de revêtement.
-
Vaporisation du matériau de revêtement
- Le matériau de revêtement, généralement un métal ou une céramique, est vaporisé ou ionisé dans la chambre à vide.
- Cette opération est réalisée à l'aide d'énergie thermique (par exemple, chauffage résistif) ou de plasma, qui décompose le matériau en particules atomiques ou moléculaires.
- Le matériau vaporisé est ensuite transporté à travers l'environnement sous vide jusqu'au substrat.
-
Processus de dépôt
- Le matériau de revêtement vaporisé se condense sur le substrat, formant une couche fine et uniforme.
- Ce processus est hautement contrôlé afin de garantir l'épaisseur et les propriétés souhaitées du revêtement, souvent à l'échelle nanométrique.
- Le dépôt peut se faire par différentes techniques PVD, telles que la pulvérisation ou l'évaporation, en fonction de l'application.
-
Préparation du substrat
- Avant l'application du revêtement, le substrat est soumis à un nettoyage approfondi afin d'éliminer les contaminants et d'assurer une bonne adhérence du revêtement.
- Il peut s'agir d'un nettoyage abrasif, de traitements chimiques ou d'un nettoyage au plasma dans la chambre à vide.
- Une bonne préparation de la surface est essentielle pour obtenir un revêtement durable et de haute qualité.
-
Principaux composants d'une unité d'enduction sous vide
- Chambre à vide et équipement d'enrobage:Il abrite le substrat et le matériau de revêtement, offrant ainsi un environnement contrôlé.
- Système d'obtention du vide:Crée et maintient le vide à l'aide de pompes et de joints.
- Système de mesure du vide:Contrôle les niveaux de pression à l'intérieur de la chambre.
- Alimentation électrique:Fournit de l'énergie pour la vaporisation, l'ionisation et la génération de plasma.
- Système d'entrée des gaz de procédé:Introduit des gaz réactifs ou inertes pour améliorer le processus de revêtement.
- Système de transmission mécanique:Déplace le substrat ou le matériau de revêtement selon les besoins.
- Chauffage et contrôle de la température:Régule la température pour des conditions de revêtement optimales.
- Source d'évaporation et de pulvérisation ionique:Génère le matériau de revêtement vaporisé.
- Système de refroidissement à l'eau:Prévient la surchauffe des composants de la machine.
-
Applications et avantages
- Le revêtement sous vide est largement utilisé dans des secteurs tels que l'aérospatiale, l'automobile, l'électronique et les appareils médicaux.
- Les revêtements offrent des propriétés améliorées, notamment en termes de dureté, de résistance à l'usure, de résistance à la corrosion et de stabilité thermique.
- Le processus est respectueux de l'environnement, car il minimise les déchets et évite les produits chimiques nocifs.
-
Contrôle et précision du processus
- La coucheuse sous vide permet un contrôle précis de l'épaisseur, de la composition et de l'uniformité du revêtement.
- Des systèmes de contrôle avancés garantissent une qualité et des performances constantes des revêtements.
- La capacité de déposer des couches à l'échelle nanométrique rend le revêtement sous vide idéal pour les applications de haute précision.
En combinant ces éléments, une tour de vernissage sous vide crée des revêtements de haute performance qui répondent aux exigences des industries modernes.Le processus témoigne de l'intégration de l'ingénierie avancée et de la science des matériaux, offrant des solutions qui améliorent la durabilité et la fonctionnalité des composants critiques.
Tableau récapitulatif :
Composant clé | Fonction |
---|---|
Chambre à vide | Fournit un environnement contrôlé et sub-atmosphérique pour le dépôt de revêtement. |
Système d'obtention du vide | Crée et maintient le vide à l'aide de pompes et de joints. |
Alimentation électrique | Fournit l'énergie nécessaire à la vaporisation, à l'ionisation et à la génération de plasma. |
Système d'alimentation en gaz de procédé | Introduit des gaz réactifs ou inertes pour améliorer le processus de revêtement. |
Système de refroidissement à l'eau | Empêche la surchauffe des composants de la machine. |
Source d'évaporation/de pulvérisation d'ions | Génère un matériau de revêtement vaporisé pour le dépôt. |
Prêt à améliorer vos matériaux avec des revêtements de précision ? Contactez nous dès aujourd'hui pour en savoir plus sur les vernisseuses sous vide !