La pulvérisation magnétron est une technique de dépôt physique en phase vapeur (PVD) largement utilisée pour déposer des couches minces de matériaux sur des substrats.Elle fonctionne dans un environnement sous vide où un matériau cible (cathode) est bombardé par des ions à haute énergie, ce qui provoque l'éjection d'atomes de la surface de la cible.Ces atomes éjectés se déplacent ensuite dans le vide et se déposent sur un substrat, formant un film mince.Le processus est amélioré par l'utilisation d'un magnétron, qui génère des champs magnétiques et électriques puissants pour confiner les électrons près de la surface de la cible, augmentant ainsi l'ionisation et la densité du plasma.Il en résulte une pulvérisation efficace et un dépôt de film de haute qualité, ce qui permet de l'utiliser pour des applications dans les domaines de l'optique, de l'électronique et des revêtements industriels.
Explication des principaux points :
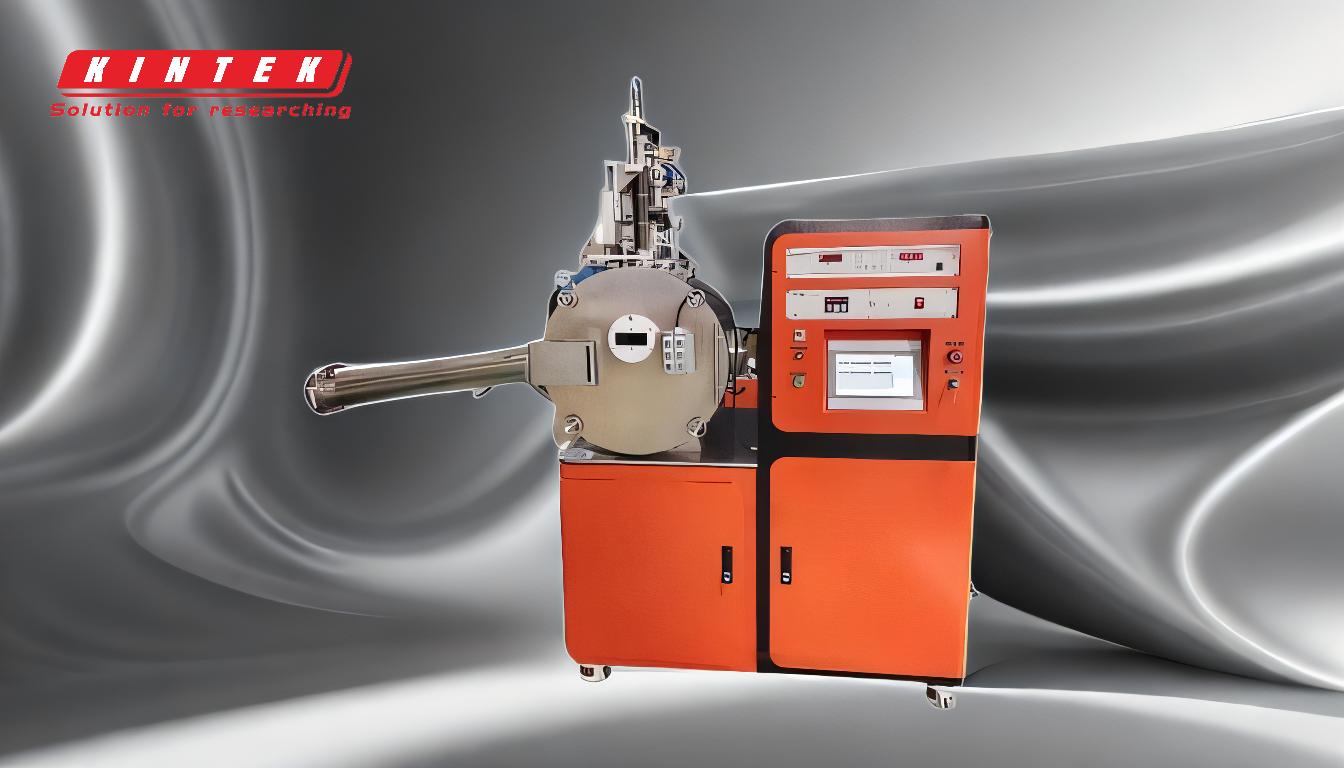
-
Mécanisme de base de la pulvérisation:
- La pulvérisation magnétron consiste à bombarder un matériau cible avec des ions à haute énergie, généralement à partir d'un gaz inerte comme l'argon.
- Les ions sont accélérés vers la cible par une tension négative appliquée à la cible (cathode).
- Lorsque les ions atteignent la cible, ils transfèrent de l'énergie cinétique aux atomes de la cible, ce qui les éjecte de la surface (pulvérisation).
-
Rôle du magnétron:
- Le magnétron génère un champ magnétique près de la surface de la cible, qui piège les électrons dans une trajectoire circulaire.
- Ce confinement augmente le temps de séjour des électrons dans le plasma, ce qui entraîne davantage de collisions avec les atomes du gaz et des taux d'ionisation plus élevés.
- L'augmentation de l'ionisation accroît la densité des ions disponibles pour la pulvérisation, améliorant ainsi l'efficacité du processus.
-
Formation et entretien du plasma:
- Le processus de pulvérisation se déroule dans une chambre à vide remplie d'un gaz inerte (par exemple, l'argon).
- L'énergie électrique est utilisée pour ioniser le gaz, créant ainsi un plasma composé d'ions, d'électrons et d'atomes neutres.
- Les électrons secondaires émis par la cible pendant la pulvérisation entrent en collision avec les atomes du gaz, ce qui contribue à entretenir le plasma.
-
Dépôt de couches minces:
- Les atomes éjectés de la cible (atomes pulvérisés) traversent le vide et se déposent sur un substrat.
- Les atomes déposés forment un film mince et uniforme présentant des propriétés telles qu'une densité élevée, une bonne adhérence et une épaisseur contrôlée.
- Ce procédé convient au dépôt d'une large gamme de matériaux, y compris les métaux, les alliages et les isolants.
-
Avantages de la pulvérisation cathodique magnétron:
- Faible température de dépôt:Convient aux substrats sensibles à la température.
- Films de haute qualité:Produit des revêtements denses, uniformes et sans défaut.
- Polyvalence:Peut déposer une grande variété de matériaux, y compris des métaux, des céramiques et des polymères.
- Évolutivité:Capable de revêtir des substrats de grande surface avec une épaisseur uniforme.
-
Applications:
- Revêtements optiques:Utilisé pour les revêtements antireflets, réfléchissants et conducteurs transparents.
- Électronique:Dépose des couches minces pour les semi-conducteurs, les capteurs et les écrans.
- Revêtements industriels:Fournit des revêtements résistants à l'usure et à la corrosion et des revêtements décoratifs.
-
Contrôle des processus:
- Les paramètres tels que la pression du gaz, la tension cible, l'intensité du champ magnétique et la température du substrat peuvent être ajustés pour optimiser les propriétés du film.
- Le processus est hautement contrôlable, ce qui permet de régler avec précision l'épaisseur, la composition et la microstructure du film.
-
Défis et considérations:
- L'utilisation des cibles peut être inégale en raison de la nature localisée du bombardement ionique.
- Le procédé nécessite un environnement sous vide poussé, dont le maintien peut s'avérer coûteux.
- Une sélection minutieuse du matériau cible et des paramètres du procédé est nécessaire pour obtenir les propriétés souhaitées du film.
En comprenant ces points clés, on peut apprécier la complexité et la polyvalence de la pulvérisation magnétron en tant que technique de revêtement, ce qui en fait un outil précieux pour diverses applications industrielles et scientifiques.
Tableau récapitulatif :
Aspect | Détails |
---|---|
Mécanisme | Bombardement d'une cible avec des ions à haute énergie pour éjecter les atomes en vue du dépôt. |
Rôle du magnétron | Confiner les électrons près de la cible, ce qui augmente l'ionisation et l'efficacité. |
Formation du plasma | Gaz inerte ionisé pour créer un plasma qui alimente le processus de pulvérisation. |
Avantages | Faible température de dépôt, films de haute qualité, polyvalence, évolutivité. |
Applications | Revêtements optiques, électronique, revêtements industriels. |
Contrôle du processus | Paramètres ajustables pour des propriétés de film précises. |
Défis | Utilisation inégale des cibles, coûts élevés du vide, sélection des matériaux. |
Vous souhaitez tirer parti de la pulvérisation magnétron pour vos projets ? Contactez nous dès aujourd'hui pour en savoir plus !