Le moulage par induction est une méthode moderne et efficace de fusion des métaux par induction électromagnétique.Ce procédé présente plusieurs avantages, notamment celui d'améliorer la qualité des produits finis.En tirant parti des courants induits, la coulée par induction assure une distribution uniforme des éléments dans l'alliage, ce qui permet d'obtenir des produits de meilleure qualité.Nous examinerons ci-dessous les principaux avantages de la coulée par induction en détail.
Les points clés expliqués :
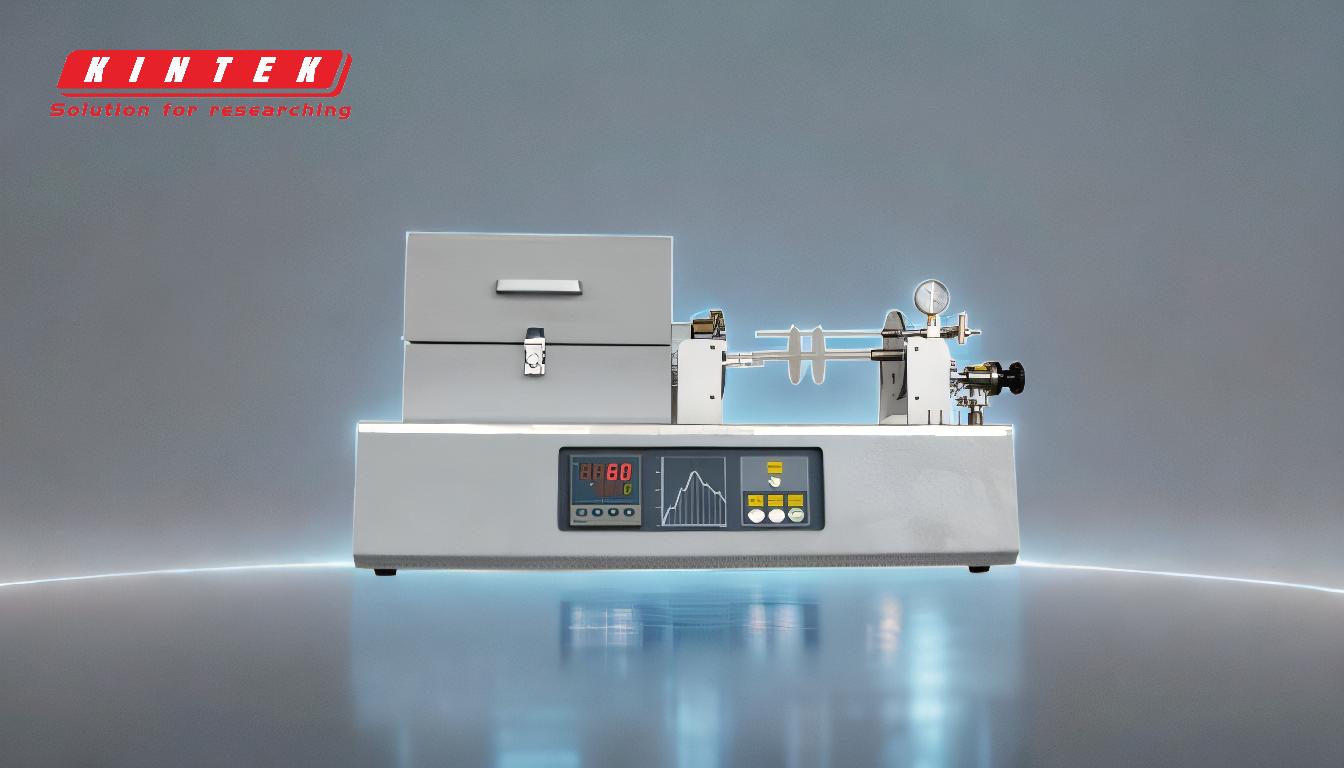
-
Amélioration de la qualité des produits finis
- Le moulage par induction améliore la qualité des produits finis en remélangeant les éléments présents dans l'alliage de fusion.Les courants induits créent un effet de brassage qui assure une dispersion uniforme de tous les éléments dans l'alliage.
- Cette uniformité élimine les incohérences, telles que la ségrégation ou la composition inégale, qui sont courantes dans les méthodes de fusion traditionnelles.En conséquence, le produit final présente des propriétés mécaniques supérieures, telles que la solidité, la durabilité et la résistance à l'usure.
-
Efficacité énergétique
- Le moulage par induction est très économe en énergie par rapport aux méthodes traditionnelles telles que les fours à gaz ou à charbon.Le processus chauffe directement le métal à l'aide de champs électromagnétiques, ce qui minimise les pertes de chaleur et réduit la consommation d'énergie.
- Cette efficacité permet non seulement de réduire les coûts d'exploitation, mais aussi de contribuer à un processus de fabrication plus durable en réduisant les émissions de carbone.
-
Précision et contrôle
- Le procédé de moulage par induction permet un contrôle précis de la température, ce qui est essentiel pour obtenir les propriétés souhaitées du matériau.Les opérateurs peuvent régler avec précision le processus de chauffage pour répondre aux exigences d'alliages spécifiques.
- Ce niveau de contrôle garantit des résultats cohérents, réduit la probabilité de défauts et permet la production de composants complexes ou de haute précision.
-
Des taux de fusion plus rapides
- Le moulage par induction chauffe rapidement les métaux, ce qui réduit considérablement les temps de fusion par rapport aux méthodes conventionnelles.Cette rapidité augmente le rendement de la production et permet aux fabricants de respecter des délais serrés sans compromettre la qualité.
- Le processus de chauffage rapide minimise également le risque d'oxydation ou de contamination, ce qui améliore encore la qualité du produit final.
-
Un processus plus propre et plus sûr
- Contrairement aux méthodes traditionnelles qui reposent sur la combustion, le moulage par induction ne produit ni flammes, ni fumée, ni émissions nocives.Cela permet de créer un environnement de travail plus propre et de réduire les risques sur le lieu de travail.
- En outre, l'absence de flammes nues minimise le risque d'accident, ce qui fait du moulage par induction une option plus sûre pour les opérateurs.
-
Polyvalence des applications
- Le moulage par induction convient à une large gamme de métaux et d'alliages, notamment l'acier, l'aluminium, le cuivre et les métaux précieux.Cette polyvalence en fait un choix idéal pour des industries telles que l'aérospatiale, l'automobile, la bijouterie et l'électronique.
- La capacité à traiter différents matériaux avec des résultats cohérents fait du moulage par induction un outil précieux pour les fabricants ayant des besoins de production diversifiés.
-
Réduction des déchets et des pertes de matériaux
- Le chauffage précis et l'action d'agitation de la coulée par induction minimisent la perte de matière due à l'oxydation ou à l'évaporation.Cette efficacité réduit les déchets et garantit qu'une plus grande partie de la matière première est utilisée dans le produit final.
- La diminution des pertes de matière se traduit par des économies et un processus de production plus durable.
En conclusion, le moulage par induction offre de nombreux avantages, notamment une meilleure qualité des produits, une efficacité énergétique, un contrôle précis, des taux de fusion plus rapides et un processus plus propre et plus sûr.Sa polyvalence et sa capacité à réduire les déchets en font un choix privilégié pour la fabrication moderne dans diverses industries.En tirant parti des avantages du moulage par induction, les fabricants peuvent obtenir des produits de meilleure qualité tout en optimisant leurs processus de production.
Tableau récapitulatif :
Avantage | Description de l'avantage |
---|---|
Qualité améliorée | La distribution uniforme des éléments garantit des propriétés mécaniques supérieures. |
Efficacité énergétique | Le chauffage direct minimise les pertes de chaleur, réduisant ainsi la consommation d'énergie et les coûts. |
Précision et contrôle | Un contrôle précis de la température permet d'obtenir des résultats constants et sans défaut. |
Des taux de fusion plus rapides | Le chauffage rapide augmente le rendement de la production et minimise la contamination. |
Processus plus propre et plus sûr | Pas de flammes ni d'émissions nocives, ce qui crée un environnement de travail plus sûr et plus propre. |
Polyvalence | Convient à l'acier, à l'aluminium, au cuivre et aux métaux précieux dans toutes les industries. |
Réduction des déchets | Minimise les pertes de matériaux, ce qui permet de réaliser des économies et d'assurer une production durable. |
Prêt à améliorer votre processus de fabrication avec le moulage par induction ? Contactez nous dès aujourd'hui pour en savoir plus !