Les fours à induction sont principalement classés en deux catégories : les fours sans noyau et les fours à canal.Les fours à induction sans noyau utilisent une bobine de solénoïde refroidie à l'eau pour générer un champ magnétique alternatif qui induit des courants de Foucault dans le métal, provoquant sa fusion.Les fours à induction à canal, quant à eux, s'appuient sur une boucle de métal fondu agissant comme un enroulement secondaire à tour unique autour d'un noyau de fer.Ces deux types de fours sont largement utilisés pour la fusion et l'alliage de métaux avec des pertes minimales, bien qu'ils offrent des capacités d'affinage limitées.En outre, les fours à induction peuvent varier en taille, en capacité, en fréquence et en conception, ce qui les rend adaptés à différentes applications industrielles.
Explication des points clés :
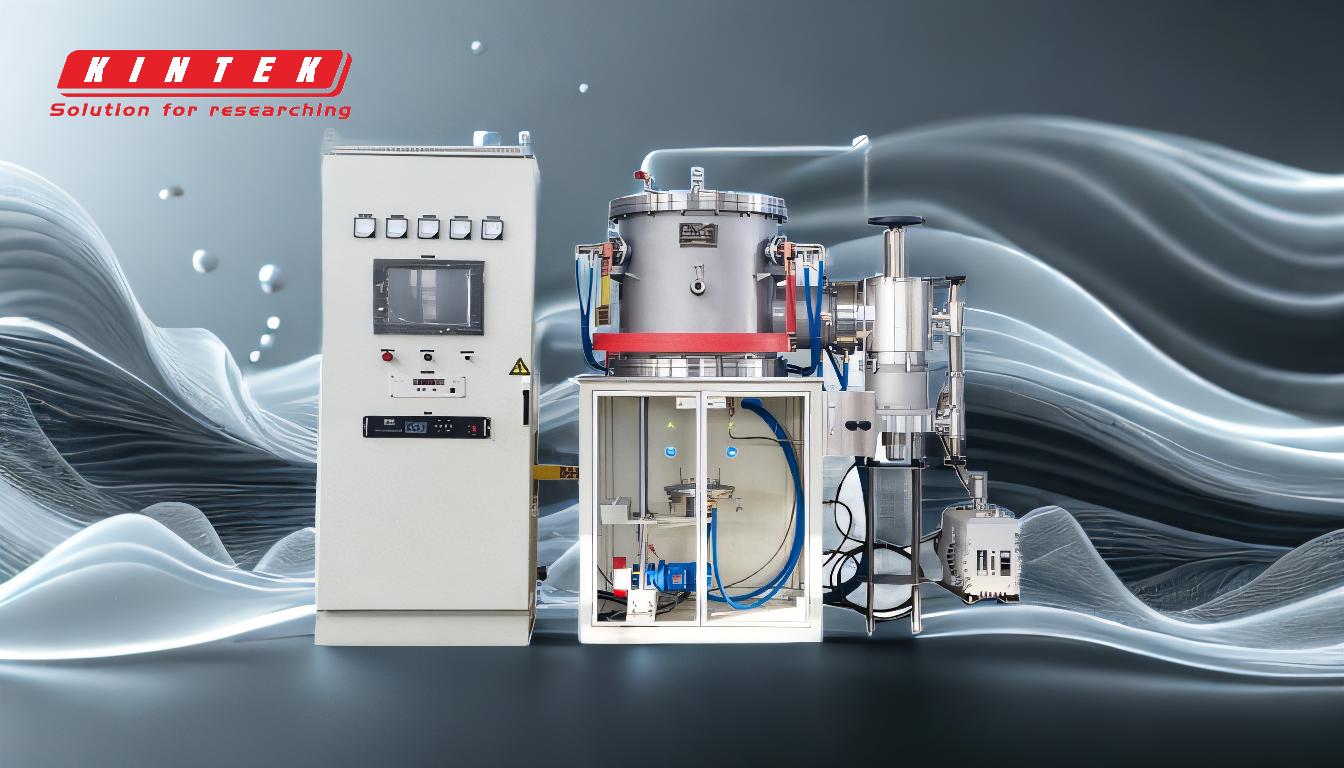
-
Fours à induction sans noyau:
- Conception:Les fours à induction sans noyau se composent d'un creuset entouré d'une bobine de courant alternatif refroidie à l'eau.Le métal à fondre est placé à l'intérieur du creuset.
- Principe de fonctionnement:Le courant alternatif dans la bobine génère un champ magnétique qui induit des courants de Foucault dans le métal.Ces courants génèrent de la chaleur et font fondre le métal.
- Applications:Idéal pour la fusion et l'alliage d'une grande variété de métaux, y compris l'acier, le fer, le cuivre et l'aluminium.
-
Avantages:
- Rendement élevé et taux de fusion rapide.
- Pertes de matière fondue et contamination minimales.
- Flexibilité dans la manipulation de différents métaux et alliages.
-
Inconvénients:
- Capacités de raffinage limitées.
- Nécessite un creuset, qui peut devoir être remplacé périodiquement.
-
Fours à induction à canal:
- Design:Les fours à induction à canal se caractérisent par une boucle de métal en fusion qui agit comme un enroulement secondaire à tour unique autour d'un noyau de fer.
- Principe de fonctionnement:La bobine primaire génère un champ magnétique, induisant un courant dans la boucle de métal fondu, qui chauffe et maintient le métal à l'état fondu.
- Applications:Utilisé couramment pour maintenir et surchauffer les métaux en fusion, en particulier dans les fonderies et les opérations de moulage de métaux.
-
Avantages:
- Rendement thermique élevé et économies d'énergie.
- Convient pour un fonctionnement continu et de longues durées de maintien en température.
- Peu d'entretien et longue durée de vie.
-
Inconvénients:
- Limité à certains types de métaux et d'alliages.
- Nécessite une charge pré-fondue pour amorcer la boucle.
-
Variations de taille, de capacité et de fréquence:
- Taille et capacité:Les fours à induction peuvent aller de petites unités de laboratoire à de grands fours industriels capables de traiter plusieurs tonnes de métal.
- Fréquence:La fréquence de fonctionnement des fours à induction peut varier, des fréquences plus élevées étant généralement utilisées pour les fours plus petits et des fréquences plus basses pour les fours plus grands.Cela influe sur la profondeur de pénétration des courants induits et sur l'efficacité du chauffage.
-
Comparaison avec d'autres types de fours:
- Fours à gaz naturel, à mazout et à propane:Ces fours reposent sur la combustion pour le chauffage et sont généralement utilisés pour le chauffage des locaux plutôt que pour la fonte des métaux.
- Fours électriques:Bien que les fours électriques puissent également être utilisés pour la fusion des métaux, les fours à induction offrent un chauffage plus rapide et un meilleur contrôle du processus de fusion.
-
Applications industrielles:
- Fonderies:Les fours à induction sont largement utilisés dans les fonderies pour la fusion et le moulage des métaux.
- Alliage de métaux:Ils sont idéaux pour créer des alliages métalliques spécifiques avec des compositions précises.
- Le recyclage:Les fours à induction sont souvent utilisés dans les opérations de recyclage des métaux en raison de leur efficacité et des pertes minimes de matière fondue.
-
Considérations pour les acheteurs:
- Efficacité énergétique:Les fours à induction sont généralement plus efficaces sur le plan énergétique que les fours traditionnels.
- Coûts d'exploitation:Si l'investissement initial peut être plus élevé, les coûts d'exploitation, y compris la maintenance et la consommation d'énergie, sont souvent moins élevés.
- La flexibilité:La capacité à traiter différents métaux et alliages rend les fours à induction polyvalents pour diverses applications industrielles.
En résumé, les fours à induction sans noyau et à canal sont les deux principaux types de fours, chacun ayant des conceptions et des applications distinctes.Les fours sans noyau sont polyvalents et efficaces pour la fusion d'une large gamme de métaux, tandis que les fours à canal sont idéaux pour maintenir et surchauffer les métaux en fusion.Les deux types de fours offrent des avantages significatifs en termes d'efficacité énergétique et de pertes minimales de matière fondue, ce qui en fait des outils essentiels dans les industries modernes de la métallurgie et du traitement des métaux.
Tableau récapitulatif :
Caractéristiques | Four à induction sans noyau | Four à induction à canal |
---|---|---|
Conception | Creuset avec bobine solénoïde refroidie à l'eau | Boucle de métal en fusion autour d'un noyau de fer |
Principe de fonctionnement | Le champ magnétique induit des courants de Foucault dans le métal. | Le champ magnétique induit un courant dans une boucle en fusion |
Applications | Fusion et alliage de divers métaux | Maintien et surchauffe des métaux en fusion |
Avantages | Rendement élevé, contamination minimale | Rendement thermique élevé, peu d'entretien |
Inconvénients | Affinage limité, remplacement du creuset | Types de métaux limités, charge pré-fondue |
Utilisations industrielles | Fonderies, alliage de métaux, recyclage | Fonderies, moulage de métaux |
Vous recherchez le four à induction adapté à vos besoins ? Contactez nos experts dès aujourd'hui pour des conseils personnalisés !