La trempe par induction, bien qu'efficace pour améliorer la résistance à l'usure et à la fatigue des pièces simples, présente plusieurs inconvénients.Elle ne convient pas aux pièces mécaniques complexes en raison de sa faible adaptabilité, ce qui limite son application à des pièces plus simples dans la production en chaîne d'assemblage.En outre, le procédé manque de capacité d'affinage, car les matériaux de charge doivent être exempts d'oxydes et de composition connue.Des éléments d'alliage peuvent également être perdus au cours du processus en raison de l'oxydation, ce qui nécessite de les ajouter à nouveau à la matière fondue.Ces limitations rendent la trempe par induction moins polyvalente et plus difficile à gérer dans certains scénarios de fabrication.
Explication des points clés :
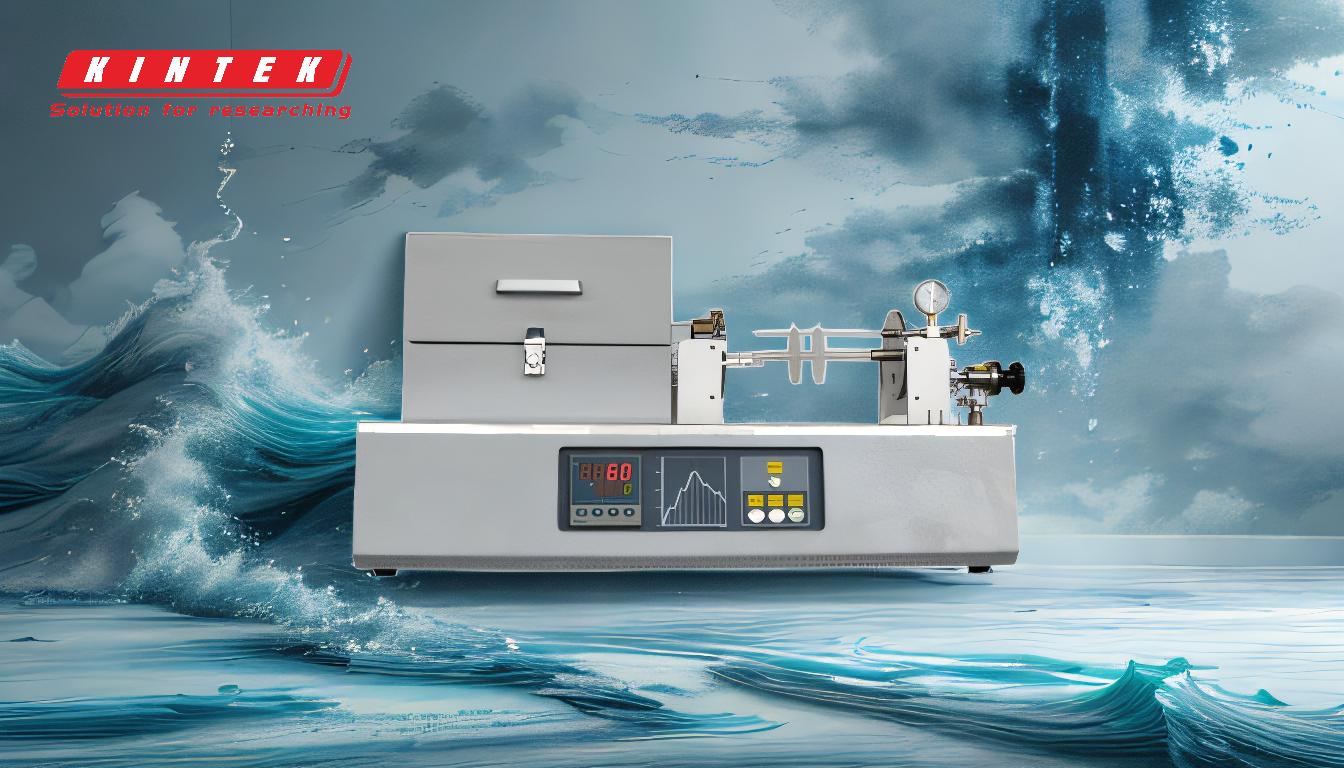
-
Mauvaise adaptation aux pièces complexes:
- La trempe par induction est principalement efficace pour les pièces simples, telles que celles utilisées dans la production en chaîne d'assemblage.En revanche, elle se heurte à des difficultés pour les pièces mécaniques complexes en raison de son adaptabilité limitée.Le processus nécessite un contrôle précis du chauffage et du refroidissement, ce qui peut être difficile à réaliser avec des géométries complexes.Cette limitation restreint son utilisation à des composants plus simples, ce qui réduit sa polyvalence dans la fabrication.
-
Manque de capacité de raffinage:
- Contrairement à d'autres procédés de trempe, la trempe par induction n'affine pas le matériau.Cela signifie que les matériaux de charge utilisés doivent déjà être exempts d'oxydes et avoir une composition connue.Toute impureté ou incohérence dans le matériau peut conduire à des résultats sous-optimaux, ce qui rend le processus moins tolérant et plus dépendant de matériaux d'entrée de haute qualité.
-
Perte d'éléments d'alliage:
- Au cours du processus de trempe par induction, certains éléments d'alliage peuvent être perdus en raison de l'oxydation.Cela peut altérer les propriétés du matériau et réduire l'efficacité du processus de durcissement.Pour y remédier, les fabricants peuvent être amenés à réintroduire ces éléments dans la masse fondue, ce qui rend le processus plus complexe et plus coûteux.Cette question est particulièrement problématique lorsque l'on travaille avec des matériaux qui nécessitent des compositions d'alliage précises pour obtenir des performances optimales.
-
Champ d'application limité:
- Les limites de cette technologie en matière de traitement des formes complexes et sa dépendance à l'égard de matériaux d'entrée de haute qualité restreignent son champ d'application.Elle convient mieux à la production en grande quantité de pièces simples, où les avantages d'une meilleure résistance à l'usure et à la fatigue peuvent être maximisés.Toutefois, pour des applications plus spécialisées ou plus complexes, d'autres méthodes de trempe peuvent s'avérer plus appropriées.
-
Défis en matière de contrôle des processus:
- Pour obtenir des résultats cohérents avec la trempe par induction, il faut contrôler avec précision les vitesses de chauffage et de refroidissement.Tout écart peut entraîner une trempe inégale, réduisant ainsi l'efficacité du processus.La nécessité d'un contrôle rigoureux peut accroître la complexité du processus de fabrication et nécessiter un équipement et une expertise plus sophistiqués.
En résumé, si la trempe par induction offre des avantages significatifs en termes de résistance à l'usure et à la fatigue pour les pièces simples, ses inconvénients - tels que la faible adaptabilité aux pièces complexes, le manque de capacité d'affinage et la perte potentielle d'éléments d'alliage - limitent son application à plus grande échelle.Ces facteurs le rendent moins adapté à certains scénarios de fabrication, en particulier ceux qui impliquent des géométries complexes ou des matériaux spécialisés.
Tableau récapitulatif :
Inconvénient | Description |
---|---|
Faible adaptabilité aux pièces complexes | Efficacité limitée pour les géométries complexes, ce qui limite l'utilisation à des composants plus simples. |
Absence de capacité d'affinage | Nécessite des matériaux de haute qualité, exempts d'oxyde ; pas d'affinage au cours du processus. |
Perte d'éléments d'alliage | L'oxydation au cours de la trempe peut entraîner la perte d'éléments d'alliage, ce qui nécessite un réajustement. |
Champ d'application limité | Convient mieux à la production en grande quantité de pièces simples ; moins efficace pour les matériaux spécialisés. |
Défis en matière de contrôle des processus | Le contrôle précis des taux de chauffage et de refroidissement est nécessaire pour obtenir des résultats cohérents. |
Vous avez besoin d'une solution de trempe adaptée à vos besoins ? Contactez nous dès aujourd'hui pour explorer les alternatives !