Bien qu'il s'agisse d'un processus de fabrication largement utilisé, le moulage des métaux présente plusieurs inconvénients qui peuvent avoir une incidence sur le coût, la qualité et l'efficacité.Ces inconvénients comprennent des coûts initiaux élevés, des limitations dans le choix des matériaux, des risques de défauts, des préoccupations environnementales et des difficultés à obtenir une précision dimensionnelle.Il est essentiel de comprendre ces inconvénients pour que les fabricants et les acheteurs puissent décider en connaissance de cause si le moulage des métaux est la meilleure méthode pour leur application spécifique.
Explication des principaux points :
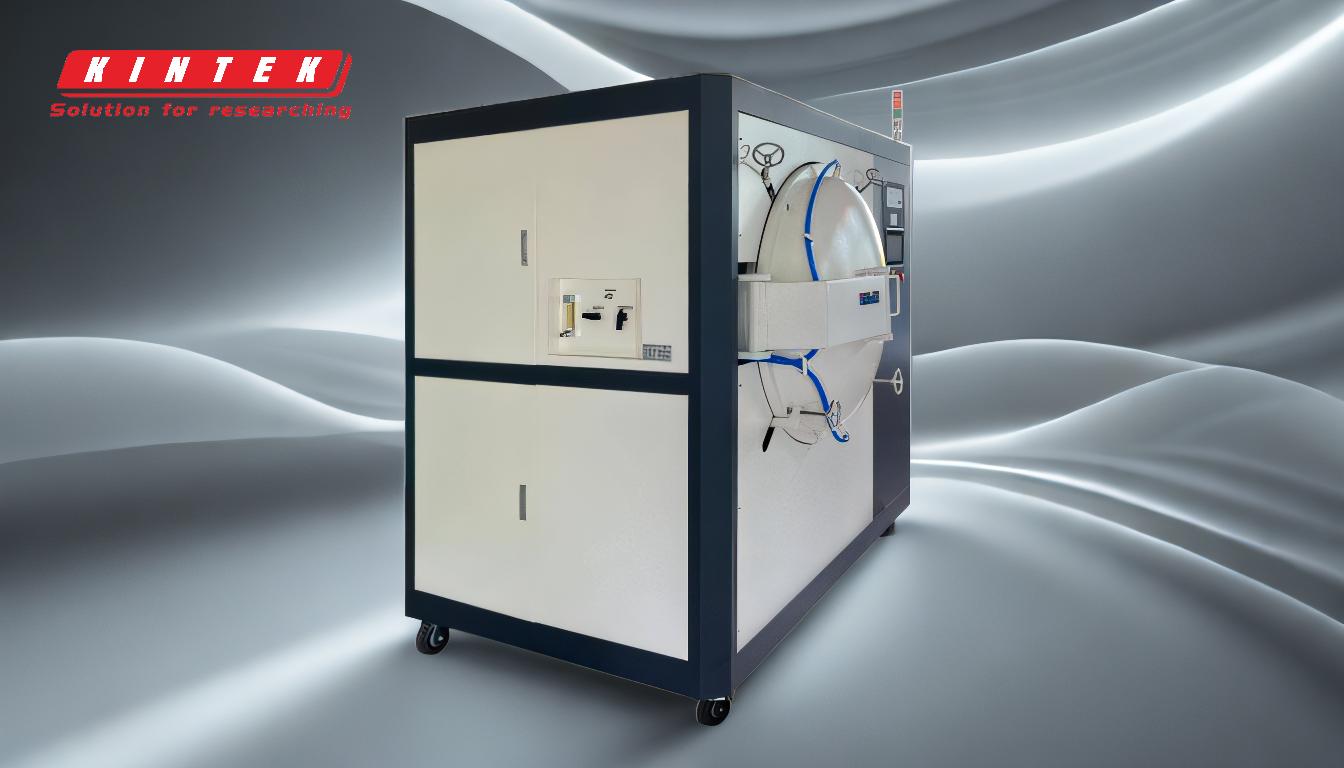
-
Des coûts initiaux élevés:
- Le moulage des métaux nécessite un investissement initial important dans l'équipement, les moules et l'outillage.La création de moules, en particulier pour les formes complexes, peut être coûteuse et prendre beaucoup de temps.
- En outre, le processus nécessite souvent des machines spécialisées et une main-d'œuvre qualifiée, ce qui augmente encore les coûts.
-
Limites des matériaux:
- Tous les métaux ne conviennent pas au moulage.Certains matériaux peuvent avoir de mauvaises caractéristiques d'écoulement ou ne pas se solidifier correctement, ce qui entraîne des défauts.
- Le choix du matériau peut également être limité par la nécessité d'équilibrer des propriétés telles que la résistance, la ductilité et la conductivité thermique.
-
Risque de défauts:
- Le moulage des métaux est sujet à divers défauts tels que la porosité, le retrait et les inclusions.Ces défauts peuvent compromettre l'intégrité structurelle et les performances du produit final.
- Des inspections post-coulée et des mesures de contrôle de la qualité sont souvent nécessaires pour identifier et résoudre ces problèmes, ce qui augmente les coûts et les délais.
-
Préoccupations environnementales:
- Le processus de coulée des métaux peut générer des quantités importantes de déchets, notamment de la ferraille, du sable usagé et des émissions.L'élimination et le traitement appropriés de ces déchets sont nécessaires pour minimiser l'impact sur l'environnement.
- La consommation d'énergie au cours des processus de fusion et de moulage peut également être élevée, ce qui contribue à l'empreinte carbone globale.
-
Défis à relever pour atteindre une précision dimensionnelle élevée:
- Il peut être difficile d'obtenir des tolérances serrées et des dimensions précises avec le moulage des métaux, en particulier pour les géométries complexes.Cela peut nécessiter des processus d'usinage ou de finition supplémentaires, ce qui augmente les délais et les coûts de production.
- Les variations de la vitesse de refroidissement et du retrait peuvent entraîner des incohérences dimensionnelles, ce qui nécessite une conception et un contrôle des processus minutieux pour les atténuer.
-
Cycles de production longs:
- Le processus de moulage des métaux, de la création du moule au produit final, peut prendre beaucoup de temps.Cela peut être un inconvénient dans les industries où la rapidité de production et les délais d'exécution sont essentiels.
- Le besoin de refroidissement et de solidification prolonge encore le cycle de production, en particulier pour les pièces moulées de grande taille ou à parois épaisses.
-
Risques pour la santé et la sécurité:
- Le processus de moulage des métaux implique des températures élevées et du métal en fusion, ce qui présente des risques importants pour la santé et la sécurité des travailleurs.Des mesures de sécurité et des équipements de protection adéquats sont essentiels pour atténuer ces risques.
- L'exposition aux fumées, à la poussière et au bruit peut également avoir des conséquences à long terme sur la santé des travailleurs.
En conclusion, si le moulage des métaux offre de nombreux avantages, tels que la possibilité de produire des formes complexes et des composants de grande taille, il est important d'examiner attentivement les inconvénients qui y sont associés.Il s'agit notamment des coûts élevés, des limitations des matériaux, des défauts potentiels, de l'impact sur l'environnement, des difficultés à obtenir des dimensions précises, des longs cycles de production et des risques pour la santé et la sécurité.En comprenant ces inconvénients, les fabricants et les acheteurs peuvent prendre des décisions plus éclairées et explorer d'autres méthodes si nécessaire.
Tableau récapitulatif :
Inconvénient | Description |
---|---|
Coûts initiaux élevés | Investissement important dans l'équipement, les moules et la main-d'œuvre qualifiée. |
Limites des matériaux | Tous les métaux ne conviennent pas au moulage en raison de problèmes d'écoulement et de solidification. |
Risque de défauts | Sujet à la porosité, au rétrécissement et aux inclusions, ce qui nécessite des inspections coûteuses. |
Problèmes environnementaux | Génère des déchets, des émissions et une forte consommation d'énergie. |
Défis en matière de précision dimensionnelle | Il est difficile d'obtenir des tolérances serrées, ce qui nécessite souvent un usinage supplémentaire. |
Cycles de production longs | Processus qui prend du temps, en particulier pour les pièces coulées de grande taille ou complexes. |
Risques pour la santé et la sécurité | Les températures élevées et l'exposition aux fumées, à la poussière et au bruit présentent des risques pour les travailleurs. |
Vous souhaitez en savoir plus sur les solutions de remplacement du moulage des métaux ? Contactez nos experts dès aujourd'hui pour des solutions sur mesure !