Les tolérances du frittage laser sont essentielles pour garantir la précision et la qualité des pièces imprimées en 3D.Le processus consiste à utiliser un laser pour fusionner couche par couche des matériaux en poudre, et il est essentiel d'obtenir des tolérances serrées pour les applications exigeant une grande précision.D'après la référence fournie, les techniques de frittage sur mesure permettent d'obtenir des tolérances de l'ordre du micron pour la linéarité et la concentricité.Ce niveau de précision est possible grâce à un contrôle avancé des paramètres du laser, des propriétés des matériaux et de l'optimisation du processus.
Explication des points clés :
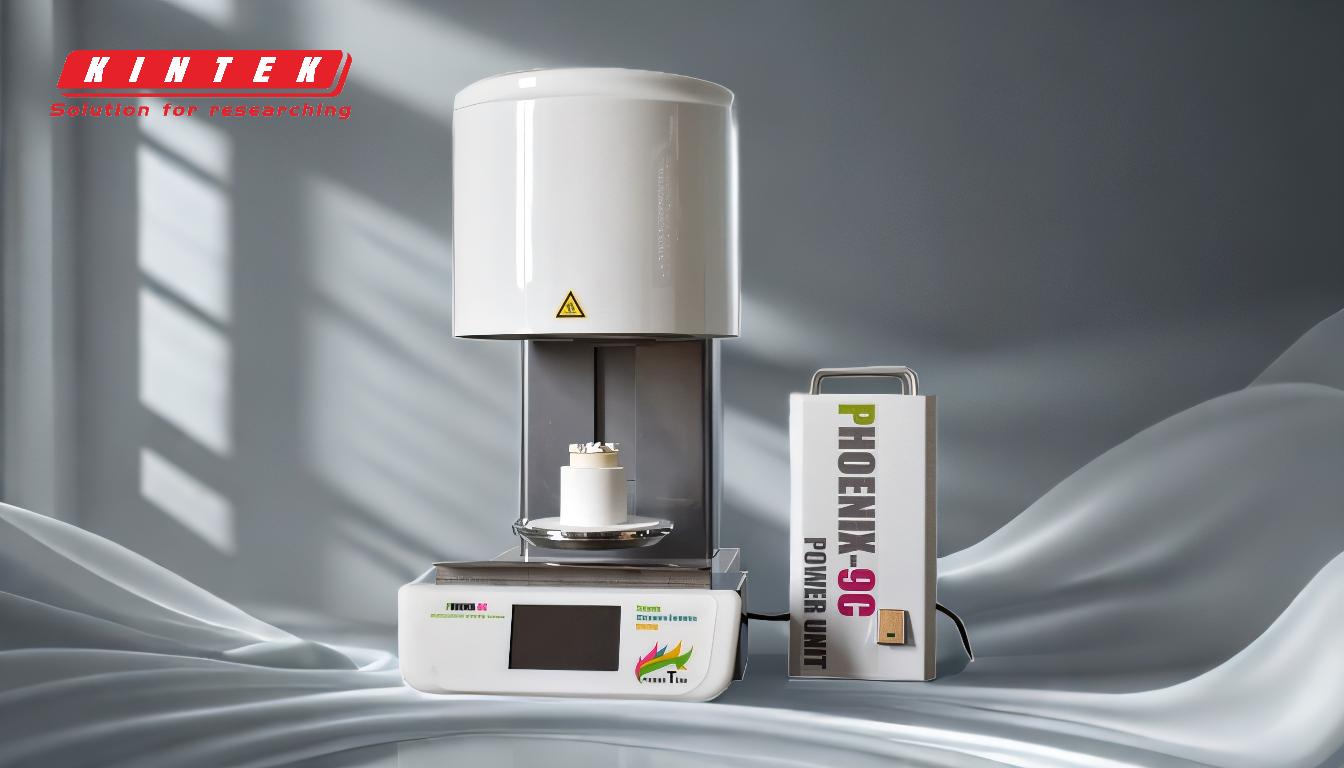
-
Définition des tolérances dans le frittage laser:
- Les tolérances font référence à l'écart admissible par rapport à une dimension ou une géométrie spécifiée dans une pièce fabriquée.
- Dans le frittage laser, les tolérances sont influencées par des facteurs tels que la puissance du laser, la vitesse de balayage, l'épaisseur de la couche et les propriétés du matériau.
-
Obtenir des tolérances de l'ordre du micron:
- La référence indique que des techniques de frittage adaptées peuvent garantir une linéarité et une concentricité de l'ordre du micron.
-
Ce niveau de précision est atteint grâce à
- un contrôle laser avancé:Contrôle précis de la puissance du laser et de la vitesse de balayage pour minimiser les variations.
- Optimisation des matériaux:Utilisation de matériaux dont la taille et la distribution des particules sont cohérentes afin de garantir un frittage uniforme.
- Surveillance du processus:Surveillance et ajustement en temps réel du processus de frittage pour maintenir des tolérances serrées.
-
Facteurs influençant les tolérances:
- Paramètres du laser:L'intensité, la focalisation et le schéma de balayage du laser ont un impact significatif sur la précision de la pièce frittée.
- Épaisseur de la couche:Des couches plus fines permettent généralement une plus grande précision mais peuvent augmenter le temps de fabrication.
- Propriétés des matériaux:La conductivité thermique, le point de fusion et la taille des particules du matériau influencent la qualité du frittage et la précision dimensionnelle finale.
- Étalonnage de la machine:Un étalonnage régulier de la machine de frittage laser est essentiel pour maintenir des performances constantes.
-
Applications nécessitant des tolérances serrées:
- Dispositifs médicaux:Les composants tels que les implants et les outils chirurgicaux nécessitent une grande précision pour garantir un ajustement et un fonctionnement corrects.
- Aérospatiale:Les pièces des avions et des engins spatiaux doivent respecter des tolérances strictes pour garantir la sécurité et les performances.
- Microélectronique:Les petits composants complexes des appareils électroniques nécessitent souvent des tolérances de l'ordre de quelques microns.
-
Les défis du maintien des tolérances:
- Distorsion thermique:La chaleur générée pendant le frittage peut entraîner le gauchissement ou la déformation des pièces, ce qui affecte la précision des dimensions.
- Rétrécissement du matériau:Certains matériaux se rétractent en refroidissant, ce qui doit être pris en compte dans la conception et le processus de frittage.
- Finition de la surface:Obtenir une finition de surface lisse tout en maintenant des tolérances serrées peut s'avérer difficile.
-
Stratégies d'amélioration des tolérances:
- Optimisation des processus:Réglage fin des paramètres du laser et des stratégies de frittage pour minimiser les écarts.
- Post-traitement:Des techniques telles que l'usinage ou le polissage peuvent être utilisées pour obtenir les tolérances et la finition de surface souhaitées.
- Conception pour la fabrication additive (DfAM):Concevoir des pièces en tenant compte des tolérances de frittage, par exemple en incorporant des tolérances de rétrécissement ou de distorsion.
En conclusion, le frittage laser permet d'obtenir des tolérances de l'ordre du micron pour la linéarité et la concentricité grâce à des techniques avancées et à un contrôle minutieux des paramètres du processus.Cependant, le maintien de tolérances aussi étroites nécessite une combinaison de matériaux optimisés, un contrôle précis du laser et une surveillance approfondie du processus.Ces tolérances sont essentielles pour les applications de haute précision dans des secteurs tels que le médical, l'aérospatial et la microélectronique.
Tableau récapitulatif :
Aspect clé | Détails |
---|---|
Définition de la tolérance | Écart admissible par rapport aux dimensions spécifiées dans les pièces frittées au laser. |
Atteindre une précision de 1 micron | Contrôle laser avancé, optimisation des matériaux et surveillance des processus en temps réel. |
Facteurs d'influence | Paramètres du laser, épaisseur de la couche, propriétés du matériau et étalonnage de la machine. |
Applications | Dispositifs médicaux, aérospatiale et microélectronique. |
Défis | Distorsion thermique, retrait du matériau et finition de la surface. |
Stratégies d'amélioration | Optimisation des processus, post-traitement et conception pour la fabrication additive (DfAM). |
Vous avez besoin d'un frittage laser de précision pour votre projet ? Contactez nos experts dès aujourd'hui pour en savoir plus !