Le traitement thermique est un processus critique pour les pièces moulées de grande taille, en particulier lorsque des propriétés mécaniques ou physiques spécifiques sont requises pour leur application prévue. Le processus consiste à chauffer la pièce moulée à une température spécifiée, à la maintenir à cette température pendant une durée prédéterminée, puis à la refroidir à l'aide de méthodes prescrites. L’objectif est d’améliorer des propriétés telles que la dureté, la solidité et la résistance à l’usure. Bien que toutes les pièces moulées ne nécessitent pas de traitement thermique, celui-ci est essentiel pour les applications exigeant des performances supérieures. Le processus de traitement thermique spécifique dépend du matériau, des propriétés souhaitées et des exigences de l'application.
Points clés expliqués :
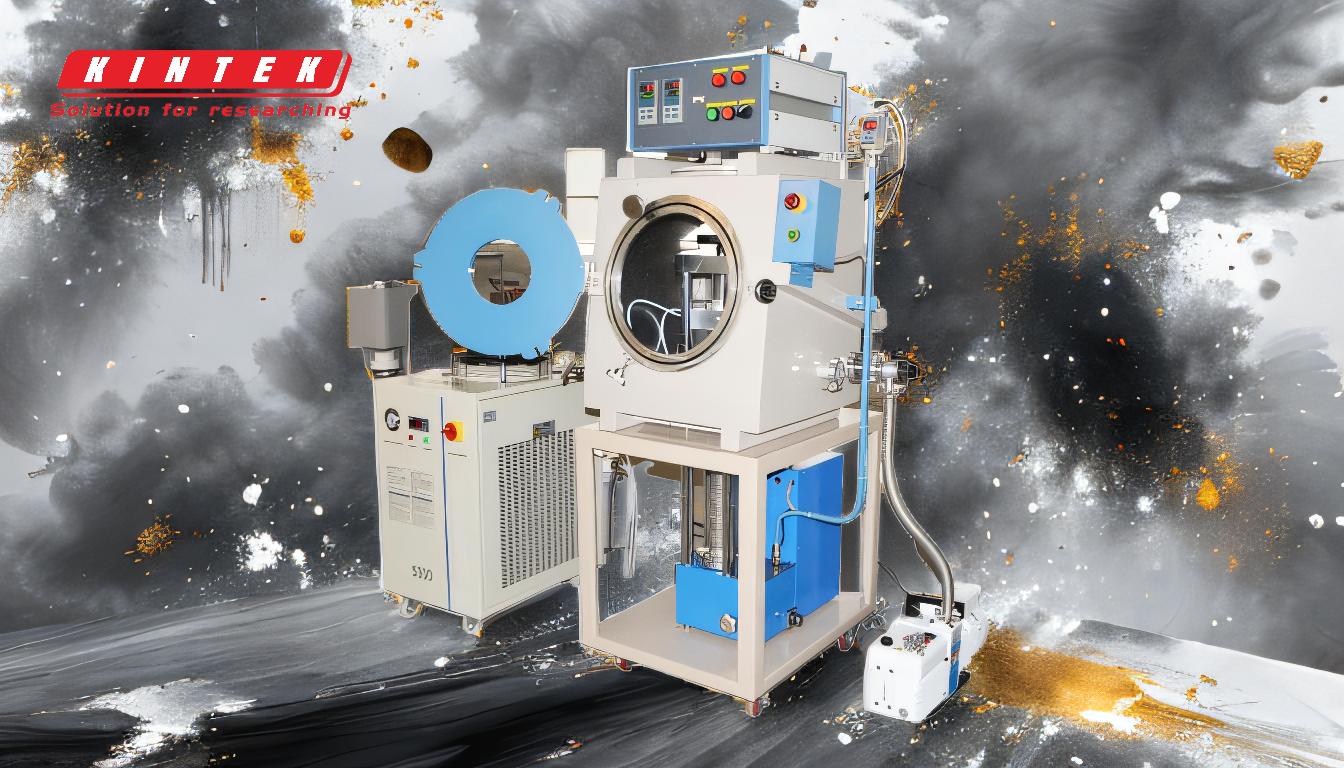
-
Objectif du traitement thermique pour les grandes pièces moulées
- Le traitement thermique est utilisé pour améliorer les propriétés mécaniques et physiques des pièces moulées de grande taille, telles que la dureté, la résistance, la ductilité et la résistance à l'usure et à la corrosion.
- Cela est particulièrement important pour les pièces moulées utilisées dans des applications exigeantes, telles que les machines lourdes, l'aérospatiale ou les composants automobiles, où les performances sous contrainte sont essentielles.
- Le traitement thermique peut également soulager les contraintes internes provoquées lors du processus de coulée, réduisant ainsi le risque de fissuration ou de déformation.
-
Étapes de base du traitement thermique
- Chauffage: La pièce moulée est chauffée à une température spécifique, qui peut aller jusqu'à 2 400 °F (1 315 °C), en fonction du matériau et du résultat souhaité.
- Holding: La coulée est maintenue à la température cible pendant une durée déterminée, qui peut varier de quelques secondes à plus de 60 heures. Cette durée garantit une répartition uniforme de la chaleur et permet des changements microstructuraux.
- Refroidissement: La pièce moulée est refroidie selon une méthode contrôlée, telle que le refroidissement à l'air, la trempe à l'huile ou la trempe à l'eau. La vitesse de refroidissement a un impact significatif sur les propriétés finales du matériau.
-
Types de processus de traitement thermique pour les grandes pièces moulées
- Recuit : Ce processus consiste à chauffer la pièce moulée à une température élevée, puis à la refroidir lentement. Il adoucit le matériau, améliore la ductilité et réduit les contraintes internes.
- Normalisation : Semblable au recuit, mais le processus de refroidissement est plus rapide. Il affine la structure des grains et améliore les propriétés mécaniques.
- Trempe : La pièce moulée est rapidement refroidie pour atteindre une dureté et une résistance élevées. Cependant, cela peut introduire des contraintes internes, qui peuvent nécessiter un revenu.
- Trempe : Après la trempe, la pièce moulée est réchauffée à une température plus basse pour réduire la fragilité et améliorer la ténacité.
- Soulagement du stress : Ce processus consiste à chauffer la pièce moulée à une température modérée, puis à la refroidir lentement pour soulager les contraintes résiduelles sans altérer de manière significative la microstructure.
-
Facteurs influençant le traitement thermique
- Composition du matériau : Différents matériaux (par exemple l'acier, la fonte, l'aluminium) nécessitent des processus de traitement thermique spécifiques pour obtenir les propriétés souhaitées.
- Taille et géométrie du moulage : Les pièces moulées de grande taille peuvent nécessiter un équipement spécialisé et des temps de chauffage/refroidissement plus longs pour garantir un traitement uniforme.
- Exigences de candidature : L'utilisation prévue de la pièce moulée détermine les propriétés nécessaires, telles que la dureté, la résistance ou la résistance à l'usure.
- Taux de refroidissement : La méthode et la vitesse de refroidissement (par exemple, air, huile, eau) affectent directement les propriétés finales du matériau.
-
Défis liés au traitement thermique de grandes pièces moulées
- Chauffage uniforme : Assurer une répartition homogène de la chaleur dans une grande pièce moulée peut être un défi, nécessitant un contrôle précis des conditions du four.
- Distorsion et fissuration : Un refroidissement rapide ou un chauffage inégal peuvent entraîner des déformations ou des fissures, en particulier dans les géométries complexes.
- Besoins en énergie et en temps : Le traitement thermique de grandes pièces moulées est gourmand en énergie et prend du temps, nécessitant souvent un équipement et une expertise spécialisés.
-
Lorsque le traitement thermique n'est pas requis
- Certaines pièces moulées peuvent être utilisées « telles quelles » si leurs propriétés matérielles répondent déjà aux exigences de l'application.
- Le traitement thermique peut ne pas être nécessaire pour les composants non critiques ou ceux fabriqués à partir de matériaux possédant intrinsèquement les propriétés souhaitées.
-
Importance de l’inspection post-traitement
- Après le traitement thermique, les grandes pièces moulées doivent être inspectées pour vérifier leur précision dimensionnelle, leur qualité de surface et leurs propriétés mécaniques.
- Les méthodes de contrôle non destructives, telles que l’inspection par ultrasons ou par magnétoscopie, peuvent détecter des défauts internes ou des incohérences.
En sélectionnant et en appliquant soigneusement le processus de traitement thermique approprié, les fabricants peuvent garantir que les pièces moulées de grande taille répondent aux exigences strictes de leurs applications prévues, améliorant ainsi les performances, la durabilité et la fiabilité.
Tableau récapitulatif :
Aspect | Détails |
---|---|
But | Améliore la dureté, la résistance, la ductilité et la résistance à l'usure et à la corrosion. |
Étapes de base | Chauffage, maintien en température, refroidissement contrôlé. |
Types de processus | Recuit, normalisant, trempe, revenu, soulagement du stress. |
Facteurs clés | Matériau, taille/géométrie, besoins d’application, vitesse de refroidissement. |
Défis | Chauffage uniforme, déformation/fissuration, besoins en énergie/temps. |
Post-traitement | Inspection de la précision, de la qualité de la surface et des propriétés mécaniques. |
Optimisez vos grandes pièces moulées avec des solutions expertes en traitement thermique— contactez-nous aujourd'hui !