La température de calcination joue un rôle essentiel dans la détermination des propriétés structurelles, chimiques et physiques des matériaux. Elle influence les transformations de phase, la cristallinité, la taille des particules, la porosité et la surface, qui à leur tour affectent les performances du matériau dans diverses applications. En contrôlant soigneusement la température de calcination, il est possible d'optimiser les propriétés du matériau pour des utilisations spécifiques, telles que la catalyse, le stockage de l'énergie ou les céramiques. Toutefois, des températures trop élevées peuvent entraîner des effets indésirables, tels que le frittage, l'agglomération ou la décomposition des phases. Il est essentiel de comprendre l'influence de la température de calcination pour adapter les matériaux à des exigences fonctionnelles spécifiques.
Explication des points clés :
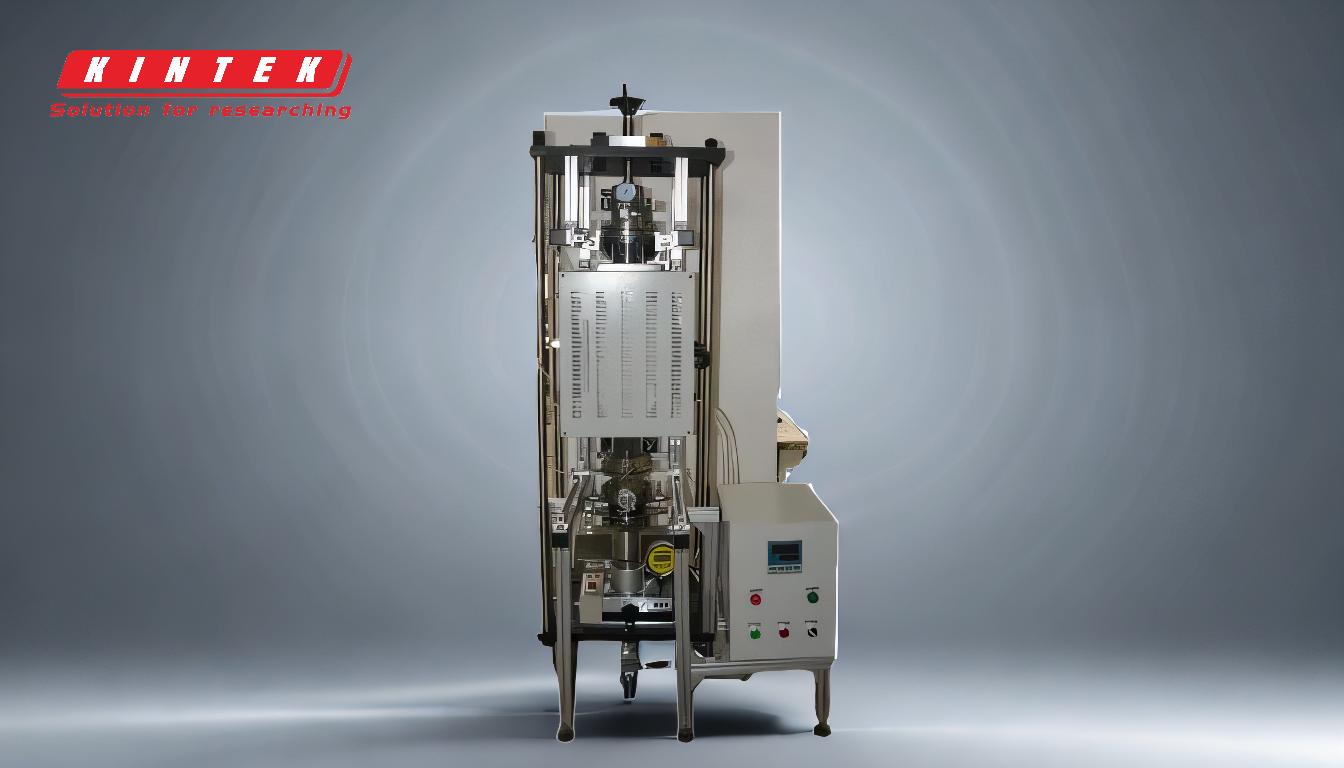
-
Transformation de phase et cristallinité :
- Explication : La température de calcination affecte directement la composition des phases et la cristallinité des matériaux. À basse température, les matériaux peuvent rester amorphes ou partiellement cristallins. À mesure que la température augmente, des transitions de phase se produisent, conduisant à la formation de phases cristallines plus stables. Par exemple, dans la production de céramiques, la calcination à des températures plus élevées peut favoriser la formation de phases cristallines souhaitées comme l'alumine ou la zircone.
- Impact : Un contrôle adéquat de la température de calcination garantit la formation de la phase souhaitée, ce qui est crucial pour obtenir des propriétés mécaniques, thermiques et chimiques optimales.
-
Taille et morphologie des particules :
- Explication : La température de calcination influence la croissance des particules. À des températures modérées, les particules peuvent croître légèrement, améliorant la cristallinité sans agglomération significative. Cependant, à des températures trop élevées, les particules peuvent se fritter ou fusionner, ce qui entraîne une augmentation de la taille des particules et une réduction de leur surface.
- Impact : Des particules de petite taille et une morphologie contrôlée sont souvent souhaitables pour des applications telles que la catalyse, où une surface élevée améliore la réactivité. Une croissance excessive des particules peut réduire les performances.
-
Porosité et surface :
- Explication : La température de calcination affecte la porosité et la surface des matériaux. Des températures plus basses peuvent préserver une surface et une porosité plus élevées, ce qui est bénéfique pour des applications telles que l'adsorption ou la catalyse. Des températures plus élevées peuvent provoquer l'effondrement ou la densification des pores, ce qui réduit la surface.
- Impact : L'adaptation de la température de calcination permet d'optimiser la porosité et la surface, qui sont essentielles pour les applications nécessitant une réactivité ou une capacité d'adsorption élevées.
-
Stabilité chimique et décomposition :
- Explication : Certains matériaux subissent une décomposition chimique ou un changement de phase à des températures spécifiques. Par exemple, les hydroxydes ou les carbonates métalliques se décomposent en oxydes pendant la calcination. La température doit être soigneusement contrôlée pour assurer une décomposition complète sans dégrader le matériau.
- Impact : Une calcination correcte garantit la formation de phases stables et de haute pureté, qui sont essentielles pour les applications dans les domaines de l'électronique, du stockage de l'énergie ou de la catalyse.
-
Frittage et agglomération :
- Explication : À des températures très élevées, il peut se produire un frittage, où les particules fusionnent, ce qui réduit la surface et la porosité. L'agglomération peut également entraîner une distribution inégale de la taille des particules.
- Impact : Le frittage et l'agglomération peuvent avoir un effet négatif sur les performances des matériaux, en particulier dans les applications nécessitant une surface élevée ou une taille de particule uniforme.
-
Propriétés thermiques et mécaniques :
- Explication : La température de calcination influence les propriétés thermiques et mécaniques des matériaux. Des températures plus élevées améliorent généralement la résistance mécanique et la stabilité thermique, mais peuvent également entraîner une fragilité.
- Impact : Il est essentiel de comprendre l'équilibre entre la température et les propriétés des matériaux pour des applications telles que les matériaux réfractaires ou les céramiques structurelles.
-
Optimisation spécifique à l'application :
- Explication : Les propriétés des matériaux varient selon les applications. Par exemple, les catalyseurs peuvent avoir besoin d'une surface et d'une porosité élevées, tandis que les céramiques structurelles nécessitent une densité et une résistance mécanique élevées.
- Impact : En ajustant la température de calcination, les matériaux peuvent être optimisés pour des applications spécifiques, garantissant une performance et une efficacité maximales.
-
Efficacité énergétique et considérations financières :
- Explication : Des températures de calcination plus élevées nécessitent plus d'énergie, ce qui augmente les coûts de production. L'équilibre entre la température et les propriétés souhaitées du matériau est essentiel pour une fabrication rentable.
- Impact : L'optimisation de la température de calcination permet de réduire la consommation d'énergie et les coûts de production tout en obtenant les propriétés souhaitées du matériau.
En comprenant et en contrôlant l'influence de la température de calcination, les fabricants et les chercheurs peuvent adapter les matériaux à des exigences fonctionnelles spécifiques, garantissant ainsi des performances optimales dans un large éventail d'applications.
Tableau récapitulatif :
Aspect | Impact |
---|---|
Transformation de la phase | Détermine la cristallinité et la stabilité des phases pour obtenir les propriétés souhaitées des matériaux. |
Taille et morphologie des particules | Contrôle la croissance des particules et la surface pour améliorer la réactivité ou la résistance. |
Porosité et surface | Optimise la porosité pour une réactivité ou une capacité d'adsorption élevée. |
Stabilité chimique | Assure une décomposition complète sans dégrader la qualité des matériaux. |
Frittage et agglomération | Empêche la fusion des particules, en maintenant une taille et une surface uniformes. |
Propriétés thermiques et mécaniques | Équilibre entre la résistance, la stabilité et la fragilité pour des applications spécifiques. |
Optimisation spécifique à l'application | Adapter les matériaux à la catalyse, aux céramiques ou au stockage de l'énergie. |
Efficacité énergétique | Réduit la consommation d'énergie et les coûts de production tout en obtenant les propriétés souhaitées. |
Besoin d'aide pour optimiser la température de calcination de vos matériaux ? Contactez nos experts dès aujourd'hui !