Les fours à arc indirect sont principalement utilisés pour la fusion des métaux, en particulier dans les scénarios où un contrôle précis de la température et une contamination minimale sont essentiels. Ces fours sont bien adaptés à la fusion d'alliages de haute qualité, de métaux réfractaires et de matériaux spéciaux tels que l'acier inoxydable, l'acier résistant à la chaleur et les superalliages. La conception de l'arc indirect garantit que l'arc électrique n'entre pas directement en contact avec la charge, ce qui réduit la contamination et permet un chauffage uniforme. Ils sont donc idéaux pour les applications dans la recherche, les laboratoires et les industries nécessitant des métaux de haute pureté, telles que l'aérospatiale, la fabrication d'outils et la production de matériaux avancés.
Explication des points clés :
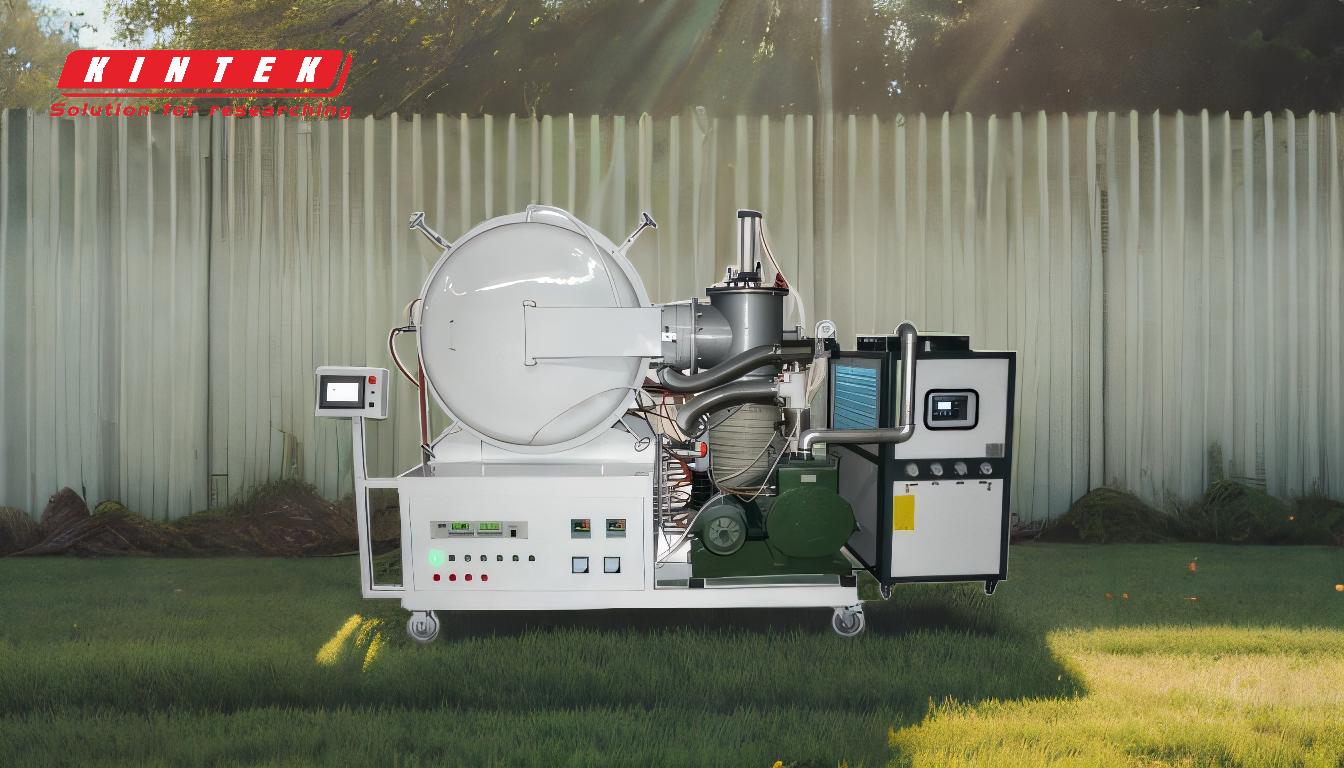
-
Principale application des fours à arc indirect:
- Les fours à arc indirect sont principalement utilisés pour la fusion des métaux les matériaux utilisés dans la fabrication des produits chimiques sont nombreux, en particulier ceux qui exigent une grande pureté et un contrôle précis de la température. Il s'agit de matériaux tels que l'acier inoxydable, l'acier résistant à la chaleur et les superalliages (par exemple, les alliages à base de nickel, de cobalt et de fer).
- La conception de l'arc indirect garantit que l'arc n'entre pas directement en contact avec la charge, ce qui minimise la contamination et permet un chauffage uniforme.
-
Conception et mécanisme de chauffage:
- Dans un four à arc indirect, l'arc électrique est frappé entre deux électrodes et la chaleur est transférée à la charge par l'intermédiaire de le rayonnement et la conduction .
- L'arc électrique chauffe la surface supérieure de la charge et la chaleur est ensuite transmise aux couches inférieures, ce qui garantit une fusion homogène sans contact direct entre l'arc et le matériau.
-
Avantages des fours à arc indirect:
- Contamination minimale: L'arc ne touchant pas la charge, le risque d'introduction d'impuretés dans le métal en fusion est moindre.
- Contrôle précis de la température: Le mécanisme de chauffage indirect permet de mieux contrôler le processus de fusion, ce qui est crucial pour les alliages de haute qualité et les métaux spéciaux.
- Chauffage uniforme: La conduction de la chaleur de la surface supérieure vers les couches inférieures assure une fonte constante tout au long de la charge.
-
Matériaux courants fondus:
- Acier inoxydable: Utilisé dans les applications nécessitant une résistance à la corrosion et une durabilité.
- Acier résistant à la chaleur: Essentiel pour les environnements à haute température, tels que l'aérospatiale et la production d'énergie.
- Superalliages: Les alliages à base de nickel, de cobalt et de fer sont fondus pour être utilisés dans des conditions extrêmes, comme les moteurs à réaction et les turbines à gaz.
- Métaux réfractaires: Les matériaux tels que le tungstène et le molybdène, qui ont des points de fusion élevés, sont souvent traités dans des fours à arc indirect.
-
Applications dans l'industrie et la recherche:
- Recherche en laboratoire: Les fours à arc indirect sont utilisés dans le cadre de la recherche pour étudier les propriétés des métaux réfractaires et des carbures métalliques.
- Aérospatiale et défense: Les métaux et alliages de haute pureté sont nécessaires pour les composants critiques de ces industries.
- Fabrication d'outils: Les aciers à outils et les aciers à roulements sont fondus pour produire des outils durables et performants.
- Matériaux avancés: Les matériaux magnétiques, les alliages élastiques et les alliages d'expansion sont traités pour des applications spécialisées.
-
Comparaison avec d'autres types de fourneaux:
- Fours à induction: Les fours à induction sont également utilisés pour la fusion des métaux, mais ils reposent sur l'induction électromagnétique pour générer de la chaleur. Les fours à arc indirect sont préférables lorsque le contact direct avec la charge doit être évité.
- Fours à induction sous vide: Ils sont utilisés pour la fusion de matériaux à haute performance tels que les superalliages, mais fonctionnent sous vide pour réduire davantage la contamination.
-
Efficacité énergétique et flexibilité:
- Les fours à arc indirect sont économes en énergie grâce à leur mécanisme de chauffage précis, qui minimise les pertes de chaleur.
- Ils offrent une grande souplesse dans le traitement d'une large gamme de matériaux, des métaux courants comme l'aluminium et le cuivre aux alliages avancés et aux métaux réfractaires.
En résumé, les fours à arc indirect sont des équipements spécialisés conçus pour fondre des métaux et des alliages de haute qualité avec un minimum de contamination. Leur mécanisme de chauffage unique et leur contrôle précis de la température les rendent indispensables dans les industries qui exigent des matériaux de haute pureté, telles que l'aérospatiale, la fabrication d'outils et la recherche sur les matériaux avancés.
Tableau récapitulatif :
Aspect | Détails |
---|---|
Application primaire | Fusion de métaux nécessitant une grande pureté et un contrôle précis de la température. |
Mécanisme de conception | L'arc électrique entre deux électrodes chauffe la charge par rayonnement/conduction. |
Avantages | Contamination minimale, contrôle précis de la température et chauffage uniforme. |
Matériaux communs | Acier inoxydable, acier résistant à la chaleur, superalliages et métaux réfractaires. |
Applications | Aérospatiale, fabrication d'outils, recherche en laboratoire et matériaux avancés. |
Efficacité énergétique | Le chauffage précis minimise les pertes de chaleur, ce qui le rend économe en énergie. |
Besoin d'une solution pour la fusion de métaux de haute pureté ? Contactez nos experts dès aujourd'hui pour en savoir plus sur les fours à arc indirect !