La perte de fusion d'un four à induction fait référence à la réduction du poids du métal pendant le processus de fusion en raison de facteurs tels que l'oxydation, l'évaporation et la formation de scories. Cette perte est influencée par plusieurs variables, notamment la vitesse de fusion, la configuration de puissance, la propreté de la charge, la conception du four et les matériaux réfractaires utilisés. Une charge propre, une longueur de bloc de four appropriée et des creusets appropriés tels que des creusets en quartz peuvent minimiser les pertes par fusion en améliorant l'efficacité et en réduisant la consommation de transfert de chaleur. De plus, une surchauffe due à un débit d'eau inapproprié, aux dimensions du revêtement du four ou à un matériau réfractaire peut exacerber les pertes par fusion. Comprendre ces facteurs permet d’optimiser les opérations du four et de réduire le gaspillage de matériaux.
Points clés expliqués :
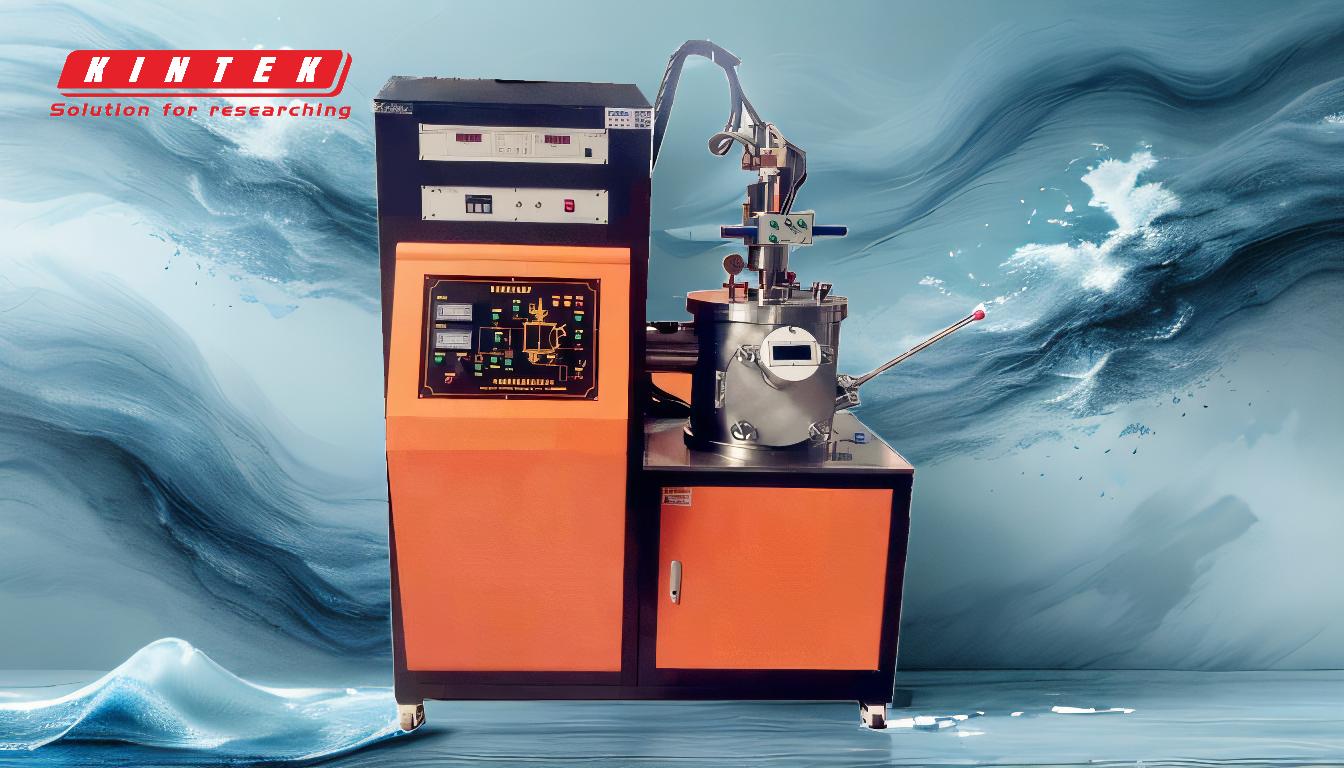
-
Définition de la perte de fusion:
- La perte par fusion fait référence à la réduction du poids du métal pendant le processus de fusion dans un four à induction. Cette perte est due à l'oxydation, à l'évaporation et à la formation de scories, inhérentes au processus de fusion.
-
Facteurs influençant la perte de fusion:
- Taux de fusion et configuration de puissance: Le taux de fusion, calculé comme (Puissance en kW) / (Consommation d'énergie standard en kWh/tonne), a un impact direct sur la perte de fusion. Des configurations de puissance plus élevée peuvent réduire le temps de fusion mais peuvent augmenter l'oxydation et l'évaporation si elles ne sont pas contrôlées.
- Propreté et taille de la charge: Une charge propre avec un minimum d'impuretés réduit la formation de scories et l'oxydation, minimisant ainsi les pertes par fusion. La taille de la charge affecte également l'uniformité de la fusion et la répartition de la chaleur.
- Matériaux Réfractaires et Creusets: Le type de matériaux réfractaires et de creusets utilisés, tels que les creusets en quartz, joue un rôle important dans la réduction des pertes par transfert de chaleur et l'amélioration de l'efficacité globale.
- Conception et revêtement du four: Des dimensions appropriées du revêtement du four et une quantité suffisante de matériau réfractaire évitent la surchauffe et l'endommagement du serpentin, ce qui pourrait autrement entraîner une perte de fusion accrue.
-
La surchauffe et son impact:
- La surchauffe du serpentin du four, provoquée par des restrictions dans le chemin d'écoulement de l'eau ou par une conception inappropriée du four, peut entraîner une augmentation des pertes de fusion. La surchauffe accélère l’oxydation et l’évaporation, contribuant ainsi à une plus grande perte de matériaux.
-
Calcul du taux et du temps de fusion:
- La vitesse de fusion est calculée selon la formule : (Puissance en kW) / (Consommation électrique standard en kWh/tonne) = (Poids du métal en kg) / (1000 kg). Par exemple, à 325 kW, la vitesse de fusion est de 520 kg/heure.
- Le temps de fusion est calculé selon la formule : (Puissance en kW * Temps en heures) / (Poids du métal en kg) = (Consommation électrique standard en kWh/tonne * 1 heure) / (1000 kg). Pour un four de 550 kg avec une alimentation de 325 kW, le temps de fusion est de 1,06 heure (64 minutes).
-
Stratégies d'optimisation:
- Chargement propre: S'assurer que la charge est exempte d'impuretés et de contaminants réduit la formation de scories et l'oxydation.
- Conception appropriée du four: Le maintien d'une longueur de bloc de four et de dimensions de revêtement appropriées évite la surchauffe et améliore l'efficacité.
- Creusets adaptés: L'utilisation de creusets comme les creusets en quartz réduit les pertes de transfert de chaleur et améliore l'efficacité de la fusion.
- Entretien régulier: L'inspection et l'entretien réguliers des chemins d'écoulement d'eau, des échangeurs de chaleur et des câbles d'alimentation évitent la surchauffe et garantissent des performances constantes.
En comprenant et en traitant ces facteurs, les opérateurs peuvent minimiser les pertes de fusion, améliorer l'efficacité du four et réduire les déchets de matériaux lors des opérations des fours à induction.
Tableau récapitulatif :
Facteur clé | Impact sur la perte de fusion |
---|---|
Taux de fusion et puissance | Une puissance plus élevée réduit le temps de fusion mais peut augmenter l'oxydation et l'évaporation. |
Propreté et taille de la charge | Les charges propres minimisent la formation de scories et l'oxydation, réduisant ainsi les pertes par fusion. |
Matériaux réfractaires | Des matériaux appropriés tels que les creusets en quartz réduisent les pertes de transfert de chaleur et améliorent l'efficacité. |
Conception et revêtement du four | Des dimensions appropriées évitent la surchauffe et les dommages aux bobines, réduisant ainsi le gaspillage de matériaux. |
Surchauffe | La surchauffe accélère l'oxydation et l'évaporation, augmentant ainsi les pertes par fusion. |
Optimisez les opérations de votre four à induction et réduisez les pertes de fusion— contactez nos experts dès aujourd'hui pour des solutions sur mesure !