Un four rotatif est un récipient cylindrique légèrement incliné qui tourne lentement autour de son axe longitudinal.Il traite les matériaux en les faisant tourner dans un tambour chauffé, assurant une exposition uniforme à la chaleur et facilitant les réactions chimiques ou les changements physiques.Le four fonctionne grâce à une combinaison de flux de gaz, de combustion de combustible, de transfert de chaleur et de mouvement des matériaux.La matière est introduite dans la partie supérieure et se déplace vers le bas sous l'effet de la gravité et de la rotation, tandis que les gaz chauds s'écoulent vers la matière, soit en même temps, soit à contre-courant.La température et le temps de rétention du four sont soigneusement contrôlés sur la base d'analyses chimiques et thermiques afin d'obtenir la réaction ou la transformation souhaitée.Le tambour rotatif est scellé aux deux extrémités pour maintenir l'atmosphère et la température internes, garantissant ainsi un traitement efficace et contrôlé.
Explication des points clés :
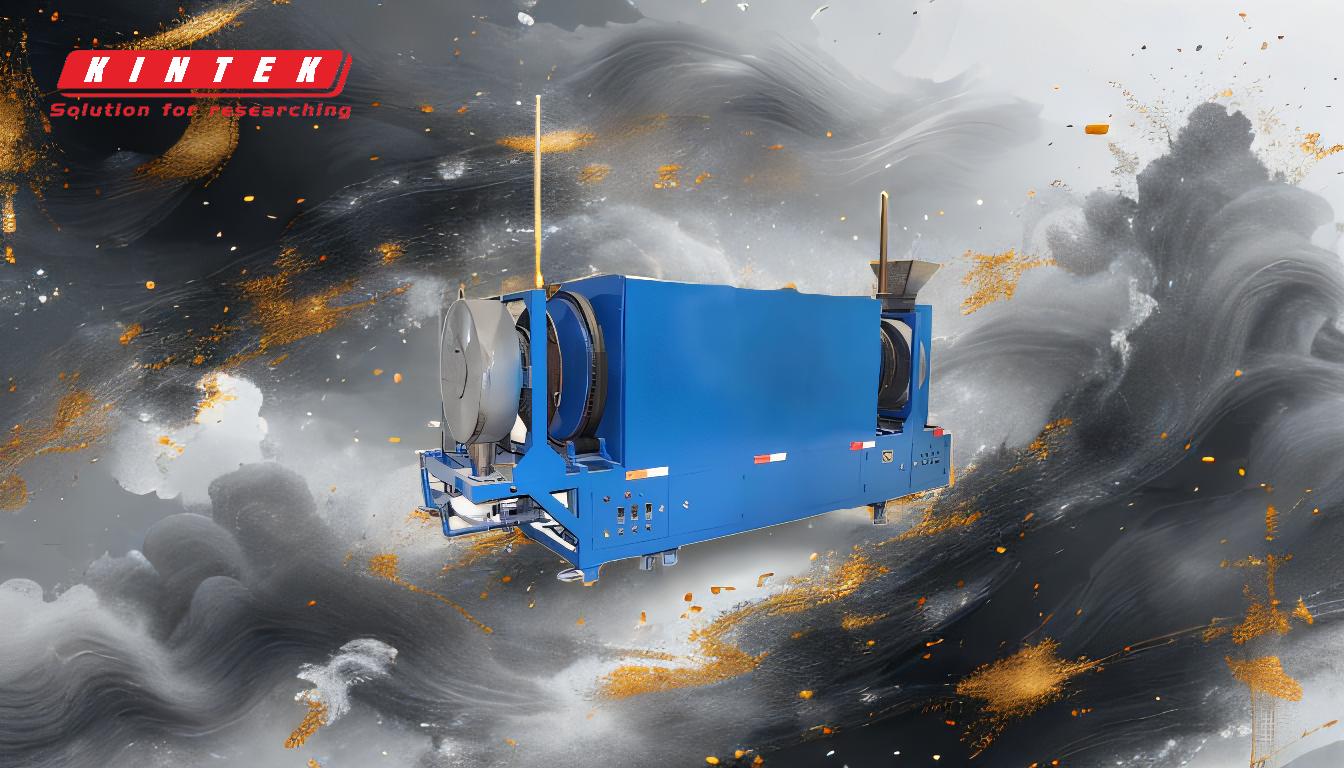
-
Conception cylindrique et rotation:
- Le four rotatif est un grand tambour cylindrique creux légèrement incliné par rapport à l'horizontale.
- Il tourne lentement autour de son axe longitudinal, ce qui permet de faire culbuter les matériaux à l'intérieur, d'assurer une exposition uniforme à la chaleur et de faciliter le mélange.
-
Mouvement des matériaux:
- Le matériau est introduit dans la partie supérieure du four.
- En raison de la rotation et de la légère inclinaison, la gravité aide à déplacer le matériau vers le bas du four en direction de l'extrémité inférieure.
-
Mécanisme de chauffage:
- Le four est chauffé soit à l'intérieur (chauffage direct), soit à l'extérieur (chauffage indirect) pour atteindre la température souhaitée.
- Les gaz chauds circulent le long du four, soit dans le même sens que le flux de matière (co-courant), soit dans le sens opposé (contre-courant).
-
Température et temps de rétention:
- La température et la durée pendant laquelle le matériau est maintenu à cette température (temps de rétention) sont prédéterminées sur la base d'analyses chimiques et thermiques.
- Cela permet de s'assurer que la matière subit les modifications physiques et chimiques nécessaires pour former le produit souhaité.
-
Flux de gaz et combustion:
- Le four veille à ce que le combustible brûle complètement, générant la chaleur nécessaire.
- La chaleur de la combustion est effectivement transférée au matériau, ce qui facilite les réactions prévues.
-
Scellage et contrôle de l'atmosphère:
- Le tambour rotatif est scellé à des culasses fixes à chaque extrémité pour contrôler l'atmosphère et la température à l'intérieur du four.
- Ce scellement est essentiel pour maintenir les conditions internes nécessaires au bon déroulement de la réaction.
-
Changements physiques et chimiques:
- Lors de son passage dans le four, le matériau subit une série de modifications physiques et chimiques.
- Ces changements sont induits par les températures élevées et l'environnement contrôlé à l'intérieur du four.
-
Ajustements de la configuration interne:
- La configuration interne du four peut être ajustée pour augmenter le culbutage ou exposer les matériaux à plus de chaleur avant leur sortie.
- Cette flexibilité permet d'optimiser le processus en fonction des exigences spécifiques du matériau traité.
En comprenant ces points clés, on peut apprécier le fonctionnement complexe mais efficace d'un four rotatif, qui est essentiel pour divers processus industriels nécessitant un traitement thermique précis des matériaux.
Tableau récapitulatif :
Aspect clé | Description de l'aspect |
---|---|
Conception cylindrique | Un tambour rotatif légèrement incliné pour une exposition uniforme à la chaleur et un mélange des matériaux. |
Mouvement des matériaux | La gravité et la rotation déplacent les matériaux vers le bas pour un traitement contrôlé. |
Mécanisme de chauffage | Chauffage direct ou indirect avec flux de gaz co-courant ou contre-courant. |
Contrôle de la température | Contrôle précis de la température et du temps de rétention pour les réactions souhaitées. |
Flux de gaz et combustion | Combustion efficace des combustibles et transfert de chaleur pour la transformation des matériaux. |
Étanchéité et atmosphère | Les extrémités scellées maintiennent les conditions internes pour des réactions efficaces. |
Changements physiques/chimiques | Les matériaux subissent des transformations sous l'effet des températures élevées et de la chaleur contrôlée. |
Réglages internes | Configurable pour optimiser le culbutage et l'exposition à la chaleur pour des matériaux spécifiques. |
Vous souhaitez optimiser vos processus industriels à l'aide d'un four rotatif ? Contactez nos experts dès aujourd'hui pour des solutions sur mesure !