Le revêtement par faisceau d'électrons est un procédé très précis et directionnel utilisé pour déposer de fines couches de matériaux, tels que des métaux ou du carbone, sur un substrat. Ce procédé consiste à évaporer le matériau source à l'aide d'un faisceau d'électrons focalisé dans une chambre à vide. Les particules évaporées s'écoulent ensuite vers le haut et se lient au substrat, formant un revêtement mince et de haute pureté dont l'épaisseur varie généralement entre 5 et 250 nanomètres. Le revêtement par faisceau d'électrons est particulièrement utile pour les applications nécessitant des couches ultraminces, un revêtement directionnel ou un impact minimal de la chaleur et des particules chargées sur le substrat. Ce procédé est largement utilisé dans les industries où la précision et la pureté sont essentielles, telles que l'optique, l'électronique et les répliques.
Explication des points clés :
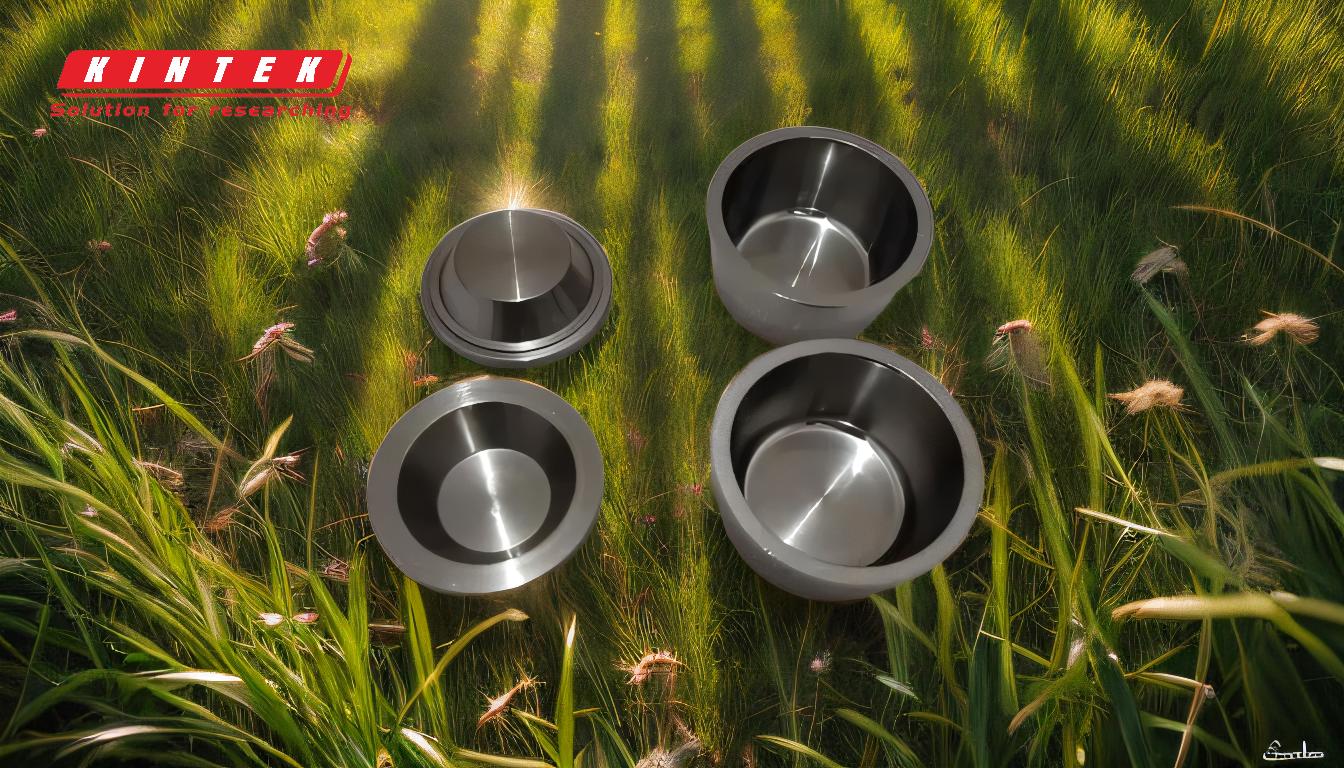
-
Aperçu du revêtement des poutres en E:
- Le revêtement par faisceau d'électrons est un procédé de dépôt sous vide qui utilise un faisceau d'électrons pour évaporer des matériaux sources tels que les métaux ou le carbone.
- Le processus est hautement directionnel, ce qui permet un contrôle précis de l'épaisseur et de l'emplacement du revêtement.
- Il est idéal pour les applications nécessitant des couches ultra-minces (5-250 nm) ou un revêtement directionnel, telles que l'ombrage et les répliques.
-
Composants du système de revêtement E-Beam:
- Pistolet à faisceau d'électrons: Génère et accélère des électrons à l'aide d'une haute tension et les concentre dans un faisceau.
- Creuset: Contient la matière première (métal ou carbone, par exemple) qui doit être évaporée.
- Chambre à vide: Il s'agit d'un environnement contrôlé qui permet de minimiser la contamination et de garantir des revêtements de haute pureté.
- Substrat: Le matériau à revêtir, placé au-dessus du creuset pour recevoir les particules évaporées.
-
Processus étape par étape de l'enrobage des poutres en E:
- Préparation: Le substrat et le matériau source sont préparés et placés dans la chambre à vide. Le substrat est nettoyé pour assurer une bonne adhérence du revêtement.
- Évaporation: Le canon à électrons génère un faisceau concentré d'électrons qui est dirigé vers le matériau de base dans le creuset. La chaleur intense du faisceau d'électrons fait fondre et évapore le matériau de base.
- Dépôt: Les particules évaporées s'écoulent vers le haut dans la chambre à vide et se lient au substrat, formant un revêtement mince et de haute pureté.
- Achèvement: Le substrat revêtu est retiré de la chambre et le revêtement est inspecté pour en vérifier la qualité et l'uniformité.
-
Avantages du revêtement des poutres en acier:
- Haute précision: La nature directionnelle du faisceau d'électrons permet un contrôle précis de l'épaisseur et de l'emplacement du revêtement.
- Haute pureté: L'environnement sous vide minimise la contamination, ce qui permet d'obtenir des revêtements d'une grande pureté.
- Impact thermique minimal: Le processus génère une chaleur minimale, ce qui réduit le risque de dommages thermiques au substrat.
- Polyvalence: Le revêtement par faisceau d'électrons peut être utilisé avec une large gamme de matériaux, y compris les métaux et le carbone.
-
Applications du revêtement des poutres en E:
- Optique: Utilisé pour créer des revêtements antireflets, des miroirs et d'autres composants optiques.
- Électronique: Appliqué à la production de semi-conducteurs, de transistors à couche mince et d'autres dispositifs électroniques.
- Répliques et ombres: Idéal pour les applications nécessitant un revêtement directionnel précis, telles que les répliques et les ombres en microscopie.
- Revêtements protecteurs: Utilisé pour appliquer des revêtements minces et durables qui protègent les substrats de l'usure, de la corrosion ou d'autres facteurs environnementaux.
-
Comparaison avec d'autres procédés de revêtement:
- Dépôt physique/chimique en phase vapeur (PVD/CVD): Le revêtement par faisceau d'électrons est un sous-ensemble du dépôt en phase vapeur (PVD), qui offre une plus grande précision et un meilleur contrôle directionnel que les autres méthodes de dépôt en phase vapeur (PVD) telles que la pulvérisation cathodique.
- Pulvérisation thermique: Le revêtement par faisceau d'électrons produit des couches plus fines et plus uniformes que la pulvérisation thermique, qui convient mieux aux revêtements plus épais.
- Dépôt électrolytique: Le revêtement par faisceau d'électrons ne nécessite pas de milieu liquide, ce qui le rend plus adapté aux applications où la contamination doit être minimisée.
-
Défis et limites:
- Surface enduite limitée: La nature directionnelle du procédé limite la taille de la zone qui peut être revêtue en un seul passage.
- Coût: L'équipement et l'environnement sous vide requis pour le revêtement par faisceau d'électrons peuvent être coûteux.
- Limites matérielles: Bien que polyvalent, le procédé ne convient pas à tous les matériaux, en particulier ceux dont le point de fusion est élevé ou dont la pression de vapeur est faible.
En comprenant le processus, les composants, les avantages et les applications du revêtement par faisceau d'électrons, les acheteurs peuvent décider en connaissance de cause si cette technologie est adaptée à leurs besoins spécifiques. Sa précision, sa pureté et sa polyvalence en font un outil précieux dans les industries où les revêtements de haute qualité sont essentiels.
Tableau récapitulatif :
Aspect | Détails |
---|---|
Processus | Utilise un faisceau d'électrons pour évaporer des matériaux dans une chambre à vide. |
Épaisseur du revêtement | 5-250 nanomètres, idéal pour les couches ultra-minces. |
Composants clés | Pistolet à faisceau d'électrons, creuset, chambre à vide, substrat. |
Avantages | Haute précision, grande pureté, impact thermique minimal, utilisation polyvalente des matériaux. |
Applications | Optique, électronique, répliques, revêtements protecteurs. |
Défis | Surface enduite limitée, coût élevé, limitation des matériaux. |
Le revêtement par faisceau d'électrons vous intéresse ? Contactez nos experts dès aujourd'hui pour en savoir plus !