Le revêtement par dépôt physique en phase vapeur (PVD) est une technique sophistiquée de dépôt de couches minces utilisée pour appliquer une fine couche de matériau sur un substrat dans un environnement sous vide.Ce processus implique la vaporisation d'un matériau solide, qui se condense ensuite sur la surface cible, formant un revêtement hautement durable et fonctionnel.Les revêtements PVD sont connus pour leurs excellentes propriétés mécaniques, chimiques et optiques, ce qui les rend idéaux pour les applications nécessitant une grande durabilité, une résistance à la corrosion et un attrait esthétique.Le processus est réalisé à des températures relativement basses, ce qui minimise les déformations et permet de l'appliquer sur une large gamme de matériaux, notamment les métaux, les céramiques et les plastiques.
Explication des principaux points :
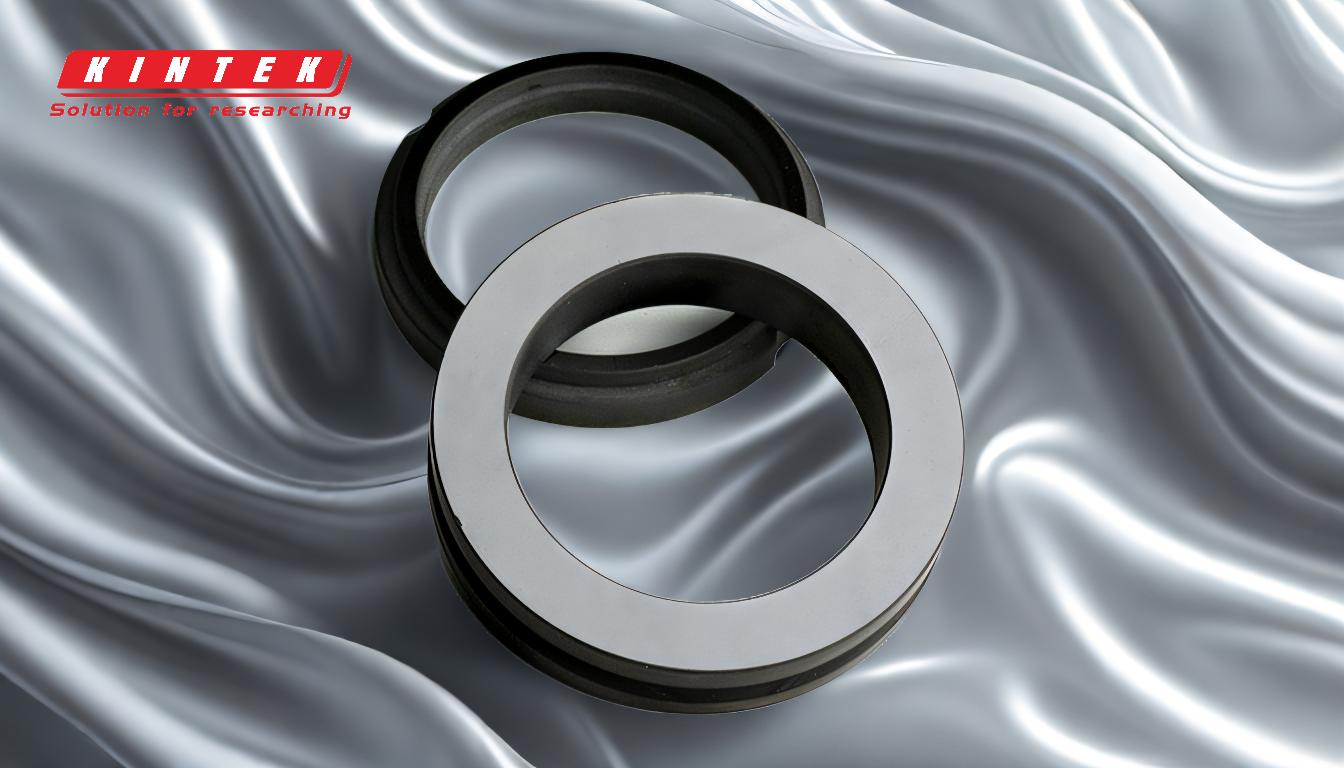
-
Définition et processus de base:
- PVD signifie Physical Vapor Deposition (dépôt physique en phase vapeur), une technique dans laquelle un matériau solide est vaporisé sous vide puis déposé sur un substrat.
- Le processus comporte trois étapes essentielles :L'évaporation, le transport et la condensation.
- Le matériau vaporisé forme un film mince sur le substrat, qui peut être un matériau pur ou une composition d'alliage.
-
Environnement sous vide:
- L'ensemble du processus se déroule dans une chambre à vide, généralement à des pressions comprises entre 10^-3 et 10^-9 Torr.
- L'environnement sous vide garantit que le matériau vaporisé reste propre et non contaminé, ce qui permet d'obtenir des revêtements de haute qualité.
-
Techniques de vaporisation:
-
Différentes méthodes sont utilisées pour vaporiser la matière solide, notamment :
- Creuset chauffé:Le matériau est chauffé jusqu'à ce qu'il se vaporise.
- Faisceau d'électrons:Un faisceau d'électrons focalisé est utilisé pour vaporiser le matériau.
- Bombardement ionique:Des ions à haute énergie sont utilisés pour pulvériser le matériau.
- Arc cathodique:Un arc électrique est utilisé pour vaporiser le matériau à partir d'une cathode.
-
Différentes méthodes sont utilisées pour vaporiser la matière solide, notamment :
-
Gaz réactifs:
- Des gaz réactifs, tels que l'azote, peuvent être introduits dans la chambre à vide pour modifier la composition du matériau vaporisé.
- Par exemple, l'ajout d'azote peut entraîner la formation d'un nitrure métallique, qui améliore les propriétés du revêtement.
-
Processus de dépôt:
- Les atomes vaporisés traversent le vide et s'incrustent dans la surface du substrat.
- Le procédé est une technique de "ligne de mire", ce qui signifie que l'objet doit être correctement positionné ou tourné pour garantir un revêtement complet et uniforme.
-
Caractéristiques du revêtement:
- Les revêtements PVD sont généralement très fins, avec des épaisseurs allant de 0,02 à 5 microns.
- Les revêtements sont très durables, résistants à la corrosion et peuvent supporter des températures élevées.
- Ils améliorent l'aspect, la durabilité et la fonctionnalité des pièces revêtues.
-
Avantages du revêtement PVD:
- Températures de traitement plus basses:Le dépôt en phase vapeur (PVD) est effectué à des températures comprises entre 50 et 600°C, ce qui minimise les distorsions dans la plupart des matériaux.
- Dépôt précis:Le procédé permet un contrôle précis de l'épaisseur et de la composition du revêtement.
- Respect de l'environnement:Le dépôt en phase vapeur est considéré comme plus écologique que d'autres techniques de revêtement telles que le dépôt chimique en phase vapeur (CVD).
-
Applications:
-
Les revêtements PVD sont largement utilisés dans diverses industries, notamment :
- les outils de coupe:Les outils de coupe en acier rapide (HSS) et en carbure bénéficient d'une durabilité et d'une résistance à l'usure accrues.
- Moulage par injection de plastique:Les composants présentant des tolérances serrées sont revêtus afin d'améliorer les performances et la longévité.
- Outils de découpage fin:Les revêtements PVD améliorent la résistance à l'usure et la durée de vie de ces outils.
- Revêtements optiques:La technique est utilisée pour appliquer des revêtements qui améliorent les propriétés optiques des lentilles et d'autres composants.
-
Les revêtements PVD sont largement utilisés dans diverses industries, notamment :
-
Options de matériaux:
- Les matériaux couramment utilisés dans les revêtements PVD sont le titane, le zirconium et le chrome.
- Ces matériaux peuvent être combinés à des gaz réactifs pour former des composés tels que le nitrure de titane (TiN), connu pour sa dureté et sa résistance à l'usure.
-
Considérations relatives à l'environnement et à la sécurité:
- Le revêtement PVD est considéré comme un procédé moderne et respectueux de l'environnement.
- L'utilisation de la technologie du vide et l'absence de produits chimiques nocifs en font une alternative plus sûre aux autres méthodes de revêtement.
En résumé, le revêtement PVD est une technique polyvalente et avancée qui offre de nombreux avantages, notamment une grande durabilité, une grande précision et un respect de l'environnement.Ses applications s'étendent à diverses industries, ce qui en fait un procédé précieux pour améliorer les performances et la longévité d'un large éventail de composants.
Tableau récapitulatif :
Aspect | Détails |
---|---|
Définition | Technique de dépôt de couches minces dans un environnement sous vide. |
Étapes du processus | Évaporation, transport, condensation. |
Méthodes de vaporisation | Creuset chauffé, faisceau d'électrons, bombardement ionique, arc cathodique. |
Épaisseur du revêtement | 0,02 à 5 microns. |
Avantages | Grande durabilité, résistance à la corrosion, basses températures de traitement, respect de l'environnement. |
Applications | Outils de coupe, moulage par injection de plastique, outils de découpage fin, optique. |
Matériaux utilisés | Titane, zirconium, chrome et composés comme le TiN. |
Vous souhaitez améliorer vos composants à l'aide d'un revêtement PVD ? Contactez nous dès aujourd'hui pour en savoir plus !