Les fours rotatifs sont des équipements de traitement à haute température utilisés dans des industries telles que la production de ciment, la réduction du minerai de fer et le traitement chimique.Leur revêtement réfractaire est un élément essentiel, car il protège l'enveloppe du four de la chaleur extrême et des réactions chimiques, tout en assurant un transfert de chaleur efficace vers le matériau traité.Le choix du matériau réfractaire dépend du processus spécifique, de la température et de l'environnement chimique à l'intérieur du four.Les matériaux réfractaires courants comprennent l'alumine à faible teneur en fer, les briques de magnésium et d'étain et les briques de magnésite, le choix étant influencé par des facteurs tels que la résistance à l'usure, la conductivité thermique et la stabilité chimique.Les réfractaires sont soit coulés (en place), soit en briques (posées manuellement), chacun offrant des avantages distincts en termes de facilité d'installation et de durabilité.
Explication des principaux points :
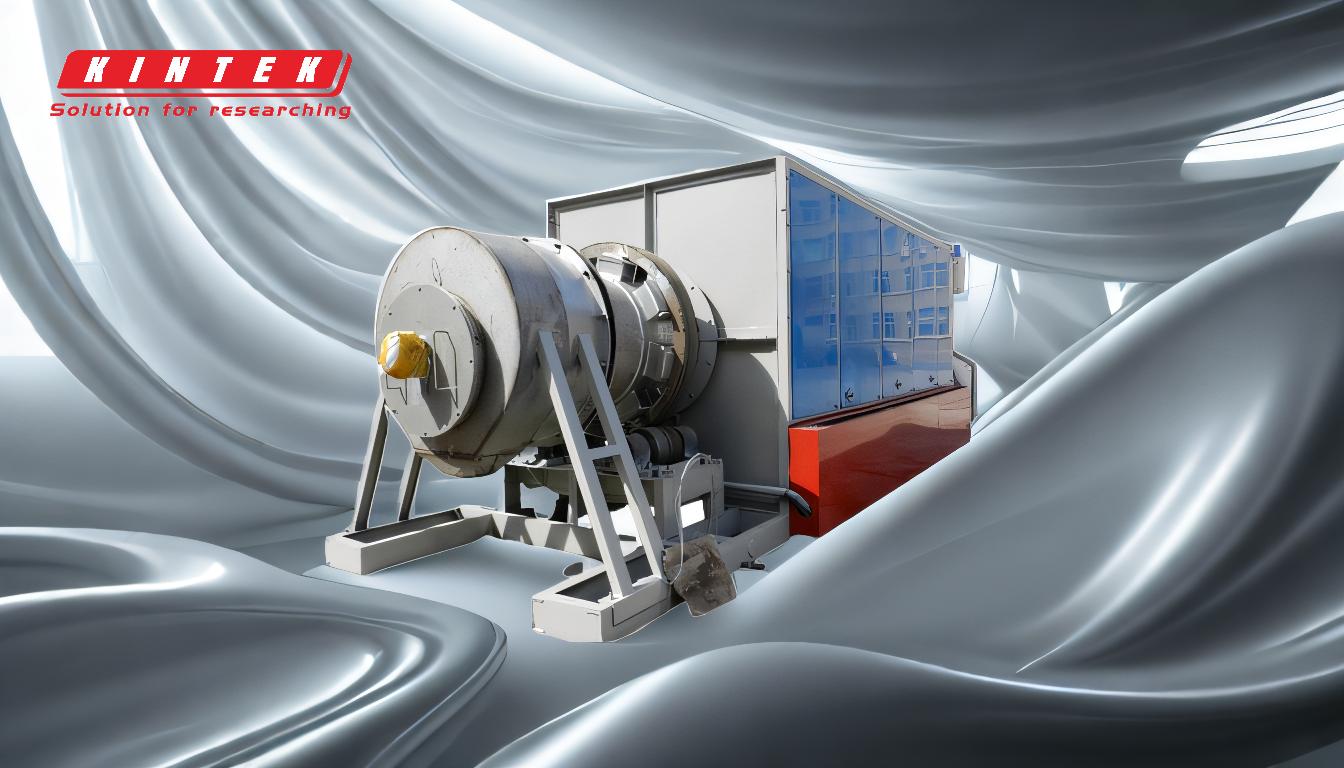
-
Objectif du revêtement réfractaire dans les fours rotatifs:
- Le revêtement réfractaire sert de barrière protectrice entre l'enveloppe du four et l'environnement à haute température à l'intérieur du four.
- Il empêche les pertes de chaleur, protège l'enveloppe des dommages thermiques et chimiques et assure un transfert de chaleur efficace vers le matériau traité.
- Le revêtement doit résister à des températures extrêmes, à des contraintes mécaniques et à des réactions chimiques pendant le fonctionnement.
-
Facteurs influençant la sélection des matériaux réfractaires:
-
Exigences du processus:Le type de matériau traité (ciment, minerai de fer ou produits chimiques) détermine le choix du réfractaire.Par exemple :
- Les briques d'alumine à faible teneur en fer ou de magnésium-spinel sont utilisées dans les fours de réduction du minerai de fer en raison de leur résistance aux atmosphères réductrices.
- Les briques de magnésite sont préférées dans les fours à ciment pour leur grande stabilité thermique et leur résistance aux environnements alcalins.
- La température:Les réfractaires doivent résister à la température de fonctionnement du four, qui peut dépasser 1 400°C dans les fours à ciment.
- Environnement chimique:Le réfractaire doit résister aux réactions chimiques avec le matériau traité, les gaz et le laitier.
- Contraintes mécaniques:Le revêtement doit résister à l'abrasion, aux chocs et aux cycles thermiques.
-
Exigences du processus:Le type de matériau traité (ciment, minerai de fer ou produits chimiques) détermine le choix du réfractaire.Par exemple :
-
Types de matériaux réfractaires:
-
Briques réfractaires:
- Fabriqués à partir de briques préformées, généralement composées de matériaux tels que la magnésite, l'alumine ou le spinelle.
- Très résistantes à l'usure, elles conviennent aux matériaux abrasifs.
- Leur installation nécessite beaucoup de main-d'œuvre, mais ils offrent une durée de vie plus longue dans des conditions difficiles.
-
Réfractaires coulables:
- Composé d'agrégats et de liants réfractaires, coulé en place pour former un revêtement monolithique.
- Plus facile et plus rapide à installer que les briques.
- Moins résistants à l'usure, mais adaptés aux environnements moins abrasifs ou aux zones à géométrie complexe.
-
Briques réfractaires:
-
Matériaux réfractaires couramment utilisés dans les fours rotatifs:
- Alumine à faible teneur en fer:Utilisée dans les fours de réduction du minerai de fer en raison de sa résistance aux atmosphères réductrices et de sa grande stabilité thermique.
- Briques de magnésium-épingle:Elles offrent une excellente résistance aux chocs thermiques et sont utilisées dans des applications à haute température.
- Briques de magnésite:Préférés dans les fours à ciment pour leur résistance aux environnements alcalins et leur conductivité thermique élevée.
-
Méthodes d'installation:
-
Revêtement de briques:
- Les briques sont posées manuellement, souvent avec du mortier ou des adhésifs spécialisés.
- Elles constituent un revêtement durable et résistant à l'usure, mais nécessitent une main-d'œuvre qualifiée et un temps d'installation plus long.
-
Revêtement coulable:
- Coulée en place et durcie pour former une structure monolithique.
- Installation plus rapide et meilleure adaptabilité aux formes complexes, mais peut nécessiter un temps de durcissement supplémentaire.
-
Revêtement de briques:
-
Considérations sur les performances:
- Conductivité thermique:Les réfractaires doivent équilibrer la rétention et le transfert de chaleur pour garantir un traitement efficace.
- Résistance à l'usure:Le revêtement doit résister à l'abrasion du matériau traité.
- Stabilité chimique:La résistance aux réactions avec les matériaux traités, les gaz et les scories est essentielle.
- Résistance aux chocs thermiques:Capacité à résister à des changements rapides de température sans se fissurer.
-
Entretien et durée de vie:
- Une inspection et un entretien réguliers sont nécessaires pour surveiller l'usure du réfractaire et prévenir les défaillances.
- La durée de vie du revêtement réfractaire dépend du matériau, des conditions d'exploitation et des pratiques d'entretien.
- Les sections réfractaires endommagées ou usées peuvent être remplacées individuellement, ce qui minimise les temps d'arrêt.
En résumé, le matériau réfractaire d'un four rotatif est un élément essentiel qui garantit un fonctionnement efficace et sûr.Le choix du matériau dépend du processus, de la température et de l'environnement chimique spécifiques. Des options telles que l'alumine à faible teneur en fer, l'étain de magnésium et les briques de magnésite sont couramment utilisées.Les réfractaires en briques et les réfractaires coulés ont tous deux leurs avantages, les briques offrant une meilleure résistance à l'usure et les produits coulés facilitant l'installation.La sélection, l'installation et l'entretien corrects du revêtement réfractaire sont essentiels pour maximiser les performances et la durée de vie du four.
Tableau récapitulatif :
Aspect clé | Détails |
---|---|
Objectif | Protège l'enveloppe du four, assure le transfert de chaleur et résiste aux conditions extrêmes. |
Facteurs de sélection des matériaux | Type de processus, température, environnement chimique et contraintes mécaniques. |
Matériaux courants | Alumine à faible teneur en fer, briques de magnésium-spinel, briques de magnésite. |
Méthodes d'installation | Brique (manuelle, durable) ou matériau coulable (coulé, installation plus rapide). |
Considérations relatives aux performances | Conductivité thermique, résistance à l'usure, stabilité chimique, choc thermique. |
Entretien | Inspections et remplacements réguliers pour maximiser la durée de vie. |
Optimisez les performances de votre four rotatif avec le revêtement réfractaire adéquat. contactez nos experts dès aujourd'hui !