Les fours de fusion à induction sont des outils très polyvalents et efficaces utilisés dans les processus de fusion des métaux, capables d'atteindre des températures extrêmement élevées. La plage de température de ces fours est un facteur critique pour les utilisateurs, car elle détermine les types de matériaux qui peuvent être fondus et l'efficacité du processus. D'après les références fournies, les fours de fusion par induction peuvent atteindre des températures allant jusqu'à 2000℃, ce qui les rend adaptés à la fusion d'une large gamme de métaux, y compris ceux ayant un point de fusion élevé comme l'acier et le fer. En outre, la température de vidange du four est généralement contrôlée entre 37°C et 65°C, avec des mécanismes de sécurité en place pour éviter la surchauffe. Cela garantit à la fois la sécurité opérationnelle et la cohérence du processus de fusion.
Explication des points clés :
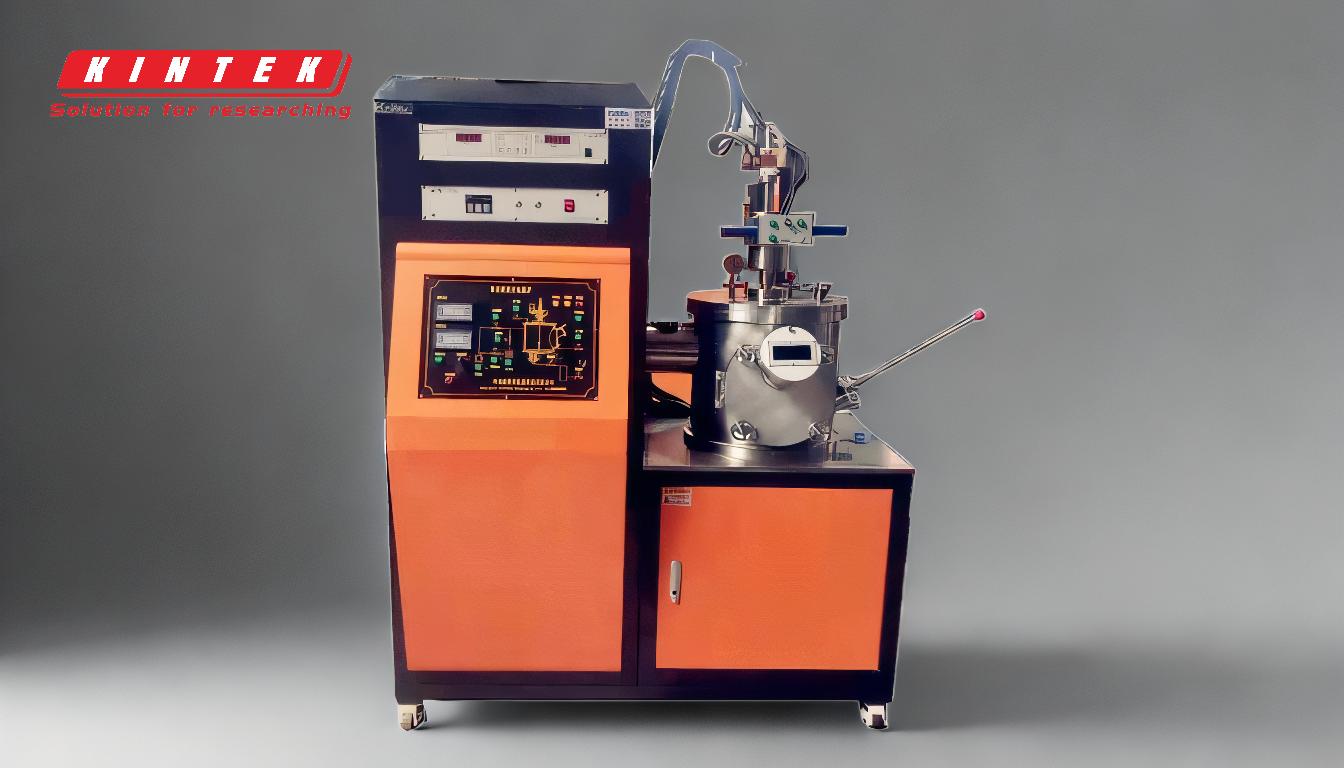
-
Capacité de température maximale:
- Les fours de fusion à induction peuvent atteindre des températures aussi élevées que 2000℃ comme indiqué dans les références. Ils conviennent donc à la fusion de métaux à haute température tels que l'acier, le fer et d'autres alliages. La température élevée est obtenue grâce à un couplage inductif efficace entre la bobine et les matériaux de charge, ce qui garantit un chauffage rapide et uniforme.
-
Contrôle de la température des drains:
- La température de vidange du four est généralement maintenue entre 100°F (37°C) et 150°F (65°C) . Cette plage garantit que le métal en fusion est à une température optimale pour la coulée ou le traitement ultérieur. Un commutateur de température de vidange de four fixe est souvent réglé à 175°F (79°C) qui agit comme un mécanisme de sécurité. Si la température dépasse ce seuil, l'alimentation électrique est automatiquement coupée, ce qui évite une surchauffe et des dommages potentiels au four. L'interrupteur se réenclenche lorsque la température redescend en dessous de 165°F (73°C) .
-
Cohérence et uniformité de la température:
- L'un des principaux avantages des fours de fusion à induction est leur capacité à maintenir un niveau de qualité élevé distribution uniforme de la température dans tout le métal en fusion. Ce résultat est obtenu grâce au champ magnétique à moyenne fréquence, qui assure un brassage magnétique. Ce brassage permet non seulement d'obtenir une température uniforme, mais aussi d'améliorer la qualité du produit composition chimique consistance du métal et facilite l'élimination des impuretés ou de l'écume.
-
Flexibilité et sécurité opérationnelles:
- Les fours de fusion par induction sont conçus avec des caractéristiques avancées telles que Conversion de la fréquence de l'IGBT et régulation de la puissance qui permettent un fonctionnement souple et sans à-coups. Ces fours peuvent fonctionner en continu pendant 24 heures ce qui les rend idéales pour les applications industrielles. En outre, ils sont équipés de des fonctions de protection complètes le système est doté d'une protection contre les surintensités, le manque d'eau, la surchauffe, la surtension, les courts-circuits et la perte de phase. Ces caractéristiques garantissent une fiabilité, une durabilité et une sécurité accrues pendant le fonctionnement.
-
Efficacité énergétique et avantages pour l'environnement:
- Les fours de fusion à induction sont efficacité énergétique et respectueux de l'environnement. Ils offrent des opérations plus propres avec moins de production de déchets , un meilleur contrôle des émissions et des niveaux de bruit réduits . La transmission efficace de la chaleur et la répartition uniforme de la température contribuent à réduction des pertes par oxydation et réduction des coûts opérationnels .
-
Conception et portabilité:
- Les fours modernes de fusion par induction sont conçus pour être compact , léger et portable . Ils occupent moins de un mètre carré d'espace, ce qui les rend adaptés aux petits ateliers ou aux installations disposant d'un espace limité. Les corps des fours sont facilement remplaçables, ce qui permet de traiter avec souplesse différents matériaux, poids et méthodes de démarrage.
-
Durée et efficacité de la fusion:
- Le temps de fusion par four est généralement de 20-30 minutes ce qui est relativement rapide par rapport aux méthodes de fusion traditionnelles. Cette efficacité, associée à la capacité de fonctionner en continu, fait des fours à induction des outils très productifs pour les applications industrielles.
En résumé, la plage de température d'un four de fusion à induction est un facteur critique qui détermine son adéquation à diverses applications de fusion des métaux. Avec une capacité de température maximale de 2000℃ et un contrôle précis des températures de vidange, ces fours offrent une combinaison de performances, de sécurité et d'efficacité élevées. Leurs caractéristiques avancées, telles que la conversion de fréquence IGBT, l'agitation magnétique et les mécanismes de protection complets, en font un choix fiable pour les industries exigeant des processus de fusion des métaux cohérents et de haute qualité.
Tableau récapitulatif :
Fonctionnalité | Détails |
---|---|
Température maximale | Jusqu'à 2000℃ il convient pour la fusion de l'acier, du fer et des alliages à haute température. |
Plage de température de vidange | 100°F (37°C) à 150°F (65°C) avec coupure de sécurité à 175°F (79°C) . |
Chauffage uniforme | L'agitation magnétique permet une répartition homogène de la température. |
Sécurité opérationnelle | Comprend des mécanismes de protection contre les surintensités, les surchauffes et les pertes de phase. |
Efficacité énergétique | Réduit les pertes par oxydation, les émissions et les coûts d'exploitation. |
Temps de fusion | 20-30 minutes par four, idéal pour une utilisation industrielle continue. |
Prêt à optimiser votre processus de fusion des métaux ? Contactez-nous dès aujourd'hui pour trouver le four à induction parfait pour vos besoins !