Présentation du pressage isostatique à froid
Table des matières
- Présentation du pressage isostatique à froid
- Pressage isostatique à froid dans la fabrication d'outils
- Application du CIP pour la production d'outils d'usure et de formage des métaux
- Utilisation de presses CIP à sacs secs et à sacs humides
- Processus de CIP impliquant un milieu liquide à base d’eau à température ambiante
- Utilisation de sacs façonnés avec noyaux et poudres sans ou avec faible teneur en cire
- Tolérances dimensionnelles des pièces produites par CIP
- Pressage isostatique à froid dans la production de poudres de métaux rares
- Pressage et extrusion isostatique à froid
- Utilisation commerciale du CIP et de l'extrusion pour produire des tiges et des barres AlBeMet extrudées
- Processus d'encapsulation, de dégazage et de préchauffage de la billette
- Processus d'extrusion à l'aide d'une filière conique
- Processus de post-extrusion comprenant la gravure chimique et l'élimination de la peau de cuivre
- Processus de recuit des alliages extrudés aluminium-béryllium
Le pressage isostatique à froid (CIP) est une technique puissante utilisée dans le traitement des matériaux pour améliorer leurs propriétés. Il s'agit de soumettre un matériau à une pression uniforme de tous les côtés en le plongeant dans un milieu fluide à haute pression et en appliquant une pression hydraulique. Le CIP est particulièrement efficace pour façonner et consolider des matériaux en poudre, créer des formes complexes et atteindre une densité verte élevée.
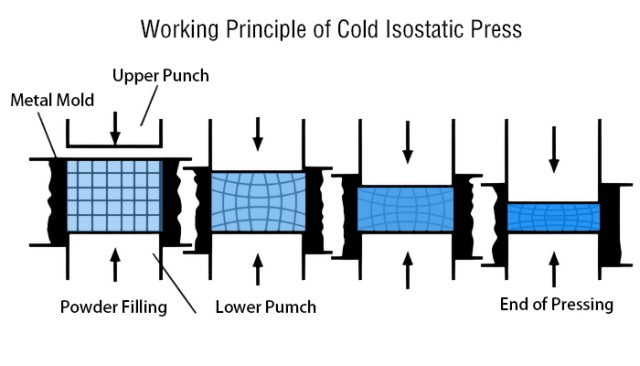
Définition et points communs du pressage isostatique à froid (CIP)
Le pressage isostatique à froid, également appelé compactage isostatique à froid, est un procédé de compactage de poudres confinées dans un moule en élastomère. Le moule est placé dans une chambre sous pression et un milieu liquide est pompé, soumettant le moule à une haute pression de tous les côtés. Le CIP est utilisé avec divers matériaux tels que la métallurgie des poudres, les carbures cémentés, les matériaux réfractaires, le graphite, la céramique, les plastiques, etc.
Utilisation des techniques de sacs humides et de sacs secs pour le CIP
Il existe deux techniques courantes utilisées dans le CIP : le sac humide et le sac sec. Dans le procédé Wetbag, le matériau en poudre est enfermé dans un sac moulé flexible, qui est immergé dans un liquide à haute pression dans un récipient sous pression. Une pression isostatique est ensuite appliquée pour comprimer la poudre dans la forme souhaitée. Ce procédé est idéal pour la production multiformes, la production de petites à grandes quantités et le pressage de produits de grande taille.
En revanche, le pressage en sac sec est utilisé pour des formes simples. Le moule rempli de poudre est scellé et la compression se produit entre le moule et le récipient sous pression. Cette technique convient pour produire des composants moins complexes.
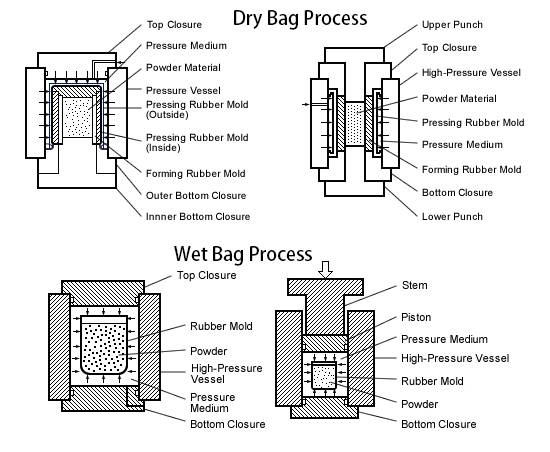
Production de composants complexes et de lingots de tungstène par CIP
Le CIP est largement utilisé dans la production de composants complexes et de lingots de tungstène. Avec la technique du wetbag, il est possible de presser des lingots de tungstène pesant jusqu'à 1 tonne. De plus, le CIP permet le compactage de composants plus complexes, grâce à sa capacité à créer des formes complexes et à atteindre une densité verte élevée.
En résumé, le pressage isostatique à froid (CIP) est une technique polyvalente pour façonner et consolider des matériaux en poudre. Il offre des avantages tels que la capacité de produire des composants complexes, de créer des formes complexes et d’atteindre une densité verte élevée. Le choix entre les techniques Wetbag et Drybag dépend des exigences spécifiques du projet.
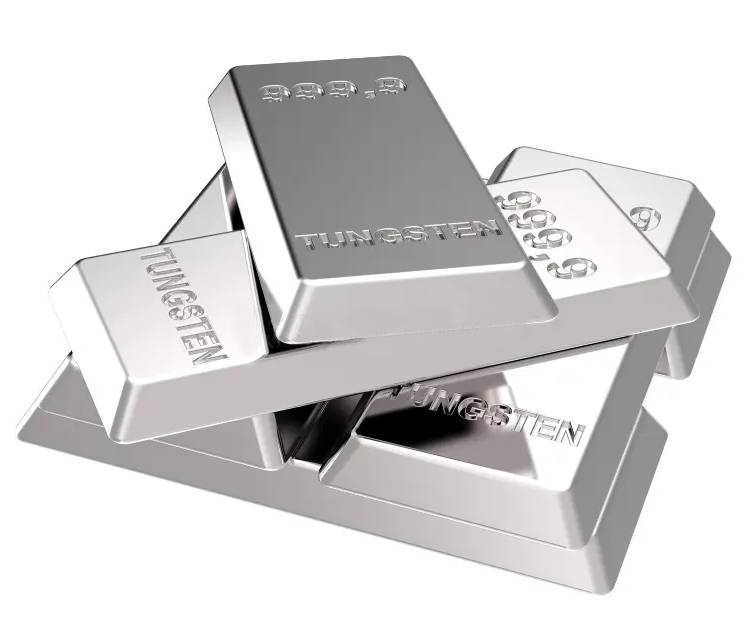
Pressage isostatique à froid dans la fabrication d'outils
Le pressage isostatique à froid (CIP) est une méthode utilisée dans la fabrication d'outils pour compacter des matériaux en poudre en une masse solide et homogène avant l'usinage ou le frittage. Il est couramment utilisé pour produire des outils d’usure et de formage des métaux. Le CIP consiste à soumettre la poudre à une pression égale dans toutes les directions, ce qui permet d'obtenir des billettes ou des préformes de haute intégrité présentant peu de distorsion ou de fissures lors de la cuisson.
Application du CIP pour la production d'outils d'usure et de formage des métaux
Le CIP est largement utilisé dans la production d’outils d’usure et de formage des métaux. Il est particulièrement adapté aux pièces trop grandes pour être pressées dans des presses uniaxiales et ne nécessitant pas une grande précision à l'état fritté. Le CIP peut produire des billettes ou des préformes de haute intégrité avec un minimum de distorsion ou de fissuration.
Utilisation de presses CIP à sacs secs et à sacs humides
Il existe deux types de procédés CIP : le sac sec et le sac humide. Dans le processus de sac sec, la poudre est placée dans un sac moulable imperméable à l’intérieur d’une chambre sous pression. Le sac est ensuite soumis à une pression isostatique à l'aide d'un milieu liquide à base d'eau à température ambiante. Ce processus est automatisé et permet une production en grand volume de formes relativement simples.
D'autre part, le processus de sac humide consiste à immerger le matériau en poudre dans un sac moulé flexible dans un liquide à haute pression dans un récipient sous pression. Une pression isostatique est ensuite appliquée pour comprimer la poudre dans la forme souhaitée. Ce procédé est idéal pour la production de formes multiples et de petites à grandes quantités, y compris le pressage de produits de grande taille.
Processus de CIP impliquant un milieu liquide à base d’eau à température ambiante
Dans le CIP, le matériau en poudre est placé dans un sac moulable imperméable à l’intérieur d’une chambre sous pression. Le sac est rempli d'un milieu liquide à base d'eau et l'ensemble du moule est uniformément soumis à une haute pression de tous les côtés. La pression est appliquée à l'aide d'un milieu liquide à base d'eau à température ambiante. Ce processus permet le compactage du matériau en poudre en une masse solide et homogène.
Utilisation de sacs façonnés avec noyaux et poudres sans ou avec faible teneur en cire
Pour obtenir des formes proches du filet, des sacs façonnés avec noyau sont utilisés dans le processus CIP. Ces sacs façonnés aident à obtenir la forme souhaitée et les tolérances dimensionnelles du produit final. De plus, des poudres sans ou avec une faible teneur en cire sont utilisées dans le pressage isostatique à froid. Cela garantit que le matériau en poudre peut être facilement compacté en une masse solide sans avoir recours à une chaleur ou une pression excessive.
Tolérances dimensionnelles des pièces produites par CIP
Les tolérances dimensionnelles des pièces produites par CIP sont relativement grandes par rapport au pressage uniaxial. Cela signifie que le contrôle de la taille et de la forme n'est pas aussi critique dans le processus CIP. Cependant, les pièces produites par CIP nécessitent toujours un usinage à l'état vert, ou préfritté, suivi d'un frittage pour obtenir les dimensions et propriétés finales.
Dans l’ensemble, le pressage isostatique à froid est une méthode polyvalente utilisée dans la fabrication d’outils pour produire des outils d’usure et de formage des métaux. Il offre des avantages tels que des billettes ou des préformes de haute intégrité, une distorsion ou une fissuration minimale et la capacité de produire des formes proches du résultat final. Le CIP est un processus rentable et efficace qui peut être utilisé pour la production en grand volume de formes complexes dans diverses industries.
Pressage isostatique à froid dans la production de poudres de métaux rares
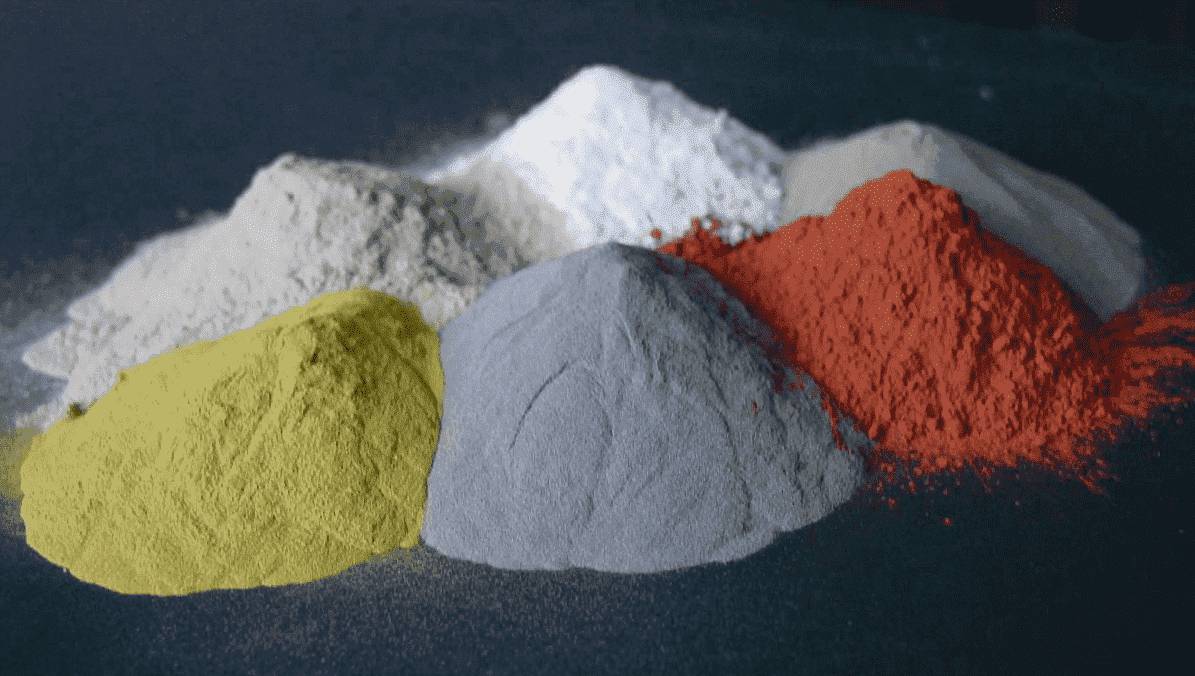
Le pressage isostatique à froid est une technique utilisée dans la production de poudres de métaux rares. Il s’agit d’appliquer une pression sur la poudre à température ambiante ou légèrement supérieure, généralement inférieure à 93°C. La pression appliquée varie de 100 à 600 MPa.
Le but du pressage isostatique à froid est d'obtenir une pièce « brute » présentant une résistance suffisante pour la manipulation, le traitement et l'éventuel frittage afin d'obtenir la résistance finale. Cette technique utilise un milieu liquide, tel que de l'eau, de l'huile ou un mélange de glycol.
Lorsqu'il s'agit de métaux, le pressage isostatique à froid peut atteindre une densité théorique d'environ 100 %. Pour les poudres céramiques, la densité atteinte est d'environ 95 %. Le pressage isostatique à froid est particulièrement utile pour former des matériaux en poudre à température ambiante en utilisant du caoutchouc ou du plastique comme matériau de moulage enveloppant et du liquide comme milieu de pression.
L’un des avantages du pressage isostatique à froid est qu’il élimine le besoin de matrices de pressage coûteuses, ce qui en fait une option rentable. Il est particulièrement avantageux lors de la production de compacts volumineux ou complexes pour lesquels le coût initial élevé des matrices de pressage ne peut être justifié.
Cette technique peut être utilisée à l’échelle commerciale pour différents types de poudres, notamment les métaux, les céramiques, les plastiques et les composites. Les pressions requises pour le compactage vont de moins de 5 000 psi à plus de 100 000 psi (34,5 à 690 MPa).
Les poudres sont compactées dans des moules en élastomère selon un procédé en sac humide ou sec. Le pressage isostatique à froid permet de produire des pièces de haute qualité pouvant subir des processus de frittage ou de pressage isostatique à chaud.
Pressage et extrusion isostatique à froid
Utilisation commerciale du CIP et de l'extrusion pour produire des tiges et des barres AlBeMet extrudées
Le pressage isostatique à froid (CIP) est largement utilisé dans les applications commerciales pour produire des tiges et des barres AlBeMet extrudées. Ce processus implique la densification préliminaire de composants de poudre métallique non frittés ou compactés par un colorant vert avant un traitement ultérieur tel que le laminage, l'usinage ou le frittage. Les systèmes CIP sont utilisés dans diverses industries, notamment l'aérospatiale, l'armée, l'industrie et le médical, pour créer des composants impeccables avec une résistance à l'état brut suffisante pour la manipulation et le frittage.
Processus d'encapsulation, de dégazage et de préchauffage de la billette
Le processus de pressage isostatique à froid commence par l'encapsulation de la poudre métallique dans un moule en élastomère composé de matériaux tels que l'uréthane, le caoutchouc ou le chlorure de polyvinyle. La poudre encapsulée est ensuite soumise à une pression de fluide, généralement utilisant de l'huile ou de l'eau, allant de 60 000 lb/po2 à 150 000 lb/po2. Cette pression contribue à compacter la poudre uniformément, ce qui donne un compact vert avec une faible précision géométrique mais une densité élevée. Le compact vert est ensuite préchauffé pour le préparer à un traitement ultérieur.
Processus d'extrusion à l'aide d'une filière conique
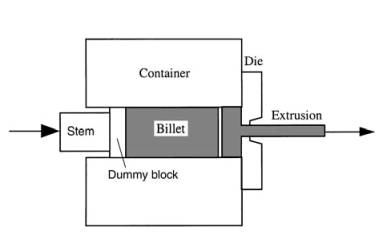
Une fois la billette préchauffée, elle subit le processus d’extrusion à l’aide d’une filière conique. La filière conique aide à façonner la tige ou la barre AlBeMet extrudée selon les dimensions souhaitées. Le processus d'extrusion consiste à appliquer une pression élevée pour forcer la billette à travers la filière conique, ce qui entraîne la formation d'un produit extrudé continu. Ce processus garantit l'uniformité et la consistance de la tige ou de la barre AlBeMet extrudée.
Processus de post-extrusion comprenant la gravure chimique et l'élimination de la peau de cuivre
Une fois le processus d'extrusion terminé, des processus de post-extrusion sont effectués pour affiner le produit extrudé. Ces processus comprennent la gravure chimique et l’élimination de la peau de cuivre. La gravure chimique aide à éliminer les impuretés ou défauts de surface, garantissant ainsi la qualité de la tige ou de la barre AlBeMet extrudée. L'élimination de la peau de cuivre est nécessaire car elle est généralement présente à la surface du produit extrudé en raison de l'utilisation d'alliages de cuivre dans le processus d'extrusion.
Processus de recuit des alliages extrudés aluminium-béryllium
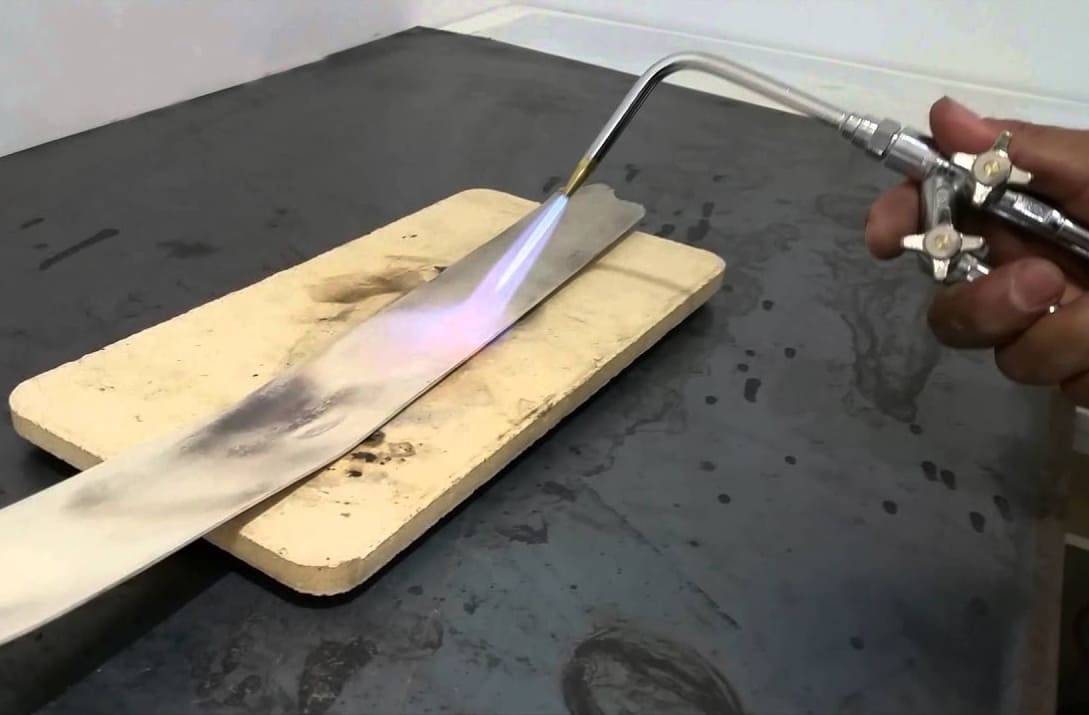
Après les processus de post-extrusion, les alliages aluminium-béryllium (AlBeMet) extrudés subissent un processus de recuit. Le recuit consiste à chauffer le produit extrudé à une température spécifique puis à le refroidir lentement pour soulager les contraintes internes et améliorer ses propriétés mécaniques. Ce processus contribue à améliorer la résistance, la ductilité et la stabilité de la tige ou de la barre AlBeMet extrudée.
Dans l’ensemble, le pressage isostatique à froid et l’extrusion jouent un rôle crucial dans la production commerciale de tiges et de barres AlBeMet extrudées. La combinaison de ces procédés garantit la production de composants de haute qualité avec des dimensions précises et d'excellentes propriétés mécaniques.
CONTACTEZ-NOUS POUR UNE CONSULTATION GRATUITE
Les produits et services de KINTEK LAB SOLUTION ont été reconnus par des clients du monde entier. Notre personnel se fera un plaisir de répondre à toute demande que vous pourriez avoir. Contactez-nous pour une consultation gratuite et parlez à un spécialiste produit pour trouver la solution la plus adaptée aux besoins de votre application !