Introduction aux atmosphères de four
Les atmosphères des fours jouent un rôle essentiel dans le processus de traitement thermique des matériaux. L'atmosphère à l'intérieur d'un four peut avoir un impact significatif sur les propriétés du produit final, telles que la résistance et la durabilité. Une atmosphère est un gaz ou un mélange de gaz entourant le matériau traité dans un four. Les atmosphères de four les plus couramment utilisées comprennent l'air, l'azote, l'hydrogène et l'argon. Comprendre les propriétés de chaque atmosphère et leurs effets sur le matériau est crucial pour produire des produits de haute qualité. L'utilisation d'atmosphères inertes, telles que l'azote et l'argon, est importante pour prévenir les réactions indésirables et l'oxydation pendant le processus de traitement thermique.
Table des matières
- Introduction aux atmosphères de four
- Qu'est-ce qu'une atmosphère inerte ?
- Pourquoi est-il important d'utiliser des atmosphères inertes ?
- Gaz courants dans les atmosphères de four
- Procédés de traitement thermique nécessitant des atmosphères inertes
- Comment mesurer l'atmosphère du four
- Outils de mesure et d'échantillonnage
- Conclusion sur l'importance des atmosphères inertes
Qu'est-ce qu'une atmosphère inerte ?
Dans le travail en laboratoire, il est essentiel de créer un environnement contrôlé pour certaines réactions ou processus. Un tel environnement est une atmosphère inerte, qui se caractérise par l'absence de gaz réactifs qui pourraient interférer avec le résultat souhaité. Des gaz inertes tels que l'azote, l'argon et l'hélium sont couramment utilisés pour créer cet environnement, ce qui peut être réalisé grâce à des techniques telles que la purge, la couverture ou l'utilisation de boîtes à gants.
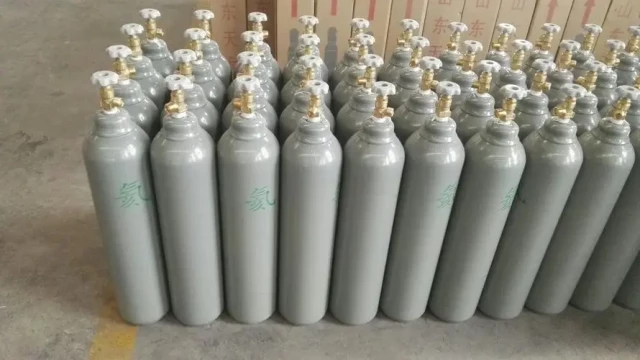
Définition de l'atmosphère inerte
Une atmosphère inerte est un environnement contrôlé utilisé pour diverses applications de laboratoire et industrielles, dans lequel l'atmosphère est exempte de gaz réactifs susceptibles de provoquer des réactions chimiques indésirables. Les gaz inertes, tels que l'azote, l'argon et l'hélium, sont couramment utilisés pour créer un tel environnement. Ces gaz sont considérés comme inertes car ils ne réagissent pas chimiquement avec d'autres substances, ce qui les rend idéaux pour créer un environnement contrôlé.
Créer une atmosphère inerte
Il existe plusieurs façons de créer une atmosphère inerte, y compris la purge, la couverture et l'utilisation de boîtes à gants. La purge consiste à éliminer tout l'air d'un conteneur ou d'un système et à le remplacer par un gaz inerte. La couverture consiste à remplir un récipient avec un gaz inerte pour créer une couche de gaz qui empêche l'entrée d'air ou d'autres gaz réactifs. Les boîtes à gants sont des espaces de travail fermés qui utilisent une atmosphère de gaz inerte pour créer un environnement contrôlé.
Utilisations des atmosphères inertes
Les atmosphères inertes sont utilisées dans diverses applications de laboratoire et industrielles, y compris les processus de traitement thermique tels que le frittage, le recuit brillant et la carbonitruration. Ces processus nécessitent des atmosphères hautement contrôlées pour produire des pièces de qualité pour des industries telles que l'aérospatiale, l'automobile et la pétrochimie. Les atmosphères inertes sont également utilisées dans la production de semi-conducteurs, où la pureté est essentielle.
Gaz inertes courants
Les gaz inertes les plus couramment utilisés pour créer une atmosphère inerte sont l'azote, l'argon et l'hélium. L'azote est le gaz inerte le plus abordable et le plus largement utilisé et est souvent utilisé dans des applications où l'humidité et l'oxygène doivent être éliminés. L'argon est un gaz plus dense et est couramment utilisé dans les applications qui nécessitent une barrière de gaz inerte plus importante. L'hélium est le gaz inerte le plus léger et est utilisé dans les applications où une faible densité et une conductivité thermique élevée sont requises.
En conclusion, une atmosphère inerte est un environnement contrôlé dans lequel l'atmosphère est exempte de gaz réactifs qui pourraient interférer avec le résultat souhaité. Cet environnement est crucial dans les applications de laboratoire et industrielles où la précision et le contrôle sont essentiels. L'utilisation de gaz atmosphériques inertes, tels que l'azote, l'argon et l'hélium, est essentielle pour créer cet environnement et garantir la qualité, la fiabilité et la reproductibilité des expériences de laboratoire et des processus industriels.
Pourquoi est-il important d'utiliser des atmosphères inertes ?
Les gaz à atmosphère inerte sont essentiels pour de nombreux processus de traitement thermique en raison de leur capacité à créer un environnement contrôlé qui empêche les réactions chimiques indésirables, l'oxydation et la contamination du produit. Dans cette section, nous discuterons des raisons pour lesquelles il est important d'utiliser des atmosphères inertes dans les atmosphères de four.
Prévenir les réactions chimiques indésirables
Lorsque vous travaillez avec un traitement thermique, un frittage ou un brasage, la présence de certains gaz tels que l'oxygène ou la vapeur d'eau peut provoquer une oxydation ou d'autres réactions chimiques indésirables. Des gaz inertes, tels que l'azote, l'argon et l'hélium, sont utilisés pour déplacer l'oxygène et la vapeur d'eau de la chambre du four, créant une atmosphère dépourvue de gaz réactifs. Cela garantit que le processus est contrôlé et que le résultat souhaité est atteint.
Amélioration de la qualité des produits
L'utilisation de gaz inertes peut augmenter l'efficacité du processus en réduisant la quantité d'énergie nécessaire pour atteindre la température souhaitée et en accélérant le processus de refroidissement. De plus, l'atmosphère inerte aide à prévenir l'oxydation et la contamination du produit, ce qui se traduit par un résultat final de meilleure qualité. Ceci est particulièrement important pour les industries telles que l'aérospatiale, l'automobile ou la pétrochimie, où des pièces critiques sont fabriquées.
Atteindre la précision et la répétabilité
Pour les processus de traitement thermique qui nécessitent une atmosphère hautement contrôlée, tels que le recuit brillant, le frittage et la carbonitruration, il est essentiel d'obtenir précision et répétabilité. Les fours utilisés dans ces processus doivent supporter une atmosphère contrôlée afin d'obtenir des résultats réussis, de haute précision et reproductibles pour ces pièces. Des atmosphères inertes sont utilisées pour s'assurer que le processus est contrôlé et que le résultat souhaité est atteint.
Réduire les dommages aux fournaises et les blessures des employés
Une atmosphère mal contrôlée pourrait endommager un four ou, pire encore, blesser des employés. Les gaz inertes sont utilisés pour empêcher les réactions chimiques à la surface d'une pièce qui compromettraient sa qualité et ses performances, conduisant à des pièces rejetées. Ceci, à son tour, entraîne des pertes financières, une perte de temps et des répercussions potentiellement dangereuses pour ceux qui utilisent la pièce si ses problèmes n'étaient pas détectés.
En conclusion, l'utilisation de gaz d'atmosphère inerte dans les atmosphères de four est essentielle pour assurer un processus contrôlé et efficace, prévenir les réactions chimiques indésirables et produire des produits de haute qualité. Il est important de comprendre pourquoi nous les utilisons et quelle est la meilleure atmosphère pour une application spécifique afin d'obtenir des résultats réussis, de haute précision et reproductibles.
Gaz courants dans les atmosphères de four
Les gaz d'atmosphère inerte jouent un rôle crucial dans les atmosphères de four pour empêcher les réactions chimiques indésirables ou l'oxydation des matériaux pendant le traitement à haute température. Les gaz les plus couramment utilisés pour les applications sous atmosphère inerte sont l'azote, l'argon et l'hélium.
Azote
L'azote est le gaz le plus couramment utilisé en raison de sa disponibilité et de son prix abordable. C'est un gaz non réactif qui fournit une atmosphère protectrice. Sa teneur en carbone, oxygène et azote ne réagit pas avec l'acier, ce qui en fait un gaz idéal pour les atmosphères de four. L'azote est utilisé pour empêcher l'oxydation dans les applications de traitement thermique et est efficace pour déplacer l'oxygène de l'atmosphère.
Argon
L'argon est souvent utilisé pour les processus qui nécessitent un niveau de pureté plus élevé ou une période prolongée de traitement à haute température. L'argon est un gaz "noble" complètement inerte et ne réagit avec aucun matériau avec lequel il entre en contact. Il déplace l'oxygène, ce qui en fait un gaz idéal pour les applications où l'oxydation est indésirable. L'argon est plus cher que l'azote mais a l'avantage de pouvoir être utilisé à des températures supérieures à 1800°C sans risque de réaction.
Hélium
L'hélium est utilisé lorsqu'une faible solubilité est requise, car c'est le gaz le moins réactif. Sa faible densité et sa conductivité thermique élevée en font un gaz idéal pour certaines applications. L'hélium est souvent utilisé dans les applications de chromatographie en phase gazeuse, de détection de fuites et de refroidissement.
En résumé, ces gaz créent un environnement sans oxygène qui protège les matériaux en cours de traitement et garantit des résultats cohérents et précis. Sans l'utilisation de gaz atmosphériques inertes, des réactions indésirables peuvent se produire, entraînant des défauts du produit, une diminution de la qualité du produit et même des dommages à l'équipement. Le choix du gaz dépend des exigences spécifiques du processus de traitement thermique, et le type d'atmosphère requis déterminera le type de four nécessaire pour le réaliser.
Procédés de traitement thermique nécessitant des atmosphères inertes
Les procédés de traitement thermique qui nécessitent des températures élevées et des atmosphères contrôlées reposent souvent sur des gaz atmosphériques inertes tels que l'azote, l'argon et l'hélium. Ces gaz jouent un rôle crucial dans la création d'un environnement exempt d'oxygène et d'autres gaz réactifs susceptibles de provoquer des réactions chimiques ou une oxydation des matériaux traités.
Pourquoi les atmosphères inertes sont essentielles
L'absence d'oxygène et d'autres gaz réactifs dans l'atmosphère du four aide à maintenir la pureté des matériaux et à prévenir la contamination ou les réactions indésirables. Les atmosphères inertes sont essentielles pour un large éventail d'applications, notamment le traitement thermique des métaux, le recuit du verre et le frittage des céramiques. L'utilisation de gaz d'atmosphère inerte dans les atmosphères de four est essentielle pour garantir la qualité et l'homogénéité des produits finaux. Tout écart dans l'atmosphère du four peut avoir un impact significatif sur les propriétés du produit final, ce qui rend essentiel de maintenir un contrôle strict sur l'environnement du four.
Gaz inertes utilisés dans les processus de traitement thermique
L'argon, l'hélium et l'azote sont les gaz inertes les plus couramment utilisés dans les procédés de traitement thermique. Le choix du gaz inerte dépend du type de matériau traité et des exigences spécifiques du processus de traitement thermique. En général, l'argon et l'hélium sont plus inertes que l'hydrogène. Une atmosphère d'azote pur assure la couverture de la pièce traitée thermiquement et peut être utilisée pour purger l'atmosphère existante ou être utilisée comme gaz porteur pour les atmosphères à carbone contrôlé.
Procédés de traitement thermique utilisant des atmosphères inertes
Les atmosphères inertes sont utilisées dans une large gamme de procédés de traitement thermique, notamment :
- Recuit (métaux non ferreux, acier allié et décarburation)
- Durcissement neutre
- Trempe
- Nitruration (aciers alliés, aciers inoxydables et aciers nitrurés)
- Frittage
- Brasage (l'azote sert de gaz vecteur)
- Processus sous vide
Combinaisons de gaz inertes
Dans certains cas, une combinaison de gaz inertes peut être utilisée dans les procédés de traitement thermique. Par exemple, une atmosphère d'hydrogène + azote fonctionne bien pour un recuit brillant ; recuit de l'acier inoxydable, de l'acier allié et de l'acier non ferreux ; durcissement neutre; et frittage. L'utilisation d'une atmosphère d'hydrogène + argon fonctionne avec un recuit brillant; recuit de l'acier inoxydable, de l'acier allié et de l'acier non ferreux ; et frittage.
Conclusion
En résumé, les gaz à atmosphère inerte jouent un rôle essentiel dans les procédés de traitement thermique qui nécessitent des températures élevées et des atmosphères contrôlées. L'utilisation de ces gaz aide à maintenir la pureté des matériaux et à prévenir la contamination ou les réactions indésirables. Le choix du gaz inerte dépend du processus de traitement thermique spécifique et du type de matériau traité. Les atmosphères inertes sont essentielles pour garantir des produits finis de haute qualité dans l'industrie du traitement thermique.
Comment mesurer l'atmosphère du four
La mesure de l'atmosphère du four est une étape cruciale pour garantir le bon fonctionnement des gaz d'atmosphère inerte et le bon déroulement du processus. Voici les étapes pour mesurer l'atmosphère du four.
Étape 1 : Déterminer le type d'analyseur
Il existe plusieurs façons de mesurer l'atmosphère du four, notamment les analyseurs de conductivité thermique, d'infrarouge et de zircone. Chaque méthode a ses forces et ses faiblesses, et le choix de l'analyseur approprié dépend de l'application spécifique et du type de gaz utilisé.
Étape 2 : Calibrer l'analyseur
Avant d'utiliser l'analyseur, il est important de le calibrer pour s'assurer qu'il lit avec précision. L'étalonnage consiste à exposer l'analyseur à un mélange de gaz connu et à l'ajuster jusqu'à ce qu'il lise les valeurs correctes.
Étape 3 : Installer l'analyseur
Installez l'analyseur dans le four ou au point de prélèvement dans le flux de gaz de combustion, selon le type d'analyseur.
Étape 4 : Prendre la mesure
Une fois l'analyseur installé, effectuez la mesure. La fréquence des mesures dépendra de l'application spécifique, mais il est important de surveiller régulièrement l'atmosphère du four pour maintenir son intégrité et assurer une qualité constante du produit.
Étape 5 : Interpréter les résultats
Interpréter les résultats obtenus à partir de l'analyseur et prendre des mesures correctives si nécessaire. Si les résultats indiquent que l'atmosphère du four ne fonctionne pas correctement, réglez les gaz de l'atmosphère inerte pour maintenir le bon équilibre.
En suivant ces étapes, les fabricants peuvent optimiser leurs processus et produire des produits de haute qualité avec précision et efficacité.
Outils de mesure et d'échantillonnage
Les gaz d'atmosphère inerte sont des composants cruciaux dans les atmosphères de four, et il est essentiel d'assurer leur sécurité et leur efficacité pendant les opérations à haute température. La mesure et l'échantillonnage de ces gaz est donc une tâche critique en laboratoire.
Analyseurs de gaz
Les analyseurs de gaz sont des outils sophistiqués qui effectuent une analyse précise des échantillons de gaz, en détectant les impuretés et les changements de concentration. Ils sont utilisés pour mesurer un large éventail de paramètres, notamment l'oxygène, le dioxyde de carbone et la vapeur d'eau. Les analyseurs de gaz sont très sensibles et peuvent détecter les moindres changements dans la composition des gaz, ce qui les rend idéaux pour surveiller les gaz inertes dans l'atmosphère.
Chromatographes en phase gazeuse
Les chromatographes en phase gazeuse sont des outils puissants qui peuvent séparer et analyser les composants individuels d'un échantillon de gaz. Ils sont capables de détecter des traces d'impuretés et peuvent mesurer avec précision les concentrations de divers gaz. Les chromatographes en phase gazeuse sont largement utilisés en laboratoire et peuvent être utilisés pour analyser les gaz d'atmosphère inerte à des fins de sécurité et de contrôle de la qualité.
Équipement d'échantillonnage
Un équipement d'échantillonnage approprié est essentiel pour mesurer et surveiller les gaz d'atmosphère inerte. Les sacs d'échantillonnage de gaz, par exemple, sont utilisés pour collecter des échantillons de gaz à analyser, tandis que les seringues à gaz sont utilisées pour extraire des échantillons directement d'un flux de gaz. D'autres types d'équipements d'échantillonnage comprennent des détecteurs de gaz, qui peuvent détecter la présence de gaz spécifiques, et des capteurs de gaz, qui peuvent mesurer les concentrations de gaz en temps réel.
Équipement d'étalonnage
L'équipement d'étalonnage est essentiel pour garantir la précision des analyseurs de gaz et autres outils de mesure de gaz. Les gaz d'étalonnage, tels que l'azote et l'oxygène, sont utilisés pour étalonner les analyseurs de gaz et garantir des lectures précises. L'équipement d'étalonnage est également utilisé pour vérifier la précision des capteurs de gaz et d'autres outils de mesure de gaz.
Avantages de la mesure et de l'échantillonnage des gaz atmosphériques inertes
La mesure et l'échantillonnage des gaz d'atmosphère inerte sont importants pour maintenir la sécurité et la qualité des processus de traitement thermique. L'échantillonnage et l'analyse réguliers des gaz inertes de l'atmosphère peuvent aider à identifier les problèmes potentiels dans le fonctionnement des fours et à éviter des dommages coûteux à l'équipement. Il peut également aider les professionnels de laboratoire et les ingénieurs à optimiser leurs processus de traitement thermique, ce qui améliore la qualité des produits et réduit les coûts de production.
En conclusion, la mesure et l'échantillonnage des gaz d'atmosphère inerte est une tâche critique en laboratoire. Les analyseurs de gaz, les chromatographes en phase gazeuse, l'équipement d'échantillonnage, l'équipement d'étalonnage et d'autres outils sont tous des composants essentiels de ce processus. En mesurant et en surveillant régulièrement les gaz d'atmosphère inerte, les professionnels de laboratoire peuvent garantir la sécurité et l'efficacité des procédés de traitement thermique et maintenir la qualité de leurs produits.
Conclusion sur l'importance des atmosphères inertes
Les atmosphères inertes jouent un rôle crucial dans le processus de traitement thermique des matériaux. Ils aident à prévenir l'oxydation, la décarburation ou d'autres réactions indésirables qui peuvent se produire en présence d'oxygène ou d'autres gaz réactifs. En utilisant des gaz inertes, tels que l'azote ou l'argon, dans les atmosphères des fours, les matériaux peuvent être chauffés et refroidis dans un environnement contrôlé, garantissant des résultats cohérents et fiables. Il est important de mesurer et de surveiller l'atmosphère dans le four pour s'assurer que les conditions souhaitées sont maintenues. L'utilisation appropriée d'atmosphères inertes peut entraîner une amélioration de la qualité des produits, une réduction des taux de rebut et une augmentation de la productivité dans l'industrie du traitement thermique.
CONTACTEZ-NOUS POUR UNE CONSULTATION GRATUITE
Les produits et services de KINTEK LAB SOLUTION ont été reconnus par des clients du monde entier. Notre personnel se fera un plaisir de répondre à toute demande que vous pourriez avoir. Contactez-nous pour une consultation gratuite et parlez à un spécialiste produit pour trouver la solution la plus adaptée aux besoins de votre application !