Principe du pressage isostatique à froid (CIP)
Table des matières
- Principe du pressage isostatique à froid (CIP)
- Comparaison entre le CIP et le pressage de moules métalliques
- Introduction au pressage de moules métalliques
- Processus automatisés dans les équipements industriels de pressage de moules métalliques
- Différences dans les processus de pressurisation du CIP et du pressage de moules métalliques
- Comparaison de la répartition de la densité dans les produits moulés par CIP et Metal Mold Pressing
- Types de traitement CIP
- Segmentation du marché
- Détails du processus de sac humide
- Détails du processus de sac sec
Comprendre le principe du CIP basé sur le concept de pression de Blaise Pascal
Le pressage isostatique à froid (CIP) est une méthode de traitement des matériaux basée sur le principe proposé par Blaise Pascal, connu sous le nom de loi de Pascal. Selon ce principe, la pression appliquée dans un fluide enfermé est transmise dans toutes les directions à travers le fluide sans aucun changement d'amplitude.
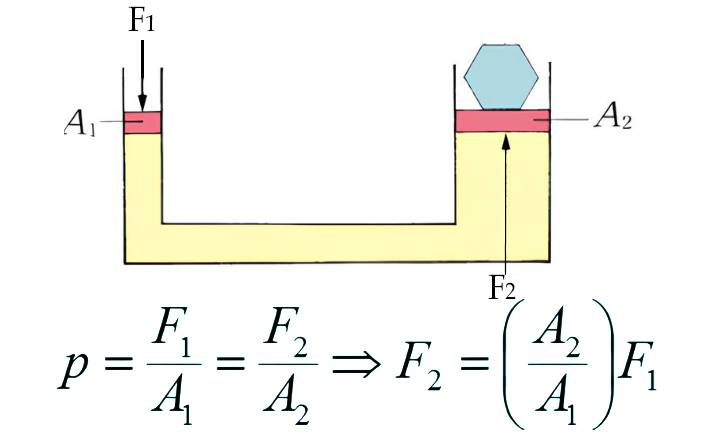
En CIP, les poudres sont compactées en les enfermant dans un moule en élastomère, qui présente une faible résistance à la déformation. Le moule est ensuite soumis à une pression liquide uniforme qui comprime les poudres. Il en résulte la formation d'un solide très compact.
Le CIP peut être utilisé pour traiter une variété de matériaux, notamment les plastiques, le graphite, la métallurgie des poudres, la céramique et les cibles de pulvérisation. Il s’agit d’une méthode polyvalente pour façonner et compacter des poudres en composants de différentes tailles et formes.
Processus de scellement de matériaux en poudre dans un moule de formage et application d'une pression de liquide
Dans le processus CIP, les matériaux en poudre sont scellés dans un moule de formage à faible résistance à la déformation, tel qu'un sac en caoutchouc. La pression du liquide est ensuite appliquée uniformément sur le moule, comprimant les poudres. Cette pression du liquide est transmise dans tout le moule, entraînant une compression uniforme du corps moulé sur toute sa surface.
Le CIP est réalisé à température ambiante et utilise un moule fabriqué à partir d'un matériau élastomère, tel que l'uréthane, le caoutchouc ou le chlorure de polyvinyle. Le fluide utilisé dans le CIP est généralement de l'huile ou de l'eau, et la pression appliquée pendant l'opération varie généralement de 60 000 lb/po2 (400 MPa) à 150 000 lb/po2 (1 000 MPa).
L’avantage du CIP est qu’il permet de réduire la distorsion, d’améliorer la précision et de minimiser le risque d’emprisonnement d’air et de vides. Il est largement utilisé dans diverses industries, notamment le médical, l’aérospatiale et l’automobile, pour la production de composants.
Le pressage de moules métalliques est une méthode similaire au CIP. Dans ce processus, les matériaux en poudre sont remplis dans un espace confiné par le moule métallique et le poinçon inférieur. Ils sont ensuite compressés en réduisant la distance entre les poinçons supérieur et inférieur.
Dans l’ensemble, le CIP est une méthode efficace pour façonner et compacter des matériaux en poudre en composants solides, offrant un haut niveau de précision et réduisant le risque de défauts.
Comparaison entre le CIP et le pressage de moules métalliques
Introduction au pressage de moules métalliques
Le pressage de moules métalliques est une méthode de traitement des matériaux similaire au pressage isostatique à froid (CIP). Dans cette méthode de pressage, les matériaux en poudre sont remplis dans un espace délimité par le moule métallique et le poinçon inférieur. Ils sont ensuite compressés en réduisant la distance entre les poinçons supérieur et inférieur.
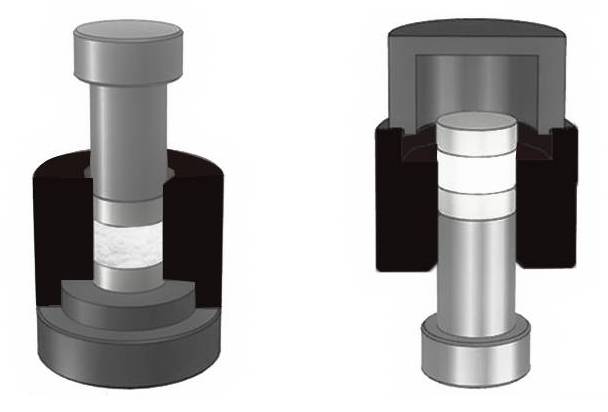
Processus automatisés dans les équipements industriels de pressage de moules métalliques
L’équipement de pressage de moules métalliques utilisé en milieu industriel comprend une série de processus automatisés. Ces processus comprennent le remplissage de poudre, la compression et le retrait du corps moulé. Le pressage à simple effet, une méthode couramment utilisée, comprime la poudre pour lui donner une forme avec le poinçon inférieur fixé.
Différences dans les processus de pressurisation du CIP et du pressage de moules métalliques
La principale différence entre le CIP et le pressage de moules métalliques réside dans les processus de pressurisation qu'ils utilisent. Le CIP applique une pression isostatique aux matériaux en utilisant la pression du liquide, tandis que le pressage des moules métalliques applique uniquement une pression uniaxiale. Cette différence se traduit par la production de produits avec des distributions de densité différentes.
Comparaison de la répartition de la densité dans les produits moulés par CIP et Metal Mold Pressing
CIP produit des produits avec une densité et une homogénéité uniformes grâce à l'absence de frictions avec un moule métallique. D’un autre côté, le pressage des moules métalliques peut entraîner des variations dans la répartition de la densité. La partie inférieure d'un corps moulé produit par pressage d'un moule métallique a tendance à avoir une densité inférieure à celle de sa partie supérieure. Ceci est dû aux frottements entre la poudre et le moule métallique ou le poinçon, ainsi qu'entre les particules de poudre.
En résumé, le CIP et le pressage de moules métalliques sont des méthodes de traitement des matériaux utilisées dans diverses industries. Bien qu'ils partagent des similitudes, telles que l'utilisation de matériaux en poudre et la compression, ils diffèrent par leurs processus de pressurisation et la répartition de la densité qui en résulte dans les produits moulés. Le CIP offre une densité et une homogénéité uniformes, tandis que le pressage des moules métalliques peut entraîner des variations de densité.
Types de traitement CIP
Les méthodes de moulage CIP sont classées en deux types ; le processus de sac humide et le processus de sac sec, selon la relation entre un moule de formage pour remplir la poudre et un milieu sous pression pour transmettre la pression.
Processus de sac humide
Dans le processus de sac humide, comme le montre la figure ci-dessous, la poudre est remplie dans un moule de formage et scellée hermétiquement à l'extérieur du récipient haute pression avant d'être immergée directement dans un milieu sous pression. Ensuite, une pression isostatique est appliquée sur les surfaces extérieures du moule pour comprimer la poudre et lui donner une forme. Cette méthode convient à divers types de production de petite qualité pour des produits de forme complexe ou à grande échelle et à la recherche sur la production d'essai.
Limites:
- Temps de cycle : 5 à 30 minutes pour un sac humide
- Froid (température ambiante)
- Densité verte uniforme
- Plus lent que le pressage uniaxial
- Formes complexes sans cire
- Les pièces peuvent nécessiter un post-usinage
Processus de sac sec
Dans le processus de sac sec, automatisé, une pièce à la fois, la poudre est remplie dans un moule de formage et scellée hermétiquement à l'intérieur du récipient haute pression. Ensuite, le fluide sous pression est introduit dans le récipient sous pression et une pression isostatique est appliquée sur les surfaces extérieures du moule pour comprimer la poudre pour lui donner une forme. Cette méthode permet de produire des pièces de formes différentes de manière rentable.
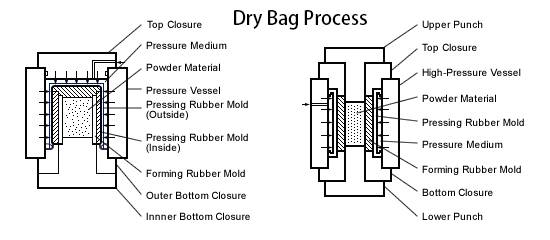
Limites:
- Temps de cycle : 3 à 5 minutes
- Chaud (100°C)
- Élimine le post-frittage
- Chaud (2200°C)
- Améliore les propriétés mécaniques et physiques
- Les temps de cycle peuvent être lents : 10-15 h
- Forme proche du net
- Pleine densité
CIP en sac humide
Deux types de méthodes CIP ont évolué au fil des années : le sac humide et le sac sec. La méthode dite du sac humide est utilisée pour produire des formes mixtes. On estime qu'il existe aujourd'hui plus de 3 000 presses à sacs humides utilisées dans le monde, d'une taille allant de 50 à 2 000 mm de diamètre.
Applications du processus CIP
En tant que technologie de traitement de forme quasi nette, le CIP est généralement utilisé dans les applications suivantes :
- Les applications dans lesquelles le matériau est relativement cher et minimisent donc les déchets (par exemple sous forme de copeaux d'usinage) en utilisant un processus de forme quasi nette offriraient un avantage économique et environnemental significatif.
- Applications où les matériaux sont difficiles à usiner et où il est plus viable de façonner la pièce par traitement en poudre.
- Applications où la complexité géométrique de la pièce nécessite un outillage coûteux (ex : canisters sacrificiels en HIP). Le CIP utilise des outils flexibles réutilisables (ou potentiellement jetables) relativement peu coûteux qui permettent de produire des formes complexes.
- Applications où l'uniformité et l'homogénéité de la microstructure sont requises pour obtenir des performances mécaniques spécifiques. Le traitement des poudres de manière isostatique offre un avantage relatif par rapport à d'autres procédés, tels que le pressage uniaxial ou le moulage.
- Applications où des structures multi-matériaux ou graduées sont requises. Dans certaines applications, les techniques d'assemblage traditionnelles ne conviennent pas, c'est pourquoi CIP propose un processus d'assemblage à semi-conducteurs.
Bien que le procédé CIP ait été développé il y a de nombreuses années, les applications commerciales des métaux sont relativement limitées. Les applications traditionnelles se concentraient sur les préformes et les formes relativement simples, telles que les pièces tubulaires ou solides avec des rapports d'aspect élevés, telles que les tuyaux, les raccords à pression hydrauliques et les revêtements de cuves à parois minces. Récemment, le CIP a été envisagé pour des applications relativement avancées dans des secteurs à forte valeur ajoutée. Par exemple, les applications automobiles incluent le forgeage de préformes pour les bielles et les composants en aluminium du système de phaseur de came du véhicule. Les applications aérospatiales comprennent les chambres de poussée refroidies par régénération. Les applications de production d'électricité comprennent les pièces de réacteurs à fission, les composants structurels des réacteurs nucléaires et les alliages ferritiques renforcés par dispersion d'oxydes utilisés pour le revêtement du combustible ou les matériaux de structure des futurs systèmes nucléaires. Les applications de défense incluent les boîtiers d’ogives de missiles. CIP+HIP a été mis en œuvre pour fabriquer des boîtiers d'ogives de missiles Stinger (avec des volumes de production allant jusqu'à ).
Segmentation du marché
En fonction du type de produit, le marché des équipements de pressage isostatique à froid (CIP) est divisé en :
- Pressage de sacs humides
Dans le processus de sac humide, le matériau en poudre est enfermé dans un sac moulé flexible, qui est immergé dans un liquide à haute pression dans un récipient sous pression. Ensuite, une pression isostatique est appliquée sur les surfaces extérieures du moule pour comprimer la poudre et lui donner une forme. Ce procédé est idéal pour la production multiformes, de petites à grandes quantités, ainsi que pour le pressage de produits de grande taille.
Les processus CIP et HIP utilisent des constructions multi-matériaux : des coques en polymère avec des poudres céramiques dans le CIP et un boîtier en tôle d'acier doux soudé avec des alliages de métallurgie des poudres haut de gamme dans le HIP. Les deux méthodes présentent donc une opportunité pour le prétraitement en une seule étape des constructions via la fabrication additive multi-matériaux. Cette approche pourrait être particulièrement bénéfique pour la production de petites séries ou de prototypes, et pourrait même réduire les coûts de fabrication en permettant une complexité accrue des pièces avec moins d'étapes et de temps de traitement.
Détails du processus de sac humide
Explication du processus de sac humide
La technologie des sacs humides est une méthode utilisée pour mouler la poudre en la remplissant dans un moule et en la fermant hermétiquement. Le moule est ensuite immergé dans un fluide sous pression dans un récipient sous pression. Une pression isostatique est appliquée sur la surface externe du moule, comprimant la poudre en une masse solide. Ce procédé convient à la production de formes multiples et de petites à grandes quantités.
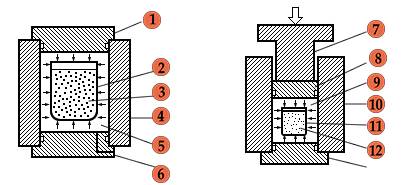
Le procédé en sac humide n’est pas aussi courant que le procédé en sac sec, mais il est encore largement utilisé. Il existe aujourd’hui plus de 3 000 presses à sacs humides utilisées dans le monde, d’une taille allant de 50 mm à 2 000 mm de diamètre. Des pompes à grand volume et des mécanismes de chargement améliorés peuvent contribuer à accélérer le processus, qui prend généralement de 5 à 30 minutes.
Adéquation du procédé Wet Bag à différents types de production
Le procédé de sac humide convient à divers types de production, en particulier aux produits de forme complexe ou à grande échelle et à la recherche sur la production d'essais. Il permet de produire des produits aux formes complexes qui peuvent être difficiles à réaliser avec d’autres méthodes. Ce procédé convient également à la production en petites quantités et peut également être utilisé pour la production de masse.
Types structurels de processus de sac humide : type de pressurisation externe et type de pressurisation directe à piston
Il existe deux types structurels de processus de sac humide : le type à pressurisation externe et le type à pressurisation directe à piston.
Le type de pressurisation externe consiste à pressuriser le fluide sous pression dans le récipient sous pression depuis l'extérieur. Le fluide sous pression est appliqué à l’extérieur du moule, comprimant la poudre à l’intérieur.
Le type à pressurisation directe à piston, quant à lui, met directement sous pression le fluide sous pression scellé à l'intérieur du récipient haute pression avec un piston installé à la place de la fermeture supérieure. Ce type de processus de sac humide élimine le besoin de pressurisation externe, ce qui le rend plus efficace.
Dans l’ensemble, le procédé du sac humide offre une méthode unique de moulage de poudre et convient à différents types de production. Il permet la production de produits de formes complexes et peut être utilisé aussi bien pour une production en petite quantité que pour une production de masse. Les deux types structurels du procédé de sac humide offrent flexibilité et efficacité dans le processus de moulage.
Détails du processus de sac sec
Explication du processus de sac sec
Le procédé Dry Bag est une méthode permettant de mouler de la poudre remplie dans un moule en caoutchouc de formage en transmettant la pression à travers un moule en caoutchouc pressant dans le récipient à haute pression. Cette méthode convient à la production en série d’une variété simple et limitée de produits grâce à son fonctionnement automatique permettant d’économiser du travail.
Adéquation du processus de sac sec pour la production de masse
Le pressage des sacs secs est différent du pressage des sacs humides dans le sens où une membrane flexible est intégrée dans le récipient sous pression et est utilisée pendant tous les cycles de pressage. Cette membrane isole le fluide sous pression du moule, qui devient un « sac sec ». Ce processus est beaucoup plus propre car le moule flexible n'est pas contaminé par de la poudre humide. De plus, moins de nettoyage du navire est nécessaire. Cette méthode a des cycles rapides et est idéale pour la production de masse automatisée de produits en poudre.
Classification des systèmes Dry Bag Process : système de pressurisation circonférentielle + axiale et système de pressurisation circonférentielle
Le procédé Dry Bag est classé en deux systèmes : le système de pressurisation circonférentielle + axiale et le système de pressurisation circonférentielle. Le système de pressurisation circonférentielle + axiale consiste à pressuriser le fluide sous pression dans le récipient sous pression depuis l'extérieur, tandis que le système de pressurisation circonférentielle met directement sous pression le fluide sous pression scellé à l'intérieur du récipient haute pression avec un piston installé à la place de la fermeture supérieure.
La technologie Dry Bag est idéale pour la production de masse de matériaux. Ce processus ne prend généralement qu’une minute, ce qui le rend beaucoup plus rapide que la technologie des sacs humides.
Si vous êtes intéressé par nos produits, veuillez visiter le site Web de notre entreprise : https://kindle-tech.com/product-categories/isostatic-press , où l'innovation a toujours été une priorité. Notre équipe R&D est composée d’ingénieurs et de scientifiques expérimentés qui suivent de près les tendances de l’industrie et repoussent constamment les limites de ce qui est possible. Notre équipement de laboratoire intègre les dernières technologies pour garantir que vous puissiez obtenir des résultats précis et reproductibles lors de vos expériences. Des instruments de haute précision aux systèmes de contrôle intelligents, nos produits vous offriront des possibilités illimitées pour votre travail expérimental.
CONTACTEZ-NOUS POUR UNE CONSULTATION GRATUITE
Les produits et services de KINTEK LAB SOLUTION ont été reconnus par des clients du monde entier. Notre personnel se fera un plaisir de répondre à toute demande que vous pourriez avoir. Contactez-nous pour une consultation gratuite et parlez à un spécialiste produit pour trouver la solution la plus adaptée aux besoins de votre application !