Bases du pressage isostatique à froid
Table des matières
- Bases du pressage isostatique à froid
- Types de pressage isostatique à froid
- CIP vs autres techniques
- Processus de pressage isostatique à froid
- Avantages et inconvénients du CIP pour la céramique d'alumine
- Applications du pressage isostatique à froid
- Comparaison avec d'autres technologies de compression
Définition et objectif du Pressage Isostatique à Froid (CIP)
Le pressage isostatique à froid (CIP) est une méthode de traitement des matériaux par compactage des poudres grâce à l'application d'une pression uniforme dans toutes les directions. Ce processus est basé sur la loi de Pascal, selon laquelle la pression appliquée dans un fluide enfermé est transmise de manière égale dans toutes les directions.
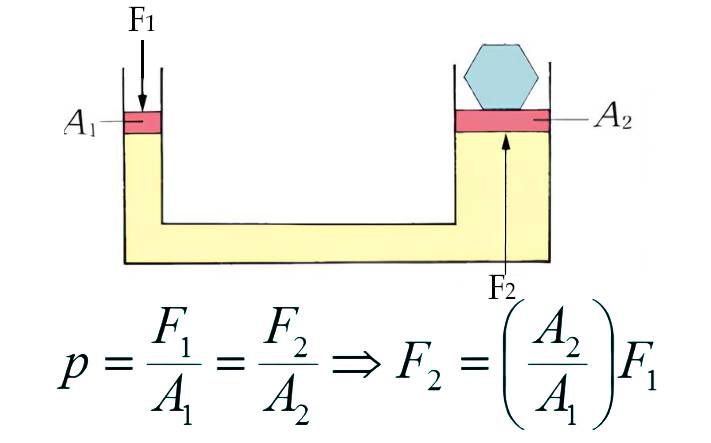
Le CIP consiste à enfermer la poudre dans un moule en élastomère et à appliquer une pression liquide pour la comprimer. Le résultat est un matériau solide très compact. Le CIP peut être utilisé pour une large gamme de matériaux tels que les plastiques, le graphite, la céramique, la métallurgie des poudres et les cibles de pulvérisation.
Différenciation entre le pressage isostatique en sac humide et en sac sec
Il existe deux types de pressage isostatique à froid : le pressage isostatique en sac humide et le pressage isostatique en sac sec.
Dans le pressage isostatique en sac humide, la poudre est enfermée dans une gaine en caoutchouc et immergée dans un liquide qui transmet uniformément la pression à la poudre. Cette méthode est utilisée pour la production à faible volume, le prototypage ainsi que la recherche et le développement.
Dans le pressage isostatique en sacs secs, le moule élastomère fait partie intégrante de la presse isostatique. La pression appliquée est principalement biaxiale et cette méthode convient à la production en grand volume.
Rôle de la qualité des poudres et de la conception des outils dans le CIP
La qualité de la poudre et la conception des outils jouent un rôle crucial dans le succès du pressage isostatique à froid.
La qualité de la poudre utilisée affecte la densité et la résistance du produit final. Les poudres avec une teneur faible ou nulle en cire sont couramment utilisées en CIP. De plus, les tolérances dimensionnelles des pièces produites par CIP sont relativement grandes, de sorte que le contrôle de la taille et de la forme peut ne pas être aussi critique que dans d'autres méthodes de pressage.
La conception des outils est également importante dans le CIP. Des moules en élastomère fabriqués à partir de matériaux comme l'uréthane, le caoutchouc ou le chlorure de polyvinyle sont utilisés. Le choix du matériau et de la conception du moule a un impact sur l’exactitude et la précision du produit final.
Concept et avantages du pressage isostatique
Le pressage isostatique, y compris le pressage isostatique à froid, offre plusieurs avantages dans le traitement des matériaux.
Un avantage majeur est la capacité à obtenir un compactage uniforme et une capacité de forme accrue par rapport au pressage uniaxial. Le pressage isostatique applique une pression dans plusieurs directions, ce qui donne des pièces de haute qualité avec une plus grande densité.
Le pressage isostatique convient également pour former des formes complexes qui ne peuvent pas être compressées par d'autres méthodes. L'utilisation de moules en élastomère permet une flexibilité et une polyvalence dans le façonnage des matériaux.
En résumé, le pressage isostatique à froid est une méthode intéressante pour façonner et compacter les poudres. Il offre des avantages uniques en termes d’uniformité, de capacité de forme et de polyvalence. En comprenant les bases du CIP et de ses applications, les entreprises peuvent tirer parti de ce processus pour produire des composants de haute qualité pour diverses industries.
Types de pressage isostatique à froid
Technique Wetbag du CIP
Le pressage isostatique à froid (CIP) est une méthode couramment utilisée pour compacter des matériaux en poudre en une masse solide et homogène avant l'usinage ou le frittage. La technique du sac humide est un sous-type de CIP où la poudre brute est versée dans des moules flexibles immergés dans l'eau ou d'autres liquides. Une pression isostatique est ensuite appliquée pour comprimer la poudre dans la forme souhaitée. Ce procédé permet de produire des composants complexes et peut même être utilisé pour presser des lingots de tungstène pesant jusqu'à 1 tonne.
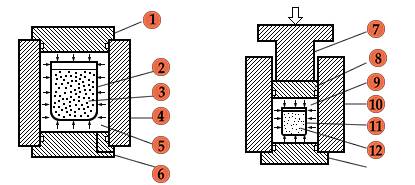
Pressage de Drybag et son application
Un autre sous-type de CIP est le pressage de sacs secs, utilisé pour des formes simples. Dans ce processus, le moule rempli de poudre est scellé et la compression se produit entre le moule et le récipient sous pression. Le pressage des sacs secs est plus adapté à la production en grand volume de formes relativement simples et peut être automatisé pour une efficacité accrue.

Comparaison de la production de formes complexes entre le CIP et le pressage uniaxial
Lorsque l’on compare le pressage isostatique à froid (CIP) au pressage uniaxial, il est évident que le CIP permet la production de formes plus complexes. Le pressage uniaxial, quant à lui, convient au pressage de formes simples aux dimensions fixes, telles que des cylindres ou des carrés. Le CIP offre une plus grande flexibilité en termes de forme et de taille, permettant la production de rapports d'aspect plus longs et un meilleur compactage de la poudre. De plus, le CIP ne nécessite pas de liant de cire comme le pressage uniaxial, éliminant ainsi le besoin d'opérations de décirage.
Avantages du CIP par rapport au pressage uniaxial
Le pressage isostatique à froid (CIP) présente plusieurs avantages par rapport au pressage uniaxial. Premièrement, le CIP permet la production de formes plus complexes par rapport au pressage uniaxial, qui se limite à des formes simples. Deuxièmement, le CIP offre des propriétés de produit plus uniformes, une plus grande homogénéité et un contrôle plus précis des dimensions du produit fini. Il permet également des rapports d’aspect plus longs, une densification améliorée de la poudre et la possibilité de traiter des matériaux présentant des caractéristiques et des formes différentes. De plus, le CIP réduit les temps de cycle et améliore la productivité.
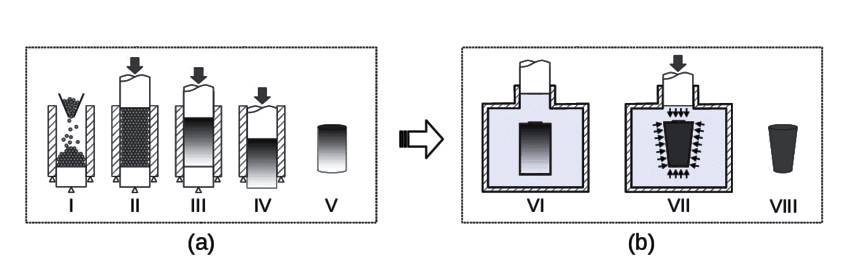
CIP vs autres techniques
Comparaison du CIP et du moulage par injection
Lorsque des composants de forme complexe sont requis au-delà des capacités du pressage uniaxial et qu'un débit de production en grand volume est nécessaire, deux options principales sont utilisées : le CIP (pressage isostatique à froid) et le moulage par injection. Le CIP a été la première méthode de haute technologie rapportée dans la littérature pour fabriquer des céramiques d'alumine. Par rapport au pressage uniaxial, le CIP permet des formes plus complexes et des gradients de pression de pressage considérablement réduits, ce qui entraîne moins de distorsions et de fissures. Cependant, le CIP n'est pas aussi courant dans l'industrie que le moulage par injection et n'est généralement utilisé que lorsque des formes très complexes sont requises et que le moulage par injection n'est pas pratique.
Rôle du CIP dans la fabrication de céramiques d'alumine
Le CIP joue un rôle crucial dans la fabrication de céramiques d'alumine. Il permet la production de composants de forme complexe qui dépassent les capacités d’autres techniques telles que le pressage uniaxial. La matière première CIP pour les céramiques d'alumine peut être de l'alumine Bayer simplement broyée, de l'alumine Bayer broyée et séchée par pulvérisation, ou des nanopoudres SolGel de haute technologie séchées par pulvérisation. Certains des principaux avantages du CIP pour les céramiques d'alumine incluent la capacité de produire des formes plus complexes, des gradients de pression de pressage réduits, un faible coût de moulage pour des pièces complexes avec de petites séries de production, l'absence de limitation de taille et des temps de cycle de traitement courts.
Utilisation du CIP dans la production d'isolateurs de bougies d'allumage
Les isolateurs de bougies d’allumage sont l’un des composants céramiques les plus produits au monde par CIP. Environ 3 milliards d’isolateurs de bougies d’allumage sont CIPed chaque année. L'utilisation du CIP dans la production d'isolateurs de bougies d'allumage démontre sa capacité à gérer de gros volumes de production et des formes complexes. Le CIP est le pilier de l'industrie des bougies d'allumage et constitue un processus relativement peu coûteux, idéal pour les formes complexes et les grandes séries de production.
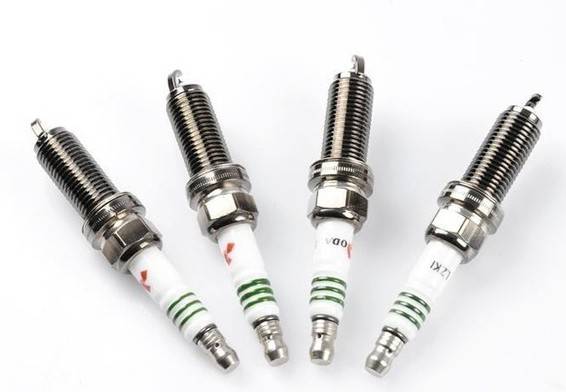
Types de matières premières CIP
Dans la production de céramiques d’alumine par CIP, différents types de matières premières peuvent être utilisés. Les matières premières couramment utilisées comprennent l'alumine Bayer broyée simple, l'alumine Bayer broyée et séchée par pulvérisation et, dans de rares cas, des nanopoudres SolGel de haute technologie séchées par pulvérisation. Le choix de la matière première dépend des exigences spécifiques du composant céramique produit. La matière première CIP nécessite une excellente fluidité, qui est généralement obtenue par séchage par pulvérisation ou par vibration du moule pendant le remplissage.
Avantages du CIP :
- Des formes plus complexes sont possibles par rapport au pressage uniaxial
- Gradients de pression de pressage considérablement réduits, ce qui entraîne moins de distorsions et de fissures
- Faible coût de moulage, idéal pour les pièces complexes avec de petites séries de production
- Aucune limitation de taille, adapté aux très grands composants
- Temps de cycle de traitement courts, aucun séchage ni brûlure du liant requis
Inconvénients du CIP :
- Contrôle dimensionnel limité par rapport au compactage avec matrice métallique
- La complexité de la forme est supérieure au pressage uniaxial mais inférieure au moulage par injection de poudre (PIM)
- Les poudres pour CIP nécessitent une excellente fluidité, souvent obtenue par séchage par pulvérisation
- Capacité et capacité limitées des navires
- Processus relativement manuel avec des taux de production inférieurs à ceux du compactage à matrice métallique
Le CIP est un procédé à l'état solide qui offre plusieurs avantages pour la production de composants métalliques hautes performances. Il offre une microstructure uniforme, une complexité de forme, un faible coût d'outillage, une évolutivité des processus et la possibilité de produire des pièces de forme presque nette avec un minimum de déchets de matériaux. Cependant, il présente également des limites, telles qu'être limité au traitement de certains types de poudres, à une capacité et une capacité de récipient limitées et à nécessiter davantage de post-traitement par rapport aux processus utilisant des outils rigides. Malgré ces limites, le CIP reste une technique précieuse pour la production en série de céramiques avancées et la production de composants de forme complexe.
Processus de pressage isostatique à froid
Processus de pressage uniforme en CIP
Le pressage isostatique à froid (CIP) est une méthode de traitement de matériaux par compactage de poudres enfermées dans un moule en élastomère. Le moule est ensuite soumis uniformément à la pression du liquide, qui comprime les poudres en un solide très compact. Ce processus garantit que la pression est appliquée uniformément dans toutes les directions, ce qui donne un produit final homogène. Le CIP peut être utilisé pour une variété de matériaux, notamment les plastiques, le graphite, la céramique et la métallurgie des poudres.
Utilisation d'un sac souple ou d'un moule pour le CIP
En CIP, un moule en élastomère ou un sac souple est utilisé pour enfermer les poudres. Ce moule présente une faible résistance à la déformation, ce qui lui permet de se comprimer facilement sous la pression appliquée. L'utilisation d'un sac souple ou d'un moule garantit que la pression est uniformément répartie dans les poudres, ce qui donne un produit final uniforme et compact.
Concept de post-CIP
Après le processus CIP, le corps moulé subit un traitement post-CIP. Ce traitement implique un traitement ultérieur ou un frittage pour obtenir la résistance et les propriétés finales souhaitées. Les traitements post-CIP peuvent varier en fonction du matériau spécifique traité.
Rôle de la chambre à huile dans le CIP
Dans le CIP, une chambre à huile est utilisée comme fluide sous pression. La chambre à huile entoure le moule en élastomère et permet l'application d'une pression de liquide. La chambre à huile joue un rôle crucial dans la transmission uniforme de la pression appliquée au moule, garantissant ainsi un compactage uniforme des poudres.
Cycles de pressurisation et de dépressurisation en CIP
Le processus CIP implique des cycles de pressurisation et de dépressurisation. Pendant le cycle de pressurisation, la pression du liquide est appliquée sur le moule en élastomère, comprimant les poudres. La pression est maintenue pendant une durée déterminée, permettant aux poudres de se consolider. Ensuite, le cycle de dépressurisation commence, relâchant la pression et permettant de récupérer le corps moulé.
Automatisation et mise en œuvre à grande échelle du CIP
Le CIP peut être automatisé et mis en œuvre à grande échelle pour la production industrielle. L'automatisation permet un contrôle précis des cycles de pressurisation et de dépressurisation, garantissant des résultats cohérents et de haute qualité. La mise en œuvre à grande échelle du CIP permet le traitement efficace d’un grand volume de matériaux, ce qui le rend adapté à diverses industries.
Dans l’ensemble, le pressage isostatique à froid est une méthode précieuse pour traiter les matériaux, fournissant un compactage uniforme et des produits finaux de haute qualité. Son utilisation d'un moule en élastomère, d'une chambre à huile et de cycles de pressurisation garantit des résultats cohérents et permet une production à grande échelle. Que ce soit pour les plastiques, les céramiques ou la métallurgie des poudres, CIP offre une solution fiable et efficace pour le traitement des matériaux.
Avantages et inconvénients du CIP pour la céramique d'alumine
Avantages du CIP par rapport au pressage uniaxial et aux autres méthodes de formage de la céramique
Lorsque des composants de forme complexe sont requis au-delà des capacités du pressage uniaxial et qu'un débit de production de grand volume est nécessaire, le CIP (pressage isostatique à froid) et le moulage par injection sont les deux principales options utilisées. Le CIP a été la première méthode de haute technologie rapportée dans la littérature pour fabriquer des céramiques d'alumine. Il est couramment utilisé pour la production en série de céramiques avancées aux formes complexes ou de composants céramiques extrêmement grands.
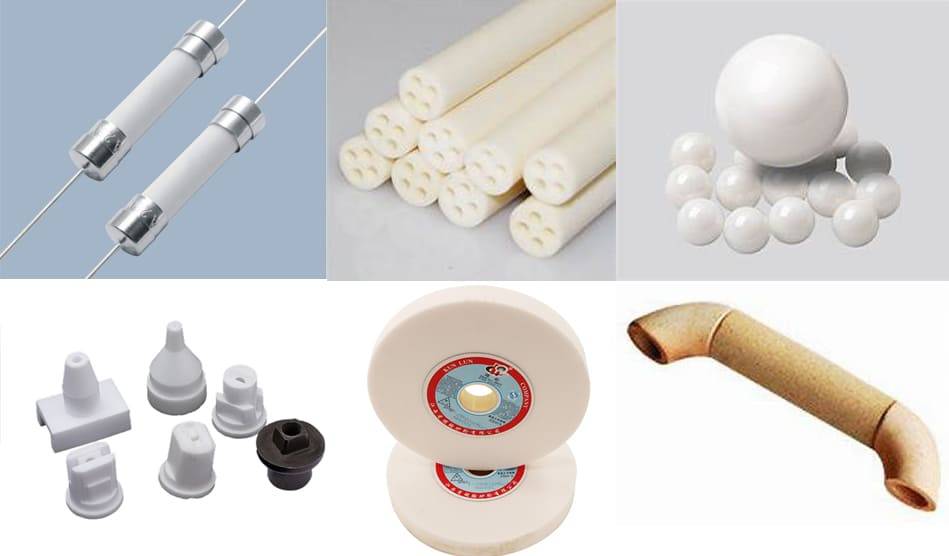
Certains des principaux avantages du CIP pour les céramiques d'alumine sont les suivants :
Des formes plus complexes sont possibles : le CIP permet la production de composants de forme complexe qui dépassent les capacités de forme du pressage uniaxial.
Gradients de pression de pressage considérablement réduits : le CIP aide à réduire la distorsion et les fissures en appliquant un pressage uniforme dans toutes les directions en trois dimensions.
Faible coût de moulage : le CIP est idéal pour les pièces complexes avec de petites séries de production, car il nécessite un faible coût de moulage.
Aucune limitation de taille : le CIP n’a aucune limitation de taille, autre que les limites de la chambre de presse. Il est donc idéal pour les composants de très grande taille, notamment ceux de forme complexe. Les composants pesant plus d'une tonne ont été CIPés.
Temps de cycle de traitement courts : le CIP ne nécessite pas de séchage ni de brûlure du liant, ce qui entraîne des temps de cycle de traitement plus courts.
Limites et défis du CIP pour la céramique
Malgré ses avantages, le CIP présente également certaines limites et défis pour la céramique :
Contrôle dimensionnel limité : L'obtention d'une haute précision est problématique en CIP en raison de la nécessité d'un moule ou d'une gaine en élastomère très fin et uniformément épais.
Complexité de forme inférieure au PIM : Bien que le CIP offre une complexité de forme supérieure à celle du pressage uniaxial, il reste inférieur au moulage par injection de poudre (PIM) en termes de complexité de forme.
Exigences de fluidité des poudres : Les poudres utilisées dans le CIP nécessitent une excellente fluidité, ce qui signifie généralement un séchage par pulvérisation ou des vibrations du moule pendant le remplissage.
Relativement manuel : le CIP est un processus relativement manuel, nécessitant une manipulation et un contrôle minutieux.
Limité au traitement de certains types de poudres : le CIP est limité au traitement de poudres présentant une excellente coulabilité, ce qui peut restreindre la gamme de matériaux pouvant être utilisés.
Capacité et capacité limitées du récipient : le CIP est limité par la capacité et la capacité de la chambre de presse, ce qui peut restreindre la taille des composants pouvant être produits.
Malgré ces limitations, le CIP reste une méthode couramment utilisée pour la production en série de céramiques avancées aux formes complexes ou en grandes séries. Il est particulièrement répandu dans l'industrie de l'alumine, où il constitue le pilier de l'industrie des bougies d'allumage et un processus relativement peu coûteux, idéal pour les formes complexes et les grandes séries de production. En plus des isolateurs de bougies d'allumage, d'autres composants couramment CIPed comprennent des composants d'usure spéciaux (tels que ceux utilisés dans les pompes et l'industrie textile) et des isolateurs électriques.
Dans l'ensemble, le CIP offre des avantages uniques pour la production de céramiques d'alumine, permettant la fabrication de composants de forme complexe avec des gradients de pression réduits et des temps de cycle de traitement plus courts. Cependant, il est important de prendre en compte ses limites et ses défis, tels que les exigences limitées en matière de contrôle dimensionnel et de fluidité de la poudre, lors du choix de la méthode de formage de la céramique appropriée pour une application spécifique.
Applications du pressage isostatique à froid
Utilisation courante du CIP dans la production de céramiques avancées
Le pressage isostatique à froid (CIP) est une technologie à base de poudre de forme presque nette utilisée pour la production de composants métalliques et céramiques. Bien qu'il soit couramment utilisé pour le traitement de la céramique, les développements récents en matière de capacités de traitement et de métallurgie des poudres ont également permis d'utiliser de plus en plus le CIP dans la fabrication de pièces métalliques hautes performances.
Des avantages tels que le traitement à l'état solide, la microstructure uniforme, la complexité des formes, le faible coût de l'outillage et l'évolutivité du processus ont fait du CIP une voie de traitement viable pour les métaux. En outre, la possibilité de produire des pièces de forme presque nette avec un minimum de déchets de matériaux a rendu le processus plus largement acceptable dans des applications de niche, telles que l'aérospatiale et l'automobile.
Les applications courantes du pressage isostatique à froid comprennent la consolidation de poudres céramiques, de graphite, de matériaux réfractaires, d'isolants électriques et la compression de céramiques avancées. Des matériaux tels que le nitrure de silicium, le carbure de silicium, le nitrure de bore, le carbure de bore, le borure de titane et le spinelle sont couramment utilisés. La technologie s'étend également à de nouvelles applications, telles que la compression de cibles de pulvérisation, le revêtement de composants de soupapes utilisés pour réduire l'usure des cylindres des moteurs et des applications dans les secteurs des télécommunications, de l'électronique, de l'aérospatiale et de l'automobile.
Rôle du CIP dans l'industrie des bougies d'allumage et l'industrie de l'alumine
CIP joue un rôle important dans l’industrie des bougies d’allumage et dans l’industrie de l’alumine. Dans l'industrie des bougies d'allumage, le CIP est couramment utilisé pour la production en série de céramiques avancées de formes complexes ou de composants céramiques extrêmement grands. Il est utilisé non seulement pour les isolateurs de bougies d'allumage, mais également pour les composants d'usure spéciaux des pompes et de l'industrie textile, ainsi que pour les isolateurs électriques.
Dans l’industrie de l’alumine, le CIP est considéré comme le pilier de l’industrie des bougies d’allumage. Il s’agit d’un processus relativement peu coûteux, idéal pour les formes complexes et les grandes séries de production. Cela en fait une technique essentielle pour fabriquer efficacement des bougies d’allumage.
Dans l’ensemble, le pressage isostatique à froid est un procédé éprouvé pour la production de pièces hautes performances dans diverses industries. Sa capacité à atteindre des densités élevées pour les céramiques et sa polyvalence dans le traitement de la céramique et des métaux en font une technique précieuse pour les fabricants.
Comparaison avec d'autres technologies de compression
Pressage isostatique à froid et pressage isostatique à chaud : un aperçu comparatif
Dans le domaine du traitement des matériaux, deux techniques puissantes se démarquent : le pressage isostatique à froid (CIP) et le pressage isostatique à chaud (HIP). Bien que les deux méthodes partagent l’objectif d’améliorer les propriétés des matériaux, elles le font dans des conditions différentes, chacune offrant des avantages uniques. Voici un aperçu comparatif du pressage isostatique à froid par rapport au pressage isostatique à chaud :
Pressage isostatique à froid (CIP) : Le pressage isostatique à froid, souvent appelé compactage isostatique à froid, consiste à soumettre un matériau à une pression uniforme de tous les côtés. Ceci est réalisé en immergeant le matériau dans un milieu fluide à haute pression et en appliquant une pression hydraulique. Le CIP est particulièrement efficace pour façonner et consolider les matériaux en poudre, créer des formes complexes et atteindre une densité verte élevée.
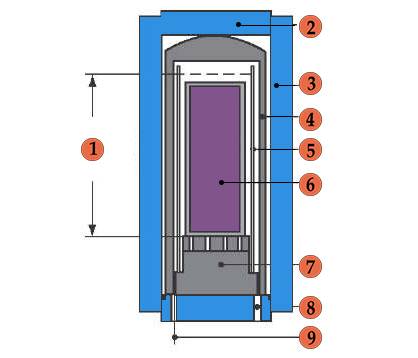
Pressage isostatique à chaud (HIP) : Le pressage isostatique à chaud (HIP) est une technologie de processus qui utilise une température et une pression élevées pour soumettre les produits métalliques ou céramiques à une pression égale dans toutes les directions afin que les pièces puissent être frittées et densifiées. En 2021, la North American Heat Treatment Association, un représentant de l'industrie mondiale du traitement thermique, a classé le pressage isostatique à chaud, la technologie de combustion de l'hydrogène et la technologie de fabrication additive comme les trois technologies et processus les plus prometteurs.
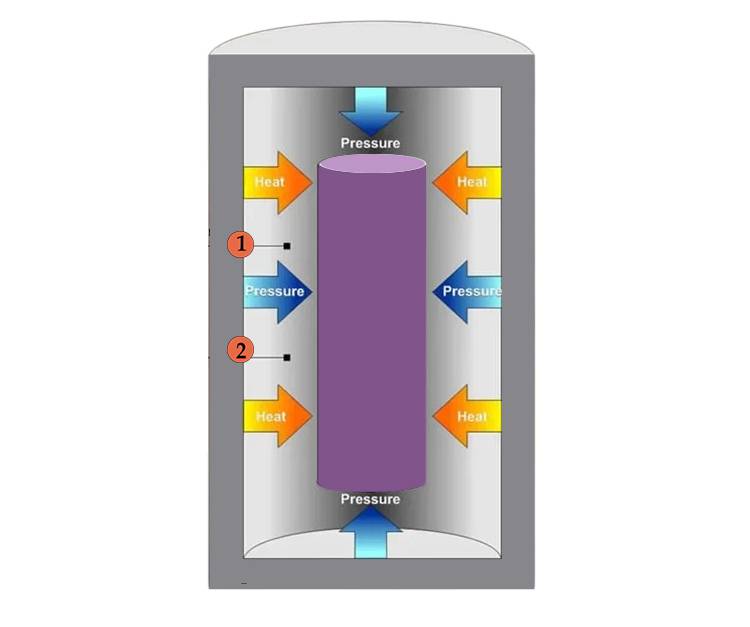
L'équipement de pressage isostatique à chaud se compose d'un récipient à haute pression, d'un four de chauffage, d'un compresseur, d'une pompe à vide, d'un réservoir de stockage, d'un système de refroidissement et d'un système de contrôle informatique, où le récipient à haute pression est le dispositif clé de l'ensemble de l'équipement.
De ce point de vue, la recherche de méthodes alternatives qui répondraient aux avancées technologiques et aux exigences technologiques non seulement pour les substrats métalliques et céramiques mais aussi pour ceux à base de polymères ont encouragé les chercheurs à travailler sur de nouvelles techniques et méthodes. La « méthode de dépôt par aérosol de poudre céramique », qui est soulignée, nécessite non seulement des étapes supplémentaires de traitement thermique ou de frittage à haute température, mais également une applicabilité homogène et continue sur de grandes surfaces. C’est devenu une tendance qui attire chaque année l’attention des chercheurs sur les technologies des matériaux semi-conducteurs. En raison de tous ces avantages, la méthode de dépôt d'aérosol a été jugée digne d'être examinée tant en termes de détails techniques que d'applicabilité, et parce qu'il s'agit d'une technologie vierge encore ouverte au développement dans le domaine, elle peut répondre au besoin dans les technologies des semi-conducteurs de nouvelle génération.
L'utilisation du pressage isostatique présente un net avantage, sauf pour l'aluminium et le fer compactés à des densités élevées. À des densités élevées, le compactage à la filière et le compactage isostatique produisent des densités vertes similaires à celles des poudres de fer et d'aluminium. Cependant, pour des matériaux tels que l'aluminium qui ont une contrainte de cisaillement constante, la pression radiale devient approximativement égale à la pression axiale, c'est-à-dire se rapproche d'une distribution de pression isostatique. Cependant, pour des matériaux comme le cuivre où la limite d'élasticité est fonction de la contrainte normale sur le plan de cisaillement, la pression radiale reste inférieure à la pression axiale. Bien que la répartition de la pression dans un comprimé pressé à froid puisse devenir isostatique, la relation pression/densité ne devrait probablement être identique à celle du compactage isostatique que si la répartition de la densité est également uniforme.
En résumé, le pressage isostatique à froid et le pressage isostatique à chaud représentent des approches distinctes du traitement des matériaux, chacune ayant ses propres avantages. La décision entre les deux dépend des objectifs spécifiques de votre projet et des caractéristiques des matériaux impliqués.
CONTACTEZ-NOUS POUR UNE CONSULTATION GRATUITE
Les produits et services de KINTEK LAB SOLUTION ont été reconnus par des clients du monde entier. Notre personnel se fera un plaisir de répondre à toute demande que vous pourriez avoir. Contactez-nous pour une consultation gratuite et parlez à un spécialiste produit pour trouver la solution la plus adaptée aux besoins de votre application !