Développement historique de la technologie de l'enrobage sous vide
Les premiers défis et la technologie CVD
La technologie de l'enduction sous vide a fait ses premiers pas dans les années 1960 avec l'avènement du dépôt chimique en phase vapeur (CVD). Cette technique pionnière, bien que révolutionnaire à l'époque, n'était pas sans poser de problèmes. L'un des obstacles les plus importants était l'exigence de températures élevées, qui limitait les types de substrats pouvant être revêtus efficacement. Les exigences thermiques élevées des procédés CVD signifiaient que seuls les matériaux à haute stabilité thermique pouvaient supporter les conditions de dépôt, ce qui réduisait considérablement le champ des applications potentielles.
En outre, les premières technologies de dépôt en phase vapeur étaient limitées par la gamme restreinte de revêtements qu'elles pouvaient produire. La complexité et la spécificité des réactions chimiques impliquées dans le dépôt en phase vapeur signifiaient que seule une poignée de matériaux pouvaient être déposés de manière fiable, ce qui restreignait encore son utilité. Ces limitations ont posé des défis importants au développement et à l'adoption généralisée de la technologie de revêtement sous vide, ce qui a nécessité la recherche de méthodes alternatives capables de surmonter ces obstacles.
Au cours des décennies suivantes, ces premiers défis ont ouvert la voie au développement de technologies de revêtement plus polyvalentes et plus efficaces, telles que le dépôt physique en phase vapeur (PVD), apparu dans les années 1970, qui offrait une solution plus adaptable et plus respectueuse de l'environnement.
Émergence de la technologie PVD
Dans les années 1970, le paysage de la technologie de revêtement sous vide a subi une transformation significative avec l'avènement de la technologie de dépôt physique en phase vapeur (PVD). Cette nouvelle méthode a non seulement répondu à certaines des préoccupations environnementales associées à son prédécesseur, le dépôt chimique en phase vapeur (CVD), mais a également introduit une myriade de propriétés de surface polyvalentes qui n'étaient pas réalisables auparavant. Le passage du dépôt chimique en phase vapeur au dépôt physique en phase vapeur a été marqué par une réduction des températures de fonctionnement et un élargissement de la gamme des revêtements pouvant être appliqués, ce qui a permis d'étendre ses applications à diverses industries.
Les avantages environnementaux du dépôt en phase vapeur sont particulièrement remarquables. Contrairement au procédé CVD, qui nécessite souvent des températures élevées et des produits chimiques potentiellement dangereux, le procédé PVD fonctionne dans des conditions plus contrôlées, ce qui permet de réduire la consommation d'énergie et les émissions. Ce respect de l'environnement, associé à sa capacité à produire des revêtements d'une dureté, d'une résistance à l'usure et d'une protection contre la corrosion supérieures, a rapidement attiré l'attention des chercheurs et des industriels.
Le développement rapide de la technologie PVD au cours de cette période peut être attribué à sa capacité d'adaptation et aux améliorations significatives qu'elle a apportées à la qualité et à la durabilité des revêtements. Des industries allant de l'automobile à l'aérospatiale ont commencé à adopter le dépôt en phase vapeur pour sa capacité à améliorer les performances des outils et des composants, ce qui a permis d'accroître l'efficacité et la durée de vie des produits. Cette adoption généralisée a favorisé les progrès des techniques de dépôt en phase vapeur, faisant avancer la technologie et consolidant sa place dans le domaine des processus industriels modernes.
Situation actuelle et défis
Un développement déséquilibré
Malgré l'adoption généralisée de la technologie de revêtement sous vide à des fins décoratives, l'application de ces revêtements dans la fabrication de moules industriels reste semée d'embûches. Le principal obstacle réside dans les exigences rigoureuses en matière d'adhérence imposées par les moules industriels, qui nécessitent une liaison plus robuste et plus durable entre le revêtement et le substrat. Cette demande accrue n'est pas facilement satisfaite par les technologies de revêtement actuelles, qui privilégient souvent l'aspect esthétique à la durabilité fonctionnelle.
En outre, l'absence de technologies de processus complètes spécialement conçues pour le revêtement des moules industriels ne fait qu'exacerber ces difficultés. Contrairement aux revêtements décoratifs, qui peuvent se permettre d'être moins rigoureux dans leurs méthodes d'application, les revêtements pour moules industriels nécessitent des processus précis et contrôlés pour garantir une performance et une longévité optimales. Cette disparité dans le développement technologique a conduit à une croissance déséquilibrée au sein de l'industrie du revêtement sous vide, où les progrès réalisés dans le domaine des revêtements décoratifs n'ont pas été reflétés de manière adéquate dans les applications industrielles.
Pour résoudre ces problèmes, il existe un besoin pressant de développer des technologies et des méthodologies spécialisées capables de répondre aux exigences uniques du revêtement des moules industriels. Il s'agit non seulement d'améliorer les propriétés d'adhérence des revêtements, mais aussi d'affiner l'ensemble de la chaîne de traitement, du prétraitement au contrôle de qualité post-application. En se concentrant sur ces domaines, l'industrie peut combler le fossé entre les revêtements décoratifs et industriels, favorisant ainsi une trajectoire de développement plus équilibrée et plus complète.
Disparités techniques
Dans le domaine des technologies de revêtement sous vide, en particulier dans le contexte du dépôt physique en phase vapeur (PVD), les capacités techniques nationales sont souvent à la traîne par rapport aux normes internationales. Cette disparité n'est pas seulement une question de sophistication de l'équipement, mais englobe également un éventail plus large de facteurs, notamment l'optimisation des processus, les progrès de la science des matériaux et les méthodologies de contrôle de la qualité.
Pour combler ce fossé, il est urgent que l'industrie nationale ne se contente pas d'introduire des équipements de pointe, mais qu'elle absorbe et intègre également les technologies de pointe. Cela implique une approche à multiples facettes, notamment
- Modernisation de l'équipement: Investir dans des chambres à vide, des alimentations électriques et des systèmes d'alimentation en gaz de pointe, capables de traiter avec précision des processus PVD complexes.
- Absorption technologique: Engagement dans la recherche et le développement en collaboration avec des partenaires internationaux afin de comprendre et de mettre en œuvre les meilleures pratiques en matière de technologie PVD.
- Optimisation des procédés: Affiner les processus existants pour garantir l'uniformité de la qualité du revêtement, en abordant des questions telles que l'adhérence et la consistance de la couche.
Aspect | Statut national | Normes internationales |
---|---|---|
L'équipement | Basique ou obsolète | Avancé et très précis |
Contrôle du processus | Manuel ou semi-automatique | Entièrement automatisé avec soutien de l'IA |
Science des matériaux | Recherche limitée | Recherche et innovation approfondies |
Contrôle de la qualité | Méthodes ad hoc | FQC systématique et rigoureux |
Le chemin vers la parité ne passe pas seulement par l'acquisition de technologies, mais aussi par le développement d'un écosystème solide qui soutient l'innovation et l'amélioration continues. Cette approche holistique est essentielle pour élever les capacités nationales et s'assurer qu'elles peuvent être compétitives à l'échelle mondiale.
Concepts de base et caractéristiques du revêtement PVD
Méthodes et techniques
Le dépôt physique en phase vapeur (PVD) englobe plusieurs méthodes avancées, chacune ayant des caractéristiques et des applications uniques. Les deux principales techniques de dépôt en phase vapeur sont le placage multi-arc et la pulvérisation magnétron.
Le dépôt multiarc implique l'évaporation d'un matériau cible à l'aide d'un arc électrique, qui ionise le matériau et le propulse vers le substrat. Cette méthode est connue pour ses taux de dépôt élevés et sa capacité à recouvrir des géométries complexes. Cependant, elle peut présenter des problèmes tels que la contamination par des particules et une épaisseur de revêtement non uniforme.
En revanche, la pulvérisation magnétron utilise un champ magnétique pour renforcer l'ionisation des atomes cibles, qui sont ensuite accélérés vers le substrat. Cette technique permet de mieux contrôler les propriétés du revêtement, notamment sa densité et son uniformité, ce qui la rend idéale pour les applications nécessitant des revêtements précis. Malgré ces avantages, la pulvérisation magnétron peut être plus lente et plus énergivore que le placage multiarc.
Méthode | Avantages | Inconvénients |
---|---|---|
Dépôt multiarc | Taux de dépôt élevés, adaptés aux géométries complexes | Contamination par des particules, épaisseur de revêtement non uniforme |
Pulvérisation magnétron | Excellent contrôle des propriétés du revêtement, densité et uniformité élevées | Processus plus lent, consommation d'énergie plus élevée |
Il est essentiel de comprendre ces méthodes et leurs avantages et inconvénients respectifs pour choisir la technique de dépôt en phase vapeur la plus appropriée pour des applications industrielles spécifiques.
Combinaison de technologies
L'intégration des technologies multi-arc et magnétron représente une avancée significative dans le domaine du revêtement sous vide. Cette combinaison n'est pas simplement la somme de ses parties, mais une approche synergique qui maximise les avantages des deux technologies, garantissant la production de revêtements stables et de haute qualité.
La métallisation multi-arc, connue pour ses taux de dépôt élevés et sa capacité à produire des revêtements denses, complète la pulvérisation magnétron, qui excelle dans la production de revêtements uniformes et conformes avec un échauffement minimal du substrat. En combinant ces méthodes, les fabricants peuvent atteindre un équilibre entre la vitesse de dépôt et l'uniformité du revêtement, ce qui est essentiel pour les applications exigeant à la fois efficacité et précision.
En outre, l'hybridation de ces technologies permet d'optimiser les propriétés du revêtement. Par exemple, l'incorporation d'ions multi-arc dans le processus de pulvérisation magnétron peut améliorer l'adhérence et la dureté des revêtements, ce qui permet de relever des défis courants dans le domaine du revêtement des moules industriels, où l'adhérence et la durabilité sont primordiales.
Cette intégration ouvre également de nouvelles voies pour la sélection des matériaux et le contrôle des processus. En tirant parti des atouts des deux technologies, il est possible de déposer une plus large gamme de matériaux aux propriétés adaptées, depuis les revêtements durs résistants à l'usure jusqu'aux structures multicouches plus complexes. Il en résulte une solution de revêtement plus polyvalente et plus robuste qui répond aux diverses exigences des différentes applications industrielles.
En résumé, la combinaison des technologies multi-arc et magnétron améliore non seulement la qualité et la stabilité des revêtements, mais élargit également le champ des propriétés matérielles et des efficacités de processus réalisables. Cette avancée est essentielle pour repousser les limites de ce que la technologie de revêtement sous vide peut réaliser, ce qui en fait une pierre angulaire de l'évolution des revêtements industriels.
Équipements et procédés de revêtement modernes
Composants et systèmes
L'équipement de revêtement moderne est un assemblage sophistiqué de composants essentiels, chacun jouant un rôle crucial dans le processus de dépôt sous vide. Au cœur de ce système se trouve lachambre à videun environnement scellé qui isole le substrat des conditions atmosphériques, garantissant une surface vierge pour le revêtement. La chambre à vide est généralement fabriquée dans des matériaux tels que l'acier inoxydable, connu pour sa durabilité et sa résistance à la corrosion.
Pour atteindre les niveaux de vide nécessaires,pièces d'obtention du vide sont utilisées. Il s'agit notamment de pompes à vide, telles que les pompes à palettes et les pompes turbomoléculaires, qui travaillent en tandem pour réduire la pression de la chambre aux niveaux ultra-faibles requis pour les procédés PVD. L'efficacité de ces pompes est essentielle, car elle a un impact direct sur la qualité et l'uniformité du revêtement.
Les blocs d'alimentation constituent un autre élément essentiel, car ils fournissent l'énergie électrique nécessaire à la vaporisation du matériau de revêtement. Les systèmes modernes utilisent souvent desdes alimentations à fréquence intermédiaire outechnologie à impulsionsLes systèmes modernes utilisent souvent des alimentations à fréquence intermédiaire ou la technologie à impulsions, qui offrent un contrôle précis du processus de dépôt, ce qui permet d'obtenir des revêtements de meilleure qualité. Ces alimentations avancées permettent d'atténuer les problèmes tels que les arcs électriques et les dépôts non uniformes, qui sont des défis courants dans les installations traditionnelles de dépôt en phase vapeur.
Enfin, lessystèmes d'alimentation en gaz de procédé font partie intégrante de l'opération. Ces systèmes introduisent des gaz réactifs dans la chambre à vide, ce qui permet la formation de revêtements complexes aux propriétés personnalisées. Le contrôle précis des débits et de la composition des gaz permet de créer des revêtements aux caractéristiques mécaniques, chimiques et optiques spécifiques, ce qui accroît la polyvalence et l'applicabilité de la technologie.
En résumé, l'équipement de revêtement moderne est une interaction complexe de chambres à vide, de pièces d'obtention du vide, d'alimentations électriques et de systèmes d'entrée de gaz de traitement, chacun contribuant à la précision et à la qualité du processus PVD.
Techniques avancées
Dans le domaine de la technologie de revêtement sous vide, plusieurs techniques avancées sont apparues, améliorant considérablement la qualité et l'applicabilité des revêtements. L'une de ces techniques est l'utilisation dechamps magnétiques non équilibrés. Ces champs permettent un contrôle plus précis du processus de dépôt, ce qui permet de créer des revêtements d'une uniformité et d'une adhérence supérieures. Cela est particulièrement utile dans les applications industrielles où la durabilité et les performances du revêtement sont essentielles.
Un autre progrès essentiel est l'introduction desalimentations à fréquence intermédiaire. Contrairement aux alimentations traditionnelles, ces systèmes à fréquence intermédiaire offrent une stabilité et une efficacité accrues. Ils facilitent le dépôt de revêtements plus épais et plus robustes sans compromettre l'intégrité du matériau sous-jacent. Cette innovation est particulièrement utile dans les industries nécessitant des revêtements de haute performance pour les moules et les outils.
En outre,technologie d'impulsion a révolutionné le processus de revêtement. En fournissant de l'énergie en courtes rafales contrôlées, la technologie par impulsions minimise le stress thermique sur le substrat, évitant ainsi le gauchissement et la dégradation. Cette méthode est particulièrement avantageuse pour les matériaux délicats ou ceux qui nécessitent des traitements de surface complexes. La précision de l'énergie délivrée garantit également une meilleure adhérence du revêtement, ce qui permet d'obtenir des résultats plus durables et plus fiables.
Ces techniques avancées contribuent collectivement à l'évolution de la technologie du revêtement sous vide, la rendant plus polyvalente et plus efficace dans diverses applications industrielles. L'intégration des champs magnétiques hors équilibre, des alimentations électriques à fréquence intermédiaire et de la technologie des impulsions permet non seulement d'améliorer la qualité des revêtements, mais aussi d'élargir leur champ d'application, répondant ainsi aux exigences de plus en plus strictes des industries modernes.
Application et contrôle de la qualité du PVD pour les moules
Procédés de prétraitement et de revêtement
Les méthodes de prétraitement sont des étapes cruciales dans la préparation des surfaces pour le revêtement par dépôt physique en phase vapeur (PVD). Ces méthodes comprennent le nettoyage à la vapeur à haute température, qui élimine efficacement les contaminants et garantit la propreté du substrat. Le sablage est une autre technique essentielle, car il permet d'obtenir une surface rugueuse qui améliore l'adhérence du revêtement. Le processus de revêtement PVD lui-même dépend fortement d'un contrôle précis de la température et d'un chauffage uniforme pour obtenir des résultats optimaux.
Le chauffage uniforme est essentiel car il garantit que le substrat est chauffé de manière homogène, ce qui permet un dépôt uniforme du matériau de revêtement. Le contrôle de la température est tout aussi important, car les écarts peuvent entraîner des incohérences dans l'épaisseur et la qualité du revêtement. Des techniques avancées telles que les alimentations électriques à fréquence intermédiaire et la technologie des impulsions sont souvent utilisées pour maintenir des conditions de chauffage stables et cohérentes, améliorant ainsi la qualité globale du revêtement PVD.
Ces processus de prétraitement et de revêtement font partie intégrante du succès des applications PVD dans les moules industriels. Ils améliorent non seulement la durabilité et les performances des moules, mais prolongent également leur durée de vie, ce qui les rend indispensables dans les environnements de fabrication de haute précision.
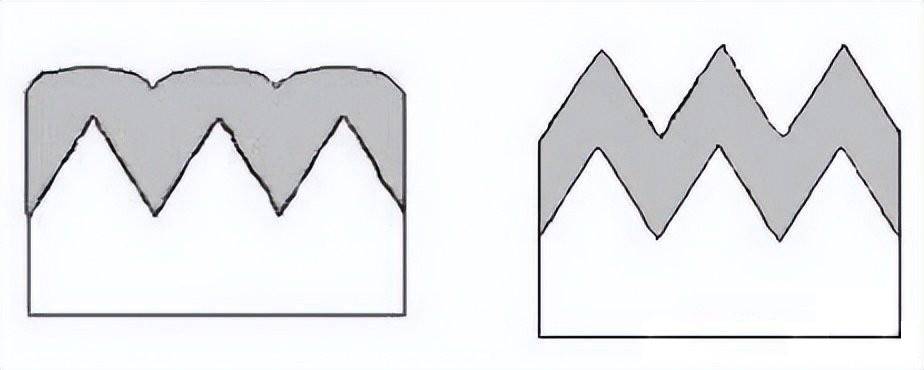
Mesures de contrôle de la qualité
Le contrôle de la qualité du fonctionnement (FQC) est un aspect essentiel pour garantir la fiabilité et les performances des moules revêtus. Ce processus comprend plusieurs inspections méticuleuses afin de garantir que les revêtements répondent aux normes requises.
L'une des principales méthodes du FQC est lel'inspection de l'apparence. Il s'agit d'un examen visuel approfondi visant à détecter les imperfections de surface telles que les rayures, les piqûres ou les décolorations. Ces défauts peuvent avoir un impact significatif sur la fonctionnalité et la durée de vie du moule, ce qui rend cette étape indispensable.
Une autre méthode clé est ll'inspection de la profondeur des couches. Cette technique permet de mesurer l'épaisseur des couches de revêtement afin de s'assurer qu'elles respectent les paramètres spécifiés. Divers instruments, tels que des profilomètres et des microscopes électroniques à balayage, sont utilisés pour déterminer avec précision la profondeur et l'uniformité du revêtement.
L'inspectioninspection de l'adhérence est également cruciale. Ce processus évalue la force d'adhérence entre le revêtement et le substrat du moule. Les méthodes les plus courantes sont les essais de rayure, les essais de traction et les essais de coupe transversale. Ces tests permettent d'identifier tout problème potentiel de délamination ou de décollement, garantissant ainsi la durabilité et l'efficacité du revêtement.
En intégrant ces méthodes FQC, les fabricants peuvent s'assurer que leurs moules revêtus sont non seulement conformes aux normes industrielles, mais qu'ils les dépassent, fournissant ainsi des outils fiables et performants pour diverses applications industrielles.
CONTACTEZ-NOUS POUR UNE CONSULTATION GRATUITE
Les produits et services de KINTEK LAB SOLUTION ont été reconnus par des clients du monde entier. Notre personnel se fera un plaisir de répondre à toute demande que vous pourriez avoir. Contactez-nous pour une consultation gratuite et parlez à un spécialiste produit pour trouver la solution la plus adaptée aux besoins de votre application !