Un four à induction utilise l'induction électromagnétique pour générer de la chaleur dans une charge métallique, ce qui permet de la faire fondre sans contact direct entre la source de chaleur et le métal.Le four est constitué d'une bobine de cuivre qui transporte un courant alternatif, créant un champ magnétique qui change rapidement.Ce champ induit des courants de Foucault dans le métal, qui génèrent de la chaleur en raison de la résistance électrique (chauffage par effet Joule).Dans les matériaux ferromagnétiques, une chaleur supplémentaire est produite par l'hystérésis magnétique.Le processus est efficace, précis et permet de contrôler la fusion des métaux à haute température, comme l'acier à 1370°C (2500°F).Le four fonctionne à des fréquences moyennes (300 Hz à 1000 Hz) afin d'optimiser le transfert d'énergie et l'efficacité du chauffage.
Explication des points clés :
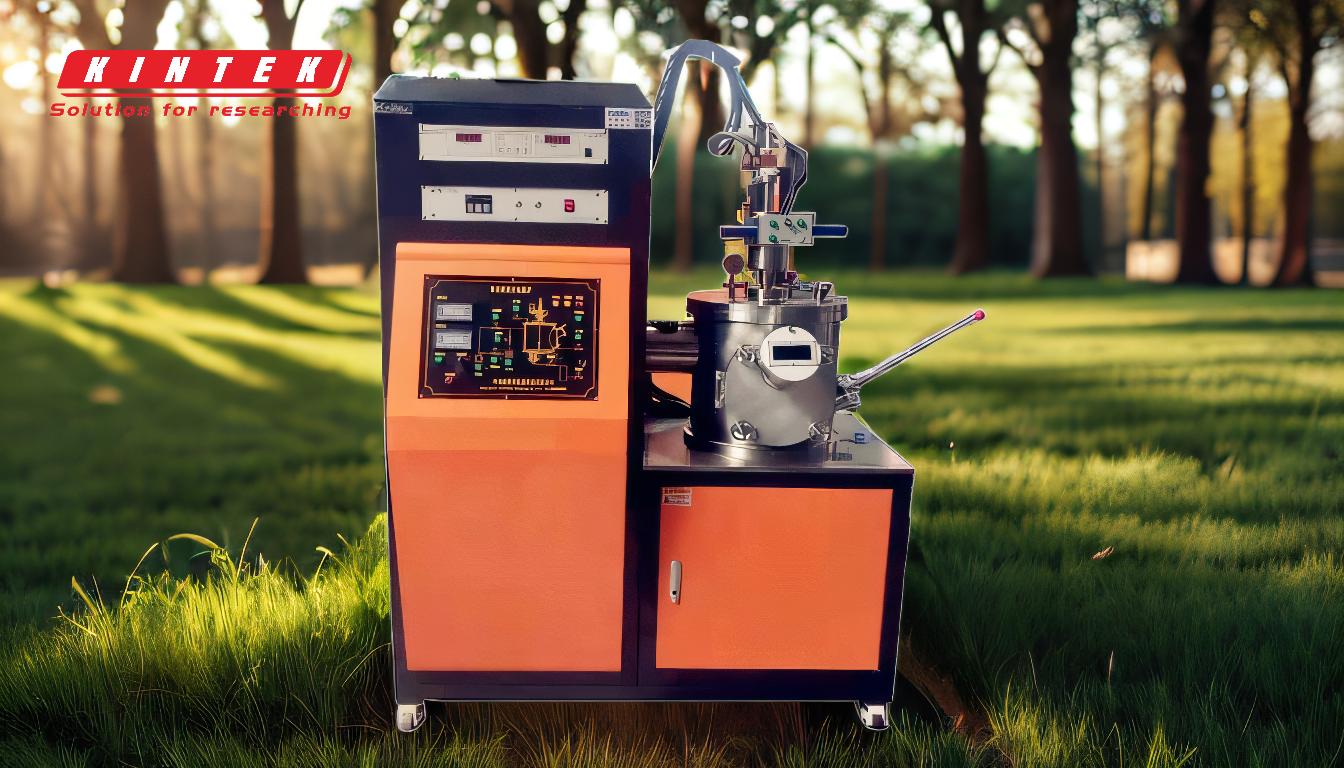
-
Induction électromagnétique:
- Le principe de base d'un four à induction est l'induction électromagnétique.Lorsqu'un courant alternatif circule dans la bobine de cuivre entourant le creuset, il génère un champ magnétique qui s'inverse rapidement.
- Ce champ magnétique pénètre la charge métallique à l'intérieur du creuset, induisant des courants de Foucault dans le métal.Ces courants circulent en boucle fermée et génèrent de la chaleur en raison de la résistance électrique du métal, un phénomène connu sous le nom de chauffage par effet Joule.
-
Chauffage sans contact:
- Contrairement aux fours traditionnels, les fours à induction ne nécessitent pas de contact direct entre la source de chaleur (la bobine) et la charge métallique.La chaleur est générée à l'intérieur du métal lui-même, ce qui garantit un chauffage uniforme et réduit les risques de contamination.
- Cette méthode sans contact minimise également l'usure des composants du four, ce qui améliore la longévité et réduit les coûts de maintenance.
-
Conversion de fréquence:
- Les fours à induction fonctionnent à des fréquences moyennes (300 Hz à 1000 Hz), qui sont supérieures à la fréquence électrique standard de 50 Hz.Cela est possible grâce à un dispositif d'alimentation qui convertit le courant alternatif triphasé en courant continu, puis en courant alternatif réglable à moyenne fréquence.
- Des fréquences plus élevées augmentent l'efficacité du transfert d'énergie et permettent un chauffage plus rapide et mieux contrôlé, ce qui rend le procédé adapté à la fusion d'une large gamme de métaux.
-
Rôle de la bobine d'induction:
- La bobine d'induction, généralement en cuivre, est un élément essentiel du four.Elle transporte le courant alternatif et génère le champ magnétique nécessaire au chauffage par induction.
- La bobine est refroidie par une circulation d'eau afin d'éviter toute surchauffe et de garantir des performances constantes pendant le fonctionnement.
-
Mécanismes de production de chaleur:
- Courants de Foucault:La principale source de chaleur dans un four à induction est constituée par les courants de Foucault induits dans le métal.Ces courants circulent en réponse au champ magnétique changeant et génèrent de la chaleur en raison de la résistance du métal.
- Hystérésis magnétique:Dans les matériaux ferromagnétiques comme le fer, une chaleur supplémentaire est produite par l'hystérésis magnétique.Cela se produit parce que les domaines magnétiques à l'intérieur du matériau se réalignent continuellement avec le champ magnétique alternatif, dissipant l'énergie sous forme de chaleur.
-
Creuset et charge métallique:
- La charge métallique est placée dans un creuset non conducteur, généralement constitué de matériaux tels que le graphite ou la céramique, qui peuvent supporter des températures élevées sans interférer avec le processus d'induction.
- Le creuset maintient fermement le métal et veille à ce que la chaleur générée soit concentrée à l'intérieur de la charge, ce qui favorise une fusion efficace.
-
Contrôle de la température et précision:
- Les fours à induction offrent un contrôle précis de la température, ce qui permet aux opérateurs d'atteindre le point de fusion exact requis pour des métaux spécifiques.Cette précision est cruciale pour les applications dans des industries telles que l'aérospatiale, l'automobile et l'électronique, où les propriétés des matériaux doivent répondre à des normes strictes.
- La possibilité d'ajuster rapidement la fréquence et la puissance absorbée permet des cycles de chauffage et de refroidissement rapides, ce qui améliore la productivité et l'efficacité énergétique.
-
Applications et avantages:
- Les fours à induction sont largement utilisés pour le moulage des métaux, la production d'alliages et le recyclage en raison de leur efficacité, de leur propreté et de leur capacité à traiter une grande variété de métaux.
- Parmi les avantages, citons une consommation d'énergie réduite, une oxydation minimale du métal et la possibilité de fonctionner dans des atmosphères contrôlées afin d'éviter toute contamination.
-
Sécurité et entretien:
- La conception des fours à induction donne la priorité à la sécurité, avec des caractéristiques telles que des bobines refroidies à l'eau et des contrôles automatisés pour éviter la surchauffe et les risques électriques.
- Les besoins en maintenance sont relativement faibles, car la méthode de chauffage sans contact réduit l'usure des composants.Toutefois, des inspections régulières de la bobine, du creuset et des systèmes de refroidissement sont essentielles pour garantir des performances optimales.
En comprenant ces points clés, un acheteur peut évaluer l'adéquation d'un four à induction à ses besoins spécifiques, en tenant compte de facteurs tels que le type de matériau, le volume de production et l'efficacité énergétique.
Tableau récapitulatif :
Caractéristique principale | Description |
---|---|
Induction électromagnétique | Génère de la chaleur grâce aux courants de Foucault et à l'hystérésis magnétique dans la charge métallique. |
Chauffage sans contact | Pas de contact direct entre la source de chaleur et le métal, ce qui réduit les risques de contamination. |
Fréquences moyennes | Fonctionne entre 300 Hz et 1000 Hz pour un transfert d'énergie optimisé et un chauffage plus rapide. |
Contrôle de la température | Contrôle précis pour la fusion de métaux tels que l'acier jusqu'à 1370°C (2500°F). |
Applications | Utilisé pour le moulage des métaux, la production d'alliages et le recyclage. |
Avantages | Efficacité énergétique, oxydation minimale et faible entretien. |
Prêt à améliorer votre processus de fusion des métaux ? Contactez nos experts dès aujourd'hui pour trouver le four à induction idéal pour vos besoins !