La coulée sous vide est un processus de fabrication utilisé pour créer des pièces détaillées de haute qualité en versant un matériau liquide dans un moule sous vide. Ce processus est particulièrement utile pour produire de petits lots de pièces aux designs complexes, car il minimise les bulles d’air et garantit un niveau de détail élevé. Le processus de coulée sous vide implique généralement plusieurs étapes clés, notamment la préparation du moule, le mélange des matériaux, l'application sous vide, le coulage, le durcissement et le démoulage. Chaque étape doit être soigneusement contrôlée pour obtenir les résultats souhaités. Ci-dessous, nous décomposons le processus en étapes détaillées et expliquons les aspects critiques de chaque étape.
Points clés expliqués :
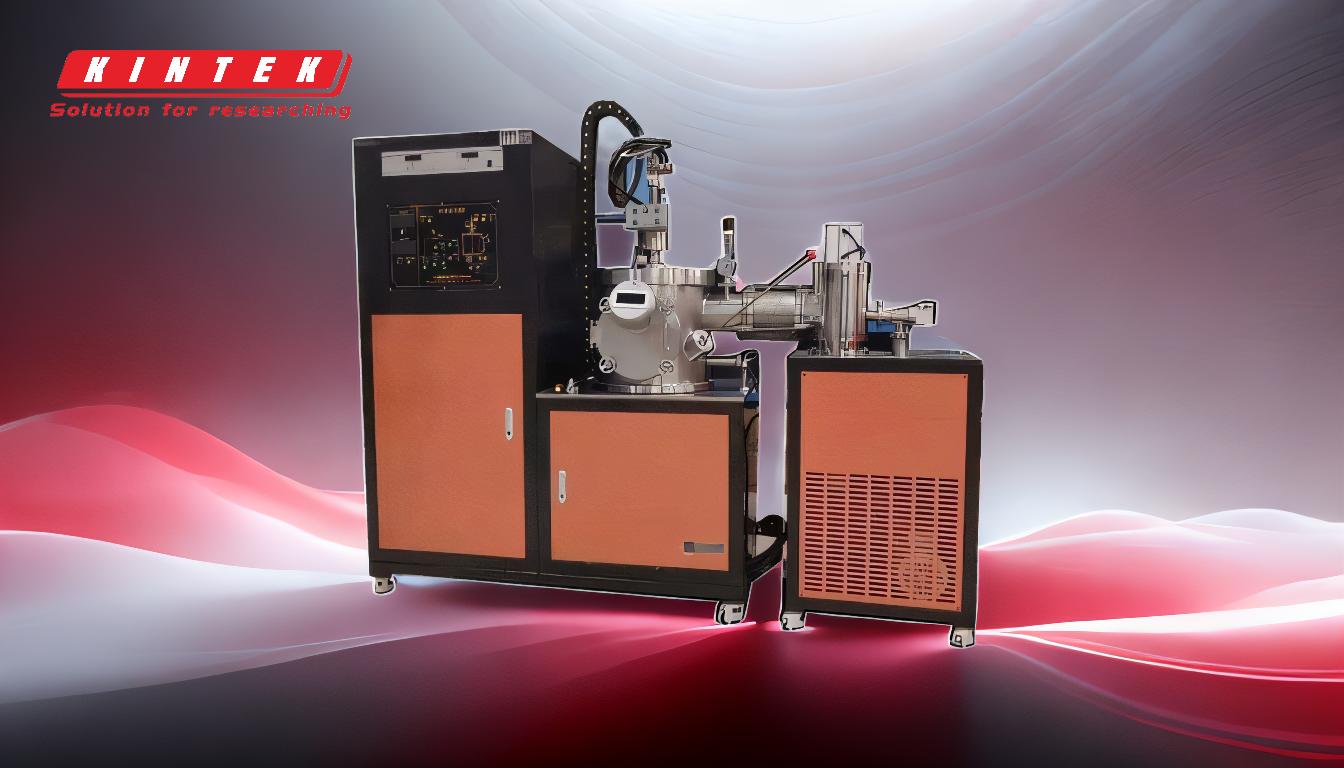
-
Préparation du moule:
- La première étape de la coulée sous vide consiste à préparer le moule. Cela implique de créer un modèle maître, généralement par impression 3D ou par usinage CNC, qui est ensuite utilisé pour fabriquer un moule en silicone.
- Le moule en silicone est créé en versant du silicone liquide autour du maître-modèle et en le laissant durcir. Une fois durci, le moule est découpé pour retirer le maître-modèle, laissant une cavité qui correspond à la forme de la pièce souhaitée.
- Le moule doit être nettoyé et inspecté pour détecter tout défaut avant utilisation afin de garantir la qualité de la pièce finale.
-
Mélange de matériaux:
- Le matériau utilisé pour la coulée sous vide est généralement une résine polyuréthane en deux parties. La résine et le durcisseur sont mélangés dans des proportions précises pour garantir un durcissement et des propriétés du matériau appropriés.
- Le mélange se fait sous vide pour éliminer les bulles d'air de la résine, qui pourraient autrement conduire à des défauts dans la pièce finale.
- La résine mélangée est ensuite dégazée davantage dans la chambre à vide pour garantir qu'elle est exempte d'air emprisonné.
-
Application sous vide:
- Le moule est placé dans une chambre à vide et la chambre est scellée. Une pompe à vide est utilisée pour éliminer l'air de la chambre, créant ainsi un environnement à basse pression.
- Le vide aide à aspirer la résine liquide dans les cavités du moule, garantissant ainsi que même les détails les plus complexes sont complètement remplis.
- Le vide aide également à éliminer les bulles d’air restantes dans la résine, ce qui donne une surface lisse et sans défauts.
-
Verser et durcir:
- Une fois le vide appliqué, la résine dégazée est coulée dans le moule. Le vide garantit que la résine s'écoule uniformément et remplit toutes les parties du moule.
- Après avoir coulé, le moule est laissé durcir. Les temps de durcissement varient en fonction de la résine utilisée et de la taille de la pièce. Certaines résines nécessitent de la chaleur pour durcir, tandis que d'autres durcissent à température ambiante.
- Lors du durcissement, la résine se solidifie et prend la forme du moule. Il est important de surveiller le processus de durcissement pour garantir que la pièce atteint les propriétés mécaniques souhaitées.
-
Démoulage et finition:
- Une fois la résine complètement durcie, le moule est ouvert et la pièce est soigneusement retirée. Le démoulage doit se faire en douceur pour éviter d'abîmer la pièce ou le moule.
- La pièce peut nécessiter un post-traitement, tel que la coupe du matériau en excès, le ponçage ou la peinture, pour obtenir l'apparence et la fonctionnalité finales souhaitées.
- Le moule en silicone peut souvent être réutilisé plusieurs fois, ce qui fait du moulage sous vide une méthode rentable pour la production en petites séries.
-
Considérations relatives à l'équipement et à la sécurité:
- La coulée sous vide nécessite un équipement spécialisé, notamment une chambre à vide, une pompe à vide et des outils de mélange. Un bon entretien de cet équipement est essentiel pour garantir des résultats cohérents.
- Des précautions de sécurité doivent être prises lorsque vous travaillez avec des résines et des équipements sous vide. Cela inclut le port d'un équipement de protection, une ventilation adéquate et le respect des directives du fabricant en matière de manipulation des matériaux.
-
Avantages de la coulée sous vide:
- Haut niveau de détail et de finition de surface.
- Capacité à produire de petits lots de pièces de manière rentable.
- Polyvalence dans le choix des matériaux, avec une large gamme de résines disponibles pour imiter différentes propriétés (par exemple, matériaux de type ABS, caoutchouc ou transparents).
- Les moules réutilisables réduisent les coûts de production globaux pour les petites séries.
-
Limites de la coulée sous vide:
- Ne convient pas à une production à grande échelle en raison du temps long du processus.
- Limité par la durabilité des moules en silicone, qui peuvent se dégrader après plusieurs utilisations.
- Les propriétés matérielles des pièces moulées peuvent ne pas correspondre à celles des pièces moulées par injection, en fonction de la résine utilisée.
En suivant ces étapes et considérations, la coulée sous vide peut être une méthode très efficace pour produire des pièces détaillées et de haute qualité. Le processus nécessite une attention particulière aux détails et un équipement approprié, mais les résultats en valent souvent la peine, en particulier pour le prototypage ou la fabrication en petits lots.
Tableau récapitulatif :
Étape | Détails clés |
---|---|
Préparation du moule | Créez un maître modèle (impression 3D/CNC), réalisez un moule en silicone, nettoyez et inspectez. |
Mélange de matériaux | Mélanger sous vide la résine polyuréthane bi-composante pour éliminer les bulles d'air. |
Application sous vide | Placez le moule dans une chambre à vide pour garantir que la résine remplisse les détails complexes. |
Verser et durcir | Versez la résine dans le moule, durcissez dans des conditions contrôlées pour des résultats optimaux. |
Démoulage/Finition | Retirer la pièce délicatement, effectuer un post-traitement (découpage, ponçage, peinture). |
Avantages | Détails élevés, petits lots rentables, matériaux polyvalents, moules réutilisables. |
Limites | Pas pour la production à grande échelle, la durabilité des moules, les limitations des propriétés des matériaux. |
Prêt à produire des pièces de haute qualité avec la coulée sous vide ? Contactez nos experts dès aujourd'hui pour commencer !