Les fours à arc électrique (FÉA) sont largement utilisés dans la production de métaux en raison de leur efficacité et de leur flexibilité. Cependant, ils présentent plusieurs inconvénients qui peuvent avoir un impact sur l'efficacité opérationnelle, le coût et la qualité du produit. Il s'agit notamment de la forte consommation d'énergie, qui met à rude épreuve les systèmes électriques, et des défis spécifiques liés aux fours à arc à électrode non autoconsommatrice, tels que les risques de contamination, les difficultés opérationnelles et les limitations dans le contrôle de la composition des alliages. En outre, les FÉA sont souvent limités à la production à petite échelle, ce qui les rend moins viables économiquement pour les opérations à grande échelle, à moins que les coûts de l'électricité ne soient exceptionnellement bas.
Explication des points clés :
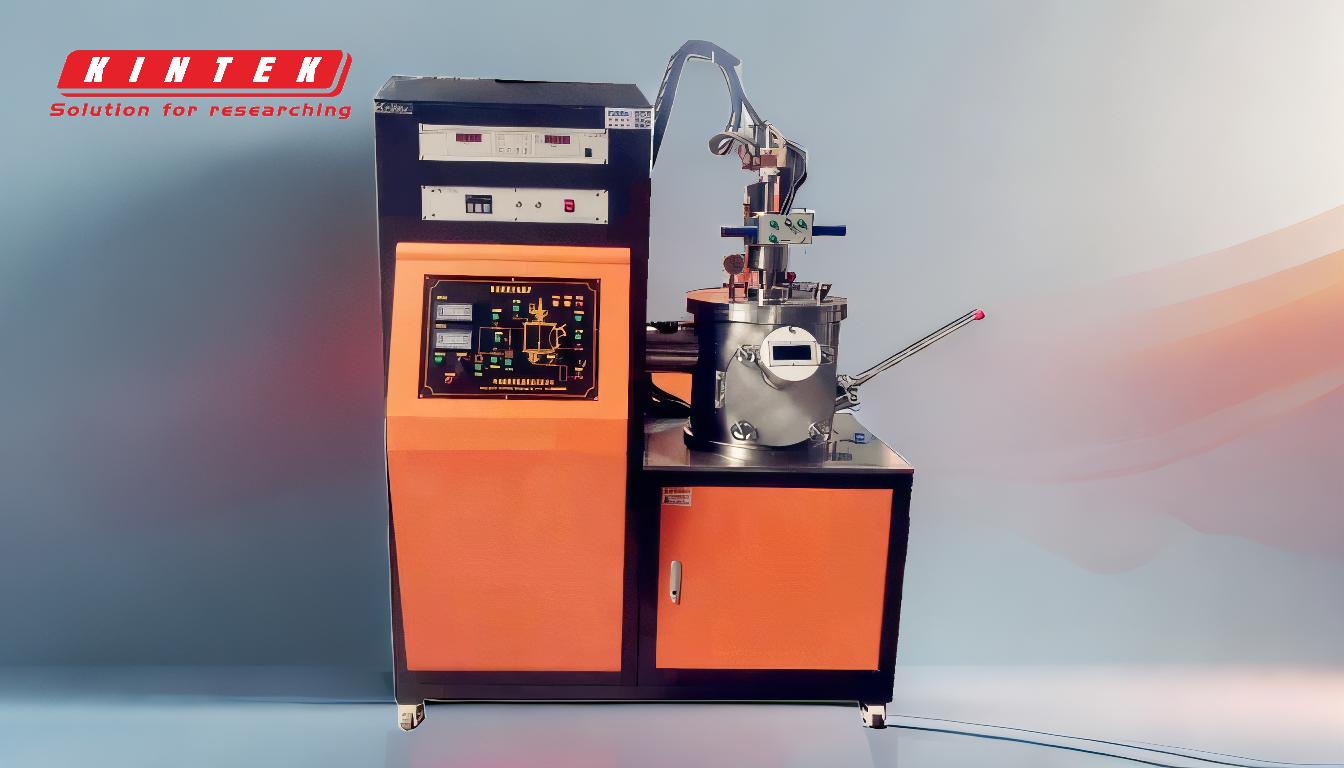
-
Consommation électrique élevée
- Les fours à arc électrique nécessitent une quantité importante d'énergie électrique pour générer la chaleur nécessaire à la fusion des métaux. Cette forte demande d'énergie peut mettre à rude épreuve les réseaux électriques locaux, en particulier dans les régions où l'infrastructure électrique est limitée.
- La dépendance à l'égard de l'électricité rend les aciéries électriques vulnérables aux fluctuations de l'alimentation électrique, qui peuvent perturber la production et augmenter les coûts d'exploitation.
- Pour les industries opérant dans des régions où le coût de l'électricité est élevé, la consommation d'énergie des fours à arc électrique peut avoir un impact significatif sur la rentabilité globale.
-
Risques de contamination dans les fours à arc à électrodes non autoconsommateurs
- Dans les fours à arc à électrode non autoconsommatrice, le métal en fusion risque d'être contaminé par le matériau de l'électrode. Bien que cette contamination soit généralement localisée et rare, elle peut compromettre la qualité du produit final.
- La contamination est particulièrement problématique dans les industries nécessitant des métaux de haute pureté, telles que l'aérospatiale ou l'électronique, où même des impuretés mineures peuvent entraîner la défaillance d'un produit.
-
Défis opérationnels dans les fours à arc à électrode non autoconsommateurs
- Les fours à arc sans autoconsommation sous vide souffrent souvent d'une mauvaise stabilité de l'arc, ce qui rend leur fonctionnement difficile. Cette instabilité peut entraîner un chauffage et une fusion irréguliers, ce qui affecte la qualité du métal produit.
- Le procédé nécessite la formation d'un bain de fusion avant le dégazage, ce qui ajoute de la complexité et du temps au processus de production.
- Ces défis opérationnels peuvent augmenter les coûts de main-d'œuvre et réduire l'efficacité globale.
-
Limites de l'échelle de production
- Les fours à arc à électrode non autoconsommatrice sont généralement limités à la production à petite échelle, avec des quantités d'alliage de fusion unique allant de quelques dizaines à quelques centaines de grammes. Ils ne conviennent donc pas aux applications industrielles à grande échelle.
- La faible capacité de production limite également leur viabilité économique, car le coût par unité de métal produite peut être sensiblement plus élevé que celui des alternatives à plus grande échelle.
-
Difficulté à contrôler la composition des alliages
- Le contrôle de la proportion des composants d'alliage dans les fours à arc à électrode non autoconsommatrice est un défi. La méthode de chargement des matériaux peut entraîner des incohérences dans la composition des alliages, ce qui affecte les propriétés du produit final.
- Ce manque de précision est un inconvénient important dans les industries où la composition spécifique des alliages est critique, comme dans la production d'alliages à haute performance pour des applications spécialisées.
-
Problèmes de viabilité économique
- Les fours à arc électrique, en particulier ceux qui utilisent des torches à plasma ou des électrodes non autoconsommatrices, sont souvent limités à quelques tonnes de crasse ou de métal à la fois. Cette opération à petite échelle n'est pas économiquement viable, à moins que l'énergie électrique ne soit exceptionnellement bon marché.
- Pour les opérations à plus grande échelle, d'autres méthodes telles que les hauts fourneaux ou les fours à induction peuvent être plus rentables, en particulier dans les régions où le coût de l'électricité est élevé.
En résumé, si les fours à arc électrique présentent plusieurs avantages, notamment en termes de flexibilité et d'efficacité, leurs inconvénients - tels que la consommation d'énergie élevée, les risques de contamination, les défis opérationnels et les limites de l'échelle de production et du contrôle des alliages - doivent être soigneusement pris en compte. Ces facteurs peuvent avoir un impact à la fois sur la qualité du produit final et sur la rentabilité globale de l'utilisation des fours à arc électrique dans les applications industrielles.
Tableau récapitulatif :
Inconvénient | Impact clé |
---|---|
Consommation électrique élevée | Sollicite les systèmes électriques, augmente les coûts d'exploitation et réduit la rentabilité. |
Risques de contamination | Compromet la qualité des produits, en particulier dans les industries des métaux de haute pureté. |
Défis opérationnels | Mauvaise stabilité de l'arc, chauffage irrégulier et augmentation des coûts de main-d'œuvre. |
Limites de l'échelle de production | Limité à la production à petite échelle, ce qui réduit la viabilité économique. |
Difficulté à contrôler la composition des alliages | Proportions d'alliages incohérentes, affectant les propriétés du produit final. |
Problèmes de viabilité économique | Les opérations à petite échelle sont moins rentables si l'électricité n'est pas bon marché. |
Besoin d'aide pour choisir le bon four pour votre production de métal ? Contactez nos experts dès aujourd'hui pour des solutions sur mesure !