Bien qu'il s'agisse d'un procédé de fabrication polyvalent et largement utilisé, la coulée sous vide présente plusieurs limites qui peuvent avoir une incidence sur son efficacité, son coût et la qualité du produit final. Ces limites découlent des propriétés des matériaux, des contraintes du processus et des défis opérationnels. Les principaux problèmes sont le retrait et la porosité des pièces moulées, le coût élevé et l'usure des matériaux de moulage, les processus de refroidissement fastidieux, la difficulté à maintenir des tolérances dimensionnelles strictes et l'inefficacité des fours. L'ensemble de ces facteurs peut affecter les propriétés mécaniques, la fiabilité et la viabilité économique des pièces moulées sous vide.
Explication des points clés :
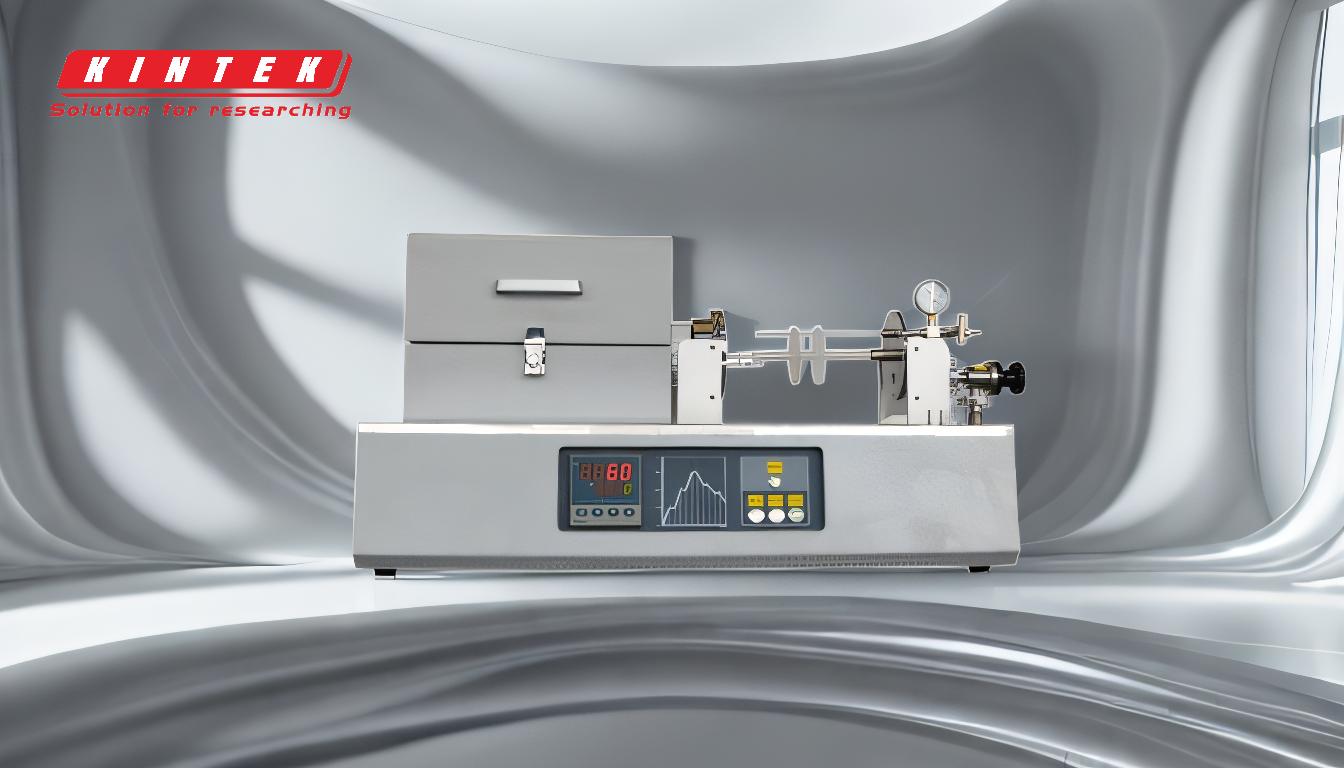
-
Retrait et porosité des pièces moulées:
- Explication: Lors de la solidification du métal dans la coulée sous vide, le retrait est une propriété inhérente qui peut conduire à des défauts tels que le retrait résiduel ou la porosité gazeuse. Ces défauts peuvent compromettre les propriétés mécaniques des pièces moulées, en particulier leur résistance aux chocs et leurs propriétés de fatigue.
- Impact: Cette limitation est critique dans les applications où une fiabilité et des performances élevées sont requises, comme dans les composants aérospatiaux. La présence de porosité peut également nécessiter des mesures supplémentaires de contrôle de la qualité et un post-traitement pour garantir l'intégrité des pièces moulées.
-
Défis liés aux matériaux de moulage:
- Explication: La méthode de pressage à chaud sous vide, une technique courante dans la coulée sous vide, implique souvent des températures élevées et des environnements réactifs qui peuvent dégrader les matériaux des moules. Cela entraîne des pertes importantes de moules et nécessite l'utilisation de matériaux de haute qualité, souvent coûteux, capables de résister à ces conditions difficiles.
- Impact: La nécessité de disposer de matériaux de moulage durables augmente le coût global du processus de moulage. En outre, l'usure des moules peut conduire à des remplacements plus fréquents, ce qui augmente encore les coûts et peut entraîner des retards de production.
-
Un processus de refroidissement qui prend beaucoup de temps:
- Explication: Le processus de refroidissement dans la coulée sous vide est intrinsèquement lent afin de garantir que le métal se solidifie uniformément et de minimiser les défauts. Ce refroidissement lent peut constituer un goulot d'étranglement dans le processus de fabrication, en particulier lorsque des cycles de production rapides sont nécessaires.
- Impact: Les temps de refroidissement prolongés peuvent entraîner des délais d'exécution plus longs et une réduction du rendement, ce qui affecte l'efficacité et la rentabilité globales du processus de fabrication.
-
Difficulté à maintenir des tolérances dimensionnelles serrées:
- Explication: Obtenir des tolérances dimensionnelles précises dans la coulée sous vide peut s'avérer difficile en raison de la nature du processus de coulée et du comportement des matériaux pendant la solidification. Les variations des vitesses de refroidissement et des propriétés des matériaux peuvent conduire à des écarts par rapport aux dimensions souhaitées.
- Impact: Cette limitation peut nécessiter des processus d'usinage ou de finition supplémentaires pour atteindre les spécifications requises, ce qui augmente le coût et la complexité de la production. Elle est particulièrement problématique dans les industries où la précision est primordiale, comme les appareils médicaux ou la mécanique de précision.
-
Inefficacités dans le fonctionnement du four:
- Explication: Les fours de coulée sous vide modernes nécessitent souvent un basculement et des changements de moules fréquents, ce qui peut entraîner un gaspillage de matériaux et une augmentation du temps de fabrication. Ces inefficacités opérationnelles peuvent constituer un inconvénient important dans les environnements de production en grande quantité.
- Impact: La nécessité de basculer et de changer continuellement de moule ralentit non seulement le processus de production, mais augmente également le risque d'erreurs et d'incohérences. Cela peut entraîner des taux de rebut plus élevés et une réduction de la productivité globale.
En résumé, si le moulage sous vide offre de nombreux avantages, notamment la possibilité de produire des formes complexes et des surfaces de haute qualité, il n'est pas sans limites. Ces limites - qui vont du retrait des matériaux et de l'usure des moules à l'inefficacité opérationnelle - doivent être gérées avec soin pour garantir la viabilité économique et fonctionnelle du processus de moulage. Les fabricants doivent évaluer ces facteurs par rapport aux exigences spécifiques de leurs applications afin de déterminer si le moulage sous vide est adapté à leurs besoins.
Tableau récapitulatif :
Limitation | Explication | Impact |
---|---|---|
Rétrécissement et porosité | Le retrait inhérent à la solidification provoque des défauts tels que la porosité. | Compromet les propriétés mécaniques, nécessite un contrôle de qualité supplémentaire et un post-traitement. |
Coût élevé et usure des matériaux de moulage | Les températures élevées dégradent les moules, ce qui nécessite des matériaux coûteux et durables. | Augmente les coûts et les retards de production en raison du remplacement fréquent des moules. |
Un processus de refroidissement qui prend beaucoup de temps | Un refroidissement lent garantit une solidification uniforme mais retarde la production. | Réduit le débit et l'efficacité, ce qui entraîne des délais plus longs. |
Difficultés liées aux tolérances dimensionnelles | Les variations des vitesses de refroidissement et des propriétés des matériaux affectent la précision. | Nécessite un usinage supplémentaire, ce qui augmente les coûts et la complexité. |
Inefficacités dans le fonctionnement du four | Les basculements et les changements de moules fréquents entraînent des pertes de matériaux et des retards de production. | Ralentit la production, augmente les taux de rebut et réduit la productivité globale. |
Besoin d'aide pour optimiser votre processus de coulée sous vide ? Contactez nos experts dès aujourd'hui pour trouver des solutions adaptées à vos besoins !