La fusion de l'aluminium nécessite des fours capables de traiter son point de fusion relativement bas (660°C ou 1220°F) tout en garantissant l'efficacité, le contrôle de la température et une contamination minimale.Les fours les plus couramment utilisés pour la fusion de l'aluminium sont les fours à creuset, les fours à induction et les fours à réverbère.Chaque type présente des avantages uniques en fonction de l'échelle d'exploitation, des exigences en matière d'efficacité énergétique et de la pureté souhaitée de l'aluminium fondu.Les fours à creuset, souvent alimentés au gaz ou au pétrole, sont populaires pour les opérations à petite et moyenne échelle en raison de leur simplicité et de leur rentabilité.Les fours à induction sont préférés pour leur précision et leur efficacité énergétique, tandis que les fours à réverbère conviennent aux applications industrielles à grande échelle.Le choix du four dépend de facteurs tels que le volume de production, la disponibilité de la source d'énergie et les exigences spécifiques de l'application.
Explication des points clés :
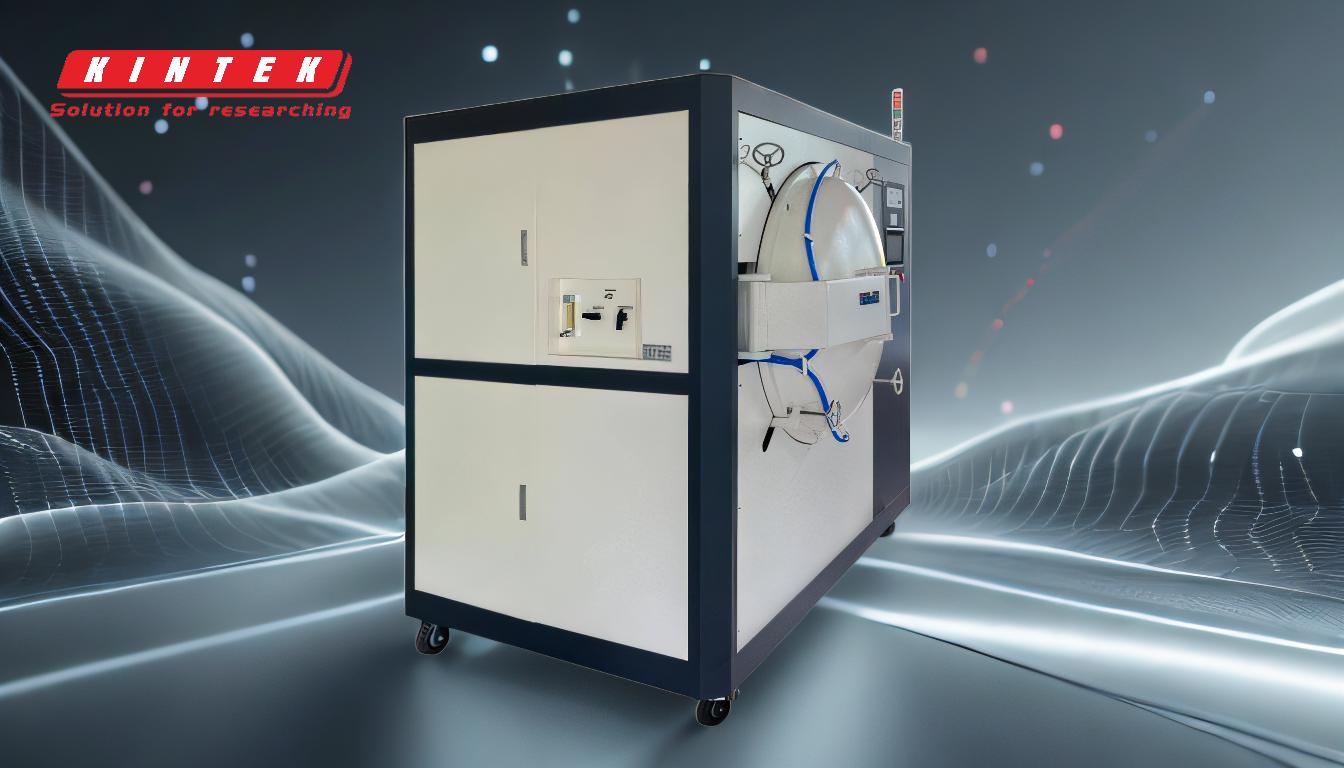
-
Fours à creuset pour la fusion de l'aluminium
- Les fours à creuset sont largement utilisés pour la fusion de l'aluminium, en particulier dans les petites et moyennes entreprises.
- Ces fours utilisent du gaz ou du pétrole comme combustible, ce qui les rend rentables et faciles à utiliser.
- L'aluminium est placé dans un creuset, qui est chauffé directement ou indirectement, assurant une fusion contrôlée avec une contamination minimale.
- Les fours à creuset basculant sont particulièrement utiles pour verser l'aluminium en fusion dans les moules, car ils permettent un contrôle précis du processus de coulée.
-
Fours à induction pour la précision et l'efficacité
- Les fours à induction sont très efficaces et utilisent l'induction électromagnétique pour générer de la chaleur directement dans l'aluminium, réduisant ainsi les pertes d'énergie.
- Ils sont idéaux pour les applications nécessitant une grande pureté et un contrôle précis de la température, comme dans l'aérospatiale ou l'industrie automobile.
- Les fours à induction peuvent faire fondre l'aluminium rapidement et conviennent aussi bien aux petites qu'aux grandes entreprises.
- Leur capacité à fonctionner sans contact direct avec les flammes minimise la contamination, ce qui en fait un choix privilégié pour la production d'aluminium de haute qualité.
-
Fours à réverbère pour les opérations à grande échelle
- Les fours à réverbère sont couramment utilisés dans les grandes installations industrielles pour fondre l'aluminium.
- Ces fours utilisent une flamme pour chauffer indirectement l'aluminium, la chaleur se reflétant sur les parois du four pour faire fondre le métal.
- Ils sont capables de traiter de grands volumes d'aluminium, ce qui les rend adaptés aux fonderies et aux installations de recyclage.
- Cependant, ils peuvent nécessiter plus d'énergie que les fours à induction et peuvent être moins efficaces pour les petites entreprises.
-
Avantages des fours à induction par rapport aux méthodes traditionnelles
- Les fours à induction sont plus puissants et plus économes en énergie que les fours traditionnels, car ils génèrent de la chaleur directement à l'intérieur du métal.
- Ils offrent des temps de fusion plus rapides et une meilleure uniformité de la température, ce qui est essentiel pour maintenir la qualité de l'aluminium.
- L'absence de contact direct avec la flamme réduit l'oxydation et la contamination, ce qui garantit une plus grande pureté de l'aluminium fondu.
-
Éléments à prendre en compte pour choisir le bon four
- Volume de production:Pour les opérations à petite échelle, les fours à creuset sont rentables, tandis que les fours à réverbère sont mieux adaptés à la production à grande échelle.
- Efficacité énergétique:Les fours à induction constituent l'option la plus efficace sur le plan énergétique, ce qui les rend idéaux pour les applications de haute précision.
- Contrôle de la contamination:Les fours à induction et à moufle offrent un meilleur contrôle de la contamination, ce qui est essentiel pour l'aluminium de haute pureté.
- Coût et maintenance:Les fours à creuset sont généralement moins chers à installer et à entretenir, tandis que les fours à induction peuvent avoir des coûts initiaux plus élevés mais des dépenses opérationnelles plus faibles.
-
Fours spécialisés pour les applications de haute pureté
- Pour les applications nécessitant une pureté extrêmement élevée, comme dans l'électronique ou l'aérospatiale, il est possible d'utiliser des fours spécialisés tels que les fours à vide ou à moufle.
- Ces fours empêchent le contact direct avec les flammes et réduisent la contamination, garantissant ainsi que l'aluminium répond à des normes de qualité rigoureuses.
En résumé, le choix d'un four pour la fusion de l'aluminium dépend des exigences spécifiques de l'opération, notamment du volume de production, de l'efficacité énergétique et du contrôle de la contamination.Les fours à creuset sont idéaux pour les opérations à petite échelle, les fours à induction offrent précision et efficacité, et les fours à réverbère conviennent aux applications industrielles à grande échelle.Il est essentiel de comprendre les points forts et les limites de chaque type de four pour choisir l'équipement adéquat pour la fusion de l'aluminium.
Tableau récapitulatif :
Type de four | Meilleur pour | Caractéristiques principales |
---|---|---|
Fours à creuset | Opérations à petite et moyenne échelle | Rentable, facile à utiliser, contamination minimale, contrôle précis de la coulée |
Fours à induction | Applications de haute pureté | Efficacité énergétique, fusion rapide, contrôle précis de la température, contamination minimale |
Fours à réverbère | Utilisation industrielle à grande échelle | Traitement de grands volumes, chauffage indirect, adapté aux fonderies et au recyclage |
Besoin d'aide pour choisir le bon four pour la fusion de l'aluminium ? Contactez nos experts dès aujourd'hui pour des conseils personnalisés !