Un four de calcination est un type spécialisé de four rotatif utilisé principalement pour le processus de calcination, qui consiste à chauffer des matériaux à des températures élevées afin d'induire une dissociation chimique ou d'éliminer l'humidité liée.Il est largement utilisé dans des industries telles que la production de ciment, la métallurgie et le traitement chimique.Le four à calciner fonctionne en exposant les matériaux à des températures élevées contrôlées, ce qui garantit que les réactions chimiques souhaitées se produisent efficacement.Sa conception comprend des composants clés tels que la coque du four, le revêtement réfractaire, les pneus de support et l'engrenage d'entraînement, qui travaillent ensemble pour faciliter le mouvement des matériaux, le transfert de chaleur et la combustion.Les options de personnalisation permettent au four de répondre à des exigences industrielles spécifiques, bien que cela augmente souvent les coûts.
Explication des points clés :
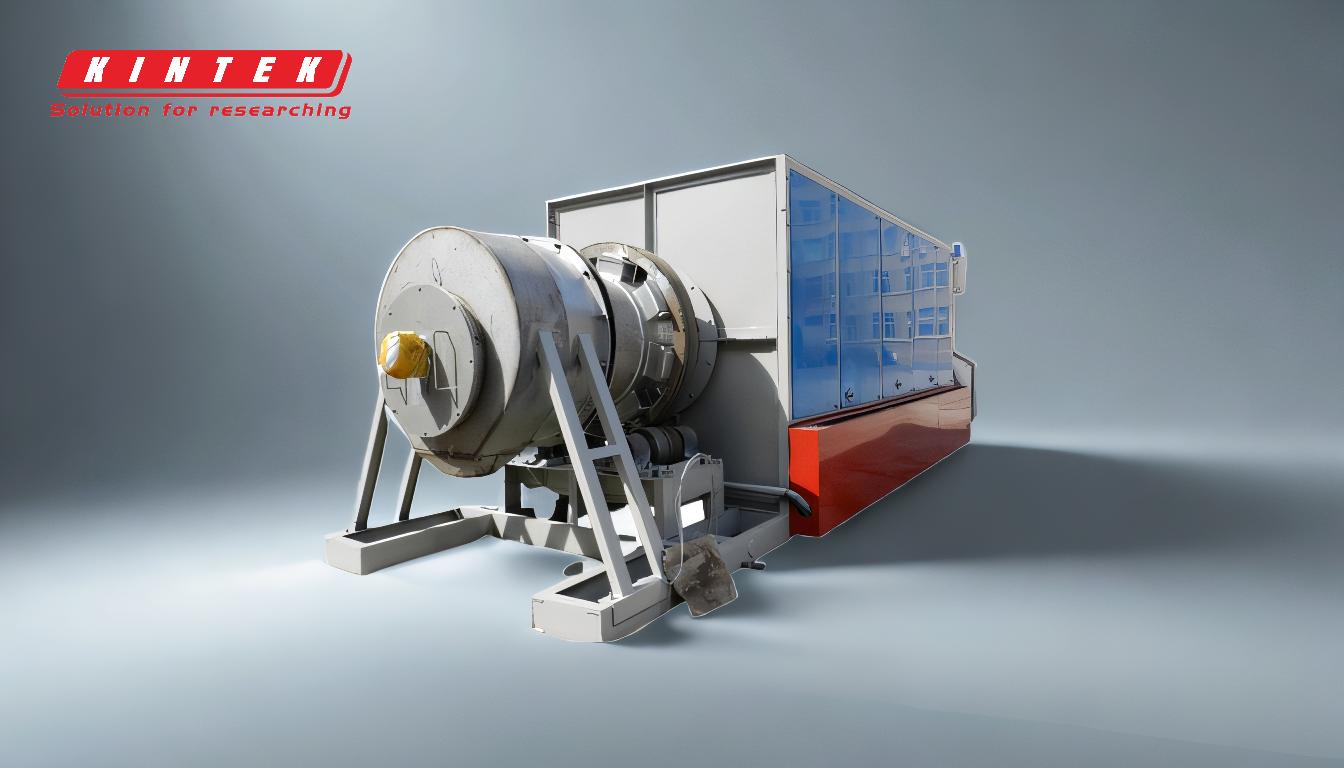
-
Définition et objectif d'un four à calciner:
- Un four de calcination est un four rotatif spécialement conçu pour la calcination, un processus thermique qui chauffe les matériaux à des températures élevées pour obtenir une dissociation chimique ou éliminer l'humidité.
- Les applications courantes comprennent la dissociation du carbonate de calcium (CaCO₃) en oxyde de calcium (CaO) et en dioxyde de carbone (CO₂) dans la production de ciment, ainsi que l'élimination de l'humidité liée à des matériaux tels que le borax.
-
Principaux éléments d'un four à calciner:
- Coquille de four:La structure extérieure qui abrite les composants internes et résiste aux températures élevées.
- Revêtement réfractaire:Un revêtement résistant à la chaleur à l'intérieur de la coque du four qui la protège des températures extrêmes et des réactions chimiques.
- Pneus de support (anneaux de roulement) et rouleaux:Ces composants supportent le poids du four et lui permettent de tourner en douceur.
- Entraînement:Alimente la rotation du four, garantissant un mouvement régulier du matériau.
- Échangeurs de chaleur internes:Faciliter un transfert de chaleur efficace vers les matériaux traités.
-
Principe de fonctionnement:
- Le four de calcination fonctionne grâce à une combinaison de flux de gaz, de combustion de combustible, de transfert de chaleur et de mouvement de matière.
- Le combustible est brûlé pour générer de la chaleur, qui est transférée au matériau à l'intérieur du four.
- Au fur et à mesure que le four tourne, le matériau passe par différentes zones de température, subissant des modifications physiques et chimiques pour former le produit désiré.
-
Personnalisation et coûts:
- Les fours calcinateurs peuvent être personnalisés pour répondre à des besoins industriels spécifiques, tels que le traitement de matériaux uniques ou l'obtention de profils de température particuliers.
- La personnalisation implique souvent la modification de composants tels que la coque du four, le revêtement réfractaire ou les échangeurs de chaleur, ce qui peut entraîner une augmentation des coûts.
-
Applications dans l'industrie:
- Production de ciment:Les fours à calciner sont essentiels à la production de clinker, un ingrédient clé du ciment.
- Métallurgie:Utilisé pour le grillage des minerais et l'élimination des impuretés.
- Traitement chimique:Le four est utilisé pour la production de matériaux inorganiques et l'élimination de l'humidité des composés chimiques.
-
Avantages de l'utilisation d'un four à calciner:
- Transfert de chaleur efficace:La conception assure une distribution optimale de la chaleur, réduisant ainsi la consommation d'énergie.
- Polyvalence:Peut prendre en charge une large gamme de matériaux et de processus.
- Évolutivité:Convient aussi bien à une utilisation en laboratoire à petite échelle qu'à une production industrielle à grande échelle.
-
Comparaison avec d'autres types de fours:
- Contrairement aux fours rotatifs standard, les fours à calciner sont spécifiquement optimisés pour les réactions chimiques à haute température.
- Ils comportent souvent des caractéristiques supplémentaires telles que des échangeurs de chaleur avancés ou des revêtements réfractaires spécialisés pour améliorer les performances.
En comprenant la conception, les composants et les principes de fonctionnement d'un four à calciner, les industries peuvent utiliser efficacement cet équipement pour réaliser un traitement thermique précis et optimiser les résultats de la production.
Tableau récapitulatif :
Aspect | Détails |
---|---|
Définition | Four rotatif optimisé pour la calcination, le chauffage de matériaux pour induire des changements chimiques ou éliminer l'humidité. |
Composants clés | Coque du four, revêtement réfractaire, pneus de support, engrenage d'entraînement, échangeurs de chaleur internes. |
Principe de fonctionnement | Combine le flux de gaz, la combustion de carburant, le transfert de chaleur et le mouvement des matériaux pour un traitement thermique précis. |
Applications | Production de ciment, métallurgie, traitement chimique. |
Avantages | Transfert de chaleur efficace, polyvalence, évolutivité. |
Personnalisation | Des conceptions sur mesure pour des besoins industriels spécifiques, même si les coûts peuvent augmenter. |
Découvrez comment un four à calciner peut optimiser vos processus industriels. contactez nos experts dès aujourd'hui !