Une atmosphère inerte pour le recuit fait référence à un environnement contrôlé où les gaz réactifs comme l'oxygène sont remplacés par des gaz non réactifs (inertes) comme l'azote ou l'argon. Cet environnement empêche l'oxydation, la décarburation et la contamination de la surface du métal pendant le processus de recuit, ce qui garantit des résultats de haute qualité. Les atmosphères inertes sont particulièrement importantes pour le recuit des aciers inoxydables et des métaux non ferreux, car elles protègent le matériau des réactions chimiques qui pourraient compromettre ses propriétés. L'utilisation de gaz inertes de haute pureté (99,99 % par exemple) et de systèmes de contrôle précis dans les fours améliore encore l'efficacité du processus de recuit.
Explication des points clés :
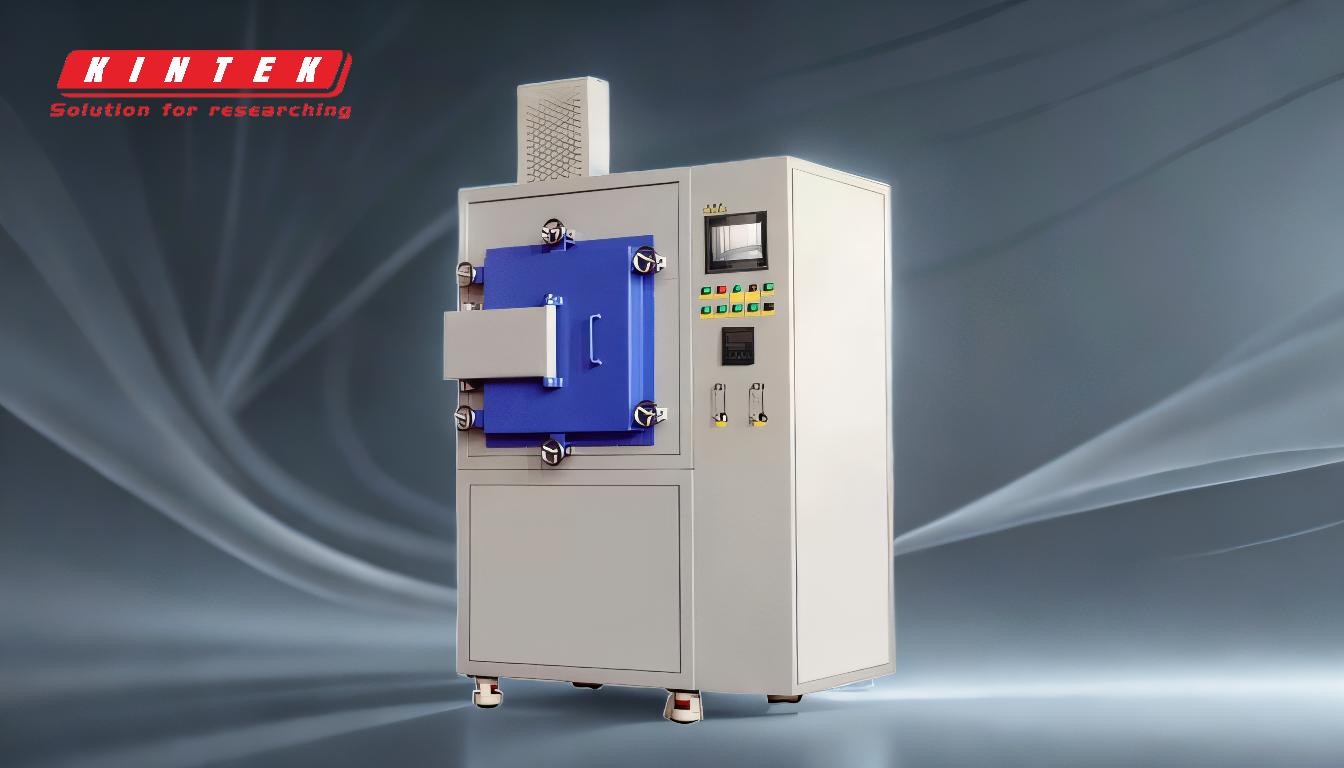
-
Définition d'une atmosphère inerte:
- Une atmosphère inerte est un environnement contrôlé dans lequel les gaz réactifs (par exemple l'oxygène) sont remplacés par des gaz non réactifs comme l'azote ou l'argon.
- Cet environnement est conçu pour éviter les réactions chimiques indésirables, telles que l'oxydation ou la décarburation, pendant les processus de traitement thermique comme le recuit.
-
Objectif de l'utilisation d'une atmosphère inerte pour le recuit:
- Prévention de l'oxydation: L'oxydation se produit lorsque les métaux réagissent avec l'oxygène, ce qui entraîne la formation de tartre à la surface. Une atmosphère inerte élimine l'oxygène, empêchant ainsi cette réaction.
- Éviter la décarburation: La décarburation est la perte de carbone à la surface de l'acier, ce qui peut affaiblir le matériau. Les gaz inertes empêchent ce phénomène en créant un environnement non réactif.
- Réduire la contamination: Les atmosphères inertes minimisent le risque de contamination par des impuretés, ce qui garantit que le métal conserve les propriétés souhaitées.
- Améliorer la reproductibilité: En maintenant un environnement cohérent, les atmosphères inertes garantissent des résultats de recuit fiables et reproductibles.
-
Types de gaz inertes utilisés:
- Azote: Le gaz inerte le plus couramment utilisé en raison de sa rentabilité et de sa nature non réactive avec l'acier. Il est largement disponible et offre une excellente protection contre l'oxydation.
- Argon: Un autre choix populaire, en particulier pour les applications nécessitant une plus grande pureté ou lorsque l'azote risque de réagir avec certains matériaux. L'argon est plus dense que l'azote, ce qui offre une meilleure protection dans certains cas.
- Hydrogène: Parfois utilisé en combinaison avec l'argon pour des applications spécifiques, telles que le recuit des aciers inoxydables, pour améliorer la propreté de la surface et réduire la formation d'oxyde.
-
Applications des atmosphères inertes dans le recuit:
- Aciers inoxydables: Les atmosphères inertes sont essentielles pour le recuit des aciers inoxydables afin d'éviter la formation d'oxyde de chrome, qui peut dégrader la résistance à la corrosion.
- Métaux non ferreux: Les métaux comme le cuivre, l'aluminium et le titane bénéficient d'atmosphères inertes pour éviter l'oxydation et maintenir la qualité de la surface.
- Traitements thermiques spécialisés: Les atmosphères inertes sont utilisées dans des processus tels que le collage, le durcissement et le traitement thermique afin de garantir un contrôle précis des propriétés des matériaux.
-
Équipements et systèmes de contrôle:
- Fours sous atmosphère de gaz inerte: Ces fours sont conçus avec des contrôles de température de précision basés sur des microprocesseurs et une isolation économe en énergie pour maintenir des conditions constantes.
- Gaz de haute pureté: Des gaz inertes d'une pureté supérieure à 99,99 % sont utilisés pour garantir une contamination minimale et des performances optimales.
- Contrôle de la pression: La pression du gaz inerte est généralement maintenue dans une plage spécifique (par exemple, 0,05 à 0,07 MPa) pour obtenir l'environnement protecteur souhaité.
-
Avantages de l'utilisation d'une atmosphère inerte:
- Amélioration de la qualité de la surface: Prévient la formation de tartre et maintient une surface propre et exempte d'oxyde.
- Propriétés améliorées des matériaux: Conserve la teneur en carbone et d'autres éléments essentiels, garantissant la résistance et la durabilité du matériau.
- Sécurité: Réduit les risques d'incendie et d'explosion en éliminant les gaz réactifs.
- Économies de coûts: Les fours à haut rendement énergétique et les systèmes de contrôle précis optimisent l'utilisation des ressources, réduisant ainsi les coûts d'exploitation.
-
Défis et considérations:
- Coût des gaz inertes: Les gaz de haute pureté comme l'argon peuvent être coûteux, ce qui a un impact sur le coût global du processus de recuit.
- Maintenance des équipements: Les fours à atmosphère de gaz inerte nécessitent un entretien régulier pour garantir des performances constantes et éviter les fuites.
- Compatibilité des matériaux: Tous les matériaux ne nécessitent pas une atmosphère inerte, il est donc essentiel d'évaluer les besoins spécifiques du matériau à recuire.
En comprenant ces points clés, les acheteurs d'équipements et de consommables peuvent prendre des décisions éclairées sur la mise en œuvre d'atmosphères inertes dans leurs processus de recuit, garantissant ainsi des résultats de haute qualité et des opérations rentables.
Tableau récapitulatif :
Aspect | Détails |
---|---|
Définition | Environnement contrôlé avec des gaz non réactifs (par exemple, azote, argon). |
Objectif | Prévient l'oxydation, la décarburation, la contamination et assure la reproductibilité. |
Gaz inertes utilisés | Azote (rentable), Argon (haute pureté), Hydrogène (spécialisé). |
Applications | Aciers inoxydables, métaux non ferreux, traitements thermiques spécialisés. |
Equipement | Fours à gaz inerte avec commandes de précision et gaz de haute pureté. |
Avantages | Amélioration de la qualité de la surface, des propriétés des matériaux, de la sécurité et des économies. |
Défis | Coût des gaz inertes, maintenance des équipements, compatibilité des matériaux. |
Besoin d'aide pour mettre en place une atmosphère inerte pour le recuit ? Contactez nos experts dès aujourd'hui pour des solutions sur mesure !