Les matériaux de revêtement de base sont des matériaux réfractaires utilisés dans des applications industrielles à haute température, telles que les fours, les étuves et les réacteurs, pour assurer l'isolation thermique, résister à la corrosion et aux chocs thermiques.Ces matériaux sont généralement composés d'éléments alcalins tels que la magnésie (MgO) ou la dolomie (CaO-MgO), qui offrent une excellente résistance aux scories basiques et aux environnements à haute température.Ils sont conçus pour assurer la durabilité, la facilité d'installation et d'entretien tout en minimisant les pertes de chaleur et en protégeant l'intégrité structurelle de l'équipement.
Explication des points clés :
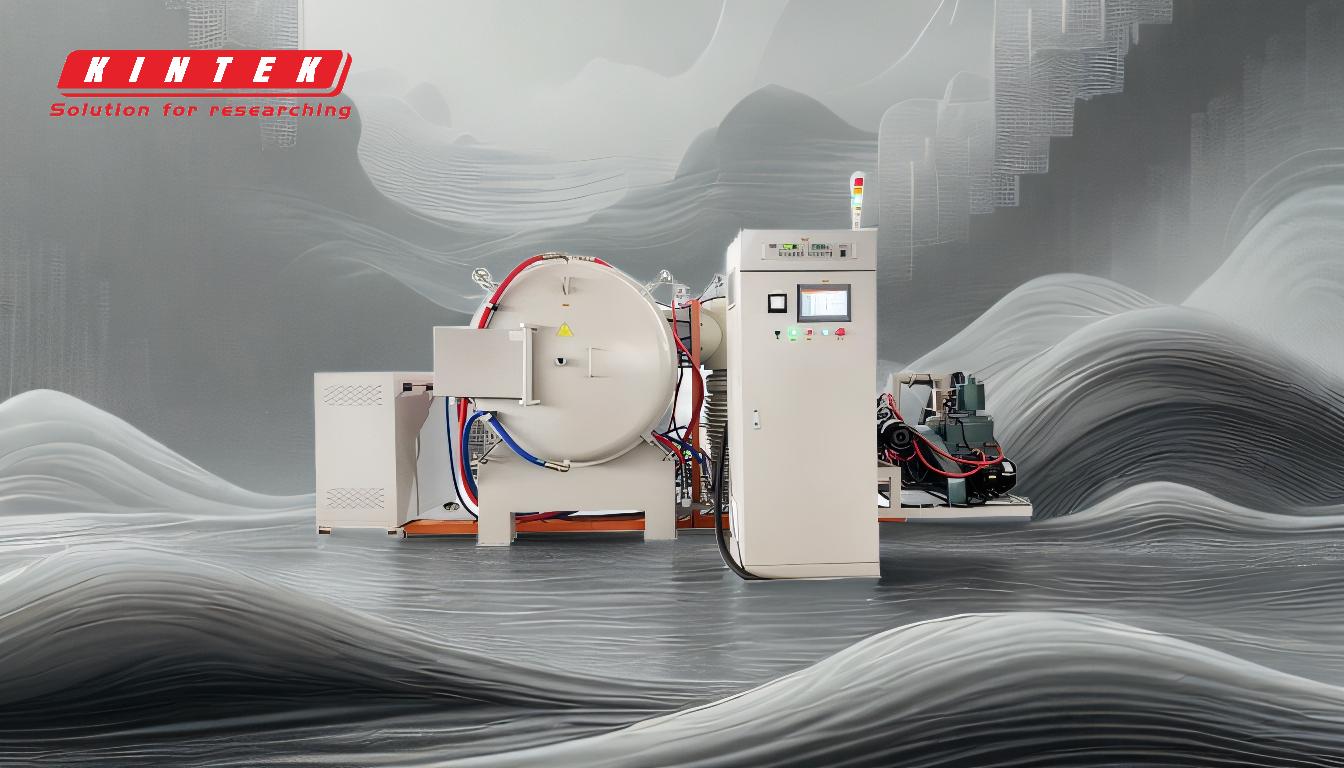
-
Définition et composition des matériaux de revêtement de base
- Les matériaux de revêtement de base sont des matériaux réfractaires composés principalement d'éléments alcalins tels que la magnésie (MgO) ou la dolomie (CaO-MgO).
- Ces matériaux sont choisis pour leur capacité à supporter des températures élevées et à résister aux réactions chimiques avec les scories basiques, ce qui les rend idéaux pour des environnements tels que les fours d'aciérie.
-
Principales propriétés des matériaux de revêtement de base
- Faible conductivité thermique:Assure une isolation thermique efficace, réduisant les pertes de chaleur et améliorant l'efficacité énergétique.
- Résistance à la corrosion:Protège le revêtement contre les attaques chimiques des scories basiques et autres substances corrosives.
- Résistance aux chocs thermiques:Permet au matériau de résister à des changements de température rapides sans se fissurer ni se détériorer.
- Facilité d'installation et d'entretien:Simplifie le processus d'application et de réparation du revêtement, réduisant ainsi les temps d'arrêt et les coûts opérationnels.
-
Applications des matériaux de revêtement de base
- Couramment utilisés dans les processus industriels à haute température, tels que la sidérurgie, la production de ciment et la fabrication du verre.
- Ils conviennent aux fours et aux réacteurs exposés à des scories basiques et à des températures extrêmes.
-
Avantages des matériaux de revêtement de base
- Durabilité:Performance durable dans les environnements difficiles.
- Efficacité énergétique:Réduit les pertes de chaleur et donc la consommation d'énergie.
- Rentabilité:Minimise la nécessité de réparations et de remplacements fréquents.
-
Éléments à prendre en compte pour la sélection
- L'application spécifique et les conditions d'exploitation (par exemple, la température, l'exposition aux produits chimiques) doivent guider le choix du matériau de revêtement de base.
- Des facteurs tels que la complexité de l'installation, les exigences de maintenance et le coût doivent également être évalués.
En résumé, les matériaux de revêtement de base sont essentiels pour les applications industrielles à haute température, car ils offrent une combinaison de durabilité, de résistance à la corrosion et aux chocs thermiques, et de facilité d'utilisation.Leur sélection et leur application doivent être adaptées aux besoins spécifiques du processus afin de garantir des performances optimales et un bon rapport coût-efficacité.
Tableau récapitulatif :
Aspect clé | Détails |
---|---|
Composition | Composés alcalins comme la magnésie (MgO) ou la dolomie (CaO-MgO). |
Propriétés principales | Faible conductivité thermique, résistance à la corrosion, résistance aux chocs thermiques. |
Applications | Sidérurgie, production de ciment, fabrication de verre. |
Avantages | Durabilité, efficacité énergétique, rentabilité. |
Considérations relatives à la sélection | Température, exposition aux produits chimiques, complexité de l'installation, besoins d'entretien. |
Vous avez besoin du bon matériau de revêtement de base pour votre application à haute température ? Contactez nos experts dès aujourd'hui pour des solutions sur mesure !