Le dépôt physique en phase vapeur (PVD) est une technologie de revêtement sous vide utilisée pour déposer des films minces ou des revêtements sur des substrats.Le procédé consiste à convertir un matériau solide ou liquide en phase vapeur par des mécanismes physiques, à transporter la vapeur dans un environnement sous vide ou à basse pression et à la condenser sur un substrat pour former un film mince.Le dépôt en phase vapeur est largement utilisé dans les industries nécessitant des revêtements précis en couches minces pour des applications mécaniques, optiques, chimiques ou électroniques, telles que les semi-conducteurs, les panneaux solaires, les emballages alimentaires et les outils de coupe.Le processus est hautement contrôlable, avec des variantes telles que la pulvérisation cathodique, l'évaporation thermique et le dépôt par faisceau d'électrons, chacune étant adaptée à des applications spécifiques.
Explication des points clés :
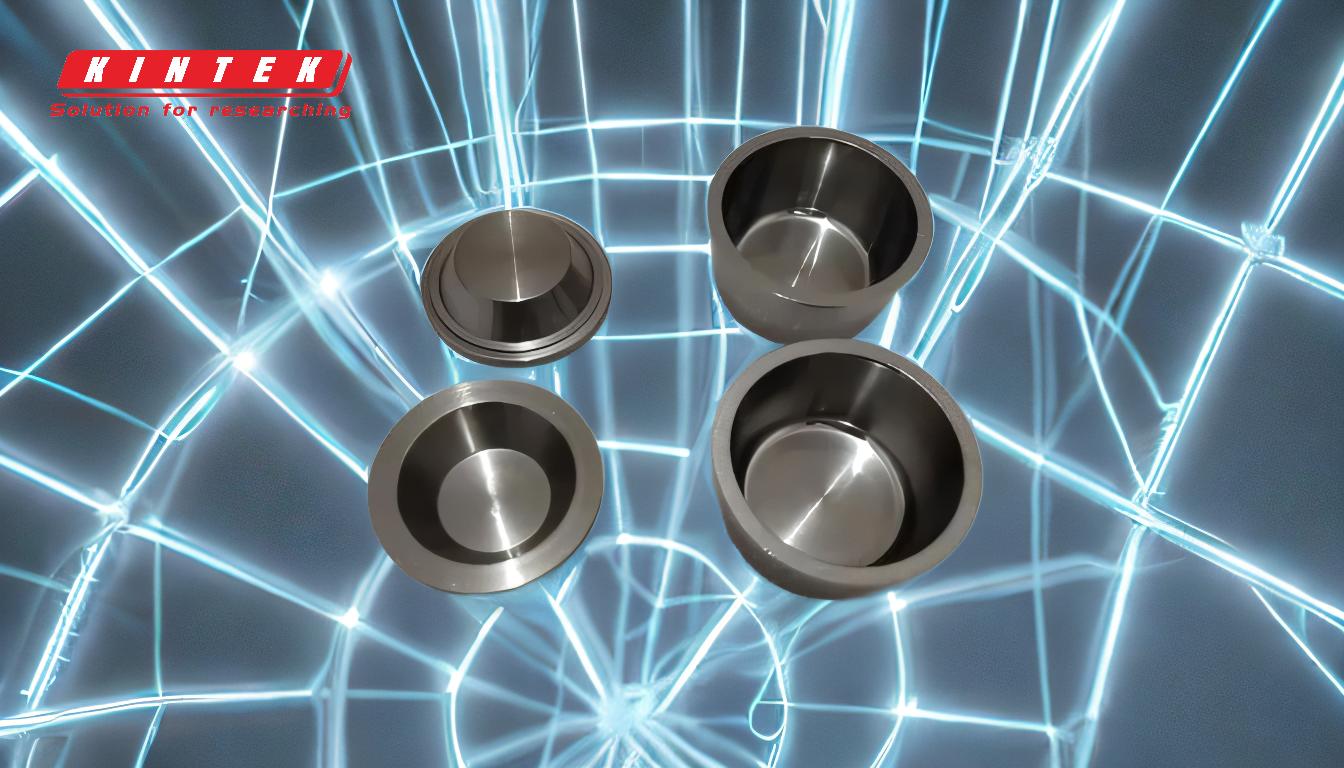
-
Définition et vue d'ensemble de la PVD:
- Le dépôt en phase vapeur est un procédé sous vide par lequel un matériau solide ou liquide est vaporisé puis condensé sur un substrat pour former un film mince.
- Il s'agit d'un procédé physique, c'est-à-dire qu'il n'implique pas de réactions chimiques pour créer la phase vapeur.
- Ce procédé est utilisé pour déposer des revêtements ayant des propriétés mécaniques, optiques, chimiques ou électroniques spécifiques.
-
Mécanismes fondamentaux du dépôt en phase vapeur (PVD):
- Vaporisation:Le matériau cible est converti d'une phase solide ou liquide en une phase vapeur à l'aide de méthodes physiques telles que la pulvérisation cathodique, l'évaporation thermique ou le bombardement par faisceau d'électrons.
- Le transport:Le matériau vaporisé est transporté dans un environnement sous vide ou à basse pression jusqu'au substrat.
- Condensation:La vapeur se condense sur le substrat, formant un film mince ou un revêtement.
-
Types de procédés PVD:
- Dépôt par pulvérisation cathodique:Les atomes sont éjectés d'un matériau cible solide par échange de momentum avec des particules à haute énergie (par exemple, des ions) et sont ensuite déposés sur le substrat.
- Évaporation thermique:Le matériau cible est chauffé jusqu'à son point de vaporisation et la vapeur qui en résulte est déposée sur le substrat.
- Dépôt par faisceau d'électrons:Un faisceau d'électrons à haute énergie est utilisé pour vaporiser le matériau cible, qui est ensuite déposé sur le substrat.
- Dépôt par laser pulsé:Un faisceau laser est utilisé pour ablater le matériau cible, créant une vapeur qui est déposée sur le substrat.
- Dépôt par arc cathodique:Un arc électrique est utilisé pour vaporiser le matériau cible, qui est ensuite déposé sur le substrat.
-
Principaux éléments de l'appareil de dépôt en phase vapeur (PVD):
- Chambre à vide:Le processus se déroule sous vide afin de minimiser la contamination et de permettre aux particules de se déplacer librement.
- Matériau cible:Le matériau solide ou liquide à vaporiser et à déposer.
- Substrat:La surface sur laquelle le film mince est déposé.
- Source d'énergie:Fournit l'énergie nécessaire pour vaporiser le matériau cible (par exemple, énergie électrique, faisceau d'électrons, laser).
- Moniteur de débit à quartz:Utilisé pour contrôler la vitesse et l'épaisseur du film déposé.
-
Applications du PVD:
- Industrie des semi-conducteurs:Utilisé pour déposer des couches minces pour les appareils électroniques, tels que les transistors et les panneaux solaires.
- Emballage alimentaire:Des films PET aluminisés sont créés par PVD pour être utilisés dans les emballages alimentaires et les ballons.
- Revêtement d'outils:Les revêtements de nitrure de titane sont appliqués aux outils de coupe pour améliorer la durabilité et les performances dans le travail des métaux.
- Revêtements optiques:Le dépôt en phase vapeur (PVD) est utilisé pour créer des revêtements antireflets et protecteurs pour les lentilles et les miroirs.
-
Avantages du PVD:
- Précision:Le procédé permet un contrôle précis de l'épaisseur et de la composition du film.
- La polyvalence:Une large gamme de matériaux peut être déposée par PVD, y compris les métaux, les céramiques et les composites.
- Durabilité:Les revêtements PVD sont très durables et résistants à l'usure, à la corrosion et aux températures élevées.
- Processus propre:L'environnement sous vide minimise la contamination, ce qui permet d'obtenir des revêtements d'une grande pureté.
-
Défis et considérations:
- Coût:L'équipement et les procédés PVD peuvent être coûteux en raison de la nécessité de disposer de systèmes sous vide et de sources d'énergie spécialisées.
- La complexité:Le procédé nécessite un contrôle minutieux des paramètres tels que la pression, la température et l'apport d'énergie.
- Compatibilité des substrats:Le substrat doit pouvoir résister aux conditions de vide et d'énergie du procédé PVD.
En résumé, le dépôt en phase vapeur est une technologie polyvalente et précise qui permet de déposer des couches minces et des revêtements dotés de propriétés fonctionnelles spécifiques.Ses applications couvrent de nombreuses industries et sa capacité à produire des revêtements durables et de haute qualité en fait un outil précieux dans la fabrication moderne.Toutefois, le processus nécessite un équipement spécialisé et un contrôle minutieux pour obtenir des résultats optimaux.
Tableau récapitulatif :
Aspect | Détails |
---|---|
Définition | Procédé sous vide permettant de déposer des couches minces sur des substrats par vaporisation. |
Mécanismes de base | Vaporisation, transport dans le vide, condensation sur le substrat. |
Types de procédés PVD | Dépôt par pulvérisation cathodique, évaporation thermique, dépôt par faisceau d'électrons, etc. |
Composants clés | Chambre à vide, matériau cible, substrat, source d'énergie, moniteur de débit. |
Applications | Semi-conducteurs, emballages alimentaires, revêtements d'outils, revêtements optiques. |
Avantages | Précision, polyvalence, durabilité, processus propre. |
Défis | Coût élevé, complexité, compatibilité des substrats. |
Découvrez comment le dépôt en phase vapeur (PVD) peut améliorer votre processus de fabrication. contactez nos experts dès aujourd'hui !