Les fours à induction électriques offrent des avantages significatifs par rapport aux fours à arc électrique (EAF) à courant continu lors des opérations de démarrage à froid. Ces avantages découlent de leur conception, de leur efficacité opérationnelle et de considérations environnementales. Les fours à induction sont connus pour leur efficacité énergétique, leur chauffage rapide, leur contrôle précis de la température et leur processus de fusion propre, ce qui les rend idéaux pour les applications industrielles. Ils éliminent le besoin d’arc ou de combustion, réduisant ainsi les risques de contamination et garantissant un environnement de travail plus sûr. De plus, leur taille compacte, leur faible consommation d’énergie et leur capacité à produire des mélanges métalliques homogènes renforcent encore leur attrait. Ci-dessous, les principaux avantages sont expliqués en détail.
Points clés expliqués :
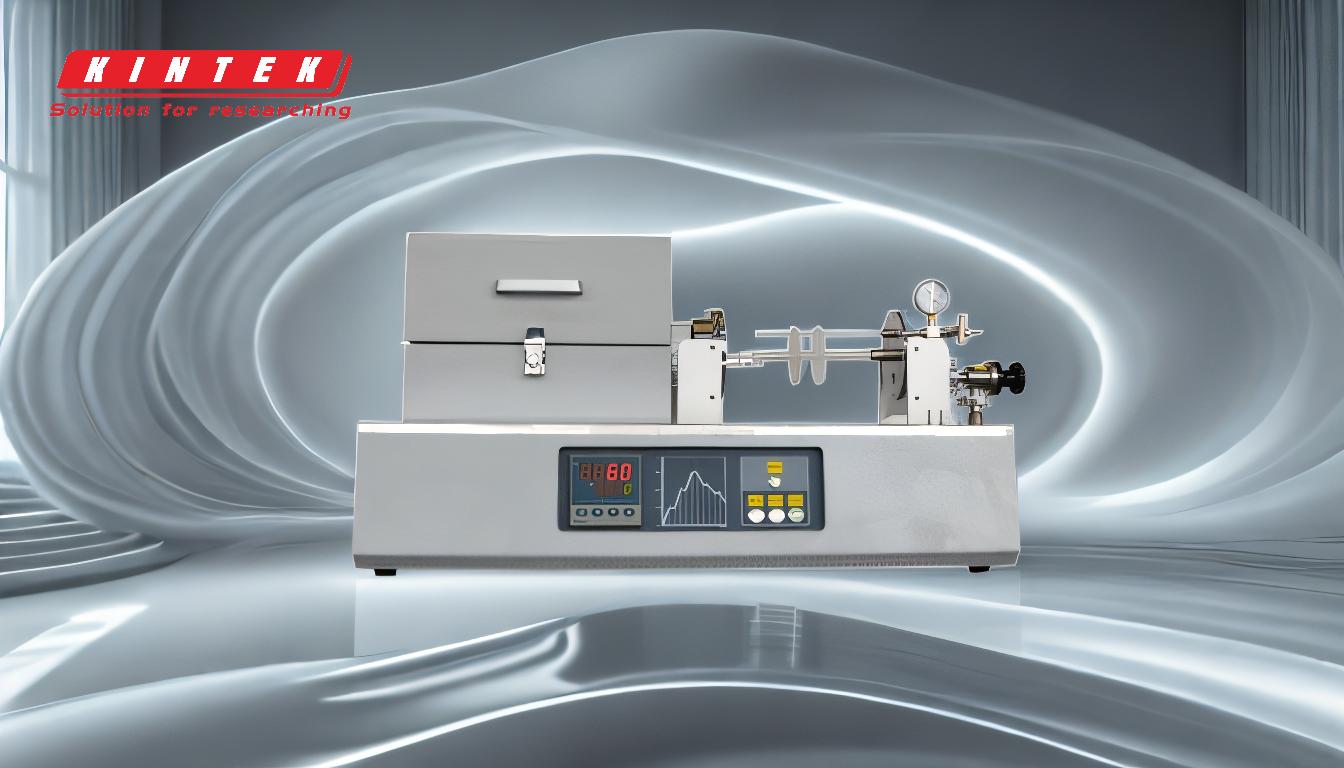
-
Efficacité énergétique et faible consommation d'énergie:
- Les fours à induction sont très économes en énergie, convertissant l’énergie électrique directement en chaleur au sein de la charge métallique. Cela minimise les pertes d'énergie et réduit la consommation d'énergie par rapport aux EAF, qui reposent sur des arcs qui peuvent être moins efficaces au démarrage.
- L'absence d'arc ou de combustion dans les fours à induction garantit une utilisation plus efficace de l'énergie, ce qui les rend adaptés à des opérations continues et réduit les coûts opérationnels globaux.
-
Chauffage rapide et efficacité de production élevée:
- Les fours à induction chauffent les métaux rapidement en raison de la génération directe de chaleur au sein de la charge métallique. Cela se traduit par des temps de démarrage plus courts et des cycles de fusion plus rapides, ce qui est particulièrement bénéfique lors des opérations de démarrage à froid.
- L'action d'agitation électromagnétique assure un chauffage et un mélange uniformes, conduisant à un mélange de métal liquide homogène sans nécessiter d'échantillonnage ou de traitement supplémentaire.
-
Contrôle précis de la température:
- Les fours à induction offrent un contrôle supérieur de la température, permettant une régulation précise du processus de fusion. Ceci est crucial pour préserver les éléments d’alliage précieux et obtenir une qualité de métal constante.
- L'absence de sources de chaleur externes réduit le risque de contamination et garantit que la température reste stable tout au long du processus.
-
Fonctionnement propre et sans pollution:
- Les fours à induction ne produisent pas de poussière, de fumées ou d'autres polluants, ce qui les rend plus respectueux de l'environnement et plus sûrs pour les travailleurs. Il s'agit d'un avantage significatif par rapport aux EAF, qui peuvent générer des émissions nocives lors du démarrage.
- L'absence de sous-produits de combustion ou liés à l'arc garantit un processus de fusion plus propre, réduisant ainsi le besoin de systèmes de filtration étendus et minimisant l'impact sur l'environnement.
-
Conception compacte et facilité d'utilisation:
- Les fours à induction sont plus petits et plus légers que les EAF, ce qui les rend plus faciles à installer et à utiliser dans des espaces confinés. Ceci est particulièrement avantageux pour les installations disposant d’un espace limité ou pour celles qui cherchent à mettre à niveau leurs équipements existants.
- La simplicité de fonctionnement et les faibles exigences de maintenance renforcent encore leur attrait, en particulier lors des opérations de démarrage à froid où la fiabilité est essentielle.
-
Distribution uniforme de la température et agitation magnétique:
- L'action d'agitation magnétique dans les fours à induction garantit une répartition uniforme de la température et une homogénéité de la composition, éliminant ainsi le besoin de mélange ou d'échantillonnage supplémentaire. Cela se traduit par des produits métalliques de meilleure qualité et réduit le temps de traitement.
- La faible différence de température entre le noyau et la surface de la charge métallique garantit une fusion constante et minimise les contraintes thermiques sur les matériaux.
-
Économies de coûts et avantages environnementaux:
- Les fours à induction permettent d'économiser des coûts de matériaux et d'exploitation en réduisant l'oxydation, la décarburation et les déchets. Leur conception économe en énergie contribue également à réduire les factures d’électricité et l’empreinte carbone.
- La capacité de fonctionner en continu pendant 24 heures sans temps d’arrêt important en fait une solution rentable pour les applications industrielles.
-
Polyvalence dans les conditions de fusion:
- Les fours à induction peuvent fonctionner dans des conditions spécifiques, telles que des environnements acides, neutres ou proches du vide, essentielles à la production d'alliages de haute qualité. Cette polyvalence n’est généralement pas disponible dans les EAF.
- L'absence d'arc électrique permet la production d'alliages à faible teneur en carbone et avec un minimum d'impuretés, ce qui rend les fours à induction idéaux pour les applications spécialisées.
En résumé, les fours à induction électriques surpassent les EAF à courant continu lors des opérations de démarrage à froid en raison de leur efficacité énergétique, de leur chauffage rapide, de leur contrôle précis et de leurs avantages environnementaux. Leur conception compacte, leur facilité d’utilisation et leur capacité à produire des produits métalliques de haute qualité en font un choix privilégié pour les environnements industriels modernes.
Tableau récapitulatif :
Avantage | Description |
---|---|
Efficacité énergétique | Convertit l'énergie électrique directement en chaleur, réduisant ainsi la consommation d'énergie. |
Chauffage rapide | Chauffage rapide et temps de démarrage plus courts pour des opérations efficaces. |
Contrôle précis de la température | Assure une fusion stable et préserve les éléments d’alliage. |
Fonctionnement propre | Pas de poussière, de fumées ou de polluants, garantissant un processus plus sûr et respectueux de l'environnement. |
Conception compacte | Plus petit et plus léger, idéal pour les espaces confinés et une utilisation facile. |
Distribution uniforme de la température | L'agitation magnétique assure un mélange homogène et une fusion constante. |
Économies de coûts | Réduit le gaspillage de matériaux, l’oxydation et les coûts opérationnels. |
Versatilité | Fonctionne dans des conditions acides, neutres ou proches du vide pour les alliages spécialisés. |
Améliorez vos opérations industrielles avec des fours à induction électriques— contactez-nous aujourd'hui pour en savoir plus !