Les méthodes de traitement des métaux, bien qu'essentielles pour la fabrication et la construction, présentent plusieurs inconvénients qui peuvent avoir un impact sur l'efficacité, le coût et la durabilité environnementale.Ces inconvénients comprennent une consommation d'énergie élevée, le gaspillage de matériaux, la pollution de l'environnement et des limitations en termes de précision et de complexité.En outre, certaines méthodes peuvent nécessiter un équipement spécialisé et une main-d'œuvre qualifiée, ce qui augmente les coûts de production.Il est essentiel de comprendre ces inconvénients pour que les industries puissent prendre des décisions éclairées et explorer des techniques alternatives ou complémentaires afin d'atténuer ces défis.
Explication des points clés :
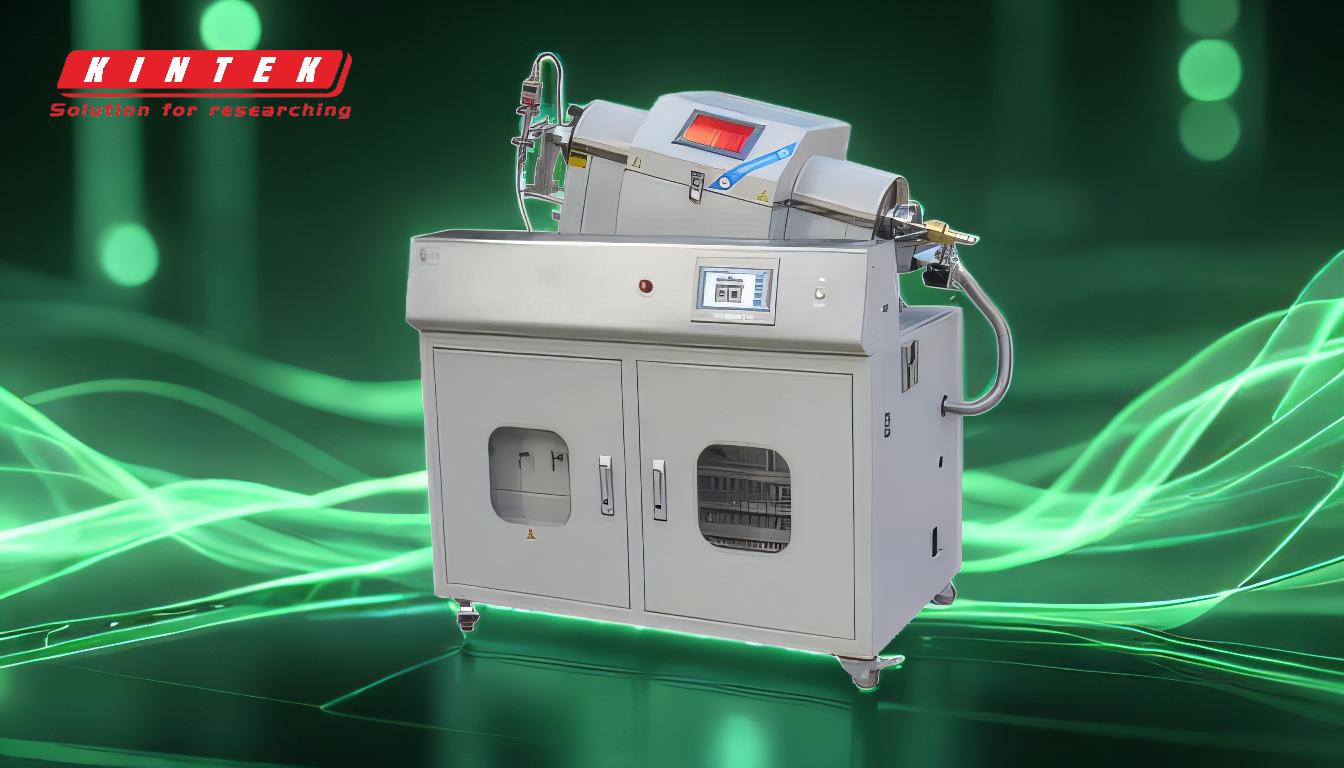
-
Consommation d'énergie élevée:
- Les méthodes de traitement des métaux telles que le moulage, le forgeage et l'usinage nécessitent souvent d'importantes quantités d'énergie pour chauffer, fondre ou façonner les métaux.Cela augmente non seulement les coûts d'exploitation, mais aussi l'empreinte carbone, en particulier lorsque des sources d'énergie non renouvelables sont utilisées.
-
Déchets de matériaux:
- De nombreuses techniques de traitement des métaux, en particulier l'usinage et le découpage, génèrent d'importants déchets de matériaux sous la forme de copeaux, d'ébarbures ou de chutes.Ces déchets peuvent être difficiles à recycler ou à réutiliser, ce qui entraîne une augmentation des coûts des matériaux et des préoccupations environnementales.
-
Pollution de l'environnement:
- Les processus tels que la fusion, le soudage et les traitements de surface peuvent libérer des polluants nocifs, notamment des gaz toxiques, des particules et des sous-produits chimiques.Ces émissions peuvent avoir des effets néfastes sur la qualité de l'air, les sources d'eau et les sols, ce qui présente des risques pour la santé humaine et les écosystèmes.
-
Limites de la précision et de la complexité:
- Les méthodes traditionnelles de traitement des métaux ne permettent pas toujours d'atteindre la haute précision et les conceptions complexes requises pour les applications d'ingénierie avancées.Les techniques telles que l'usinage CNC offrent une meilleure précision, mais sont souvent limitées par la complexité de la géométrie de la pièce et les propriétés du matériau.
-
Équipement spécialisé et main-d'œuvre qualifiée:
- De nombreuses méthodes de traitement des métaux nécessitent un équipement spécialisé coûteux et des opérateurs hautement qualifiés.Cela peut augmenter les coûts d'investissement initiaux et les dépenses opérationnelles courantes, ce qui complique la tâche des petites entreprises qui veulent être compétitives sur le marché.
-
Contraintes thermiques et mécaniques:
- Les processus tels que le soudage et le traitement thermique peuvent introduire des contraintes thermiques et mécaniques dans le métal, ce qui peut entraîner des défauts tels que le gauchissement, la fissuration ou l'affaiblissement de l'intégrité structurelle.Ces problèmes peuvent compromettre la qualité et la durabilité du produit final.
-
Lenteur de la production:
- Certaines techniques de traitement des métaux, en particulier celles qui impliquent un travail manuel ou des configurations complexes, peuvent prendre beaucoup de temps.Cela peut conduire à des taux de production plus lents, qui peuvent ne pas répondre aux exigences d'une fabrication en grande quantité ou à des délais de projet serrés.
-
Risques pour la santé et la sécurité:
- Le traitement des métaux implique souvent des conditions dangereuses, telles que l'exposition à des températures élevées, à des outils tranchants et à des produits chimiques nocifs.Garantir la sécurité des travailleurs nécessite des mesures de sécurité strictes, ce qui peut augmenter le coût global et la complexité des opérations.
En comprenant ces inconvénients, les industries peuvent explorer des méthodes alternatives telles que la fabrication additive, qui permet de réduire les déchets, d'améliorer la flexibilité de la conception et de diminuer la consommation d'énergie dans certains cas.En outre, l'adoption de pratiques durables et l'investissement dans des technologies de pointe peuvent contribuer à atténuer les effets négatifs des méthodes traditionnelles de traitement des métaux.
Tableau récapitulatif :
Désavantage | Impact clé |
---|---|
Consommation d'énergie élevée | Augmente les coûts opérationnels et l'empreinte carbone. |
Déchets de matériaux | Génère des copeaux et des chutes, ce qui entraîne une augmentation des coûts des matériaux. |
Pollution de l'environnement | Rejet de gaz toxiques, de particules et de sous-produits chimiques. |
Limites de précision et de complexité | Difficultés liées aux conceptions complexes et aux exigences de haute précision. |
Équipement et main-d'œuvre spécialisés | Nécessite des équipements coûteux et des opérateurs qualifiés, ce qui augmente les coûts de production. |
Contraintes thermiques et mécaniques | Peut provoquer des déformations, des fissures ou un affaiblissement de l'intégrité structurelle. |
Ralentissement des taux de production | Les processus qui prennent du temps peuvent retarder la fabrication en grande série. |
Risques pour la santé et la sécurité | Implique des conditions dangereuses, nécessitant des mesures de sécurité rigoureuses. |
Vous recherchez des solutions durables pour le traitement des métaux ? Contactez nos experts dès aujourd'hui pour explorer les alternatives !