La méthode d'évaporation du dépôt physique en phase vapeur (PVD) est une technique largement utilisée pour déposer des couches minces de matériau sur un substrat.Cette méthode consiste à chauffer le matériau jusqu'à ce qu'il s'évapore, formant une vapeur qui se condense ensuite sur le substrat pour former un film mince.Ce processus est très contrôlable et permet de produire des films d'une pureté, d'une uniformité et d'une adhérence excellentes.Les techniques courantes de la méthode d'évaporation comprennent l'évaporation thermique et l'évaporation par faisceau d'électrons, chacune utilisant des mécanismes de chauffage différents pour obtenir la vaporisation souhaitée du matériau.
Explication des points clés :
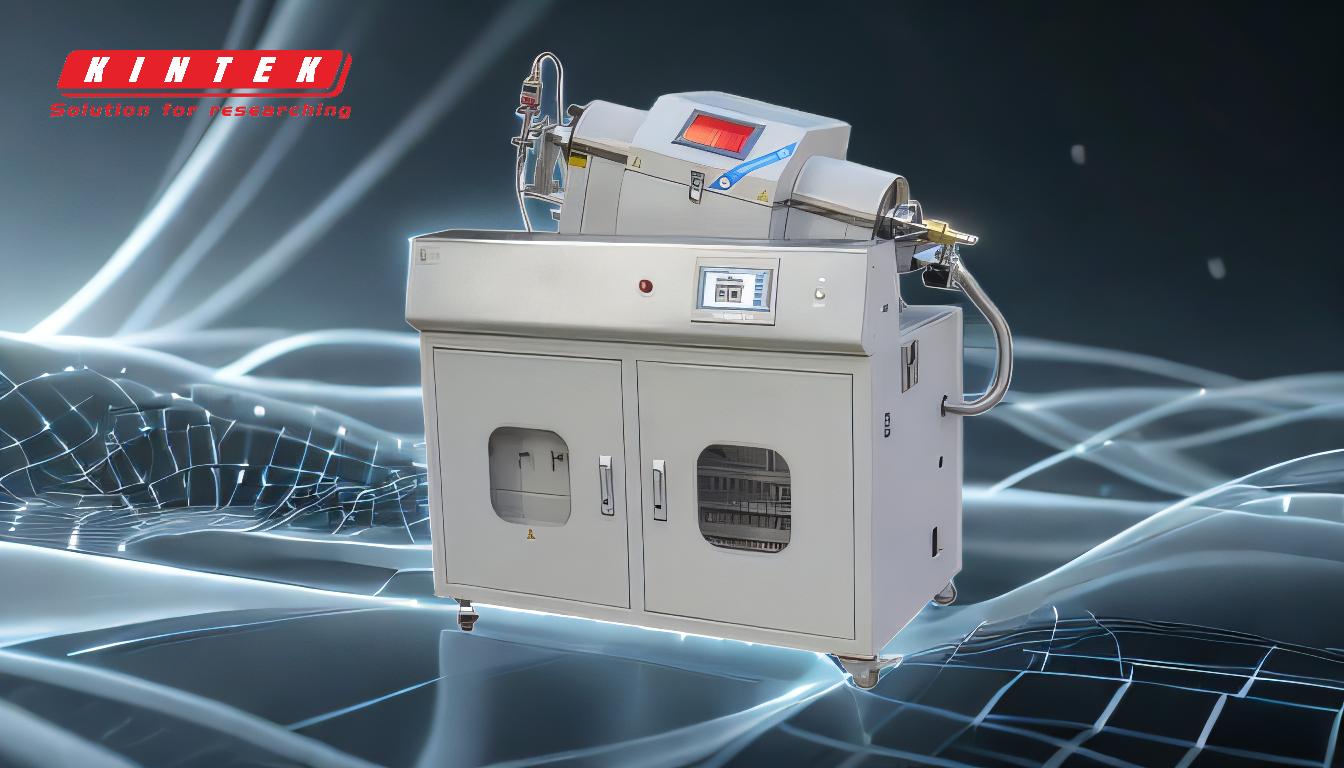
-
Evaporation thermique Dépôt:
- Dans l'évaporation thermique, le matériau à déposer est placé dans un bateau ou une bobine de résistance, qui est généralement constitué d'un large ruban métallique avec une grande cavité.Des pastilles de matériau sont placées dans la cavité et un courant électrique traverse le ruban pour le chauffer.Ce chauffage fait fondre les pastilles, qui finissent par s'évaporer.La vapeur traverse alors le vide et se dépose sur le substrat, formant un film mince.
- Cette méthode est particulièrement utile pour les matériaux qui peuvent être facilement vaporisés à des températures relativement basses.Il s'agit d'une technique simple et rentable, ce qui la rend populaire dans diverses applications, y compris la production de revêtements optiques et de dispositifs électroniques.
-
Evaporation par faisceau d'électrons:
- L'évaporation par faisceau d'électrons est une technique plus avancée dans laquelle un faisceau d'électrons est utilisé pour chauffer le matériau.Le faisceau d'électrons est focalisé sur le matériau, ce qui le fait chauffer rapidement et s'évaporer.La vapeur se dépose alors sur le substrat, formant un film mince.
- Cette méthode est particulièrement utile pour les matériaux dont l'évaporation nécessite des températures élevées, car le faisceau d'électrons peut fournir une source de chaleur concentrée.Elle est souvent utilisée dans des applications nécessitant des films de haute pureté, comme dans l'industrie des semi-conducteurs.Les films produits par évaporation par faisceau d'électrons présentent généralement d'excellentes propriétés de réflectivité, ce qui les rend adaptés aux applications optiques.
-
Avantages de la méthode d'évaporation:
- Haute pureté:La méthode d'évaporation permet de produire des films d'une très grande pureté, car le processus se déroule sous vide, ce qui minimise la contamination.
- Uniformité:Les films produits sont très uniformes, ce qui est crucial pour les applications nécessitant un contrôle précis de l'épaisseur.
- Adhésion:Les films adhèrent bien au substrat, ce qui garantit leur durabilité et leur longévité.
- Polyvalence:La méthode peut être utilisée avec une large gamme de matériaux, y compris les métaux, les semi-conducteurs et les isolants.
-
Comparaison avec d'autres méthodes de dépôt en phase vapeur (PVD):
- Dépôt thermique en phase vapeur:Semblable à l'évaporation thermique, mais elle consiste généralement à chauffer le matériau à l'aide d'un appareil de chauffage électrique jusqu'à ce qu'il entre dans la phase gazeuse.Cette méthode est également utilisée pour produire des films purs et uniformes.
- Epitaxie par faisceaux moléculaires (MBE):Une forme plus spécialisée de PVD utilisée pour produire des films cristallins de haute qualité.Elle implique l'utilisation de faisceaux moléculaires dans un environnement de vide très poussé.
- Dépôt par pulvérisation cathodique d'un faisceau d'ions:Cette méthode consiste à bombarder un matériau cible avec des ions pour éjecter des atomes, qui se déposent ensuite sur le substrat.Cette méthode est connue pour produire des films ayant une excellente adhérence et densité.
-
Applications de la méthode d'évaporation:
- Revêtements optiques:Utilisé pour créer des revêtements réfléchissants et antireflets sur les lentilles et les miroirs.
- Électronique:Essentiel pour le dépôt de couches minces dans la fabrication de semi-conducteurs et d'autres composants électroniques.
- Revêtements décoratifs:Utilisé pour appliquer des films minces à des fins esthétiques, par exemple sur des bijoux ou des pièces automobiles.
- Couches barrières:Appliqué dans les emballages pour créer des couches barrières qui protègent les produits de l'humidité et de l'oxygène.
En résumé, la méthode d'évaporation en PVD est une technique polyvalente et efficace pour déposer des couches minces d'une grande pureté, d'une grande uniformité et d'une grande adhérence.Elle comprend à la fois l'évaporation thermique et l'évaporation par faisceau d'électrons, chacune étant adaptée à des matériaux et des applications différents.Cette méthode est largement utilisée dans des secteurs allant de l'électronique à l'optique, ce qui en fait la pierre angulaire de la technologie moderne des couches minces.
Tableau récapitulatif :
Aspect | Détails |
---|---|
Techniques | Evaporation thermique, Evaporation par faisceau d'électrons |
Avantages | Haute pureté, uniformité, adhérence, polyvalence |
Applications | Revêtements optiques, électronique, revêtements décoratifs, couches barrières |
Comparaison avec le dépôt en phase vapeur (PVD) | Dépôt thermique en phase vapeur, épitaxie par faisceau moléculaire, pulvérisation cathodique par faisceau d'ions |
Découvrez comment la méthode d'évaporation peut améliorer vos procédés de fabrication de couches minces. contactez nos experts dès aujourd'hui !