Le revêtement par dépôt sous vide est un procédé sophistiqué utilisé pour appliquer de fines couches de matériau sur un substrat dans un environnement contrôlé et sous vide poussé.Cette méthode permet d'obtenir des revêtements précis et de haute qualité pour des applications allant de la protection contre la corrosion aux finitions optiques et décoratives.Le procédé consiste à créer un vide pour éliminer les gaz interférents, à préparer le substrat, à évaporer ou à pulvériser le matériau de revêtement, à le déposer sur le substrat et à refroidir le système.Il est largement utilisé dans des secteurs tels que l'électronique, l'automobile et l'énergie en raison de sa capacité à produire des revêtements uniformes, durables et fonctionnels au niveau atomique ou moléculaire.
Explication des principaux points :
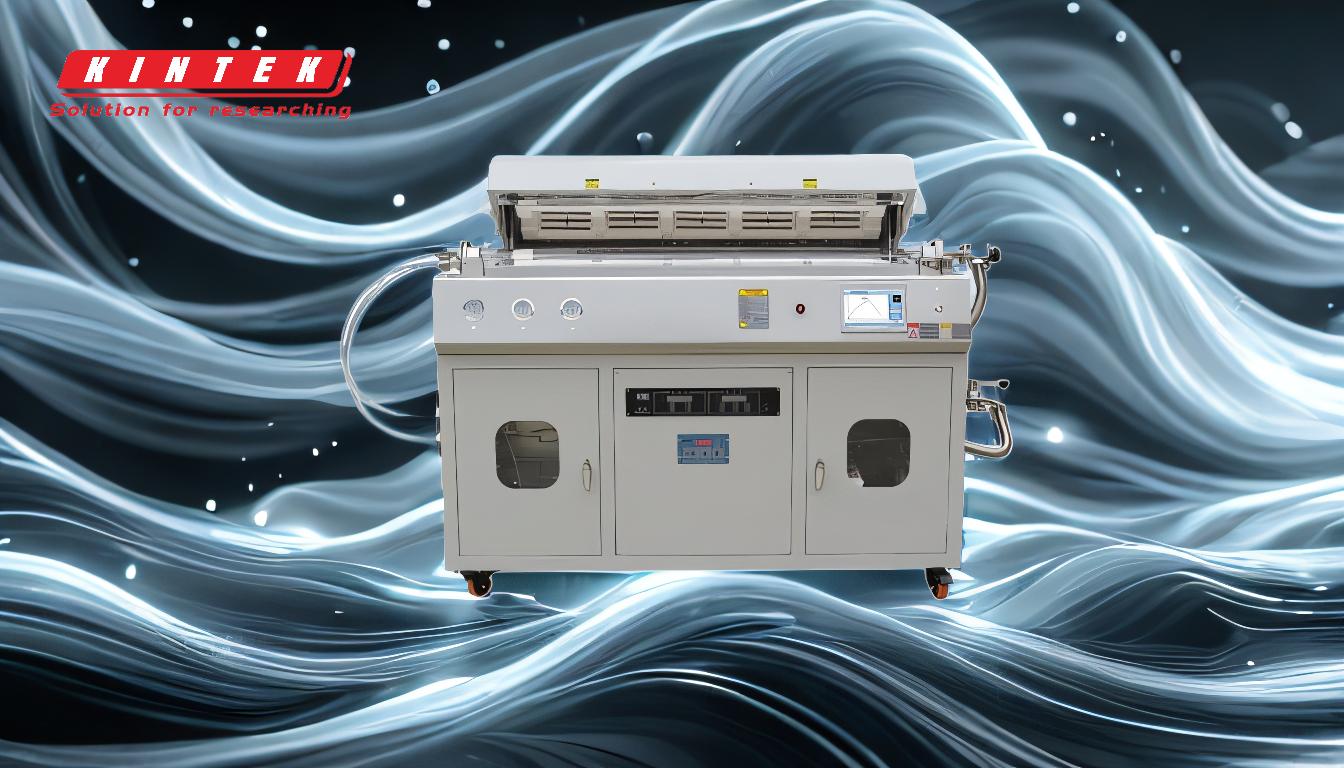
-
Création d'un environnement sous vide
- La première étape du dépôt sous vide consiste à créer un vide à l'intérieur de la chambre de dépôt.Cela permet d'éliminer l'air et les gaz qui pourraient interférer avec le processus de dépôt ou contaminer le revêtement.
- Un vide poussé permet au matériau de revêtement de se déplacer librement vers le substrat sans entrer en collision avec les molécules de gaz, ce qui permet d'obtenir un film uniforme et de haute qualité.
- Le vide réduit également l'oxydation et d'autres réactions chimiques susceptibles de dégrader les performances du revêtement.
-
Préparation du substrat
- Avant le dépôt, le substrat doit être soigneusement nettoyé et traité pour garantir une bonne adhérence du matériau de revêtement.
- Les méthodes de nettoyage peuvent inclure le nettoyage par ultrasons, les traitements chimiques ou le nettoyage au plasma pour éliminer les contaminants tels que les huiles, les poussières ou les oxydes.
- Les traitements de surface, tels que la gravure ou l'application de couches favorisant l'adhésion, peuvent également être utilisés pour améliorer la liaison entre le substrat et le revêtement.
-
Évaporation ou pulvérisation du matériau de revêtement
-
Le matériau de revêtement est introduit dans la chambre à vide de deux manières principales : par évaporation ou par pulvérisation.
- L'évaporation:Le matériau est chauffé jusqu'à ce qu'il se vaporise, soit par chauffage résistif, soit par faisceaux d'électrons, soit par ablation laser.Les atomes ou molécules vaporisés traversent alors le vide et se déposent sur le substrat.
- Pulvérisation:Des ions à haute énergie (souvent de l'argon) sont utilisés pour bombarder un matériau cible, arrachant des atomes ou des molécules qui se déposent ensuite sur le substrat.
- Les deux méthodes permettent un contrôle précis de l'épaisseur et de la composition de la couche déposée, même à l'échelle du nanomètre.
-
Le matériau de revêtement est introduit dans la chambre à vide de deux manières principales : par évaporation ou par pulvérisation.
-
Dépôt du revêtement
- Le matériau vaporisé ou pulvérisé traverse le vide et adhère au substrat, formant un film mince.
- Le processus de dépôt peut être contrôlé pour obtenir des propriétés de film spécifiques, telles que l'épaisseur, l'uniformité et la microstructure.
- Des obturateurs, des contrôleurs de vitesse de dépôt et des réchauffeurs peuvent être utilisés pour affiner le processus et garantir des résultats cohérents.
-
Refroidissement et ventilation du système
- Une fois le dépôt terminé, on laisse le système refroidir pour éviter toute contrainte thermique sur le substrat ou le revêtement.
- La chambre à vide est ensuite ventilée pour permettre au substrat revêtu d'être retiré en toute sécurité.
- Un refroidissement et une ventilation corrects sont essentiels pour préserver l'intégrité du revêtement et garantir que le système est prêt pour le cycle suivant.
-
Applications de la déposition sous vide
-
Le dépôt sous vide est utilisé dans un large éventail d'industries et d'applications, notamment :
- Revêtements optiques:Revêtements antireflets, miroirs et interférences pour les lentilles, les miroirs et les écrans.
- Revêtements décoratifs:Finitions métalliques ou colorées pour les produits de consommation.
- Revêtements résistants à l'usure:Couches dures et durables pour les outils et les machines.
- Protection contre la corrosion:Films minces qui protègent les métaux de la dégradation de l'environnement.
- Dispositifs à semi-conducteurs:Couches précises pour la conduction électrique et l'isolation.
- Cellules solaires:Matériaux photovoltaïques en couche mince pour la production d'énergie.
- La polyvalence du dépôt sous vide en fait une pierre angulaire de la science et de l'ingénierie des matériaux modernes.
-
Le dépôt sous vide est utilisé dans un large éventail d'industries et d'applications, notamment :
En suivant ces étapes, le revêtement par dépôt sous vide permet d'obtenir des résultats hautement contrôlés et reproductibles, ce qui en fait une technologie essentielle pour la production de matériaux et de revêtements avancés dans diverses industries.
Tableau récapitulatif :
Étape | Description de l'étape |
---|---|
1.Création d'un vide | Élimine l'air et les gaz afin de garantir un environnement exempt de contaminants pour un dépôt uniforme du revêtement. |
2.Préparation du support | Nettoyage et traitement du substrat pour améliorer l'adhérence du matériau de revêtement. |
3.Évaporation/Sputérisation | Le matériau de revêtement est vaporisé ou pulvérisé pour créer un film mince. |
4.Dépôt | Le matériau de revêtement adhère au substrat, formant une couche précise et uniforme. |
5.Refroidissement et ventilation | Le système se refroidit pour éviter les contraintes thermiques ; la chambre est ventilée pour permettre l'enlèvement du substrat en toute sécurité. |
6.Applications | Utilisé dans les domaines de l'optique, de la décoration, de la résistance à l'usure, de la protection contre la corrosion, des semi-conducteurs et des cellules solaires. |
Découvrez comment le revêtement par dépôt sous vide peut transformer vos matériaux. contactez nos experts dès aujourd'hui !