Le procédé du four rotatif est une méthode de traitement thermique à haute température utilisée pour traiter les matériaux granulaires ou en poudre.Il consiste à chauffer les matériaux dans un tambour rotatif afin de faciliter les réactions chimiques telles que la calcination, l'oxydation, la réduction ou le frittage.Les fours rotatifs électriques sont un type particulier de fours rotatifs qui utilisent des éléments chauffants électriques pour atteindre les températures requises.Ces fours sont conçus avec plusieurs zones de chauffage, chacune contrôlée indépendamment, et sont équipés de systèmes de refroidissement pour gérer la température de sortie du matériau.Le processus est hautement personnalisable, la taille du four, les éléments chauffants et la vitesse de rotation étant adaptés aux exigences spécifiques du matériau et de la production.Les fours rotatifs électriques sont particulièrement efficaces pour les applications nécessitant un contrôle précis de la température et de l'uniformité.
Explication des principaux points :
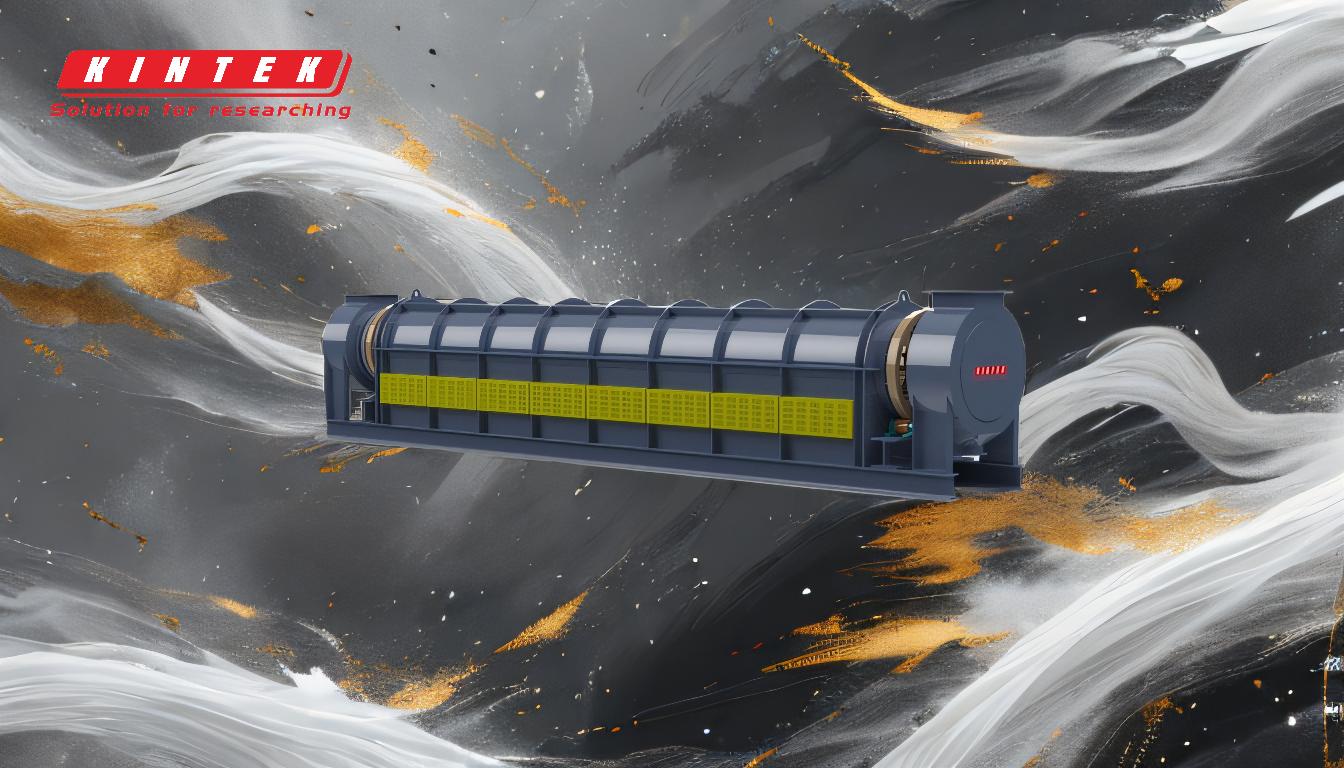
-
Types de fours rotatifs:
- Les fours rotatifs peuvent être à feu direct ou à feu indirect (calcinateurs) .Les fours à combustion directe utilisent le contact direct entre le matériau et le gaz de traitement pour induire des réactions, tandis que les fours à combustion indirecte s'appuient sur la chaleur de l'enveloppe du tambour chauffée de l'extérieur.
- Les fours rotatifs électriques Les fours rotatifs électriques sont un type de four spécialisé qui utilise des éléments chauffants électriques pour atteindre des températures élevées, ce qui les rend idéaux pour un traitement thermique précis.
-
Applications des fours rotatifs électriques:
- Les fours rotatifs électriques sont utilisés pour la calcination de matériaux granulaires ou pulvérulents et faciliter les réactions à haute température telles que l'oxydation et réduction .
- Ils sont également utilisés pour frittage Le frittage est un processus par lequel des matériaux sont chauffés juste en dessous de leur point de fusion afin d'augmenter leur résistance. Ce procédé est couramment utilisé pour la granulation du minerai de fer et la production de proppants.
-
Système de chauffage:
- Les éléments chauffants d'un four rotatif électrique sont généralement fabriqués à partir d'alliages de alliages nickel-chrome (par exemple, 1Cr18Ni9Ti, Cr25Ni20Si2) ou alliages fer-chrome-aluminium (par exemple, 0Cr13A14, 0Cr25A15).
- Ces éléments en forme de spirale sont installés sur les côtés et le fond du four, divisés en quatre zones de chauffage chacune avec un contrôle indépendant de la température.
-
Processus de refroidissement:
- Le refroidissement est réalisé à l'aide d'un refroidisseur à tambour Le refroidisseur à tambour est un système de refroidissement indirect par pulvérisation d'eau sur l'extérieur du cylindre, qui permet de refroidir indirectement le matériau lors de son passage dans le tambour.
- Cela permet de s'assurer que le matériau atteint la température de décharge requise.
-
Mécanisme de rotation:
- Le four est mis en rotation par un engrenage relié à un moteur électrique à vitesse variable .Par exemple, un four de 6 x 60 m nécessite environ 800 kW pour tourner à 3 tours .
- A variateur de vitesse contrôle le débit du matériau, et un entraînement auxiliaire (par exemple, un petit moteur électrique ou un moteur diesel) est utilisé pendant les pannes de courant pour éviter les dommages.
-
Construction du four:
- Le tube rotatif est fabriqué à partir alliages à base de nickel capables de résister à des températures allant jusqu'à 1100℃ .
- Le diamètre et la longueur du tambour peuvent être personnalisés en fonction de la capacité de traitement des matériaux, et plusieurs zones de chauffage indépendantes peuvent être conçues pour répondre aux besoins de la production.
-
Dimensionnement et conception:
- Le dimensionnement d'un four rotatif implique des principes d'ingénierie , les analyses thermiques et chimiques et l'expérience pour atteindre les objectifs de traitement.
- Les facteurs clés sont les suivants la capacité , production de chaleur , vitesse d'avance maximale , temps de rétention et le profil du lit qui déterminent le diamètre et la longueur du four.
-
Personnalisation et flexibilité:
- Les fours rotatifs électriques offrent une grande flexibilité, avec des zones de chauffage , les vitesses de rotation et systèmes de refroidissement adaptés à des matériaux et à des exigences de production spécifiques.
- Ils conviennent donc à une large gamme d'applications industrielles, de la calcination au frittage.
En combinant un contrôle précis de la température, un refroidissement efficace et une conception personnalisable, les fours rotatifs électriques constituent une solution fiable et polyvalente pour le traitement des matériaux à haute température.
Tableau récapitulatif :
Aspect | Détails |
---|---|
Types de fours rotatifs | Fours rotatifs à feu direct, à feu indirect (calcinateurs) et électriques. |
Applications | Calcination, oxydation, réduction et frittage. |
Système de chauffage | Éléments chauffants en alliage d'aluminium nickel-chrome ou fer-chrome. |
Processus de refroidissement | Refroidisseur à tambour avec pulvérisation d'eau pour le refroidissement indirect. |
Mécanisme de rotation | Engrenage et moteur électrique à vitesse variable pour un contrôle précis. |
Construction du four | Tubes en alliage à base de nickel, diamètre et longueur personnalisables. |
Personnalisation | Zones de chauffage, vitesses de rotation et systèmes de refroidissement réglables. |
Découvrez comment les fours rotatifs électriques peuvent optimiser votre traitement des matériaux. contactez-nous dès aujourd'hui pour obtenir des conseils d'experts !