Le procédé de cémentation, bien que largement utilisé pour le durcissement superficiel des composants en acier, présente plusieurs inconvénients selon la méthode utilisée (cémentation sous atmosphère ou sous vide). Ceux-ci incluent des coûts d'investissement initiaux élevés, la nécessité d'un contrôle empirique des processus, des préoccupations environnementales et de sécurité, ainsi que des défis liés à la maintenance et au post-traitement des équipements. Chaque méthode présente des inconvénients uniques, tels que la formation de suie et de goudron lors de la cémentation sous vide ou des problèmes de qualité de profondeur de cuvette lors de la cémentation sous atmosphère. Comprendre ces inconvénients est crucial pour que les acheteurs d’équipements et de consommables puissent prendre des décisions éclairées.
Points clés expliqués :
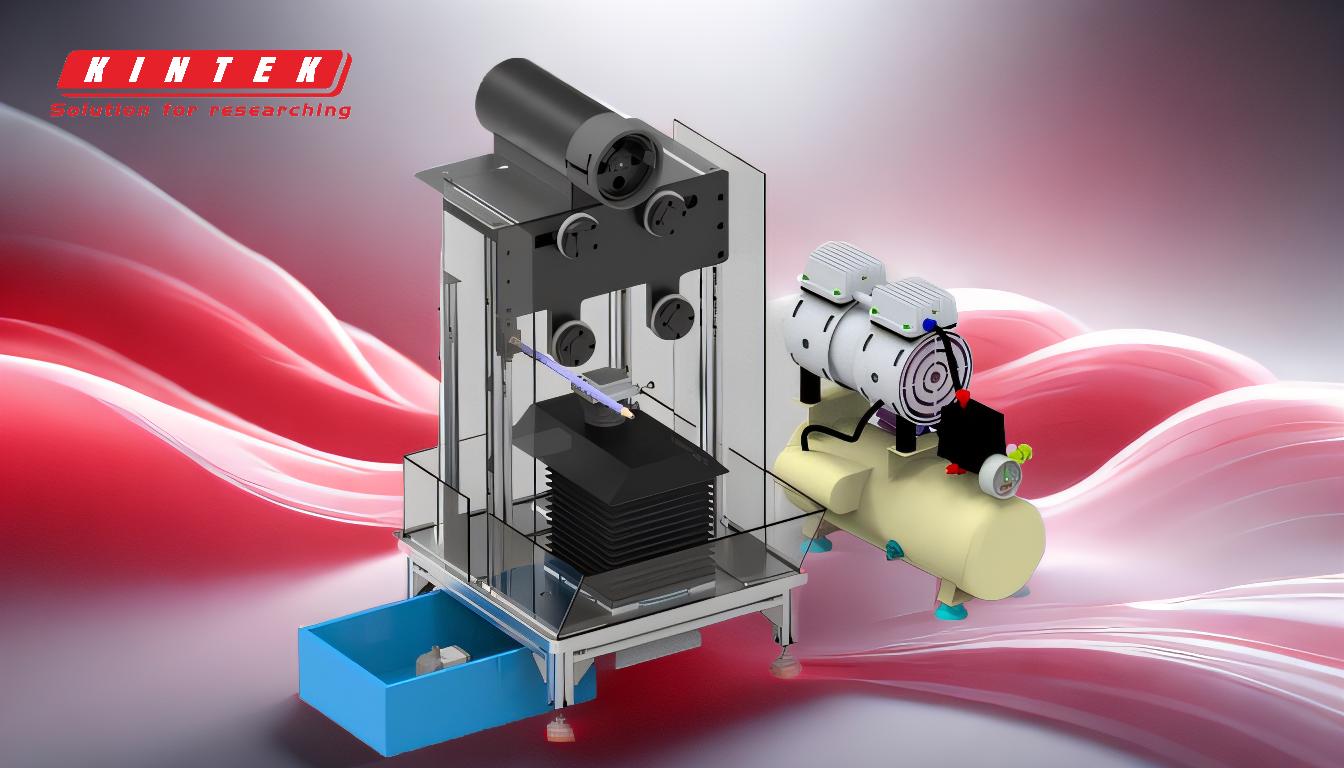
-
Coût d’équipement initial élevé:
- Explication: La cémentation sous vide nécessite un équipement spécialisé, qui s'accompagne souvent d'un investissement initial plus élevé que la cémentation sous atmosphère traditionnelle. Cela comprend des chambres à vide avancées, des systèmes de traitement des gaz et des mécanismes précis de contrôle de la température.
- Impact: Pour les entreprises, cela signifie un engagement financier initial important, ce qui peut ne pas être réalisable pour les petites opérations ou celles disposant de budgets limités.
-
Contrôle empirique des processus:
- Explication: La cémentation sous atmosphère et sous vide s'appuie fortement sur des données empiriques pour obtenir des résultats reproductibles. Cela signifie que les opérateurs doivent posséder une vaste expérience et effectuer de nombreux essais pour déterminer les réglages optimaux pour chaque charge spécifique.
- Impact: Cette dépendance aux essais et erreurs peut entraîner des inefficacités, une augmentation du temps de production et des coûts plus élevés en raison du besoin de personnel qualifié et du gaspillage potentiel de matériel lors des tests.
-
Formation de suie et de goudron (cémentation sous vide):
- Explication: Lors de la cémentation sous vide, le type, la pression et la quantité d'hydrocarbures gazeux introduits peuvent conduire à la formation de suie et de goudron. Ces sous-produits peuvent contaminer les équipements et les pièces en cours de traitement.
- Impact: Cela nécessite un nettoyage et un entretien fréquents de l'équipement, ce qui augmente les temps d'arrêt et les coûts d'exploitation. De plus, la présence de suie et de goudron peut affecter la qualité de la couche carburée, conduisant potentiellement à une reprise ou à la mise au rebut des pièces.
-
Conditionnement d'équipement (cémentation en atmosphère):
- Explication: L'équipement de cémentation atmosphérique doit être correctement conditionné s'il est inutilisé ou arrêté pendant une période quelconque. Il s'agit de purger le système et de s'assurer du bon équilibre de l'atmosphère avant de reprendre les opérations.
- Impact: Cette exigence peut entraîner des retards dans la production, surtout si l'équipement est fréquemment arrêté et démarré. Cela ajoute également à la complexité opérationnelle et nécessite des ressources supplémentaires pour la maintenance.
-
Grandes tolérances matérielles pour le post-traitement:
- Explication: Les deux méthodes nécessitent souvent des tolérances de matière importantes pour s'adapter aux opérations de post-traitement telles que le meulage ou l'usinage. Ceci est nécessaire pour obtenir les dimensions finales et l’état de surface après cémentation.
- Impact: Cela augmente les coûts des matériaux et peut conduire à une production de déchets plus importante, ce qui peut ne pas être durable ou rentable à long terme.
-
Problèmes de qualité de profondeur de cas:
- Explication: Il peut être difficile d'obtenir une profondeur de cuvelage constante lors de la cémentation sous atmosphère en raison des variations du potentiel de carbone de l'atmosphère et d'autres variables du processus.
- Impact: Une profondeur de boîtier incohérente peut conduire à des pièces qui ne répondent pas aux spécifications, entraînant des reprises, des rebuts ou même une défaillance en service. Cette variabilité peut également compliquer les processus de contrôle qualité.
-
Problèmes de pollution de l’environnement et de sécurité:
- Explication: La cémentation atmosphérique implique l'utilisation de gaz potentiellement dangereux, qui nécessitent une surveillance constante pour prévenir la pollution de l'environnement et garantir la sécurité du lieu de travail.
- Impact: Cela ajoute à la charge opérationnelle, nécessitant des investissements dans les équipements de sécurité, la formation et le respect des réglementations environnementales. Ne pas gérer correctement ces aspects peut entraîner des amendes, des problèmes juridiques et nuire à la réputation de l’entreprise.
En résumé, bien que la cémentation soit une méthode efficace pour améliorer les propriétés de surface des composants en acier, elle présente plusieurs inconvénients qui doivent être soigneusement pris en compte. Ceux-ci incluent des coûts initiaux élevés, la nécessité d'un contrôle empirique des processus, des préoccupations environnementales et de sécurité, ainsi que des défis liés à la maintenance et au post-traitement des équipements. Comprendre ces inconvénients est essentiel pour prendre des décisions éclairées lors de la sélection et de la mise en œuvre des procédés de carburation.
Tableau récapitulatif :
Inconvénient | Méthode | Impact |
---|---|---|
Coût d’équipement initial élevé | Cémentation sous vide | Un investissement initial important, un défi pour les petites opérations |
Contrôle empirique des processus | Les deux méthodes | Nécessite du personnel qualifié, des essais et des erreurs et un temps de production accru |
Formation de suie et de goudron | Cémentation sous vide | Nettoyage fréquent, contamination de l'équipement et retouche potentielle des pièces |
Conditionnement des équipements | Cémentation en atmosphère | Retards de production et complexité opérationnelle accrue |
Grandes allocations matérielles | Les deux méthodes | Augmentation des coûts des matériaux et production de déchets plus élevée |
Problèmes de qualité de profondeur de cas | Carburation en atmosphère | Résultats incohérents, retouches ou mise au rebut de pièces |
Pollution de l'environnement | Carburation en atmosphère | Problèmes de sécurité, conformité réglementaire et amendes potentielles |
Besoin d'aide pour choisir le bon processus de durcissement de surface ? Contactez nos experts dès aujourd'hui pour des solutions sur mesure !