Les fours à induction utilisent des fréquences élevées principalement pour améliorer l'efficacité, la précision et le contrôle du processus de fusion.Les fours à induction à haute fréquence sont particulièrement efficaces pour les petits volumes de métal en raison de l'effet de profondeur de peau, qui garantit que le courant alternatif ne pénètre que la couche superficielle du matériau.Il en résulte un chauffage plus rapide, un temps de fusion réduit et un meilleur contrôle de la température.En outre, les hautes fréquences permettent le brassage automatique du métal en fusion par des courants de Foucault, ce qui améliore l'homogénéité.La conception des fours à haute fréquence est plus simple et plus rentable, ce qui les rend idéaux pour les applications exigeant précision et rapidité de fusion.Globalement, les hautes fréquences optimisent le transfert d'énergie et l'efficacité opérationnelle des fours à induction.
Explication des points clés :
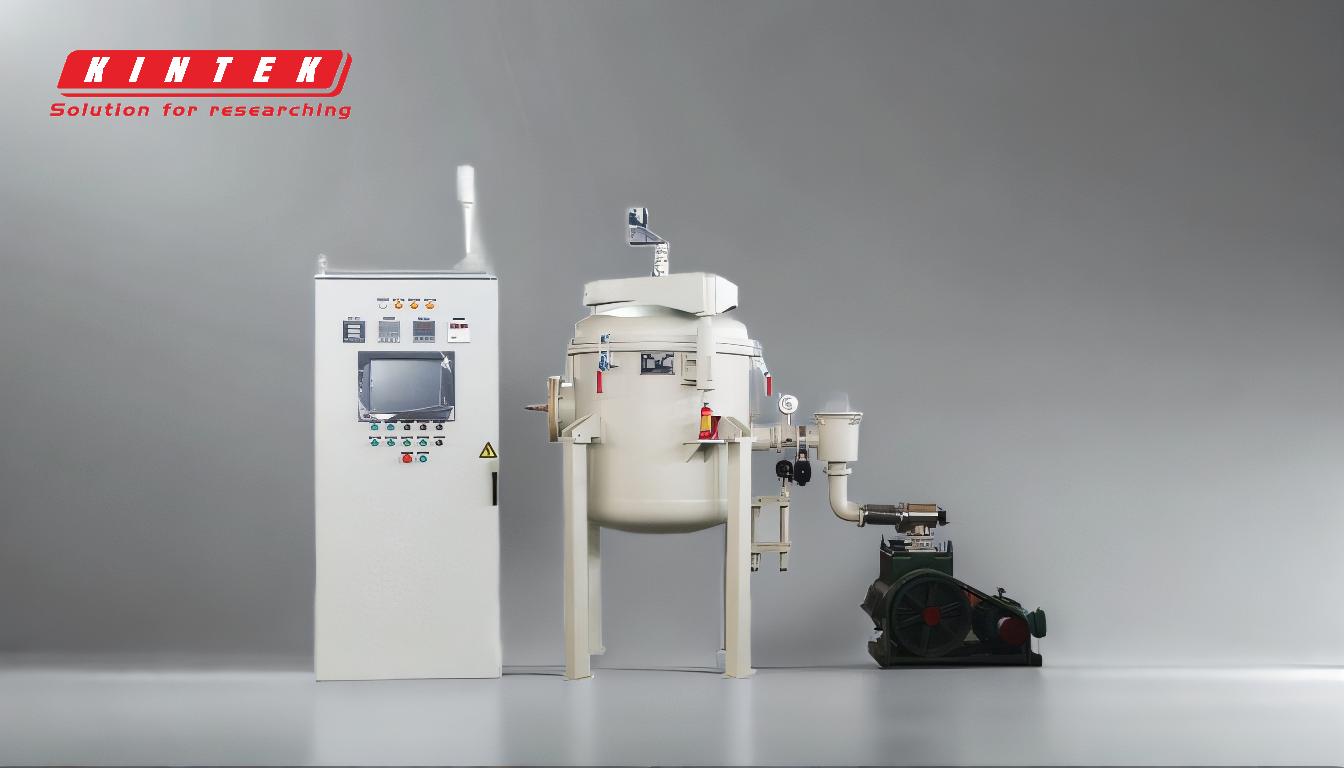
-
Effet de profondeur de la peau et pénétration:
- Les fours à induction à haute fréquence exploitent l'effet de profondeur de la peau. effet de profondeur de peau L'effet de profondeur de la peau, qui se réfère à la profondeur à laquelle le courant alternatif pénètre dans un matériau conducteur.
- Des fréquences plus élevées entraînent une une pénétration moins profonde concentrant la chaleur à la surface du matériau.Cela est particulièrement bénéfique pour les petits volumes de métal, car cela garantit un chauffage rapide et efficace.
- Les basses fréquences, en revanche, pénètrent plus profondément mais sont moins efficaces pour les petites fusions et peuvent provoquer des turbulences dans le métal en fusion.
-
Fusion plus rapide et temps de traitement réduit:
- Les hautes fréquences réduisent considérablement réduisent considérablement le temps de fusion en concentrant l'énergie sur la surface du matériau, là où elle est la plus efficace.
- Ceci est particulièrement avantageux pour les applications nécessitant des délais d'exécution rapides, comme dans les fonderies ou les industries métallurgiques.
-
Contrôle précis de la température:
- Les fours à induction à haute fréquence permettent un contrôle précis de la température Le contrôle précis de la température permet de s'assurer que le métal atteint la température souhaitée sans surchauffe.
- Cette précision est essentielle pour les procédés exigeant des propriétés métallurgiques spécifiques ou pour la fusion d'alliages dont la plage de température est étroite.
-
Agitation automatique par courants de Foucault:
- Le courant alternatif à haute fréquence génère des courants de Foucault dans le métal en fusion, créant ainsi un effet de brassage naturel.
- Ce brassage automatique assure l'homogénéité dans le métal en fusion, ce qui réduit la nécessité d'une intervention manuelle et améliore la qualité du produit final.
-
Conception simplifiée et coûts réduits:
- Les fours à induction à haute fréquence ont une conception plus simple du creuset et du récipient réduisant ainsi les besoins de maintenance et la complexité opérationnelle.
- Le coût coût d'exploitation est plus faible en raison d'une plus grande efficacité énergétique et d'une réduction du temps de traitement.
-
Efficacité énergétique et principes des transformateurs:
- Les fours à induction fonctionnent selon principes du transformateur Le transformateur est un appareil de mesure de l'énergie, où l'enroulement primaire (bobine d'induction) transfère de l'énergie à l'enroulement secondaire (la charge métallique).
- Les hautes fréquences (typiquement 500 Hz à 1000 Hz) assurent un transfert d'énergie efficace, minimisant les pertes et maximisant la production de chaleur par les courants de Foucault.
-
Applications et adéquation des matériaux:
- Les fours à induction à haute fréquence sont idéaux pour la fusion de les petits volumes de matériaux conducteurs tels que les métaux précieux, les alliages et les aciers spéciaux.
- Ils conviennent également aux applications nécessitant un chauffage rapide et un contrôle précis, comme dans les laboratoires ou la fabrication à petite échelle.
-
Comparaison avec les fours à induction à basse fréquence:
- Les fours à basse fréquence sont mieux adaptés aux volumes plus importants de métal, lorsqu'une pénétration plus profonde est nécessaire.
- Cependant, ils sont moins efficaces pour les petites pièces fondues et peuvent nécessiter des mécanismes d'agitation supplémentaires, ce qui augmente la complexité et le coût.
En résumé, les fours à induction à haute fréquence sont préférés pour leur capacité à fournir un chauffage rapide, précis et efficace, en particulier pour les petits volumes de métal.L'effet de profondeur de peau, le brassage automatique et la conception simplifiée en font un choix rentable et fiable pour une large gamme d'applications industrielles.
Tableau récapitulatif :
Caractéristiques principales | Avantages |
---|---|
Effet de profondeur de la peau | Concentre la chaleur sur la surface pour un chauffage rapide et efficace. |
Fusion plus rapide | Réduit le temps de traitement, idéal pour les applications à rotation rapide. |
Contrôle précis de la température | Assure un chauffage précis sans surchauffe, ce qui est essentiel pour certains alliages. |
Agitation automatique | Les courants de Foucault créent une homogénéité qui améliore la qualité du métal en fusion. |
Conception simplifiée | Coûts de maintenance et d'exploitation réduits, idéal pour les applications à petite échelle. |
Prêt à optimiser votre processus de fusion des métaux ? Contactez nous dès aujourd'hui pour en savoir plus sur les fours à induction à haute fréquence. pour en savoir plus sur les fours à induction à haute fréquence !