L'hydrogène gazeux est largement utilisé dans les fours de recuit en raison de ses propriétés uniques, telles qu'une conductivité thermique élevée, de fortes capacités de désoxydation et sa capacité à créer une atmosphère contrôlée qui empêche l'oxydation et la contamination. Il est particulièrement efficace pour le recuit des aciers à faible teneur en carbone, des aciers inoxydables et d'autres matériaux, car il garantit un processus propre et efficace. Toutefois, son utilisation nécessite un contrôle minutieux pour éviter des problèmes tels que la fragilisation par l'hydrogène ou la décarburation dans les matériaux à forte teneur en carbone. Le coefficient de transfert thermique élevé de l'hydrogène rend également le processus de recuit plus efficace, en particulier pour le traitement thermique des pièces moulées et soudées.
Explication des points clés :
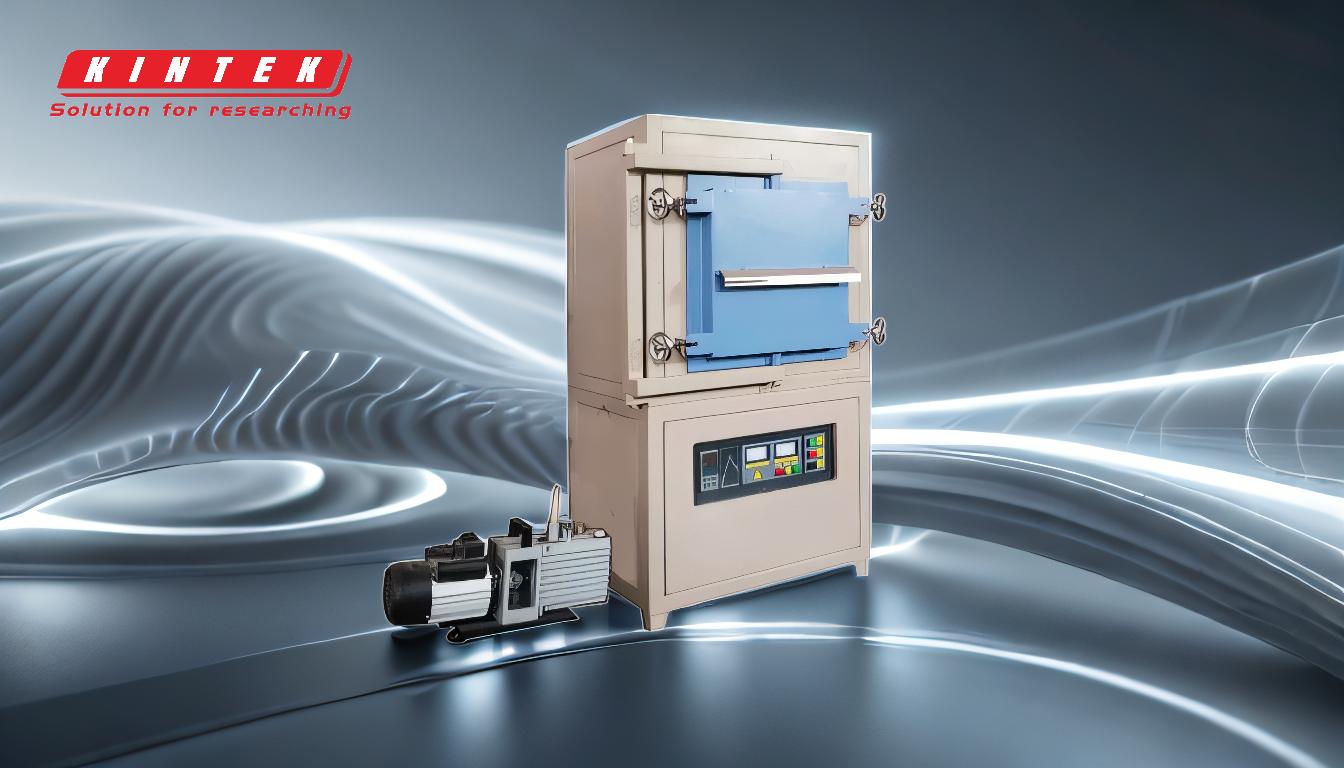
-
Conductivité thermique élevée:
- L'hydrogène a une conductivité thermique sept fois supérieure à celle de l'air. Cette propriété permet un transfert de chaleur plus rapide et plus uniforme pendant le processus de recuit, ce qui le rend plus efficace.
- Le coefficient élevé de transfert de chaleur permet au matériau recuit d'atteindre rapidement et uniformément la température souhaitée, ce qui réduit le temps de traitement et la consommation d'énergie.
-
Propriétés désoxydantes:
- L'hydrogène agit comme un puissant désoxydant, ce qui est essentiel pour empêcher l'oxydation du matériau pendant le recuit. Ceci est particulièrement important pour les métaux tels que l'acier inoxydable et les aciers à faible teneur en carbone, où l'oxydation peut dégrader les propriétés du matériau.
- À l'état sec, l'hydrogène peut éliminer efficacement l'oxygène de la surface du matériau, ce qui garantit une finition propre et exempte d'oxyde.
-
Atmosphère contrôlée:
- L'hydrogène est utilisé pour créer une atmosphère contrôlée dans le four de recuit, qui empêche la contamination par d'autres gaz comme l'oxygène ou l'azote. Cela est essentiel pour maintenir l'intégrité et la qualité du matériau recuit.
- L'atmosphère contrôlée est particulièrement bénéfique pour les processus tels que le frittage du carbure de tungstène, les composants en poudre métallique et la réduction directe des minerais métalliques.
-
Prévention de l'oxydation:
- En utilisant l'hydrogène comme atmosphère protectrice, le processus de recuit peut être réalisé sans risque d'oxydation. Ceci est particulièrement important pour les matériaux sensibles à l'oxydation, tels que les aciers inoxydables et les alliages magnétiques.
- L'absence d'oxygène dans l'atmosphère du four garantit que le matériau reste propre et exempt de défauts de surface.
-
Efficacité du traitement thermique:
- La conductivité thermique élevée et l'atmosphère contrôlée fournies par l'hydrogène rendent le processus de recuit plus efficace. Ceci est particulièrement bénéfique pour le traitement thermique des pièces moulées et soudées, où un chauffage uniforme est essentiel.
- L'efficacité de l'hydrogène dans le transfert de chaleur réduit le temps de traitement global, ce qui permet de réaliser des économies et d'améliorer la productivité.
-
Défis et limites:
- Fragilisation par l'hydrogène: L'hydrogène peut fragiliser les aciers à haute teneur en carbone et d'autres matériaux, entraînant une réduction de la ductilité et une défaillance potentielle. Il s'agit d'un problème important qui nécessite un contrôle minutieux du processus de recuit.
- Décarburation: Dans les matériaux à forte teneur en carbone, l'hydrogène peut entraîner une décarburation, c'est-à-dire que le carbone est éliminé de la surface, ce qui affaiblit le matériau. Ce phénomène est particulièrement problématique dans les aciers à haute teneur en carbone.
- Teneur en eau: L'efficacité de l'hydrogène en tant que désoxydant est limitée par sa teneur en eau. Il faut de l'hydrogène sec pour obtenir l'effet désoxydant désiré.
-
Applications dans diverses industries:
- Les fours de recuit à l'hydrogène sont utilisés dans un large éventail d'industries, notamment pour le traitement des alliages durs, des matériaux céramiques, des matériaux magnétiques et des métaux réfractaires rares.
- Ils sont également utilisés pour la métallurgie des poudres de frittage, le traitement des alliages de semi-conducteurs et le recuit et la purification des pièces en verre pour le scellement des pièces métalliques.
-
Caractéristiques de fonctionnement des fours de recuit à l'hydrogène:
- Ces fours sont équipés de systèmes de contrôle automatiques et manuels, permettant une régulation précise de la température.
- Ils peuvent atteindre des températures maximales de 1600℃, avec une précision de contrôle automatique de la température de ±1℃ et une uniformité de température de ±3℃ à ±10℃, selon les besoins de l'utilisateur.
- La possibilité de mémoriser plusieurs programmes de chauffage rend ces fours polyvalents et capables de répondre à diverses exigences en matière de processus.
En résumé, l'hydrogène gazeux est utilisé dans les fours de recuit en raison de sa conductivité thermique élevée, de ses propriétés désoxydantes et de sa capacité à créer une atmosphère contrôlée qui empêche l'oxydation et la contamination. Bien qu'il offre des avantages significatifs en termes d'efficacité et de qualité des matériaux, son utilisation doit être gérée avec soin pour éviter des problèmes tels que la fragilisation par l'hydrogène et la décarburation. La polyvalence et la précision des fours de recuit à l'hydrogène les rendent indispensables dans diverses applications industrielles.
Tableau récapitulatif :
Propriété | Avantages |
---|---|
Conductivité thermique élevée | 7x plus élevé que l'air ; assure un transfert de chaleur plus rapide et uniforme. |
Propriétés désoxydantes | Prévient l'oxydation, idéal pour l'acier inoxydable et les aciers à faible teneur en carbone. |
Atmosphère contrôlée | Empêche la contamination, ce qui est essentiel pour les processus de frittage et de poudres métalliques. |
Prévention de l'oxydation | Garantit des finitions propres et exemptes d'oxyde pour les matériaux sensibles. |
Efficacité du traitement thermique | Réduit le temps de traitement et la consommation d'énergie. |
Défis | Risque de fragilisation par l'hydrogène et de décarburation dans les aciers à haute teneur en carbone. |
Prêt à optimiser votre processus de recuit avec des fours à hydrogène ? Contactez nos experts dès aujourd'hui pour en savoir plus !