Introduction au frittage par étincelage (SPS)
Le frittage par plasma étincelant (SPS) représente une approche novatrice dans les technologies modernes de traitement des matériaux, révolutionnant la manière dont les matériaux sont frittés. Cette méthode innovante se distingue par l'utilisation d'impulsions de courant continu pour obtenir un chauffage et un frittage rapides, ce qui diffère considérablement des techniques traditionnelles. Le processus unique de SPS implique la génération d'un plasma d'étincelles par le biais de courants pulsés, ce qui facilite la création de matériaux aux propriétés supérieures. Au fil de ce guide complet, nous explorerons les subtilités du SPS, sa myriade d'applications dans diverses industries et les avantages substantiels qu'il offre par rapport aux méthodes de frittage conventionnelles. Rejoignez-nous pour découvrir le potentiel de transformation du frittage par plasma étincelant, qui façonnera l'avenir de la science des matériaux.
Comment fonctionne le four de frittage par plasma étincelant ?
Le frittage par étincelles de plasma (SPS), également connu sous le nom de frittage par courant électrique pulsé (PECS), frittage activé par plasma (PAS) ou technologie de frittage assisté par champ (FAST), est une technique de frittage sophistiquée qui utilise des courants continus pulsés élevés pour chauffer une poudre compacte dans une configuration de matrice/poinçonneuse. Cette méthode permet d'appliquer des forces de compression allant jusqu'à 250 kN, avec des sorties de transformateur pouvant atteindre 10 V et des courants allant jusqu'à 10 kA. Les modèles de courant continu pulsé peuvent être réglés avec des segments ON et OFF allant de 0 à 255 ms, ce qui permet un contrôle précis du processus de frittage.
Le procédé SPS se caractérise par des vitesses de chauffage et de refroidissement rapides, qui peuvent dépasser respectivement 1000°C/min et 400°C/min, en fonction de la taille et de la conception de l'outil. Ce cycle thermique rapide minimise les processus de grossissement à basse température et préserve les nanostructures intrinsèques même après une densification complète. La température à l'intérieur du four SPS est contrôlée à l'aide d'un pyromètre central qui se concentre sur le fond d'un trou de forage dans le poinçon supérieur, garantissant une mesure précise de la température quelles que soient les propriétés ou la taille de l'échantillon. Un pyromètre externe et des thermocouples flexibles placés à différents endroits permettent d'assurer une surveillance supplémentaire de la température.
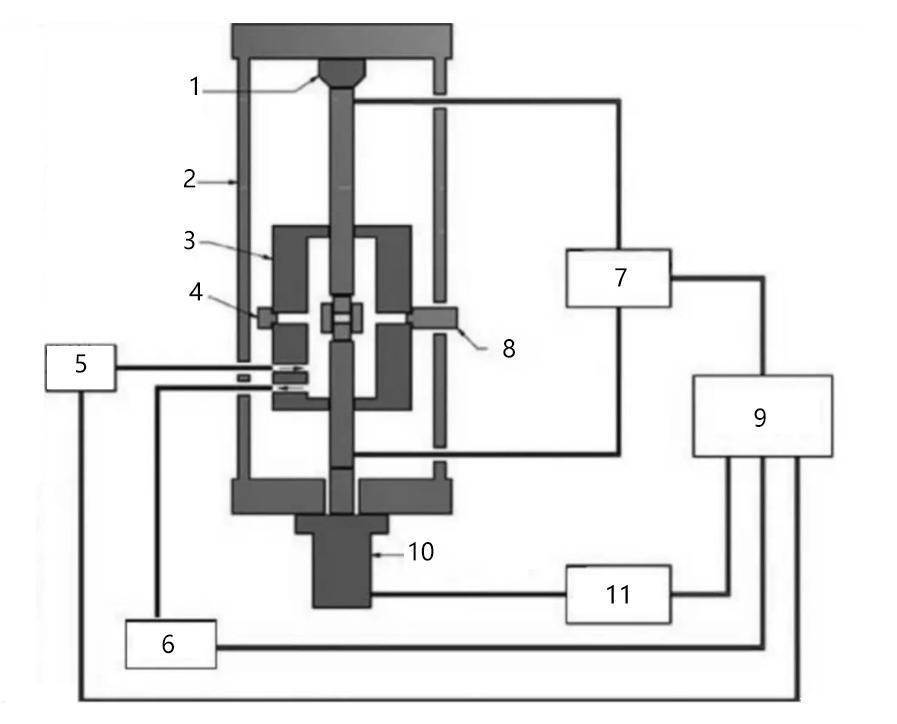
1. Unité de chargement 2. Cadre de chargement 3. Chambre à vide 4. Fenêtre d'observation 5. Canal de gaz inerte 6. Pompe à vide 7. Interrupteur à impulsion 8. Compteur de température 9. Système de contrôle 10. Cylindre hydraulique 11. Système hydraulique
Les composants clés d'un four SPS comprennent le dispositif de pression axiale, l'électrode de poinçonnage refroidie à l'eau et la chambre à vide. Le dispositif de pression axiale applique la force de compression nécessaire, tandis que les électrodes de poinçonnage refroidies à l'eau aident à gérer la chaleur générée au cours du processus. La chambre à vide, associée à un système de contrôle de l'atmosphère qui peut passer du vide à l'argon, assure des conditions de frittage optimales. L'alimentation électrique à impulsion DC, ainsi qu'un système d'eau de refroidissement, des unités de mesure du déplacement, de mesure de la température et de contrôle de la sécurité, complètent l'installation SPS, facilitant le contrôle complet du processus et la programmation du cycle de frittage par le biais d'une interface conviviale à écran tactile.
Le four SPS est largement utilisé pour le frittage d'une large gamme de matériaux, y compris les céramiques, les cermets et les métaux. Ses principaux avantages techniques résident dans ses vitesses de chauffage et de refroidissement élevées, qui réduisent considérablement les temps de traitement. Le courant pulsé élevé améliore non seulement la densification des matériaux conducteurs d'électricité, mais active également de multiples mécanismes de frittage tels que l'élimination des oxydes de surface, l'électromigration et l'électroplasticité. Cette combinaison de pression mécanique, de champ électrique et de champ thermique améliore considérablement la liaison et la densification entre les particules, ce qui fait du SPS une méthode privilégiée pour la préparation de matériaux à hautes performances.
En résumé, le procédé de frittage par plasma étincelant est une méthode très efficace et contrôlée de densification des matériaux, offrant des temps de traitement rapides et la capacité de maintenir des microstructures fines. Ses applications couvrent divers domaines, des céramiques avancées aux composites métalliques, ce qui souligne sa polyvalence et son importance dans la science et l'ingénierie des matériaux modernes.
Avantages de l'utilisation du frittage par plasma étincelant dans le traitement des matériaux
Le frittage par plasma étincelant (SPS) a révolutionné le domaine du traitement des matériaux en offrant des avantages significatifs par rapport aux techniques de frittage traditionnelles. Le frittage par étincelage est une technique de frittage assistée par champ qui utilise à la fois la température et la pression pour obtenir une densification rapide des matériaux. Cette méthode est particulièrement efficace pour le frittage d'une large gamme de matériaux, y compris les céramiques, les métaux et les composites, avec une efficacité et une précision remarquables.
Taux de frittage rapide
L'un des avantages les plus notables de la technologie SPS est sa capacité à atteindre des taux de frittage rapides. Les méthodes de frittage traditionnelles, telles que le pressage à chaud et le frittage sans pression, peuvent prendre plusieurs heures pour obtenir la densification souhaitée. En revanche, la technologie SPS permet de densifier les matériaux en quelques minutes seulement. Ce frittage rapide est rendu possible par les vitesses de chauffe élevées, qui peuvent dépasser 500°C par minute. Par exemple, une température de 1200°C peut être atteinte en seulement 4 minutes avec la technologie SPS, contre 2 à 4 heures avec les méthodes conventionnelles. Cette rapidité permet non seulement d'améliorer la productivité, mais aussi de réduire la consommation d'énergie et les coûts d'exploitation.
Frittage à grain fin
La technologie SPS facilite le frittage de grains fins, ce qui est essentiel pour améliorer les propriétés mécaniques et physiques des matériaux frittés. Les taux de chauffage rapides inhibent la croissance des grains, ce qui permet de créer des matériaux avec des microstructures contrôlées. Ceci est particulièrement bénéfique pour la production de matériaux nanocristallins, où le maintien de grains de petite taille est essentiel pour obtenir des propriétés supérieures. Le frittage à grains fins améliore également l'homogénéité des produits frittés, ce qui permet d'obtenir des performances plus cohérentes et plus fiables.
Capacité à contrôler les gradients de densité et de température
La technologie SPS permet un excellent contrôle des gradients de densité et de température à l'intérieur des matériaux frittés. Ce niveau de contrôle est obtenu par l'application simultanée de la température et de la pression, ce qui permet des ajustements précis du processus de frittage. Le contrôle de la densité est particulièrement important pour créer des matériaux présentant des niveaux de porosité spécifiques ou pour obtenir une densification complète. En outre, le système SPS peut créer des gradients de température à l'intérieur du moule, ce qui permet de fritter simultanément des matériaux ayant des points de fusion différents. Cette capacité est inestimable pour la production de matériaux à gradation fonctionnelle, dont la composition et les propriétés varient dans l'espace.
Efficacité et compacité des fours SPS
Les fours SPS sont conçus pour être très efficaces et compacts, ce qui les rend idéaux pour la recherche et les applications industrielles. La conception compacte des fours SPS réduit l'espace nécessaire au sol et permet une intégration facile dans les lignes de production existantes. En outre, l'efficacité des fours SPS est renforcée par leur capacité à atteindre des vitesses de chauffage et de refroidissement rapides, ce qui contribue à des économies d'énergie et à une réduction des coûts d'exploitation. Le mécanisme de chauffage interne, qui implique le chauffage par effet Joule du moule en graphite et de la briquette de poudre, assure une distribution uniforme de la chaleur et minimise les pertes de chaleur, optimisant ainsi le processus de frittage.
Frittage de purification et d'activation
Le procédé SPS offre également des avantages uniques en termes de purification et de frittage d'activation. Le processus peut éliminer les gaz adsorbés et les films d'oxyde de la surface des particules, ce qui permet d'obtenir des interfaces plus propres et une meilleure liaison. Cet effet de purification, combiné à l'activation des surfaces des particules, permet le frittage de matériaux autrement difficiles à traiter. Cette capacité élargit la gamme des matériaux qui peuvent être frittés efficacement à l'aide du SPS, y compris les céramiques et les composites avancés.
En conclusion, le frittage par plasma étincelant (SPS) offre une multitude d'avantages qui en font un choix supérieur pour le traitement des matériaux. Ses taux de frittage rapides, ses capacités de frittage à grains fins, son contrôle de la densité et du gradient de température, son efficacité et sa compacité en font un outil inestimable pour la recherche et les applications industrielles. En tirant parti de ces avantages, la technologie SPS continue de repousser les limites de la science et de l'ingénierie des matériaux, permettant le développement de matériaux innovants et performants.
Applications du frittage par plasma étincelant dans diverses industries
La technologie du frittage par plasma étincelant (SPS) a révolutionné les processus de fabrication dans de nombreuses industries, permettant la création de matériaux avancés aux propriétés uniques. La technologie SPS est particulièrement réputée pour sa capacité à produire rapidement et à des températures relativement basses des matériaux à haute densité et à grain fin, ce qui en fait une méthode privilégiée pour la synthèse de nanomatériaux, de céramiques, de composites et d'implants médicaux.
Nanomatériaux
L'une des applications les plus importantes de la SPS est la préparation de nanomatériaux. Les nanomatériaux présentent des propriétés mécaniques et physiques exceptionnelles en raison de la petite taille de leurs grains, qui renforce leur résistance et leur plasticité. La SPS facilite la synthèse de ces matériaux en inhibant la croissance des grains pendant le processus de frittage. Le chauffage rapide et les temps de frittage courts inhérents à la SPS permettent de maintenir la taille des grains à l'échelle du nanomètre, ce qui est crucial pour la performance des nanomatériaux. Cette technique est particulièrement efficace pour le frittage de poudres obtenues par des méthodes telles que l'alliage mécanique, qui sont souvent difficiles à consolider par des méthodes traditionnelles.
Céramiques et cermets
La technologie SPS est également largement utilisée dans la production de céramiques et de cermets à haute densité et à grain fin. Le mécanisme de chauffage unique de la SPS, où chaque particule de poudre et les pores entre elles agissent comme des sources de chaleur, permet une densification rapide et une réduction significative des temps et des températures de frittage. Cette méthode est très avantageuse pour la production industrielle car elle permet d'économiser de l'énergie et d'améliorer l'efficacité de la production. La capacité à produire des céramiques à haute densité et à structure granulaire fine améliore leur résistance mécanique et leur durabilité, ce qui les rend adaptées à diverses applications techniques.
Matériaux fonctionnels à gradient
Les matériaux fonctionnels à gradient, qui présentent une distribution à gradient dans certaines directions, sont un autre domaine dans lequel les SPS ont apporté des contributions significatives. Les méthodes de frittage traditionnelles ont du mal à gérer les différentes températures de frittage requises pour chaque couche dans les matériaux à gradient. La technologie SPS, en revanche, peut gérer efficacement ce gradient, ce qui permet la production à l'échelle industrielle de ces matériaux complexes. Le processus de frittage contrôlé de SPS garantit que chaque couche atteint les propriétés souhaitées sans compromettre l'intégrité de la structure globale.
Implants médicaux
Dans le domaine médical, la technologie SPS est utilisée pour fabriquer des implants aux propriétés mécaniques et à la biocompatibilité adaptées. La possibilité de contrôler avec précision les conditions de frittage permet de créer des implants dont les propriétés mécaniques spécifiques correspondent à celles de l'os humain, ce qui améliore leur fonctionnalité et leur longévité. En outre, les SPS peuvent être utilisés pour produire des structures poreuses qui facilitent la croissance osseuse, améliorant ainsi l'intégration des implants dans les tissus environnants.
Composites et matériaux nanostructurés
La technologie SPS permet de fabriquer des matériaux composites et nanostructurés dotés de propriétés améliorées telles que les caractéristiques magnétiques, piézoélectriques, thermoélectriques et optiques. Le processus de frittage rapide dans les SPS permet de maintenir la nanostructure des matériaux, ce qui est crucial pour leurs performances. Par exemple, le SPS est utilisé pour le frittage de nanotubes de carbone afin de développer des électrodes d'émission d'électrons de champ, ce qui démontre sa polyvalence dans le traitement de différents types de matériaux.
En conclusion, le frittage par plasma étincelant s'est imposé comme une technique polyvalente et puissante dont les applications s'étendent à de nombreux secteurs. Sa capacité à produire des matériaux avancés de haute qualité aux propriétés uniques en fait un outil indispensable à la fabrication moderne. Au fur et à mesure que la recherche et le développement dans ce domaine progressent, les applications potentielles du frittage par plasma étincelant devraient encore s'étendre, stimulant ainsi l'innovation dans la science et l'ingénierie des matériaux.
Études de cas : Mise en œuvre réussie des techniques de frittage par plasma étincelant
La technologie du frittage par plasma étincelant (SPS) a révolutionné le domaine de la science des matériaux, en permettant le frittage et la densification rapides d'une large gamme de matériaux aux propriétés améliorées. Cette section présente plusieurs études de cas qui mettent en évidence les applications réussies du SPS dans la recherche et dans l'industrie, démontrant ainsi sa polyvalence et son efficacité.
Matériaux de stockage d'énergie
L'une des applications les plus importantes des SPS est le développement de matériaux avancés pour le stockage de l'énergie. Par exemple, la technologie SPS a été utilisée pour produire des batteries lithium-ion de grande capacité et aux performances améliorées. En contrôlant précisément les paramètres de frittage, les chercheurs ont été en mesure de créer des matériaux de batterie avec des densités d'énergie plus élevées et une meilleure durée de vie. Selon des études, les batteries lithium-ion traitées par SPS ont montré une augmentation de 20 % de la capacité de stockage d'énergie par rapport aux méthodes conventionnelles, ce qui les rend idéales pour une utilisation dans les véhicules électriques et l'électronique portable.
Ingénierie biomédicale
Dans le domaine de l'ingénierie biomédicale, les SPS ont contribué à la création de céramiques poreuses pour l'administration de médicaments et d'échafaudages pour l'ingénierie tissulaire. Ces matériaux nécessitent un contrôle précis de leur microstructure pour assurer leur compatibilité avec les systèmes biologiques. La technologie SPS permet de fabriquer des structures très poreuses dont la taille des pores est contrôlée, ce qui est essentiel pour l'administration efficace de médicaments et la croissance des tissus. Par exemple, des échafaudages d'hydroxyapatite traités par SPS ont été utilisés dans l'ingénierie des tissus osseux, démontrant une biocompatibilité et une résistance mécanique supérieures à celles des méthodes traditionnelles.
Céramique avancée
La technologie SPS a également été largement utilisée dans la production de céramiques avancées, telles que les supraconducteurs à haute température et les céramiques piézoélectriques à haute performance. Ces matériaux sont essentiels pour des applications allant de la transmission d'énergie aux capteurs et actionneurs. La technologie SPS permet de densifier ces céramiques à des températures plus basses et dans des délais plus courts, tout en préservant leurs propriétés uniques. Par exemple, la SPS a été utilisée pour produire des supraconducteurs à base d'oxyde de cuivre et de baryum et d'yttrium (YBCO) avec des densités proches de la théorie, améliorant ainsi de manière significative leurs températures de transition supraconductrices.
Matériaux intermétalliques et composites
La polyvalence de la technologie SPS est également démontrée dans le traitement des intermétalliques et des composites. La SPS a été utilisée pour créer des alliages avancés aux propriétés mécaniques, thermiques et électriques améliorées. Par exemple, la SPS a été utilisée pour synthétiser des alliages intermétalliques d'aluminure de titane (TiAl), qui présentent une résistance supérieure à haute température et à l'oxydation. En outre, la SPS a permis la production de céramiques et de métaux renforcés aux propriétés mécaniques améliorées, tels que les composites à matrice de titane avec des particules de céramique incorporées, ce qui donne des matériaux très solides et résistants à l'usure.
Applications industrielles
Dans l'industrie, la technologie SPS a été adoptée pour la production de divers matériaux, notamment des matériaux magnétiques, des matériaux durs et des matériaux fonctionnels à gradient. Par exemple, des entreprises japonaises comme Ohta Seiki ont mis en œuvre avec succès la technologie SPS pour la production de masse de matériaux superdurs 100 % WC, fournissant plus de 40 fabricants au Japon et à l'étranger. Ces matériaux sont utilisés dans une large gamme d'applications, allant des outils de coupe aux composants électroniques, ce qui démontre l'évolutivité industrielle de la technologie SPS.
Conclusion
Les études de cas présentées ici illustrent les vastes possibilités d'application des SPS dans divers domaines, du stockage de l'énergie à l'ingénierie biomédicale en passant par les matériaux avancés. La capacité de la technologie SPS à fritter et à densifier rapidement des matériaux à des températures plus basses, associée à un contrôle précis du processus, en fait un outil inestimable pour les scientifiques et les ingénieurs spécialisés dans les matériaux. Au fur et à mesure que la recherche et le développement progressent, les applications potentielles de la technologie SPS devraient encore s'étendre, consolidant ainsi sa position en tant que technologie de pointe dans le domaine du traitement des matériaux.
Défis et considérations concernant le frittage par plasma étincelant
La mise en œuvre de la technologie de frittage par plasma étincelant (SPS) présente plusieurs défis et considérations que les organisations doivent relever pour tirer pleinement parti de ses avantages. Il s'agit notamment du coût élevé des équipements, de la complexité des opérations et de la nécessité d'une formation spécialisée. Il est essentiel de comprendre ces défis et d'élaborer des stratégies pour les surmonter afin de réussir l'intégration et l'utilisation de la technologie SPS.
Coûts des équipements
L'un des principaux obstacles à l'adoption de la technologie SPS est l'investissement initial élevé requis pour l'équipement. Les systèmes SPS sont sophistiqués et comportent des caractéristiques avancées telles qu'un contrôle précis de la température et de la pression, des systèmes de vide et des blocs d'alimentation spécialisés. Ces composants augmentent non seulement le coût initial, mais nécessitent également un entretien et un étalonnage réguliers pour garantir des performances optimales.
Complexité des opérations
Les opérations SPS comportent plusieurs étapes, notamment la création du vide, l'application de la pression, le chauffage par résistance et le refroidissement contrôlé. Chaque étape nécessite une surveillance et un réglage minutieux afin d'éviter les défauts et de garantir les propriétés souhaitées du matériau. La complexité de ces opérations nécessite un niveau élevé d'expertise technique et une attention méticuleuse aux détails, ce qui peut représenter un défi pour les organisations qui n'ont pas d'expérience préalable dans les techniques de frittage avancées.
Formation spécialisée
Compte tenu de la nature technique des SPS, le personnel chargé de l'exploitation et de l'entretien de l'équipement doit suivre une formation spécialisée. Cette formation doit porter non seulement sur le fonctionnement de base du système SPS, mais aussi sur des sujets avancés tels que l'optimisation du processus, le dépannage et les protocoles de sécurité. Le coût et le temps nécessaires à cette formation peuvent être importants, ce qui risque de retarder la mise en œuvre de la technologie SPS.
Stratégies pour surmonter les difficultés
Pour surmonter ces difficultés, les entreprises peuvent adopter plusieurs stratégies :
-
Investissement dans des équipements de haute qualité: Bien que le coût initial soit élevé, l'investissement dans un équipement SPS fiable et de haute qualité peut réduire les coûts de maintenance et d'exploitation à long terme. Le choix d'équipements provenant de fabricants réputés disposant de solides réseaux d'assistance et de service peut également contribuer à atténuer les problèmes qui surviennent en cours d'exploitation.
-
Collaboration et partenariats: Un partenariat avec des instituts de recherche ou d'autres entreprises qui ont de l'expérience dans le domaine des MSP peut apporter des informations et un soutien précieux. Les projets de collaboration peuvent aider à partager les coûts et l'expertise nécessaires à une mise en œuvre réussie.
-
Formation et développement continus: Investir dans la formation continue du personnel permet de s'assurer qu'il reste au fait des dernières techniques et des meilleures pratiques dans le domaine des MSP. Cela peut se faire par le biais d'ateliers, de cours en ligne et de séances de formation pratique.
-
Optimisation des processus: L'élaboration de processus solides, bien documentés et normalisés peut contribuer à réduire la variabilité et à améliorer la cohérence des résultats. Cela implique une expérimentation et une validation minutieuses afin d'identifier les conditions optimales pour chaque matériau et chaque application.
-
Accent sur la recherche et le développement: S'engager dans une recherche et un développement continus peut aider les organisations à rester à la pointe de la technologie SPS. Il peut s'agir d'explorer de nouveaux matériaux, d'optimiser les processus existants et de développer des applications innovantes pour les composants produits par les SPS.
Conclusion
Bien que la mise en œuvre de la technologie SPS présente plusieurs défis, ceux-ci peuvent être gérés efficacement grâce à des stratégies et des investissements appropriés. En s'attaquant aux coûts élevés, aux complexités opérationnelles et aux exigences en matière de formation, les organisations peuvent libérer tout le potentiel de la technologie SPS, ce qui permettra des avancées significatives dans les domaines de la science des matériaux et de la fabrication.
Tendances futures du frittage par plasma étincelant
La technologie du frittage par étincelage (SPS), connue pour ses capacités de frittage rapide à des températures relativement basses, continue d'évoluer, offrant des avancées significatives en termes d'efficacité, d'évolutivité et de diversité des applications. Alors que la demande de nouveaux matériaux et de procédés de fabrication efficaces augmente, la technologie SPS est à la pointe de l'innovation technologique dans le domaine de la science des matériaux.
Amélioration de l'efficacité
L'un des principaux domaines d'intérêt de la technologie SPS est l'amélioration de son efficacité. Les méthodes de frittage traditionnelles peuvent prendre beaucoup de temps et consommer beaucoup d'énergie, alors que la technologie SPS réduit considérablement le temps de traitement et la consommation d'énergie. Les développements futurs visent à optimiser davantage ces aspects en affinant les techniques de courant pulsé et en améliorant les systèmes de contrôle des dispositifs SPS. Par exemple, des progrès dans les systèmes d'alimentation et de contrôle pourraient permettre un contrôle plus précis de la température et de la pression, conduisant à des processus de frittage plus efficaces.
Amélioration de l'évolutivité
L'extensibilité est un autre aspect essentiel de la technologie SPS. À l'heure actuelle, les SPS sont principalement utilisées en laboratoire et pour la production à petite échelle. Cependant, pour répondre à la demande industrielle, les futurs systèmes SPS devront traiter des volumes plus importants et des formes plus complexes. Les chercheurs étudient de nouveaux matériaux et modèles de moules capables de résister à des pressions et à des températures plus élevées, tout en garantissant l'intégrité et la réutilisation des moules. En outre, l'intégration de la robotique avancée et de l'automatisation dans l'équipement SPS pourrait faciliter la production de pièces plus grandes et plus complexes, faisant de la SPS une option viable pour la fabrication de grands volumes.
Expansion vers de nouveaux types de matériaux et de nouvelles industries
La technologie SPS est traditionnellement utilisée pour le frittage des métaux et des céramiques. Cependant, ses capacités uniques offrent un potentiel d'expansion vers de nouveaux types de matériaux et de nouvelles industries. Les recherches futures devraient se concentrer sur l'application de la technologie SPS à une gamme plus large de matériaux, y compris les polymères, les composites et les nanomatériaux. Cette extension pourrait ouvrir la voie à de nouvelles applications dans des secteurs tels que l'électronique, l'aérospatiale et l'ingénierie biomédicale, où le contrôle précis des propriétés des matériaux est crucial.
Avantages environnementaux et économiques
Les avantages environnementaux et économiques de la technologie SPS sont également à l'origine de son développement futur. Le processus de production économe en énergie et à faible taux de déchets de SPS s'aligne sur les objectifs mondiaux en matière de développement durable. Les industries recherchant de plus en plus des solutions de fabrication respectueuses de l'environnement, les SPS pourraient devenir une méthode privilégiée pour la production de matériaux de haute performance. En outre, la réduction des temps de traitement et des coûts énergétiques associée à la technologie SPS peut entraîner d'importantes économies, ce qui en fait une option attrayante pour les fabricants.
Intégration et collaboration technologiques
Enfin, l'avenir de la technologie des SPS passera probablement par une plus grande intégration avec d'autres technologies de fabrication avancées et par des efforts de collaboration dans différents domaines. Par exemple, la combinaison des SPS et des techniques de fabrication additive pourrait conduire à la création de processus de fabrication hybrides qui tireraient parti des atouts des deux technologies. En outre, la recherche interdisciplinaire impliquant la science des matériaux, l'ingénierie électrique et l'ingénierie mécanique pourrait conduire à des percées dans la compréhension et l'optimisation du processus SPS.
En conclusion, l'avenir du frittage par plasma étincelant est prometteur, avec des avancées potentielles susceptibles d'en faire une technologie plus efficace, plus évolutive et plus polyvalente. Avec la poursuite de la recherche et du développement, le frittage par plasma étincelant pourrait révolutionner la façon dont nous produisons des matériaux avancés, en contribuant aux innovations dans diverses industries et en favorisant des pratiques de fabrication durables.
Conclusion : Le rôle des SPS dans l'évolution de la science des matériaux
En conclusion, lefrittage par étincelage et plasma (SPS) se distingue comme une technologie transformatrice dans le domaine de la science des matériaux. Sa capacité à fritter rapidement des matériaux à des niveaux de grains fins, associée à son efficacité et à sa polyvalence, fait du SPS une pierre angulaire du traitement moderne des matériaux. Pour l'avenir, la technologie SPS est prête à apporter des innovations significatives, à étendre ses applications à diverses industries et à ouvrir la voie au développement de matériaux avancés à hautes performances. L'évolution et l'adoption continues de la technologie SPS façonneront sans aucun doute l'avenir de la science des matériaux, en offrant de nouvelles possibilités et solutions aux défis complexes posés par les matériaux.
CONTACTEZ-NOUS POUR UNE CONSULTATION GRATUITE
Les produits et services de KINTEK LAB SOLUTION ont été reconnus par des clients du monde entier. Notre personnel se fera un plaisir de répondre à toute demande que vous pourriez avoir. Contactez-nous pour une consultation gratuite et parlez à un spécialiste produit pour trouver la solution la plus adaptée aux besoins de votre application !